A Practical Solution
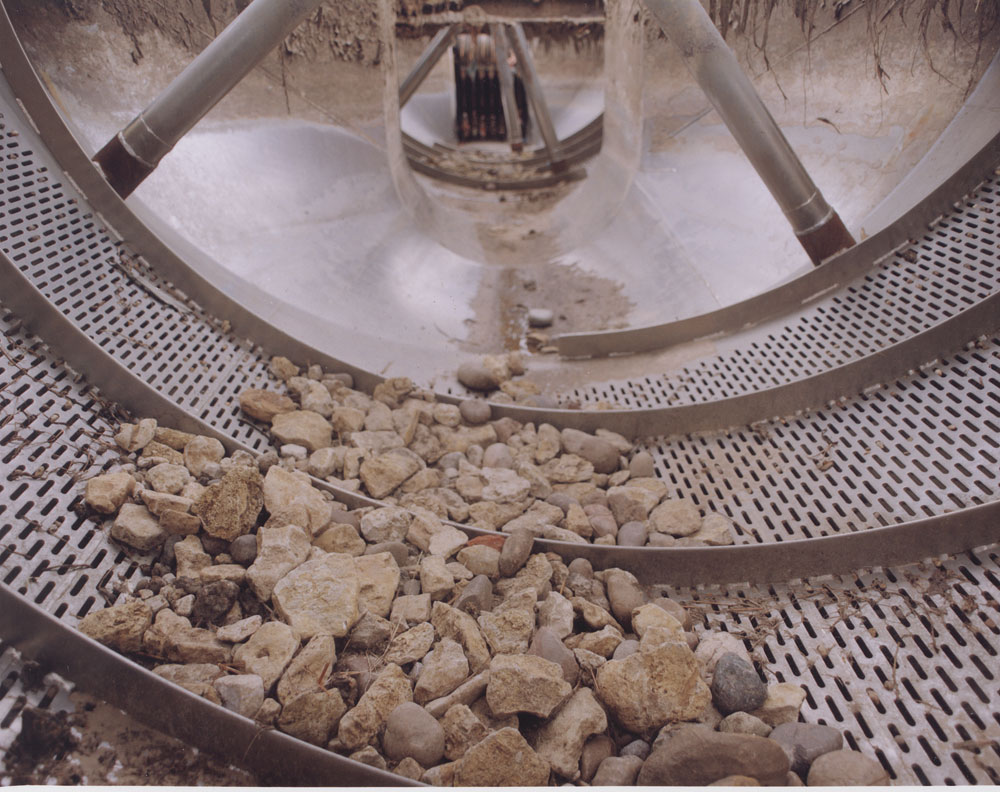
3CR12 helps solve corrosion problems in quarries, Phil Shirley reports
There is probably not a single aggregate processing unit in the UK today that is not being scrutinized for every potential cost saving. One area that deserves particular attention is the condition of materials-handling equipment. According to the manager of one of the UK’s largest sand and gravel units, the aggregates industry is so handcuffed by inadequate repair and maintenance budgets that unit managers are forced to adopt a ‘patch it and make do until it falls down’ philosophy.
‘Organizations need to take a long, hard look at how corrosion and wear problems will effect them in the long run,’ said one frustrated quarry manager. ‘These problems lead to downtime, which negatively affects plant productivity. We either need to take more care of our current equipment or invest in better materials that don’t fall apart after two or three years.’
The message is consistent, if not always clear — if you want your aggregates to flow, why not build equipment with materials that outwear steel, have a low coefficient of friction and, at the same time, will not corrode. In short, those at the cutting edge of the aggregates industry are being forced to rethink their choice of material for their conveyors, chutes, hoppers, bins and silos.
Recent inspections of equipment at several key sites in the UK, carried out by the technical manager of a company specializing in corrosion-resistant steel, has revealed major corrosion and wear in critical areas. During a site visit in July this year, hoppers used for processing sand and aggregate were examined. In general, the hoppers appeared to be suffering extensively from corrosion, both in the hoppers themselves and in the chutes below the hoppers.
The corrosion clearly showed material suffering hang-up on the walls, to the extent that one of the hoppers had a significantly reduced capacity. In addition to causing poor flow properties within the hopper, there was a consequent loss of wall thickness, which ultimately will affect the hopper integrity.
Another recent review was carried out on similar hoppers installed at another aggregate and sand handling facility. The bins, fabricated from mild steel, were installed in December 1998 on a depreciation term of 10 years but are already showing visible signs of corrosion on both the inner and outer areas, and particularly where the aggregates enter the bins via the conveyor. In this area a considerable amount of corrosion and de-lamination of the metal has occurred, with bits of material falling off the walls of the bins on to the aggregate, sometimes in sizes large enough to block the outlet.
Thickness checks were made from the outside of the bin using an ultrasonic depth gauge. The original depth of the material used to fabricate the bins was 8mm. After approximately three years service material thickness loss was in the range of 1.0mm to 2.4mm, representing a wall thickness loss of between 12.5% and 30.0%. From these findings it is clear that the bins in their current condition will not fulfil the original 10-year life specified.
