Taking ADT Safety to New Levels
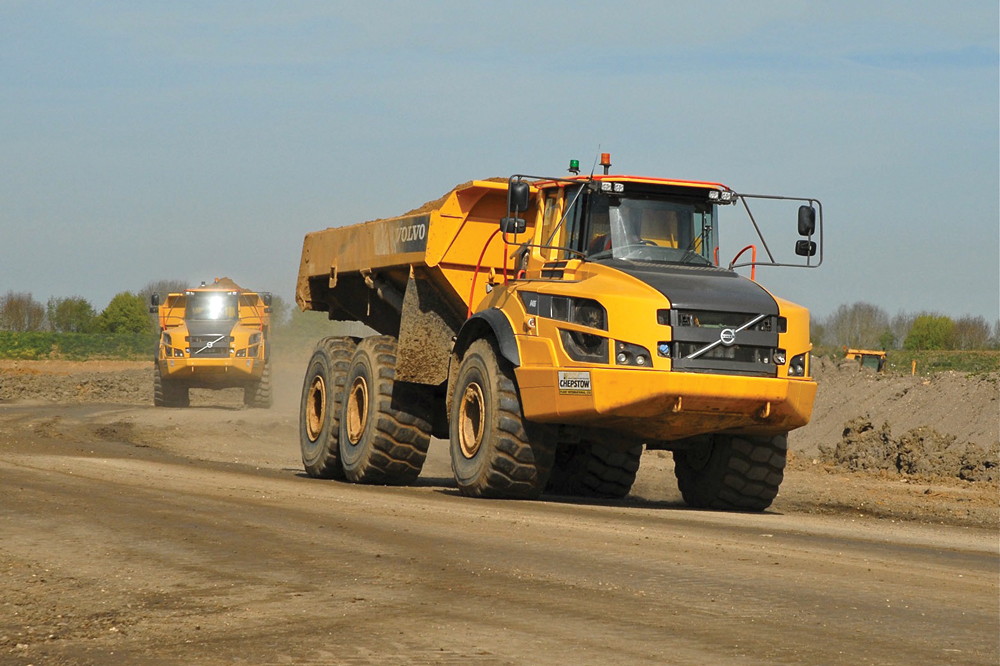
First published in the November 2017 issue of Quarry Management
Chepstow Plant working with clients and equipment partners to maintain the best possible levels of safe working practice on site
Like many contractors, Chepstow Plant International take health and safety very seriously. In particular, they have increased their focus on articulated dumptruck (ADT) safety and operator training, to ensure that their quarry operatives are maintaining the best possible levels of safe working practice on site, and their Volvo excavator simulator training service is now also being offered to other contractors and quarry businesses.
John Corcoran, managing director of Chepstow Plant, explained: ‘The ADT has become the vehicle of choice given its scope and capabilities – and they’ve been used in a variety of applications over the years with a design that ensures the safety of the operator should anything go awry. But, with increased ADT use, a new set of challenges to quarrying has arisen. We’ve analysed some of these by working alongside our quarry customers to find solutions, such as reviewing operating procedures to provide optimum terrain conditions for ADTs to work on, and having trucks equipped with extra safety technology, supported by state-of-the-art operator training for ADT drivers.’
Among an extensive fleet of plant, in which the majority of excavating machines weigh between 30 and 80 tonnes, Chepstow also operate a large number of articulated dumptrucks. Indeed, the company has added 73 Volvo ADTs to its fleet in the past 12 months alone. Having so many machines requires a large number of highly skilled operators – all of whom must be familiar with the latest equipment and capable of working in a safe, productive manner on site. The majority of the company’s work is in quarrying, so Chepstow routinely qualify their operators to Mineral Products Qualifications Council (MPQC) Plant Operator Competency Scheme levels.
