The Rise Of The ADT
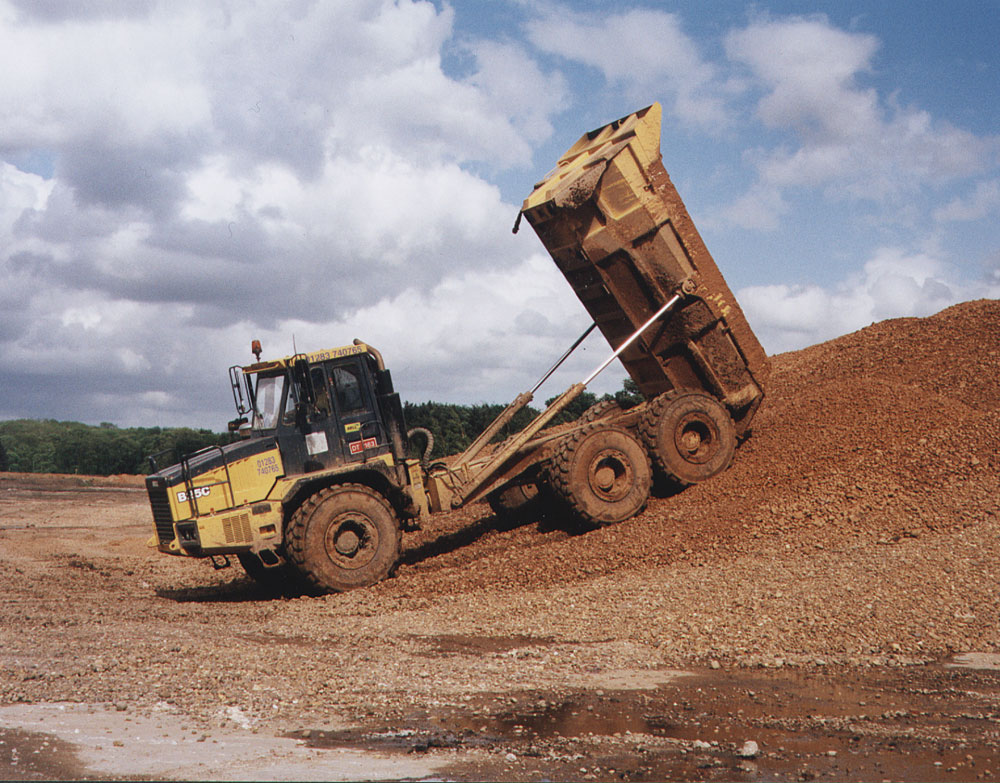
Why the success of articulated dumptrucks in world markets in the last decade?
The articulated dumptruck (ADT) is certainly not a new concept in earthmoving equipment, nor was it revolutionary during the last decade. In fact the ADT’s roots lie in the UK and Europe back in the late 1960s. It has therefore been an option for customers worldwide for the better part of 30 years.
However, the last 10 years of the 1900s saw a dramatic rise in the sales of ADTs across all markets and to all corners of the globe. In 1990 the world sales figures of all ADT manufacturers totalled marginally less than 2,000 units. By the turn of the century this had risen to 4,300 units, with a peak of 4,800 units having been achieved in 1997.
The huge increase in the demand for ADTs during this period has been significant, especially at a time when all other ‘families’ of earthmoving equipment, with the possible exception of skid-steer loaders, were declining in numbers, some quite dramatically. Included among these other ‘families’ are the motorized scraper, rigid dumptruck, dozer, wheel loader and motor grader.
A further thought when considering the ADT as the ‘item of choice’ by customers worldwide during the past 10 years, is that it generally took place against a backdrop of declining markets, none more so than in the mining and quarrying industries, but also in other sectors such as construction, timber and sugar.
Against this background, why has this upward trend occurred and what does the future hold for the ADT?
The ADT is a high-performance, all-terrain earthmoving machine capable of tackling most jobs cost-effectively regardless of travel distance, material type or ground/haul road conditions. It can be described as a ‘jack of all trades and master of one’. The ADT can undertake most jobs at a reasonable cost per tonne while being the only machine capable of handling really severe underfoot conditions. From a customer’s point of view, this adds up to unparalleled versatility and comfort on the job site.
