Wheel Washers
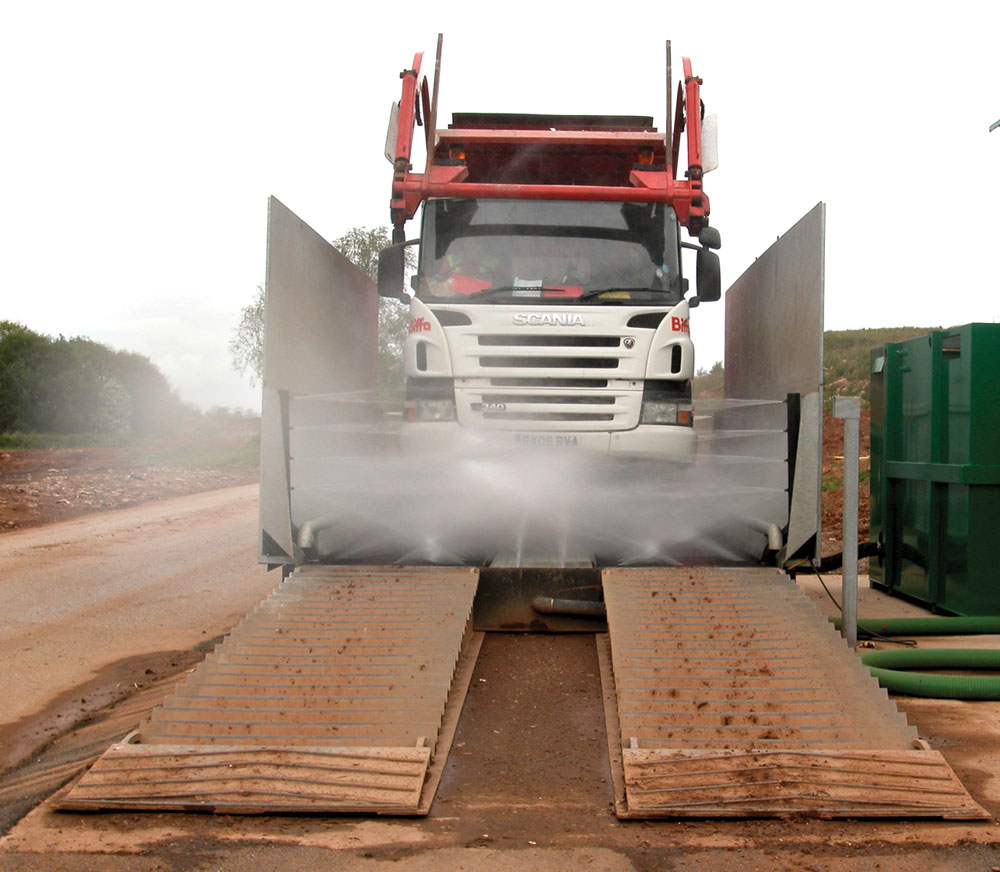
A necessary evil or essential piece of plant equipment? Christopher McCumesky, managing director of Hippowash, reviews the technology
To the uninitiated, vehicle wheel washers can be seen as an expensive and non-productive piece of capital equipment to keep the local authorities happy. However, nothing could be further from the truth and they play an important role at many busy sites. By definition, wheel washers operate in very harsh environments and it is important that they are designed for optimum reliability, energy usage and water consumption.
Companies running operations such as quarries, mines, waste and recycling plants, landfill sites and construction sites have a legal obligation to ensure that vehicles leaving their premises do not take mud or debris out on to the public highways. Those operators failing to keep roads clean are potentially contravening several sections of the Highways Act 1980 (see box below) and are liable for severe financial penalties (there is additional legislation under the Town and Country Planning Act 1990 relating to mobile plant not being allowed to transfer dirt and debris on to the highways).
Persistent offenders can have their operation shut down. If companies do not operate on-site wheel-washing facilities, they are obligated to incur the added expense and inconvenience of using contracted road sweepers. The highway authority has the power to clean the road and recover its expenses from the person causing the obstruction or nuisance. It is now common practice for planners to stipulate that wheel-washing facilities are installed at new or upgraded sites as part of the planning consent.
Wheel-washing operation
A wheel-washing system effectively consists of an open platform over which vehicles are driven at slow speed. As the vehicle passes, powerful jets of water from the sides and below are sprayed on to the wheels and under chassis to remove mud, dirt and debris. The platform typically has two rows of rumble grids constructed of evenly spaced inverted steel angle running at right angles to the direction of travel. This angle plays an important part in the cleaning cycle by loosening dirt and mud in the tyre treads and under-body.
