Remanufactured Transmissions
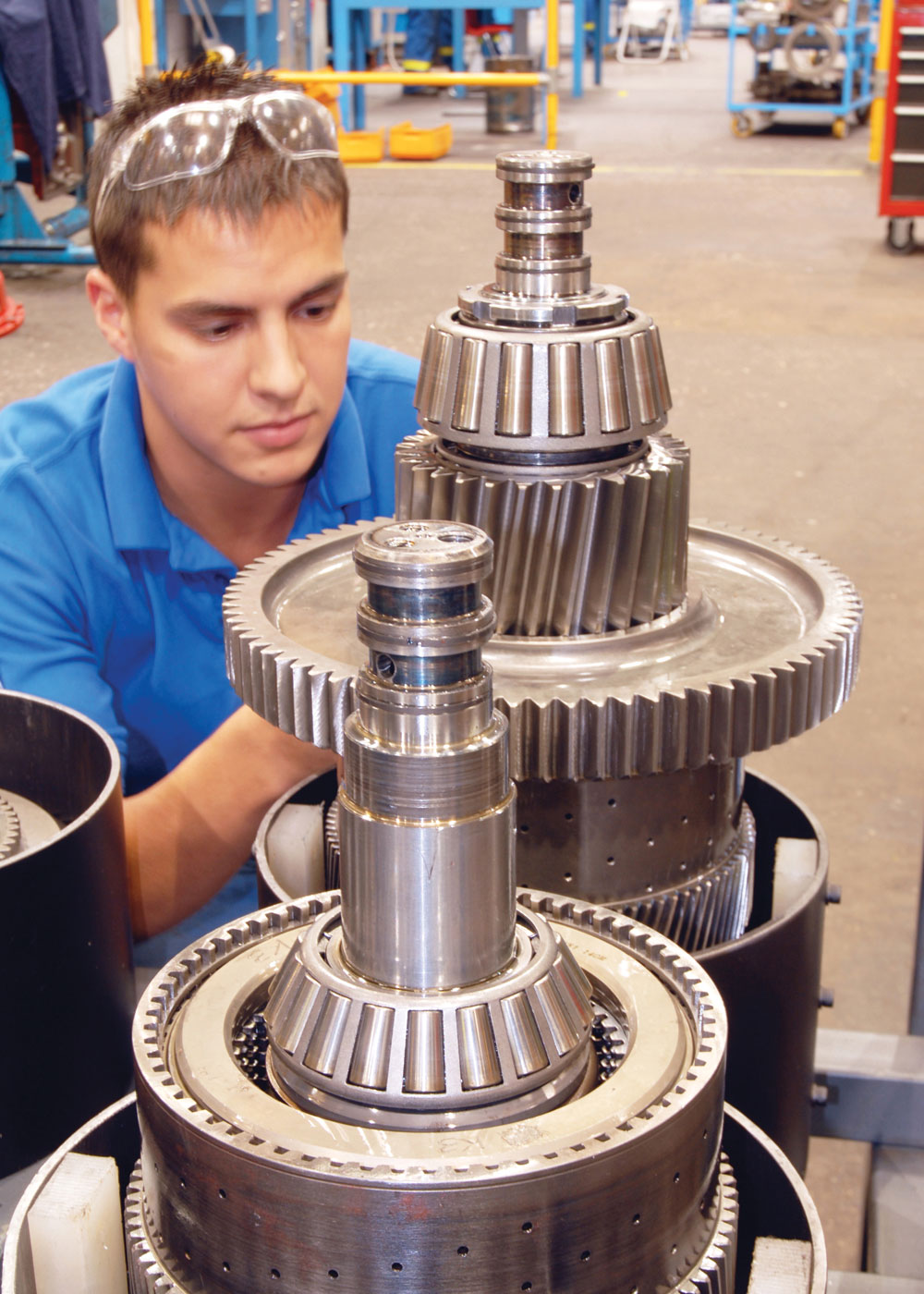
How to get the most out of your mobile plant assets
By Mike Goatley, sales manager, ZF Off-Highway Division
For companies seeking to gain maximum utility from their mobile assets, the remanufacture of transmissions is a proven way of extending asset life considerably. In addition, the updates that can be implemented during the remanufacturing operation mean that the transmission is often more efficient and flexible, and offers more facilities than previously.
