Keeping The Process Moving
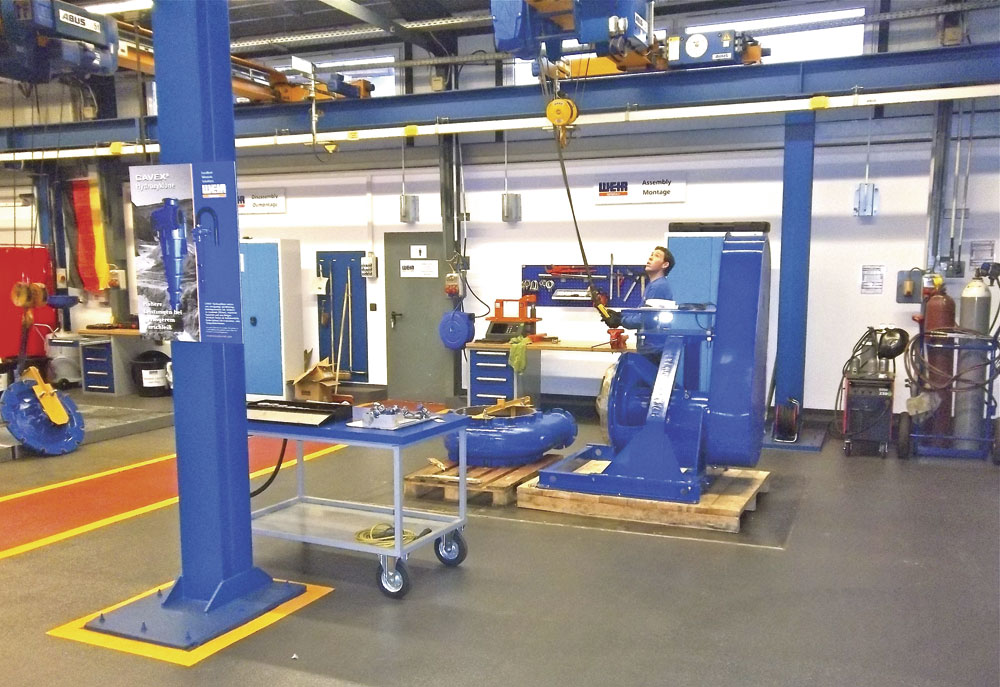
Wet processes in quarrying operations unavoidably expose process equipment to a great deal of wear and tear. Paul Brooks, European service support manager with Weir Minerals Europe, outlines the critical importance of good repair and maintenance strategies in minimizing downtime and boosting productivity.
For any aggregate extraction operation to be carried out effectively, it is critical that every stage in the process runs with maximum efficiency and reliability.
There have been rapid technological advances in areas such as materials science and mechanical and electrical design and engineering, and this has seen dramatic improvements in the efficiency and lifespan of process equipment, as well as in ease of access to key parts to allow quick and easy maintenance and repairs.
However, equipment design is only part of the story, and the highly demanding applications performed by quarrying equipment will mean that the system will always be subject to wear and tear – so it is equally important that the correct repair and maintenance strategies are in place.
Nasty surprises?
Historically, the vast majority of process maintenance within quarries has been carried out on a purely reactive basis, but there are a number of disadvantages to this approach. First and foremost among these is that it effectively means accepting that failures in the system will inevitably happen during the lifespan of the project.
It is important not to underestimate the significant impact that the failure of even a simple piece of equipment can have on the bottom line. Many modern processes run end to end, with flow rates at every stage carefully calculated to ensure that material flows through the system without either excessive build-ups or the need to frequently stop and start equipment to control throughput.
In such carefully balanced processes, a failure at any stage will therefore halt the entire process and have a direct impact on bottom-line production. The duration of the resulting period of downtime can vary significantly depending on whether it is immediately apparent what has caused the problem, how long it takes for qualified personnel to reach the site, the scale of the repairs required and the availability of replacement parts.
In the most serious scenarios, failures can cause processes to be down for several days, with serious implications for the profitability of the operation. So what can be done to minimize the occurrence of these crises?
Prevention rather than cure
By far the best way to mitigate the impact of failures is to put a proactive maintenance programme in place to minimize the chances of them occurring in the first place. By scheduling regular system checks the condition of critical parts can be tracked over time allowing replacements to be made before excessive wear leads to a failure.
Although checking the condition of internal parts, such as a pump’s impeller and lining, may mean taking the pump out of action for a brief period, well-managed scheduled procedures require much less downtime than an unexpected reactive repair.
How frequently these internal checks are carried out should be informed by a good knowledge of the average optimal lifespan of critical parts under given conditions and levels of operation. This will ensure that checks are performed often enough to guard against unexpected failure, but infrequently enough to keep downtime to a minimum.