For optimum cleaning, wash platforms are usually designed so their length allows between one and two complete wheel revolutions. Although the platform can be mounted flush with the road surface, it is usual to have entry and exit ramps constructed in a similar way to the main platform. Not only do these slow the vehicles down as they approach and depart the wash, but they also remove additional mud. Side screens deflect any spray back into the washer.
The wash system is usually fully automatic requiring no driver involvement. Vehicle detection sensors start the main wash pump as vehicles approach and then a second sensor switches the pump off as the vehicle exits.
Mud and debris-laden water from the wash is channelled down into the integral sump where the sump pump grinds up the solid material and sends it to the water-cleaning system. Some wash platforms are engineered to be self-cleaning. This is achieved via the power and volume of water used in the wash, the construction of the sub-floor and the use of a submersible slurry pump, which is fitted with an agitator. The volume of water used and the flow rate of both pumps are designed to ensure that the waste wash water and debris is removed from the platform before it has had a chance to settle.
Bespoke designs
Although standard designs are suitable for most applications, certain installations require bespoke wheel washers to offer cleaning flexibility for a range of vehicles. A large steel works is one such example where it is essential to keep internal roads clean as well as the surrounding public highways. In such an application, washing requirements may need to accommodate vehicles ranging from small vans up to 120-tonne off-road dumper trucks with huge double-wheel axles.
Water consumption
Water usage can be upwards of 1,100 litres/min and therefore effective cleaning and reuse of that water is an essential part of wheel washer design. Expensive and expansive settlement lagoons are becoming a thing of the past and are being replaced by compact and effective waste water clarifying systems. These are usually located adjacent to the washer and consist of one or more hoppers containing an arrangement of equally spaced plates to accelerate the filtration/settlement process.
As water is pumped into the top of the system, this lamella design rapidly removes over 95% of solids down to 15 microns, leaving clean water for the next wash cycle. The settled sludge can then be easily disposed of via the hoppers at the bottom of the clarifier, as required, either manually or automatically via compressor-operated gate valves. This closed-loop water system, together with the side screens, minimizes water wastage and removes the need for expensive, water-hungry lagoons.
Power consumption
It is clear that wheel washers are energy-hungry items of equipment, especially at busy sites. As a result, it is essential that the design of the pump control system is optimized, while ensuring pump longevity. There are a number of ways of starting pump motors each requiring different levels of start-up currents. Using a basic direct on-line start requires a 132kW peak power for a typical 22kW wash pump, while a star-delta start requires a 103kW peak and a soft start requires 55kW.
In addition, typically, pump manufacturers stipulate that their guarantee is invalid if their pumps are started more than 12 times per day using these methods. The optimum solution is to use an inverter, which offers up to 50% energy savings. This method has a 22kW peak power requirement for the 22kW pump and offers greater operational flexibility. It also means that a less-expensive, lighter-duty on-site electrical installation is required.
Although the initial build cost is higher using an inverter, the energy savings, improved reliability and operational flexibility offer significant cost savings which soon pay for the higher initial investment. A key advantage of using an inverter is that it allows the operator to reduce the power to the main pump when site conditions are less onerous. In summer, for example, only light washing may be required to remove dust and, at a simple turn of the control knob, the power usage can be reduced.
Conclusion
Wheel washers are essential items of equipment on many sites. Not only do they keep roads clear of potentially dangerous mud and debris, but they also help with vehicle reliability by keeping them clean. A number of important factors should be considered when choosing a wheel washer and the overall choice should be based on reliability and cost of ownership. Options that initially appear to be cheaper may not seem so attractive when running costs and maintenance bills are assessed.
Highways Act 1980
Section 137 states: ‘If a person, without lawful authority or excuse, in any way wilfully obstructs the free passage along a highway he is guilty of an offence’.
Section 148 states: ‘If without lawful authority or excuse a person deposits anything whatsoever on a highway to the interruption of any user of the highway he is guilty of an offence’.
Section 149 states: ‘If anything is deposited on the highway so as to constitute a nuisance/danger the Highway Authority can require the person who put it there to remove it forthwith’.
Section 161 states: ‘If a person, without lawful authority or excuse, deposits anything whatsoever on a highway in consequence of which a user of the highway is injured or endangered, that person is guilty of an offence’.