Bearing Failure: causes and cure
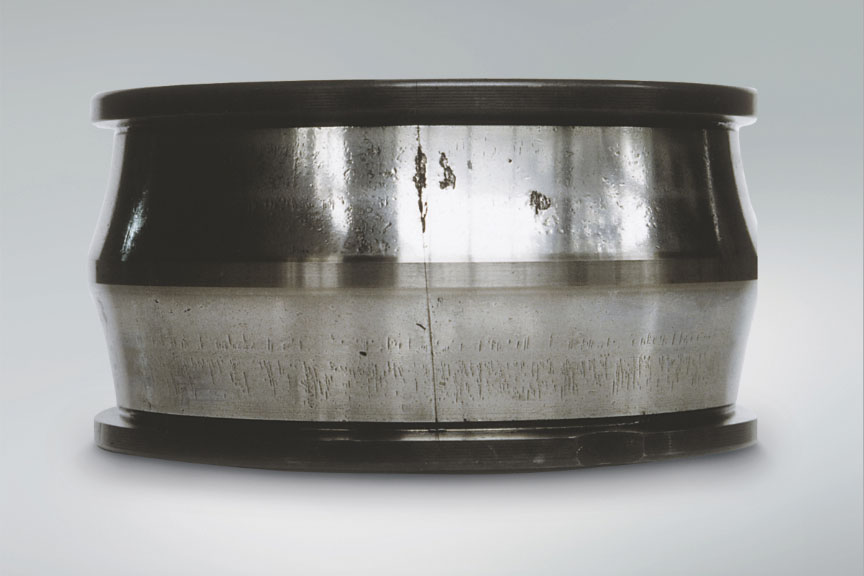
First published in the May 2017 issue of Quarry Management
Rolling element bearings are a key constituent part of virtually every rotating machine and, consequently, represent a significant cost for manufacturers. But bearings are one of the most frequently damaged components, as failure can be caused by a multitude of factors – from improper installation to particulate contamination. Brammer and NSK Bearings look at common types of bearing damage and how they can be prevented.
When smooth rolling surfaces are damaged, through cracks (fig. 1), wear, lubricant deficiency, corrosion or plastic deformation, amongst others, higher stress conditions are imposed upon the surface, significantly reducing the life of the bearing.
When roller bearings are used correctly, they will survive their predicted fatigue life. However, bearings often fail prematurely due to avoidable mistakes, such as improper mounting, mishandling, and poor lubrication, as well as the entry of foreign matter or abnormal heat generation. A bearing in the early stages of failure may display some or all of the following symptoms:
- Leakage or contamination of lubricant
- Component vibration
- Irregular noises
- Increased temperature above the norm when running
- Misalignment
- Unusual odours
When damage is initially suspected, further investigation will be required to determine the exact nature and, importantly, cause of the deterioration. As most types of damage can be prevented by correct mounting, lubrication and sealing, it is vital that a damaged bearing is not simply replaced without uncovering the underlying reasons, because if these are not rectified the cycle of damage will most likely continue.
Bearing damage is often attributed simply to ‘wear’. Wear is surface deterioration caused by sliding friction between raceway and rolling element surfaces. In most cases there is an adequate oil film between these surfaces to prevent damage, however this can change dramatically in the presence of contaminating materials. These typically enter a bearing through a faulty seal or contaminated lubricant, and can cause misalignment in the bearing, especially in tapered bearings where some surfaces will be subject to greater abrasion than others. A thorough clean before installation and effective lubrication management/filtration can prevent this. Slightly harder foreign particles, such as metal offcuts, dirt or grit, tend to cause pitting (fig. 2). These contaminants are usually caused by wear elsewhere in the machinery and, when carried through the machine in lubricating fluid, result in damage throughout the system. Again, replacing the bearing here will not resolve the issue as particles will continue to travel through the system.
Wear can also be generated if the wrong type of lubricant is used, which can result in a restricted oil film being present to keep the rolling surfaces apart. If a fluid such as water or solvent thins the lubricant, corrosion can occur.
There are several types of corrosion that can damage a bearing. Etching is caused by moisture entering a bearing through damaged seals, or as steam or condensate. Care must be taken when washing down equipment, particularly where wash-downs are frequent, and effective re-lubrication must take place immediately after thorough drying. Rust corrosion is most common on ring surfaces or rolling elements and can be caused by high temperatures and humidity when stationary, as well as the presence of water droplets.
Corrosion can also be caused by improper handling, so it is advisable to keep bearings in their protective packaging until just before usage and, where possible, to use protective lint-free gloves when handling bearings. Electrical corrosion (fig. 3) is caused by electric currents passing through the thin film of lubricating fluid found at the race and rolling elements of a bearing. The resulting burning can cause fluting or groove-like corrugations in the bearing surface, and can be prevented by fully insulating the bearing from surrounding instruments to protect against any electrical difference between the inner and outer rings, or electrical potential difference of frequency.
There are several other types of damage that can be caused by inadequate or insufficient lubrication, and these tend to manifest themselves through various stages of deterioration, meaning early identification could prevent a complete failure. The first stage is often discolouration (fig. 4) or staining due to a reaction of the lubricant at high temperatures, followed by peeling or flaking (fig. 5) as lubrication levels fall further and temperatures rise, causing small fragments of the raceway surface or rolling elements to become detached. If left untreated, cracks can develop, leading to irregular operation. These types of damage can also be caused by debris contamination or by incorrect mounting, so these factors, as well as lubrication management, should be assessed to prevent recurrence.
A number of types of damage can be put down to misalignment or incorrect mounting, which can be avoided with the use of a press machine, utilizing an appropriate jig or tool, and centring the relative mating parts during mounting. Mounting flaws can also cause cage damage (fig. 6), which includes, but is not limited to, deformation, fracture and wear to the cage, cage pillar, side face, pocket surface or guide surface. These problems can also be caused by large moment load, sudden acceleration or deceleration, excessive rotation speed, poor lubrication or rises in temperature.
Cleanliness at the point of bearing installation is also crucial in preventing damage. Dirt, grit or metallic particles in the housing can cause denting of the bearing raceway or rolling element surface. If denting is identified, the housing should be thoroughly washed, while the filtration system for lubrication should be checked and, if necessary, repaired. Denting at the ball or roller pitch is likely to be indicative of static impact damage. This can occur either through improper mounting – such as impacting the outer ring when mounting on the shaft or impacting the inner ring when mounting in the housing – or by static vibration.
Most types of bearing damage are easily avoidable if the bearing is installed carefully and maintained as part of a wider programme taking into account other system components. To simply replace a bearing that has failed without knowing the cause can prove to be very costly in terms of both time and equipment. It is always best to examine the system as a whole and identify the root cause of failure, as this method will provide a greater payback in the long run.
- Subscribe to Quarry Management, the monthly journal for the mineral products industry, to read articles before they appear on Agg-Net.com