Transmission Revamp
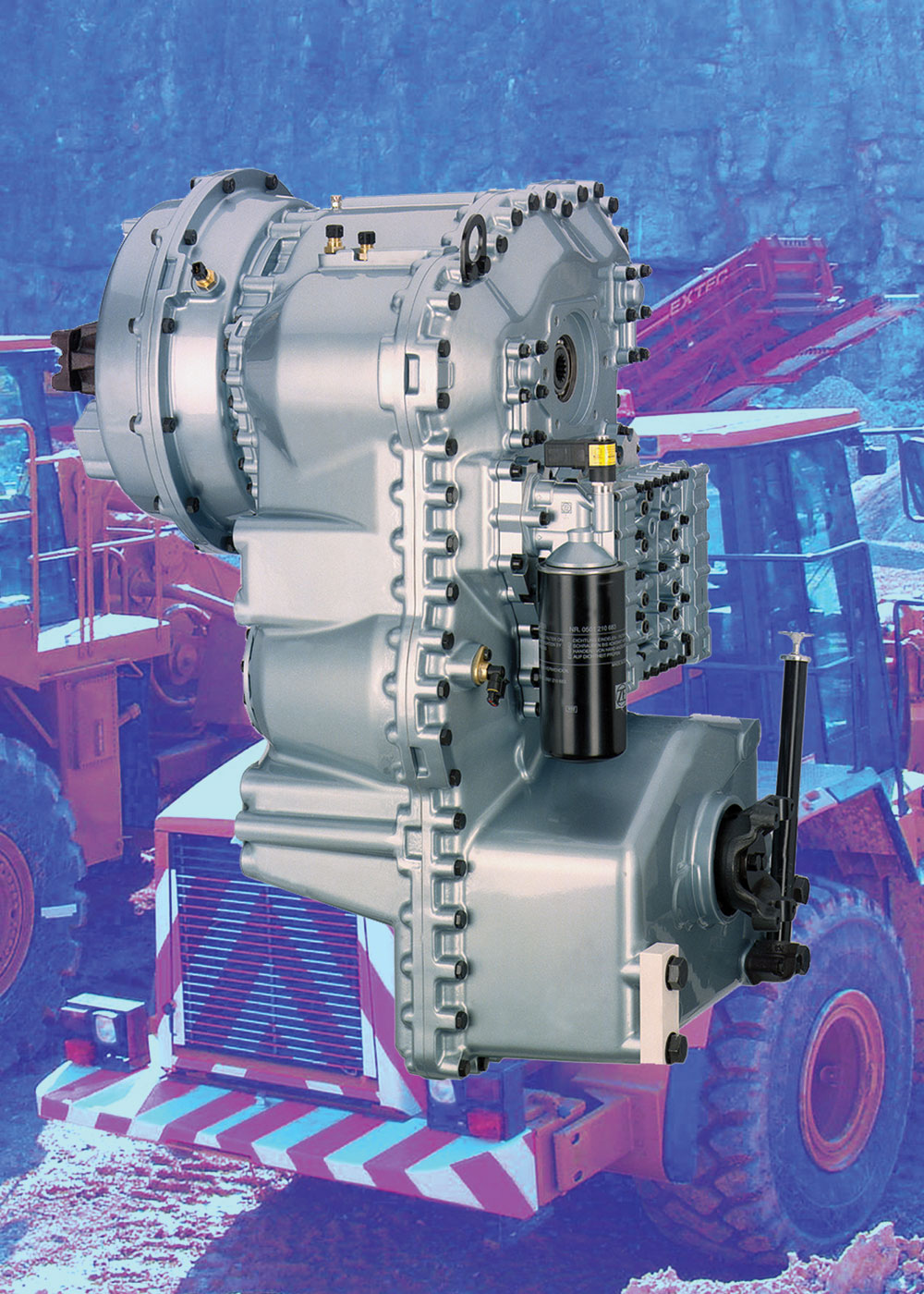
Is manufacturer repair and refurbishment of off-highway transmissions always best for the vehicle user? Mike Goatley of ZF’s Off-Highway Division makes the case, both from an economic and a safety point of view
The complexity of the transmissions used on the latest generations of wheel loaders, backhoes and dumptrucks is such that manufacturers say only they should repair them in the event of faults or breakdowns. The response of many in the quarrying industry is likely to be: ‘They would say that wouldn’t they’. But do the manufacturers have a case?
