Extracting Maximum Bearing Life in Quarrying Machinery
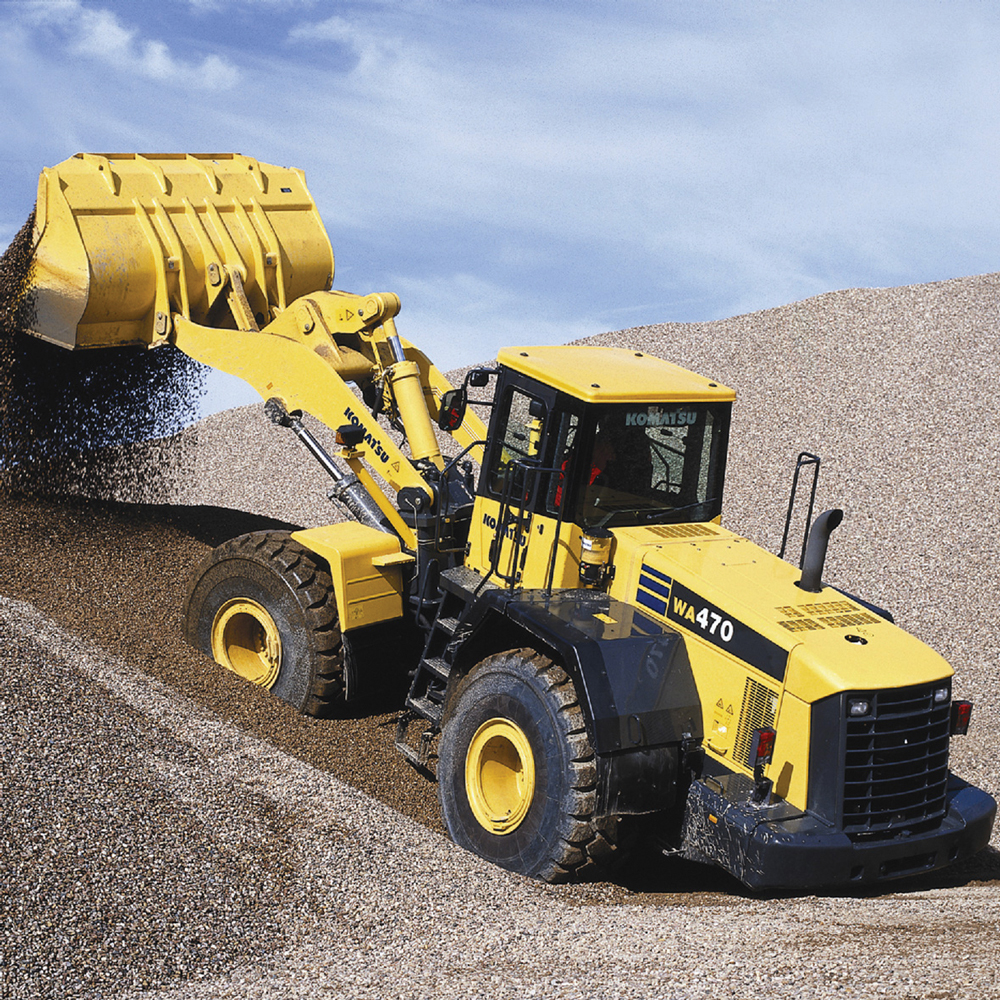
First published in the November 2016 issue of Quarry Management as Extracting Maximum Bearing Life
Dean Askew, bearings product manager with Brammer, and David Oliver, channel and platform manager for bearings and units at SKF, look at the demands placed on quarrying machinery and the components that ensure peak performance across a site
Dust, grit, water, temperature extremes and vibration are the norm in quarrying environments, and all too often these are aggregated together under the label ‘harsh conditions’ when specifying equipment. In truth, each piece of machinery or internal component experiences these conditions to a differing degree and, as they perform varying roles, requires a different set of characteristics to withstand them.
