Selecting The Right Grease
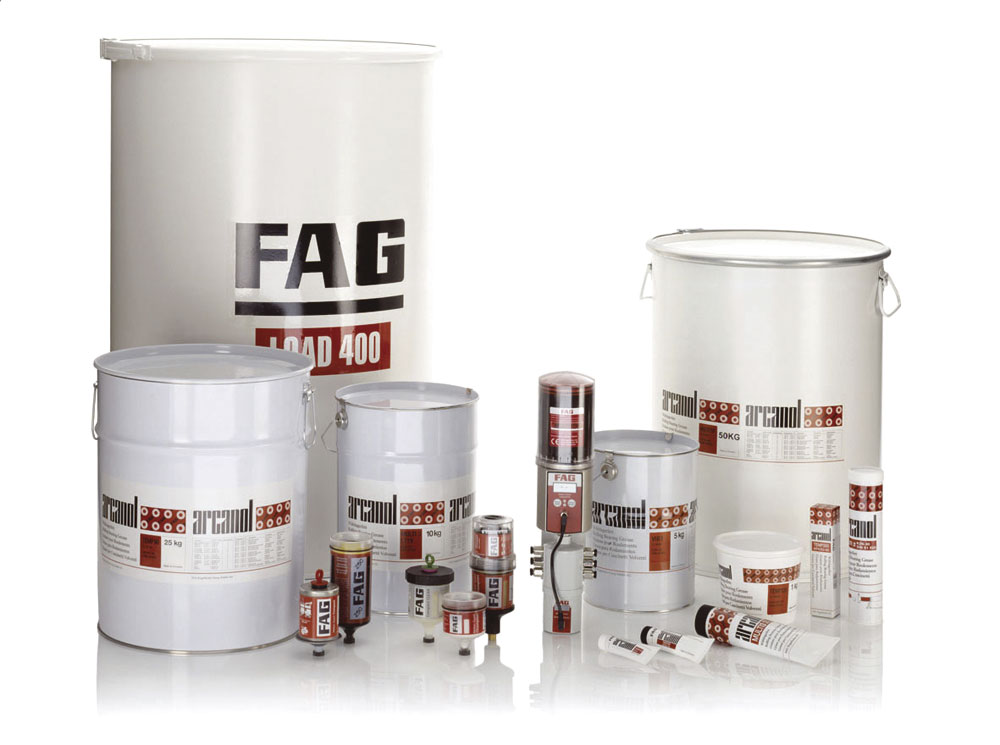
More than 40% of all premature failures of rolling bearings are caused by inadequate or incorrect selection of lubricant. Choosing the most appropriate grease and re-lubrication equipment for a bearing application is therefore vital, as Ian Pledger of Schaeffler (UK) Ltd explains
More than 80% of all rolling bearings are lubricated with grease. It is critical, therefore, that engineers select the most appropriate grease for the bearing and the application it is operating in. Not only will correct selection prolong the life of the bearing, allowing it to operate at its full capacity, but it also ensures smoother running behaviour and improved operational safety.
However, selecting a suitable lubricant for a rolling bearing can be a complex process. Grease is basically a type of oil with a thickening agent added to it, giving it a more viscous form. There are many different types of bearing grease available, so engineers should take the time to make more informed selections that ensure a long and trouble-free life for the bearing.
Greases can be used effectively to lubricate bearings over a very wide range of operating conditions. However, initial selection is based on two critical parameters.
First, the ‘P/C’ ratio, which is a measure of the load ‘P’ on the bearing in relation to the dynamic capacity ‘C’, which is calculated according to international standards and quoted by all leading bearing manufacturers in their technical literature. In general, if the ‘P/C’ ratio is greater than 0.15, the bearing is regarded as heavily loaded, and special lubricants with extreme-pressure additives will be required to increase the load-carrying capacity of the bearing and to prevent metal-to-metal contact, which leads to high wear and premature bearing failure. Generally, a P/C of less than 0.15 for radially loaded bearings using standard lithium soap greases (normal operating conditions) is 400,000 min-1.mm.
It is also important to keep the ‘P/C’ ratio above 0.02, as, in general, below this value the bearing will ‘skid’ rather than roll, again resulting in possible premature bearing failure due to high wear and an increase in friction. To avoid slippage with caged ball bearings, engineers should work on a P/C of 0.01, and for caged roller bearings, a P/C of 0.02 is advised.
Secondly, the ‘ndm’ value, which is calculated from the speed of the bearing ‘n’ in revs/min and the bearing mean diameter ‘dm’ in mm, will give an indication of the relative speed of rotation to the physical size of the bearing. In general, if the ‘ndm’ value is below 400,000 standard general-purpose bearing greases can be effectively used to lubricate the bearing. For ‘ndm’ values in excess of this, special greases that have relatively low base oil viscosities are required, in order to reduce the amount of heat generated by the bearing when rotating at higher speeds. It is quite possible, with recent developments in both bearings and grease lubricants, to achieve ‘ndm’ values of up to 2,000,000.
While grease lubrication is inherently simple, there are many bearing applications where oil is the only choice available, since it has the key attribute of being able to remove the heat generated in the bearing due to load and speed. It is quite possible that ‘ndm’ values up to 4,000,000 could be achieved with oil-jet lubrication.
Schaeffler’s Arcanol range of rolling-bearing greases provides optimum conditions for achieving reliable, durable and cost-effective bearing solutions.
The company works closely with lubricant manufacturers to develop special greases that are suitable for rolling bearings. Schaeffler conduct a series of stringent in-house tests on the lubricant to determine service life, friction and wear characteristics. Only the best-performing greases are selected to undergo subsequent tests under simulated field conditions in far more complex rolling-bearing test rigs. If the grease fulfils Schaeffler’s stringent tests, it is awarded the Arcanol seal of quality. In addition, each incoming batch of grease is 100% inspected by Schaeffler to ensure the uniform quality of the product.