The ADT target market is a wide and varied one, thereby ensuring a large customer base. Construction and bulk earthworks contractors involved in roads, dams, airports, landfills and development projects are large users. So too are the mining (particularly pioneering, short-term projects), quarrying and contract mining industries, especially in southern Africa, the UK and Australia. Load and haul (both surface and underground operations), tunnelling, overburden removal and mining in poor weather with poor haul road conditions are all well within the capabilities of the ADT. Other user groups that have increased their usage of, and dependence on, ADTs in the last decade include the agricultural industry (most notably timber and sugar); general industry, for waste handling and stockpiling; the military and civil services for disaster/emergency and strategic work; and the rental companies for short-term work in numerous applications.
In addition to the more traditional markets and customers, in recent years the ADT has also been found to be particularly suitable for conversion to special applications. Bell Equipment have been involved in a number of such ‘specials’, including:
- flat-deck carriers: these are suitable for the haulage of products in the dimension stone and timber industries. They can also be used as pipe carriers. The deck can be either a fixed platform or a hitch-type roll-on/roll-off arrangement
- diesel and water tankers: various tank sizes ranging from 15,000 litres up to 36,000 litres can be fitted to the appropriate size of ADT chassis/cab
- concrete mixers: outsourced concrete mixers can be fitted to the cassis/cab
- service vehicles: with the dump body removed, an ADT can be modified into an effective service vehicle, the large deck area allowing the fitment of tools, tanks, crane etc
- drill rig: the ADT chassis/cab, if fitted with a fifth-wheel arrangement, can be used for off-road transportation of drill rigs
- waste handling: the 6x6 drive configuration is useful in high rolling-resistance waste-handling applications
- slag-pot carriers: the ADT chassis/cab can be used in conjunction with a custom-built rear end to suit different types and sizes of slag pots.
The past decade saw a reduction in the construction of major road links in the developed world, most notably in Europe and North America. This resulted in a decrease in the utilization of specialized plant, such as motorized scrapers and off-road rigid dumptrucks, while plant offering greater versatility and flexibility, such as the ADT and hydraulic excavator, gained favour. Coupled to this was a growing awareness in North America of the cost-effectiveness and versatility of the ADT when compared to motorized scrapers and small rigid dumptrucks. It should be noted that North America represents approximately 40% of the global ADT market and thereby has a pronounced effect on annual sales.
In the majority of vehicle manufacturing operations economies of scale play an important role in reducing the cost of manufacture. In the case of motorized scrapers and small rigid dumptrucks, reduced sales meant manufacturers were unable to achieve critical mass. This has been reflected in the higher retail prices on these families of machines, particularly when compared to pricing on ADTs.
The 1990s also saw a dramatic increase in the price of oil, resulting in equally dramatic price hikes in diesel fuel. Today fuel consumption represents approximately 30% of the total ownership cost of any item of earthmoving plant. Fuel consumption is therefore a critical element and, quite correctly, more attention is being focused on this issue. Huge annual savings can be achieved if, for example, one particular item of plant is 10–15% more fuel efficient per hour than another, particularly in 24h operations. During the past 10 years or so the ADT has been proven to be far more fuel efficient than motorized scrapers and rigid dumptrucks of equivalent size.
Where once there were only three major players in the ADT business, the 1990s saw increased competition in this market. Bell entered the international fray as did a number of other manufacturers. This had the effect of making the market more ADT aware. In addition, mechanical and performance improvements in the past 15 years or so have resulted in greater reliability and better customer acceptance.
Perhaps most significantly, cost per tonne, or cost per tonne/km, is the single most important criteria for any mine or quarry. The ADT, with all its versatility and increased performance capabilities, coupled with its attractive purchase price and low operating costs, makes it today’s preferred choice of plant.
So what lies in store for the ADT during the next decade? It is generally felt that a global market of between 5,000–6,000 units annually is sustainable, although naturally the performance of the world’s leading economies will play a major role in this scenario.
Manufacturers of ADTs are also sure to produce units larger than the present 40-tonne maximum capacity. Indeed, taking a lead in this respect, Bell Equipment have recently introduced the B50D, a 50-tonne capacity 6x6 ADT (see page 29). And in the underground, low-profile 4x4 market, articulated trucks offering capacities of 50 tonnes and 55 tonnes are now on offer. The future of the ADT therefore seems assured, but interesting challenges and demands lie in store for all the manufacturers over the next 10 years.
This article is based on a paper presented to the Institute of Quarrying Southern Africa's September 2001 conference by Terry Gillham, marketing director of Bell Equipment Co. S.A. (Pty) Ltd