The past two decades have seen driveline technology in all types of vehicles optimized by the use of electronics and software. Nowhere has this development been more evident than with earthmovers and wheel loaders. Today, through the harmonized interaction of electronics, hydraulics and mechanics, gear shifting on off-highway vehicles is totally automatic, which means optimized gear shifting whatever the situation, ensuring longer clutch and transmission life and optimal use of engine power without torque peaks and vibration. As a result, incorrect shifts, which can cause damage to transmissions, have largely become a thing of the past.
At the heart of this automated shifting system on ZF transmissions is a transmission control unit (TCU). This communicates, via the well proven CAN network, with other ‘on-vehicle’ systems, such as shift and clutch modules, and a host of sensors measuring everything from temperature to pressure. Using this data, the TCU optimizes the operation of the vehicle. However, in addition to its control functions, the TCU is also equipped with an error memory, which allows it to record faults occurring on the transmission system.
This means that when a transmission failure happens, the TCU records the cause of the fault. When the transmission is removed subsequently by ZF this histogram data is retrieved from the TCU, allowing the fault to be rectified so that it does not occur again.
However, when the transmission is removed for repair by a third party, the TCU fault information is not available, so the consequent repair is undertaken in ignorance of what caused the failure in the first place. As a result, such repairs only address the effects of the failure, not the causes, so the same failure may well occur again.
The wide availability of fault data from transmissions also means that ZF no longer practice a conventional repair regime. The term ‘repair’ generally means rectifying the part that has gone wrong. In the field under pressurized working, this can mean quick replacement of components that have failed. Once again, however, this practice takes no account of what caused the failure initially. It is for this reason that ZF now prefer to offer a remanufacturing service rather than a repair service, although they will provide either. The remanufacturing approach is used by a number of major off-highway manufacturers; when a transmission fails it is immediately shipped back to ZF and a fully remanufactured and tested replacement is shipped back in its place. This reduces the overall time the off-highway vehicle is standing idle and is far more cost-efficient overall for the vehicle operator.
Remanufacture is far wider in its scope than repair. It entails the unit being fully stripped to component level; all parts are then cleaned and inspected to factory standards and any that need changing are replaced with genuine parts to OEM standards. New bearings and any product updates or improvements are also included in the remanufacturing programme. Units are reassembled to OEM standards and then fully load tested by ZF to ensure that they function in accordance with factory specifications.
Importantly, remanufacturing effectively addresses the issue of genuine parts. A lot of controversy surrounds this issue, mainly regarding cost. What must be considered, however, is that when ZF design and manufacture a transmission, the parts that are used provide a synergy of operation – all of them play their part in the overall calculated life of the transmission. This selection process extends down to material specification and the types of seals used on bearings. If, in the event of a failure, cheaper non-genuine parts are used in the transmission this operating synergy is lost and the vehicle operator has no warranty to fall back on.
The other major issue with genuine parts is safety. The litigation culture that pervades society today means that an operator using parts not recommended by the manufacturer could find himself in trouble if, for some reason, an accident occurs and those parts are highlighted in any subsequent investigation.
Once the remanufacturing process is complete the transmission unit is tested for up to 6h on one of ZF’s purpose-built test rigs. Only then is it ready to be shipped back to the customer, complete with a ZF warranty. However, if the transmission is a service exchange unit, it is put into ZF’s core stock as a replacement unit for future emergencies.
With most non-manufacturer repair operations, shipping the unit back to the customer signals the end of the process. The failure of this approach is that it does not raise any questions about what happens when the transmission is reinstalled. ZF identified this problem some years ago and offer an optional installation check to obviate any post-installation problems. The service involves the checking of transmission mountings, propshafts, engine connections and the operation of any direct interlocks or other safety functions.
In addition, it involves installing the latest updated software in the transmission control unit. The ZF engineer will also clear the error memory on the TCU, allowing the vehicle operator to start with a clean slate, and crucial for smooth operation of the vehicle, which is run a clutch calibration programme. This programme is designed to optimize shift quality and clutch life. It is crucial that this is performed upon reinstallation of the transmission because of the requirement to ensure that the clutch fills at the optimum rate for smooth shifting. A build-up of tolerances can cause the clutch to fill too slowly, resulting in a dwell in the shift process that can cause the vehicle to roll backwards. In contrast, if the clutch fills too quickly, a harsh shift may be the result, with negative ramifications for clutch and gear life.
The value of the service installation check can be judged from the fact that, in over 75% of cases where it has been applied, ZF have been able to point out things on the vehicle that are not right or not working, and give information to the operator on how to correct them and, as a consequence, extend transmission life.
For further information, contact ZF Great Britain Ltd on tel: (0115) 986 9211; fax: (0115) 986 9261.