To markets that have traditionally relied on repairs, remanufacture is something new that suggests higher cost. This is true; remanufacture is more comprehensive in its scope and is, therefore, more expensive than repair. However, cost is relative; if a fleet of trucks is standing idle because of a transmission failure on a loading shovel, then the cost of refurbishing the transmission against the cost of the lost productive time of the other vehicles is minimal.
Repairs are something that all quarry managers are well used to and comfortable with; but by pausing for a moment to consider the narrow definition of the word, it is easy to appreciate why more and more operators are adopting remanufacture instead. Repair generally means rectifying the part, or parts, that have gone wrong. In the field under pressurized working conditions, this means quick replacement of components that have failed. However, this takes no account of what caused the failure initially. Consequently, a failure may be rectified with a repair, only for it to occur again due to the original cause not being identified and put right.
But it does not have to be this way; ZF off-highway transmissions, for example, are equipped with electronic black boxes (TCUs), both to optimize transmission operation and to record operational data. The TCU is provided with an error memory that allows it to record faults occurring on the transmission system. This means that when a transmission failure happens, the TCU records the cause of the fault, and when the transmission is removed subsequently, this data is retrieved, which means that not only is the failure identified, but also its not-so-obvious cause. As a result, a more comprehensive refurbishment regime can be applied to ensure both problems are eliminated.
Experience gained from recording and analysing fault data in this way has convinced ZF that the remanufacture process is far more comprehensive and offers greater benefits to the off-highway vehicle operator than simple repair.
This message has already been heeded by a number of major off-highway vehicle manufacturers, who ship failed transmissions directly back to ZF and receive fully remanufactured and tested ones in their place. The major benefit of this procedure is that it reduces the overall time the off-highway vehicle is standing idle and is far more cost-efficient overall for the vehicle operator (see box 1).
Compared to a new aftermarket transmission, remanufacture is around one third to one half of the cost; a saving that can make manufacturers, who often face long lead times for new equipment, review their options. The process of remanufacture entails a unit being fully stripped to component level; all parts are then cleaned and inspected to factory standards, and any parts that need replacing are exchanged for genuine parts to OEM standards. New bearings and any product updates or improvements are also included in the remanufacturing programme. Units are reassembled to OEM standards and then fully load tested by ZF to ensure that they function in accordance with factory specifications.
Remanufacture offers the user many safeguards; first a total quality management (TQM) programme run by ZF ensures that the job is always done ‘right first time’. Secondly, remanufacture addresses the critical issue of genuine parts. To many operators the policy of using non-standard parts in repairs is acceptable due to cost savings. This policy is flawed, however, because many non-genuine parts are designed using reverse engineering. This is because manufacturers of such components do not have access to original designs. As a result, many non-genuine parts are designed and manufactured from inferior materials and with poor tolerances. In contrast, when ZF design and manufacture a transmission, the parts used provide a synergy of operation – all play their part in the overall calculated life of the transmission. If, in the event of a failure, cheaper non-genuine parts are used in the transmission, this operating synergy is lost and the vehicle operator has no warranty to fall back on (see box 2).
The third remanufacturing safeguard is safety. If operators are using parts not recommended by the manufacturer, they could find themselves in trouble if an accident occurs and those parts are highlighted in any subsequent investigation.
The fourth safeguard is testing; repairs undertaken in the field generally cannot be tested, and the investment required for comprehensive in-house testing by non-manufacturer repairers is usually beyond the scope of their resources. This is not the case with manufacturers such as ZF, where every remanufactured (and repaired) transmission unit is tested for up to 6h on a purpose-built test rig. Only then is it deemed ready to be shipped back to the customer, complete with a ZF warranty.
This is not quite the end of the story, however, as ZF have also considered the question of what happens when a remanufactured or repaired transmission is reinstalled. This has resulted in the introduction of an optional service of installation check, to obviate any post-installation problems. The service is designed to optimize shift quality and clutch life; it is crucial to perform this upon reinstallation of the transmission because of the requirement to ensure that the clutch fills at the optimum rate for smooth shifting.
Also included in the service check are transmission mountings, propshafts, engine connections and the operation of any direct interlocks or other safety functions. In addition, the ZF service engineer will install the latest updated software in the transmission control unit, ensuring maximum operating efficiency for the vehicle user.