There is also a wide range of checks that can be carried out during operation which will alert operators to any potential problems without interruption to the process. These include measurements of flow rates through key parts of the system, the energy consumption of pumps, and temperature and vibration measurements on any moving parts. Monitoring these for changes over time will give a good indication of the health of the system and provide an early alert to any potential problems. It is also important to regularly check and, if necessary, adjust mechanical seals – particularly the glands that maintain the seals around the drive shafts of pumps.
Naturally, the scale of the proactive maintenance programme that is needed will vary significantly between different types of application and different scales of operation. Establishing the right level of monitoring or frequency of scheduled checks for any given process is key to striking the right balance between achieving peak reliability and over-spending on unnecessary maintenance.
There is no standard approach, as conditions and systems vary so much from site to site and different operations have widely differing demands in terms of performance margins.
Taking ownership
One of the key questions that needs to be asked when planning a maintenance programme is who will perform the checks and accept responsibility for them being carried out properly.
Traditionally, the relationship between quarry operators and their equipment suppliers was purely transactional – with the client taking full responsibility for the performance and maintenance of any equipment. However, aftermarket support has become much more important in today’s minerals processing industry and increasingly clients are looking to their equipment suppliers to provide ongoing maintenance support and take responsibility for the optimal performance of systems.
This shift has meant a marked change in the way many suppliers interact with the customers, as providing an effective repair and maintenance service means being able to regularly attend sites to provide scheduled support and also to respond rapidly if reactive repairs are required. Relationships that operate in this way are much more challenging to run from a distance, and virtually impossible without an effective team of reactive repair engineers stationed relatively nearby. Having quick-response teams on the ground ready to attend to any issues can be a very expensive proposition, significantly adding to the challenge of competing with other suppliers with a local presence.
Case study: Sibelco
One example of how changing the nature of the client/supplier relationship can lead to improvements in performance came recently when Weir Minerals began working with the UK operation of international minerals business Sibelco.
Sibelco are one of the world’s leading industrial minerals companies. Originally established in Belgium in 1872, the company today operates 228 production sites in 41 countries with a team of around 10,000 people. Sibelco extract and process a diverse portfolio of non-metallic minerals for a broad range of industries.
A particular specialism of the company is the production of high-quality silica sands; Sibelco being a global market leader in this sector. In the UK, Sibelco operate 14 sites and employ around 500 personnel, with a major focus on clays and refined sands for the ceramics, glass, foundry, sport and leisure, and paper industries.
As with virtually all mining processes, Sibelco’s extraction operations in the UK involve the intensive use of pumps at every stage of the process. When Weir Minerals first spoke to a representative of the business, it was reported more than 70 unplanned pump-related interruptions to processing were taking place each year. This was building significant inefficiencies into the process and having a substantial impact on the bottom line.
It was clear that the fundamental cause of the issues was the nature of Sibelco’s relationship with their pump supplier, who was providing no after-sales support. Beyond delivering the requested equipment, the supplier had no further involvement in its application or operation.
The stock was wholly owned by the customer, placing the entire cost of the inventory of pumping equipment on its books. As well as this, there were no formalized performance incentives in place, so all risk effectively sat with Sibelco.
As a trial run, Weir Minerals proposed to take responsibility for Sibelco’s stock across the firm’s three Devon sites. A full audit was carried out of the existing equipment in use to determine its condition and suitability for purpose. This formed the basis for a transition strategy to replace stock where necessary and bring all equipment under Weir Minerals’ management. A performance clause was incorporated in the arrangement, ensuring that Weir Minerals’ engineers had the same objective as the Sibelco project team – minimum downtime and maximum efficiency.
The strict maintenance regime delivered a drastic and immediate increase in mean time between failure (MTBF) – the key indicator of pump reliability. This translated into reduced downtime, delivering a significant increase in production across the sites. As a result of this success, three months into the contract Sibelco approached Weir Minerals with a view to having them take over the management of pumps at a further four sites across the UK.
After replicating the performance gains at these sites over the following 12 months, Weir Minerals were appointed to manage Sibelco’s pump fleet nationwide.
In the 12 months after Weir Minerals took responsibility for performance across Sibelco’s operation, their teams attended just seven breakdown situations, representing a tenfold improvement in performance levels at the outset and a clear demonstration of the benefits of well-structured and managed proactive maintenance regimes.
Going forward
The nature of the UK quarrying industry – with a large number of small suppliers across the country catering for local requirements – can mean that innovations are slow to catch on across the board and many quarries still source their equipment on a transactional basis.
While this may be working well for these businesses, it is important that operators of all sizes are aware of the services now offered by the pump supply industry in terms of proactive maintenance and monitoring, and the cost benefits these strategies can provide.
The commercial and environmental benefits of keeping processes operating at peak performance are clear. However, for many of the managers Weir Minerals work with, the biggest draw of a proactive approach is peace of mind that the process is in good shape and that an unexpected and expensive repair is not going to cause chaos on site.
For further information visit: www.weirminerals.com