The Arcanol range includes 15 rolling-bearing greases, each graduated to cover all application areas. For example, MULTITOP is a universal grease for ball and rolling bearings that is suitable for use in construction machinery, automotive engineering, rolling mills and grinding machine spindles; VIB3 is a mineral-based grease with a polycarbamide thickener that offers excellent resistance to high temperatures, high loads and oscillating motion; while MULTI3 is a specially formulated grease for large electric motors and fans.
Re-lubrication equipment
In harsh operating conditions or aggressive environments, rolling bearings should be re-lubricated frequently via lubrication nipples. Schaeffler, therefore, offer their FAG grease guns and matching reinforced hoses for this purpose, which allows rapid manual re-lubrication of bearings.
However, controlled re-lubrication of bearings is often required in order to extend service and maintenance intervals and minimize plant downtime. Schaeffler offer three main products for this:
- Motion Guard COMPACT – a single- point electro-chemical lubrication system that comprises a housing filled with 120cm3 of grease, controlled via an activation screw.
- Motion Guard CHAMPION – a single- point battery-operated lubricator that comprises either a 120cm3 or 250cm3 volume of grease, with drive unit and adaptor.
- Motion Guard CONCEPT 6 – an electromechanical single-point lubrication system that can be expanded to include up to six lubrication points.
FAG metering devices are also provided, allowing customers to supply grease to rolling bearings in metered quantities, from 10cm3 up to 133cm3. Using a pneumatically driven, double-direction piston pump, the lubricant is transferred from the grease drum (25kg or 180kg), via the metering valve, to the point of application.
Case study: Bearing lubricators save up to €450,000 per year at cement quarry
By investing in an intelligent lubrication system for vibrating screen bearings, a crushed rock producer in Austria is saving up to €450,000 per year in maintenance costs and production downtime.
Located in Bad Deutsch-Altenburg, Hollitzer Baustoffwerke Betriebs-Gesellschaft mbH are part of the CEMEX Group. The Hollitzer quarry employs around 30 staff and specializes in crushed rock production for ready-mixed concrete.
The quarry uses a combination of double- and single-deck circular vibrating screens to grade the feed rock prior to crushing. In the past, these vibrating screens caused problems at the plant and frequently had to be shut down due to bearing failures caused by insufficient bearing lubrication.
The latest vibrating screen was installed at the quarry in August 2006. After only a short time in operation, this machine suffered a bearing failure due to insufficient lubrication. The bearings themselves support the screen arms, which have to perform heavy and continuous oscillating movements. The screens also have to withstand the harsh, dusty conditions.
At this time, Hollitzer contacted FAG Industrial Services (F’IS), the maintenance and condition monitoring company within the Schaeffler Group, to recommend a course of action for the bearings. In December 2006, F’IS agreed to install an FAG Motion Guard CONCEPT 6 automatic lubrication system on one of the vibrating screens at Hollitzer. This unit served a six-month trial in order to prove the solution would work and the potential savings it would provide. The unit was mounted in a protective housing and filled with Schaeffler’s recommended Arcanol MULTITOP grease in a 500cm3 canister.
As mentioned earlier, the FAG Motion Guard CONCEPT 6 is an intelligent lubrication system which can be used for either single- or multi-point lubrication. The system can supply up to six different lubricating points with grease and can lubricate a wide range of bearings and applications, including rolling bearings, plain bearings, drive chains, guides, conveyor chains and open gears.
At Hollitzer, the CONCEPT 6 trial demonstrated that significant time and cost savings could be made if the quarry installed lubricators on each vibrating screen. Prior to installing CONCEPT 6, bearing failures at the site averaged between four and six a year. Each bearing failure required a bearing replacement, which meant the plant had to be shut down for one complete shift (10h). With a machine-hour rate of €2,000, a 10h bearing replacement cost the plant around €20,000. In addition, loss of production (approx 6,000–7,000 tonnes per day) was estimated at €70,000, resulting in a total cost for one bearing failure of around €90,000. For an average of five bearing failures in one year, the total cost was €450,000.
Well suited to extreme applications, CONCEPT 6 can be used both indoors and outside. Each system within the series discharges individual and precise amounts of lubricant over extended periods, removing the need for costly central lubrication systems. CONCEPT 6 is also fully automatic and maintenance-free thanks to constant re-lubrication, resulting in longer bearing life, longer maintenance intervals for machinery and considerable cost savings for users.
‘Almost 50% of all bearing damage is caused by insufficient or incorrect lubrication,’ commented Steve Lacey, engineering manager at Schaeffler (UK). ‘This can be very costly for businesses as bearing damage often results in unscheduled downtime, which in turn can result in loss of production and repair costs that often amount to tens of thousands of pounds. This kind of damage can be prevented by using automatic lubricators such as the FAG Motion Guard line.’
FAG Motion Guard CONCEPT 6 is easy to programme using two push-buttons and features an accurate and easy-to-read LED function light which displays lubricant level. The system can be used in operating temperatures ranging from –20°C to +60°C with a maximum counter pressure for each system of 25 bar for longer distances.
Each model has an electromechanical drive system housed in a robust metal unit. Available in battery-powered or machine-controlled options, CONCEPT 6 comes with either 250cm3 or 500cm3 lubrication canisters.
Used in conjunction with the FAG Easy Check rolling bearing monitoring system, CONCEPT 6 (battery powered) and CONCEPT 6 Control (machine controlled) can be used as a complete, reliable safety package for critical bearing locations. These independent systems are fully compatible and can be connected directly to the lubricating point.