Second Chance
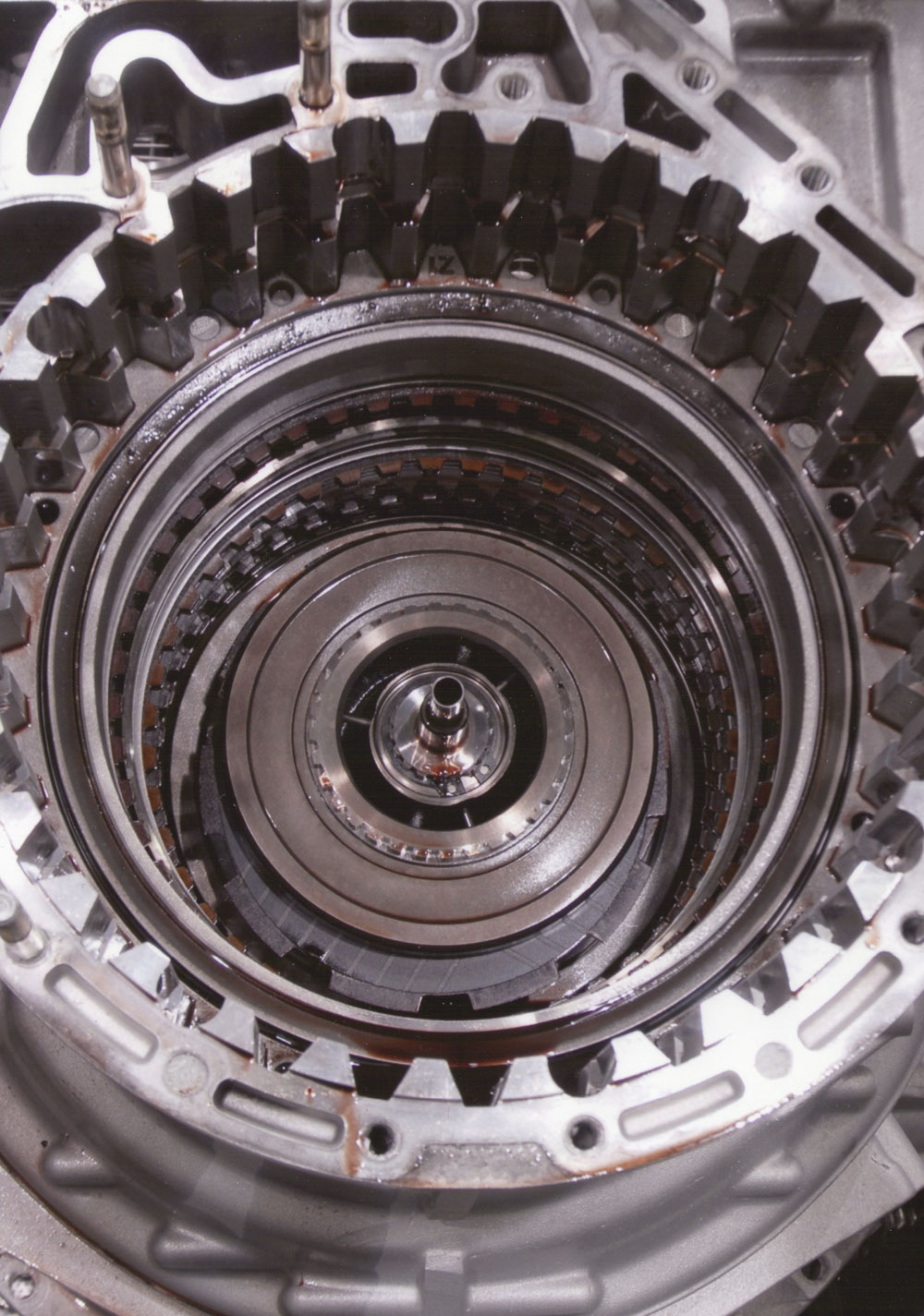
Taking the remanufacturing approach could help plant operators overcome the current economic crisis
It is safe to say that the current global recession has hit the off-highway vehicle market hard. First, with the credit crunch affecting the previously buoyant construction industry, there is now a declining demand for plant and equipment; and secondly, the reduced availability of capital loans from banks means vehicle operators are finding it difficult to purchase new equipment.
According to ZFGB, such depressed market conditions require the adoption of a different operating strategy – one of mend rather than replace. In the off-road vehicle market this is achieved by the process of remanufacture, which, when undertaken properly, can extend vehicle life substantially.
In more buoyant times, remanufacture tends to be less favoured than buying new. However, a recent study estimated that the total annual turnover of remanufacture businesses in the US is over $50 billion, and possibly even more in connected industries. It also reported that the sector directly employs around 500,000 people.
Interestingly, the same study concluded that remanufacturing in the UK is making a significant contribution to materials efficiency, claiming that ‘this unrecognized sector contributes around £5 billion to GNP; recovers around 270,000 tonnes of materials with an equivalent carbon saving of around 800,000 tonnes; and employs around 50,000 people.’
In addition to the environmental and economic benefits, remanufacture makes sense at the micro level for users. First, it is a proven way of extending asset life considerably. Secondly, it is less expensive than buying new, helping companies to preserve capital in adverse trading conditions. Thirdly, the updates that can be implemented to key equipment, such as transmissions, during the remanufacturing operation, mean that the vehicle is often more efficient than before. Fourthly, although more relevant in an expanding market, remanufacture is a major method of avoiding long delays for new plant and equipment.
Remanufacture should not be confused with repair; it is far wider in scope and differs from other recovery processes. A remanufactured unit should meet the same customer requirements, receive all of the improvements and have the expected life and warranty of a new machine.
At ZFGB, the remanufacturing process starts with a vehicle transmission fully stripped to component level. All parts are then cleaned and inspected to factory standards. Any parts that need replacing will be genuine ZF parts built to OEM standards.
New bearings and any product updates or improvements are also part of the remanufacture programme. The transmission is then reassembled to OEM standards, followed by a test to ensure that it operates in accordance with factory specifications.
Importantly, remanufacturing effectively addresses the issue of genuine parts and cost. However, what must be taken into consideration is that, when ZFGB designs and manufactures a transmission, all the parts used provide a synergy of operation, each one playing a key part in achieving the overall calculated service life of the transmission. If a third-party reconditions the unit using cheaper non-genuine parts, this synergy is lost and the performance of the transmission is compromised.
The other major issue associated with genuine parts is safety. The litigation culture that pervades society today means that an operator using parts not recommended by the manufacturer could be liable should an accident occur.
A further safeguard essential for remanufactured transmissions is testing. Increasingly, the investment required for comprehensive in-house testing is generally beyond the scope of third-party repairers. At ZFGB, every remanufactured transmission unit is tested for up to 6h on a purpose-built test rig. It is then delivered back to the customer, complete with a warranty.