Metso Rebuild Primary Crusher for Norwegian Company
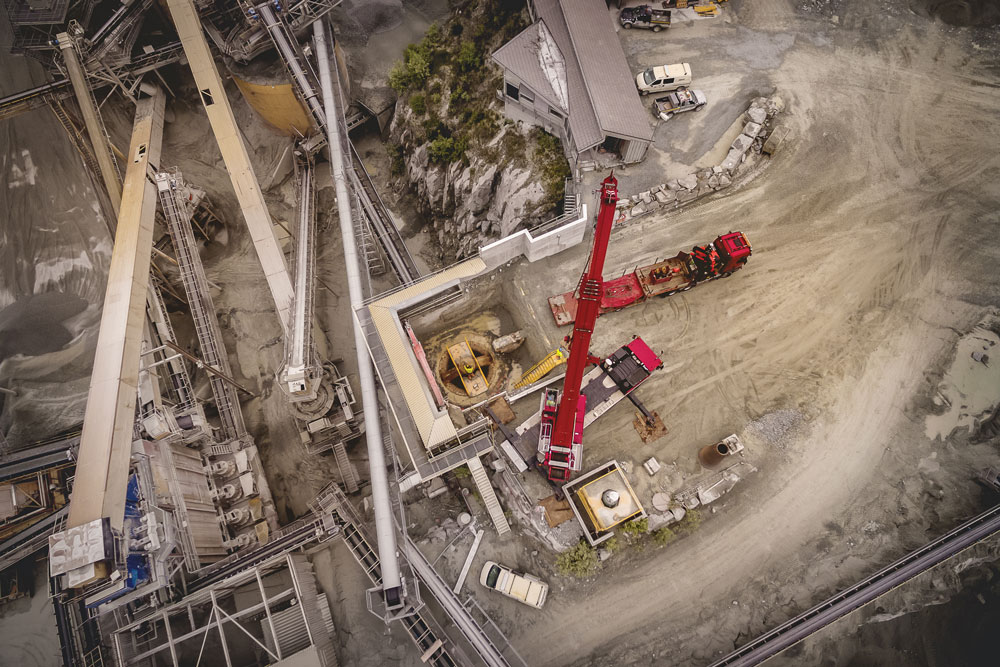
First published in the May 2017 issue of Quarry Management as Seamless Collaboration
Metso rebuild results in 30% drop in primary crusher power draw at Norstone Tau
When an investment in brand new equipment is not feasible, a rebuild is an option that can also result in significant improvements. This was the case at Norstone Tau in 2012. Located on Norway’s south-west coast, near Stavanger, Tau is the largest Norstone plant in the country. Half of the quarry’s production is shipped for export, while the rest is sold in Norway, with the biggest customers being asphalt producers.
The primary gyratory crusher had seen its best days and was consuming excessive amounts of power. The quarry was looking for ways to boost short-term production capacity, and the primary could not keep up. But a bigger expansion was also on the horizon, and likely to include an investment in an in-pit primary crushing solution in five to seven years time. So, how best to solve the interim bottlenecks?
Norstone decided to call on Metso’s knowledge to assess the situation. The existing primary crusher, a Svedala Superior 54-74, had been commissioned in 1984. After careful evaluation, the decision was made to replace the spider, the top shell and the bottom shell.
Due to the nature and scope of the project, Metso experts frequented the site to share experiences and discuss requirements with Norstone. Countless hours of measuring, drawing and designing ensued. Metso had to work out how to increase the crusher’s capacity while reducing the power draw. The final element, wear part design, also played a key role in the outcome of the project.
Thanks to detailed planning and seamless co-operation between the two parties, the removal of the old parts and the installation and commissioning of the new components was completed in less than four weeks during a pre-planned shutdown in late 2014.
‘We have always had good collaboration with Metso. You can really see that the people visiting us are highly skilled, they know what they are talking about, and they’re actually offering us valuable advice,’ said plant manager Marie Reumont.
According to Norstone Tau, the results speak for themselves. The average power draw during operation has dropped from 250kW to 170kW, while the average capacity has gone up from 900 tonnes/h to 1,260 tonnes/h at a 47% load.
According to Ms Reumont, the concave segments now last for about 2.4 million tonnes, which was also the goal. At first, Metso were on site every three months to help track and monitor wear, and to establish a routine.
But the real work of optimizing and fine-tuning is only just starting. ‘I think that there is always room for more improvement, however small, so we will keep monitoring this and working to maximize the optimization,’ said Ms Reumont.
‘And because the results with Metso have been very good, we are looking into the possibility of further improvements on other machines,’ she continued.
First up for optimization is the secondary crusher. Because this cone produces a finer product, the goals for optimization are somewhat different. Lifetime extension is not enough; the quality of the end product is another crucial parameter. ‘We are pleased that Metso have understood our needs so that we can work together in that direction,’ she concluded.
- Subscribe to Quarry Management, the monthly journal for the mineral products industry, to read articles before they appear on Agg-Net.com