Box 1 - Case Study: JCB team up with ZF to cut costs and downtime
JCB have teamed up with ZF to offer the next-day supply of replacement transmissions for their range of wheel loaders, dumptrucks and wheeled excavators. The service exchange principle is straightforward; when a transmission part is damaged or wears out and requires replacement, JCB dealers can now offer a service exchange unit ‘off the shelf’, ensuring that the vehicle is not out of action for long periods of time.
A service exchange unit is guaranteed to have been remanufactured by the OEM and carries the same guarantee as a brand new unit; it is also likely to be considerably cheaper than a brand new unit (up to 50% cheaper in some instances).
Mike Goatley, sales manager of ZF Great Britain’s Off-Highway Division, said: ‘The service exchange scheme introduced by JCB is similar to other major vehicle manufacturers in that we take ultimate responsibility for the item. Beyond the quality issue, the benefits to the end user are massive, particularly in faster repairs and maximized uptime.’
Unlike many other repairers, ZF have complete traceability of the transmission, from the day it leaves the production line to the day it is reinstalled after remanufacture. This ensures that any technical updates issued since the introduction of the transmission can be retro-fitted to the remanufactured unit.
All ZF components fitted to JCB equipment, including transmissions, transaxles and associated equipment, are kept ‘on the shelf’ at the JCB World Parts Centre in Staffordshire, by JCB dealers, or at ZF Great Britain in Nottingham. The items are available as immediate replacements when worn or damaged units are sent in by operators or approved repairers.
Guy Robinson, director and general manager of JCB Service, commented: ‘At JCB we understand the importance to our customers of maximizing the productivity of our machines, and that is why we carry over £1 million of service exchange stock. We routinely keep replacement parts for vehicles that went out of production over
10 years ago, ensuring that JCB machines, both old and new, are supported.
‘Off-highway vehicles are hard-working and valuable machines, and the real cost of them not being available is significant. To a contractor it means added pressure on meeting contract deadlines; for owner-operators, hire companies, lease hire companies and large fleet operators, the cost of having a machine out of service can amount to hundreds or even thousands of pounds a day. Because a service exchange part is always available, JCB units can be restored to full working order in the minimum time possible.’
And while environmental concerns may not be the first consideration of a site foreman or plant hire fleet manager when a vehicle is out of service, JCB say the additional environmental benefits the service exchange offers are very important, as recycling major components through the scheme reduces the impact of manufacturing new parts on natural resources and the inevitable energy usage involved in manufacturing from scratch.
Box 2 - The case for genuine manufacturers’ parts
Using genuine manufacturers’ parts in off-road vehicle transmissions is vital for maximum profitability and performance. Buying components that fail quickly or do not perform as efficiently and cost-effectively as those specified originally is clearly more costly than genuine parts that last and do the job perfectly.
However, is this always the case? Should companies reduce their costs by using alternative parts? Are manufacturers simply trying to maximize their profits by insisting that only genuine parts should be used?
According to ZF, it really is best to use original parts; they say costs are rarely reduced by using non-genuine parts and, in some cases, customers could end up paying more due to premature failure of the components concerned.
It has been demonstrated time and again, say ZF, that genuine parts deliver the lowest operating costs per hour and the best profitability and performance to the customer, simply because they have been specifically designed for the task that they are required to perform. Despite these arguments, however, the replacement of genuine components with non-genuine parts continues.
ZF say it is paramount for operators to ensure that replacement parts keep a machine functioning at the same level of performance as previously. If this requirement is not fulfilled, then the fault and the cost of premature failure lie squarely with the customer.
To avoid such problems, ZF design their transmissions with parts that are optimized on a materials, heat treatment, mechanical design and lubrication platform, to provide efficient and reliable operation. If cheaper, non-genuine parts are used in the transmission, the operating synergy is lost and the vehicle operator will not have the support of a manufacturer’s warranty to fall back on.
There is also the key issue of servicing; transmissions that use only genuine manufacturer parts are far easier to diagnose from a servicing viewpoint when problems arise. The transparency of the life of the transmission means that problems can be pinpointed more quickly, helping to safeguard the operator from the potentially crippling cost of vehicle downtime.