In line with Chepstow’s initiative, excavator operators have to prepare level loading areas, dozer operators must keep level tips and stockpiles, and methodology and geotechnical assessments now have to be detailed to support developments with the company’s new ADT stability programme. The company also keeps an ADT Risk Register and has changed its operating procedures. The company’s safety and quality manager, Steve Smith, now visits every site where ADTs are going to be used. He explained: ‘We thoroughly assess weather conditions, unstable or uneven ground levels, the plant being operated, pre-start daily inspections, tyres, haul roads, inclines and downhill haul sections, plus loading and tipping areas, and re-inspect again a few days after work has started. For us, safety always comes before production.’
In addition, one of Chepstow’s client partners, Tarmac, recently worked alongside them to develop an inclinometer that allows for an even greater safety margin during ADT operations, providing improved preventative controls to stop the rear chassis of an ADT from turning over in the extreme terrain conditions often found in quarries.
‘It compensates for any ‘overly enthusiastic’ handling that quarrying operatives may engage in,’ said Mr Smith. ‘We all know that, in severe conditions, the rear chassis of an ADT can roll over leaving the cab safely upright, safeguarding the operator. But we would much rather there was never a situation where this happens at all. Now, if the body of a truck tilts more than 9° either left or right, the system will automatically alert the operator and stop the tipping hydraulics. Likewise, if the body is down, the operator will be warned if the rear section of the chassis exceeds 12° of roll angle during travel.’
Both of these angles are well within Volvo’s own stability parameters, but as Mr Smith explained: ‘We’ve actually gone for around one-third of the angle that Volvo recommend, to give us an even smaller window, which should eliminate quarry trucks getting anywhere near those parameters. The training and familiarization programmes we have rolled out focus primarily on the behavioural approach to the operation and supervision of ADT operations, in line with the technical improvements we have developed.’
State-of-the-art simulator training
Chepstow Plant have also been operating a complex Oryx Volvo excavator simulator for the past two years, training excavator operators before allowing them in the cab of actual machines, and, more recently, have purchased a second simulator for ADT and wheel loader operator training and development. This is with a view to developing top-calibre operators, not only to perform with optimum competency, but also so they have an understanding of the true purpose and capability of the ADT through increased awareness and specific training.
This new simulator provides a dual function – the unit has fold-down armrests that have Volvo wheel loader controls in place, so it can be used for both loading shovels and ADT training. It uses actual operating site data to deliver a highly realistic driving experience with the entire unit tilting up to 23° forwards or backwards, and up to 15° to either side, meaning a seatbelt is necessary to remain in the seat.
Training exercises become increasingly difficult and longer in duration, teaching operators how to use engine and transmission braking, and training them in vehicle manoeuvres, and loading, hauling and production scenarios. The simulator even records how much fuel is being used, to allow drivers to see that their right foot has a direct effect on the running cost of the machine.
Chepstow have been testing the ADT simulator at Tarmac’s Mountsorrel Quarry, in Leicestershire. The first trainee to prove the effectiveness of the machine was Jason Rust, an experienced construction site operative but a machine novice. Having undergone training on the simulator, Mr Rust has now passed his MPQC assessment and graduated to operating a Volvo ADT at the quarry. He said: ‘When I first got in, it was all new, but after just a few days I felt that I’d got my head around it, and it was a lot less worrying than getting straight into a truck.’
Simulators make life easier for both the trainee and the trainer. There is a buddy seat in an ADT, unlike an excavator where the instructor has to stand clear of the machine while in radio contact with the trainee. Chepstow Plant’s national training manager, Martin Stephens, said: ‘The beauty of a simulator is that if anything does go wrong, it’s simply a case of pressing restart, which cannot be done in a live site situation. It only takes around five to seven days to get to a point where significant risk can be managed. This is risk-free training for both accredited and novice personnel.’
Managing director John Corcoran summed up: ‘There are clear safety and cost benefits to having this state-of-the-art technology, and it’s an investment that Chepstow feel is worth making to ensure risk-free, specialized training. This high level of expertise will not be limited to Chepstow’s own operators either, as the company is offering a complete operator training service to other contractors and quarry businesses. Our aim is to inspire a change in mindset to the way ADT stability is viewed and managed.’
- Subscribe to Quarry Management, the monthly journal for the mineral products industry, to read articles before they appear on Agg-Net.com