Historically it has been shown that mild steel corrosion will continue once a surface oxide has formed, due to the porous nature of the corrosion product. If this product is undisturbed the rate of corrosion will reduce, but if mechanical action removes the corrosion product periodically the rate of attack will remain significantly high.
According to the manager of one of the UK’s largest sand and gravel units, mild steel corrosion within the aggregates industry is often underestimated. ‘I find it hard to believe that we are still building equipment out of mild steel,’ he said. ‘We expect conveyors and hoppers made out of mild steel to handle wet sand day in and day out, and then complain about the cost of replacing corroded sections when they inevitably last only a fraction of their predicted life.
‘The amount of badly corroded steelwork at sites across the UK is staggering. Incredibly, because the repair and maintenance budget is so low, the usual course of action is a lick of paint or a quick cut-and-weld job in the middle of the night when the plant is shut down. What is really needed is a review of the material used in the construction of equipment. We need to start looking long term.’
One answer could be to follow the example of other materials-handling sectors, including coal and sugar, where the use of 3CR12, a low-cost stainless steel, is providing a practical and economical solution to corrosion problems. Used successfully throughout the world, 3CR12 was originally developed as an effective answer to corrosion/abrasion in materials-handling operations but now has a rich testimony of success in a wide range of applications.
Corrosion resistance is an inherent characteristic of 3CR12, which contains 12% chromium and has 250 times the corrosion resistance of unpainted mild steel. Regarded as the original and now probably the world's most recognized utility stainless steel, 3CR12 is able to provide benefits such as good weldability and formability, making it capable of fabrication by conventional techniques. Additionally, 3CR12 provides the benefits of strength, corrosion and abrasion resistance, durability and low maintenance.
3CR12 was developed to provide a superior alternative to coated carbon steels and other materials which have poor corrosive/abrasive resistance, and because it does not depend on expensive alloying elements like nickel and molybdenum, it has maintained a consistently low cost advantage compared with other corrosion-resisting materials. It also helps to reduce costs by minimizing protective treatments and corrosion allowances. In service, 3CR12 goes on to generate savings in reduced maintenance, improved productivity and longer service life.
Significantly for the aggregates industry, in wet or damp conditions where abrasion occurs, 3CR12 has demonstrated impressive performance by resisting corrosive attack and maintaining better flow and slideability characteristics compared to non- or low-alloy steels, including abrasion-resistant grades.
The mechanisms of both dry and wet abrasion resistance have been carefully researched to establish how 3CR12 compares (with regard to rate of wear and cost-effectiveness) with other commonly used materials such as mild steel, abrasion-resistant steel and stainless steels. Under dry conditions where the moisture content is less than 4%, 3CR12 performs no better than mild steel in its resistance to abrasion. However, under wet conditions where the moisture content is greater than 4%, the rate of corrosion is often underestimated.
Where corrosion is present 3CR12 is shown to be vastly superior to carbon and low-alloy steels. When cost per unit volume loss is also taken into consideration 3CR12 is superior to all types of steel that have been tested. For materials-handling applications, whether for storage, such as hoppers, bins, bunkers or silos, or for movement of materials in chute bodies or liners, a factor described as ‘slideability’ is another important design consideration. In essence, slideability describes how well a given material flows over a given surface. It can be determined by the minimum angle a surface has to be tilted to cause the material to flow.
The superior slideability of 3CR12 can be exploited not only to restore lost capabilities in existing plant, but also to save costs in new plant. The shallower chute and hopper angles which are possible with 3CR12 allow for greater storage capacity for bins of a given height. Bunkers designed on core flow may benefit from the installation of low-friction linings to promote mass flow. Even if a bunker is of good mass-flow design there are still occasions when flow problems can be reduced by the use of low-friction linings to reduce the bulk/solid wall friction angle.
Owing to the improved slideability of 3CR12, it has found wide use in the storage and handling of coal, allowing rapid throughput of material. Independent tests have demonstrated the superior slideability of 3CR12 against a wide range of other materials.
As a result of this research, at least one major UK aggregates producer is now looking at the possibility of replacing mild steel with 3CR12. ‘Anything that reduces regular maintenance is worth looking at,’ said one quarry manager. ‘We have to ensure that component integrity is maintained, but maintenance significantly adds to life cost of the equipment.
‘Historically, coatings have been applied to steel to improve its life, typically galvanizing and rubber sheeting. These are quickly degraded to leave unprotected steel that readily corrodes. It’s a vicious circle, bound by financial constraints, and the only way to escape it is to look at the longer-term benefits rather than the short-term fix which is the current way of thinking.’
Cromweld Steels Ltd, The Old Vicarage, Tittensor, Stoke-on-Trent, Staffs ST12 9HY; tel: (01782) 374139; fax: (01782) 373388; email: sales@cromweld.com; website: www.cromweld.com
PP Group (Engineering Support Services), Vere Street, Weaste, Salford, Manchester M50 2GQ; tel: (0161) 736 9299; fax: (0161) 745 7915;?e-mail: sales@ppplasmaltd.co.uk