In contrast to the highly controlled and often sterile environment of a modern manufacturing facility, mining and quarrying applications have a host of challenges to withstand – from the unpredictability of the outdoor elements, the nature of the materials themselves, to the heavy-duty machinery required to extract, crush and process minerals. As each of the individual assets used in these environments perform different tasks and are made up of distinct components, it is difficult to rely on a ‘one size fits all’ approach to their specification and procurement, and nowhere is this better illustrated than with bearings.
Facilitating the very low frictional movement necessary for rotating equipment, bearings are essential in a host of mining machinery and applications. To function properly they must be well lubricated, free from contamination, cool and stable – all at odds with the rain and quarry process water, abrasive grit, high temperatures, shocks and vibration common in quarry environments. A variety of solutions exist to enhance bearing life in such applications, each individually tailored to particular demands.
Conveyors are one example of a demanding quarry application. They must withstand the weight of excavated aggregates and minerals, and operate in conditions which can vary between dry and dusty, and wet and dirty, often in remote or inaccessible areas of the site. Approximately 51% of bearing failures are said to be due to contamination and ineffective lubrication, so good sealing and a reduced need for relubrication can help avoid these failure modes.
The chosen bearings must also be able to cope with misalignment or shaft deflections associated with this type of application. Spherical roller bearings are, therefore, the ideal choice in this situation. Upgraded SKF Explorer spherical roller bearings have a patented heat treatment that provides a harder, fine-grained structure that performs particularly well in contaminated or poorly lubricated conditions. These bearings can additionally be equipped with contact seals fitted in recesses in the outer ring, which helps retain the grease and guards against contamination.
For optimal protection, a sealed spherical roller bearing can be combined with a plummer block housing containing taconite seals and a grease fill in the housing cavity to create a three-tiered system which puts up multiple barriers against contaminants – the ultimate SKF three-barrier solution.
Crushers also benefit from the application of spherical roller bearings, having to cope on a daily basis with heavy loads and structural movement. If a crusher bearing fails prematurely, downtime costs can begin to mount up, so the robustness of a spherical roller bearing coupled with the option to seal out contamination can increase working life and reduce maintenance. For some applications, however, even these bearings have needed to evolve to meet more demanding needs – particularly those of vibrating screens. Here, specific spherical roller bearings for vibratory applications have been developed. One variant features a polytetrafluoroethylene (PTFE, often known by the brand name Teflon) coated bore which virtually eliminates the common issue of fretting corrosion between the shaft and the bearing bore. These bearing designs can also operate at much cooler temperatures, which in turn can double the relubrication intervals, while vibration-specific bearing types will extend service life and maintenance intervals whilst also improving safety.
Vertical roller mills typically work under high temperatures and with high particulate concentrations, making them exactly the kind of machinery where maintenance is difficult. Bearings in such assets are often costly and large sometimes with an associated extended lead times for replacements. When specified, bearing rating life for mill rollers is greater than eight years, but actual service life can often be as little as three to four years with resulting damage such as rust, indentations and microcracks. Even at this point around 40% of bearings can be remanufactured with a potential reduced replacement cost and reduced time to repair, meaning that a valuable asset is available for production more quickly.
Mobile machines too use bearings, and work under arguably even more demanding conditions than static assets, as they not only hold, but must move greater loads. Shovels, draglines and excavators, including bucket-wheel excavators, place huge pressure on their bearings, with failure often causing processing to grind to a halt. Likewise, slewing bearings support very high loads combined with slow or oscillating movements and are vital for the performance and reliability of these assets.
Haul trucks are often the primary means of material transfer from shovels or excavators to crushers, so maintenance needs to be minimized and unexpected failures reduced to keep these valuable assets operational. One common solution applied across a number of positions is spherical plain bearings which reduce failures resulting from contamination ingress and poor lubrication.
While all machinery in operation in a mine or quarry operates in harsh conditions, it is clear that the sheer complexity of – and variance between – each asset means one type of bearing will not suit every application and careful specification must take place. To optimize the working life of a machine and reduce total cost of ownership, thorough life-cycle management of an asset is vital and most effective when undertaken with the support of specialist component manufacturers and expert authorized distributors. For further information visit www.brammeruk.com or www.skf.com/mining
• Subscribe to Quarry Management, the monthly journal for the mineral products industry, to read articles before they appear on Agg-Net.com