SKF improving efficiency with automatic lubrication systems
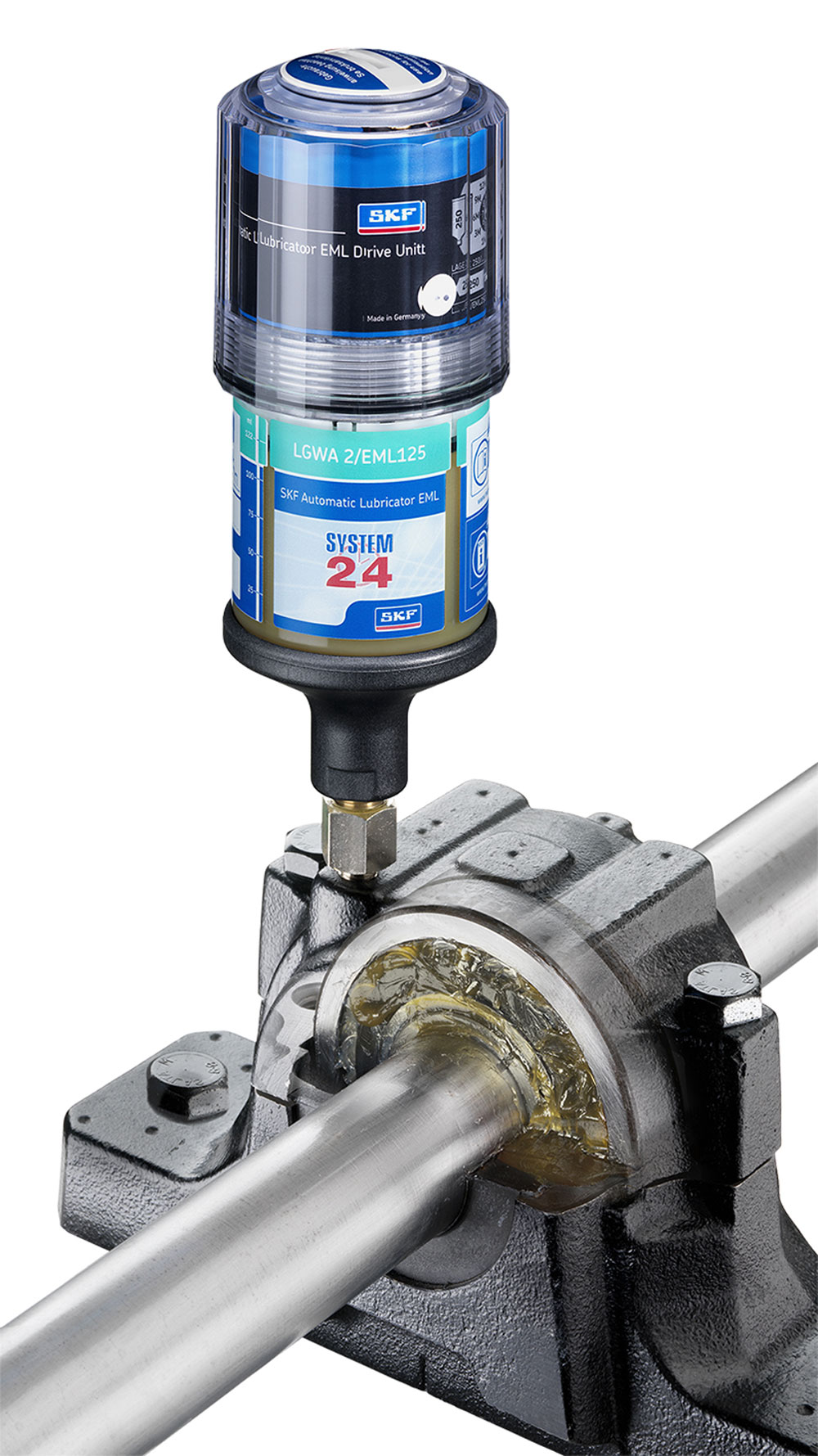
First published in the October 2013 issue of Quarry Management as Automatically Efficient
The days of manual lubrication are long gone. Today, automatic lubrication systems lubricate and protect the right points on each machine, using the right amount of the right lubricant at the right time. Phil Burge, communication manager for SKF, looks at automatic lubrication systems and how they strengthen efficiency at a time when financial pressures on quarry management are greater than ever.
Friction, wear, corrosion and dirt are words that are etched into the hearts of most engineers – especially those responsible for the operation and maintenance of heavy plant and machinery where downtime means missed deadlines, delayed schedules and cost penalties. Machine availability depends on a variety of factors, of which correct lubrication is undoubtedly one of the most important.
However, determining which lubrication system provides the best results from an economic and ecological point of view depends largely on the type of machine it serves, the ambient temperature, operating conditions and so on. If correctly specified, automatic lubrication systems swiftly repay investment, not least when integrated with heavy machinery in the construction, civil engineering, mining and quarrying industries where lubrication is critical.
Automatic lubrication systems reduce the risk of machine failure and support improved machine productivity, a crucial factor when meeting ever-tighter project deadlines and budgets. The mining and quarrying industries must maximize efficiency to extract raw materials from the ground in the most cost-effective way, and this means embracing the most up-to-date methods of production, state-of-the-art products and new technologies, such as automatic lubrication.
It also means making sure that all engineers are aware of the issues that affect efficiency. For example, most engineers are aware that insufficient lubricant can bring a system to a standstill, because without lubrication the bearings will run dry and the elevated temperature will ultimately cause machine failure. However, it is also important to remember that too much lubricant can increase both friction and temperature, and effect the migration of grease into parts, such as electric motors, where it can cause damage. This underlines why it is so important to manage lubricant delivery.
A good example of how automated systems prevent over-lubrication is to consider a bearing that has to be manually re-lubricated with 2g of grease every week. Using a standard grease gun this would mean that the bearing should receive about 1.3 ‘strokes’. However, manually delivering 0.3 strokes is difficult. So, in reality, two strokes would likely be given. In other words, the bearing will receive 3g instead of 2g of lubricant each time. Over a year, the bearing will receive 156g (52 weeks x 3g per week) instead of 104g (52 weeks x 2g per week).
In heavy industries where corrosion and dirt pose a major challenge to the effective function of mechanical components, automatic lubrication systems offer a powerful alternative to conventional methods. For example, the latest generation of SKF System 24 automatic lubricators provides a reliable, easy-to-use and cost-effective way to deliver a continuous supply of premium-quality SKF lubricant to machine components, reducing costly unplanned downtime and extending bearing service life. By removing the need for manual lubrication practices, the end result is continuous and optimum lubrication, even in applications subject to high levels of contamination. System 24 automatic lubricators also provide reliable service in demanding, hard-to-reach, remote, and hazardous areas, as they are ATEX certified.
Multiple lubrication points can also be greased by a single automatic lubricator. For example, the SKF MultiPoint LAGD 400, a centralized automatic lubricator, will keep up to eight points simultaneously greased. All the operator needs to do is set the correct grease dispense rate using DialSet, SKF’s re-lubrication calculation programme, and refill when notified by the alarm. A greater number of lubrication points can be served by the SKF MultiPoint LAGD 1000 device, which can lubricate as many as 20 lubrication points and offers high flexibility in the types of lubricants that can be used. The sturdy, robust design and IP65 rating of the LAGD 1000 makes it suitable for most industrial environments and the range of programming options available offers the flexibility to suit most applications.
Automatic lubrication systems such as this offer many simple but extremely useful functions, such as transparent containers that allow the dispensing function and lubricant levels to be easily checked. The best of today’s automatic lubricators can also be temporarily deactivated when machinery is not running, eg during scheduled maintenance, and, increasingly, disposed of in an environmentally friendly way.
Customers have achieved significant savings and reductions in maintenance times simply by upgrading their bearing units and fitting System 24 single-point automatic lubricators. In applications such as quarrying, where machinery is running seven days a week and is exposed to the elements, automatic lubrication can make a huge difference.
The operating environment in the quarrying industry is especially tough, with contamination an ever-present threat. In conditions such as this, machinery requires constant maintenance; in particular, bearings fitted to rotating drives and shafts need regular lubrication and frequent replacement. However, manual lubrication can often be hard to achieve safely as the components concerned may be in inaccessible locations. Additionally, it can be difficult to apply the correct volume of lubricant and/or lubrication points may be missed, the result being that bearings can run dry or become over-lubricated. Ultimately, the operating life of bearings is significantly shortened, resulting in considerable downtime. Indeed, it is not uncommon for machines to be off-line for several days, delaying production and keeping engineers tied up on repairs.
However, with a dedicated automatic lubricator attached to each bearing, the need for manual lubrication can be eliminated. Integrated into the head of the System 24 cartridge is a hydrogen cell that releases gas at controlled intervals to pressurize an internal piston; in turn, this forces lubricant through the neck of the cartridge, which is screwed directly into the bearing unit. The piston and internal cartridge surfaces are shaped to ensure that all the lubricant is thoroughly dispensed, while the rate at which the lubricant is distributed is accurately controlled by an integrated timer. This can be adjusted on site, allowing oil or grease to be distributed at intervals of between one month and 12 months, and at rates that can be as low as 4.5g per month.
The best of today’s automatic lubricators are robust enough to withstand harsh operating conditions, are simple to fit and set up, and are available with a range of different lubricants. A quick visual check of reservoir levels is all that’s required during a routine monthly maintenance check and each device operates for around 12 months before needing replenishment.
Switching to automatic lubricators contributes to significantly increased bearing life and offers a fast return on investment. In contrast, incorrect lubrication, either excessive or inadequate, is problematic. SKF estimate that overtime labour is mostly a result of machine failures, typically caused by inadequate lubrication, so there is a pressing need for engineers to consider a more efficient way to lubricate machinery. Not all lubricants are suitable for all automatic lubrication systems, and conversely, the impact of a lubrication system on the structure of the lubricant depends on the technology of the particular lubrication system. It is important, therefore, to get the best advice from an expert supplier when choosing to move into automatic lubrication. As stated earlier, however, there are solutions available in the market for virtually every application, and it is difficult to imagine any critical application in the engineering workplace today that is not worth equipping with an automatic lubrication device.
Moreover, automatic systems are continuing to evolve, allowing the delivery of lubricant to be carried out easily and efficiently. New options include compatibility with iOS and android apps, and tool-free set-up, all of which offer the opportunity to establish an efficient and easily managed lubrication regime.
It is crucial to the efficient operation of machinery that effective lubrication is provided, and the failure of manual lubrication to deliver the correct lubrication to the correct degree can lead to excessive waste, increased cost, machine wear and failure. The latest automatic systems can reverse this trend, bringing sustainability, efficiency and cost savings at a time when all three are high on the business agenda.
For further information visit: www.skf.co.uk
- Subscribe to Quarry Management, the monthly journal for the mineral products industry, to read articles before they appear on Agg-Net