Reaching Maximum Potential
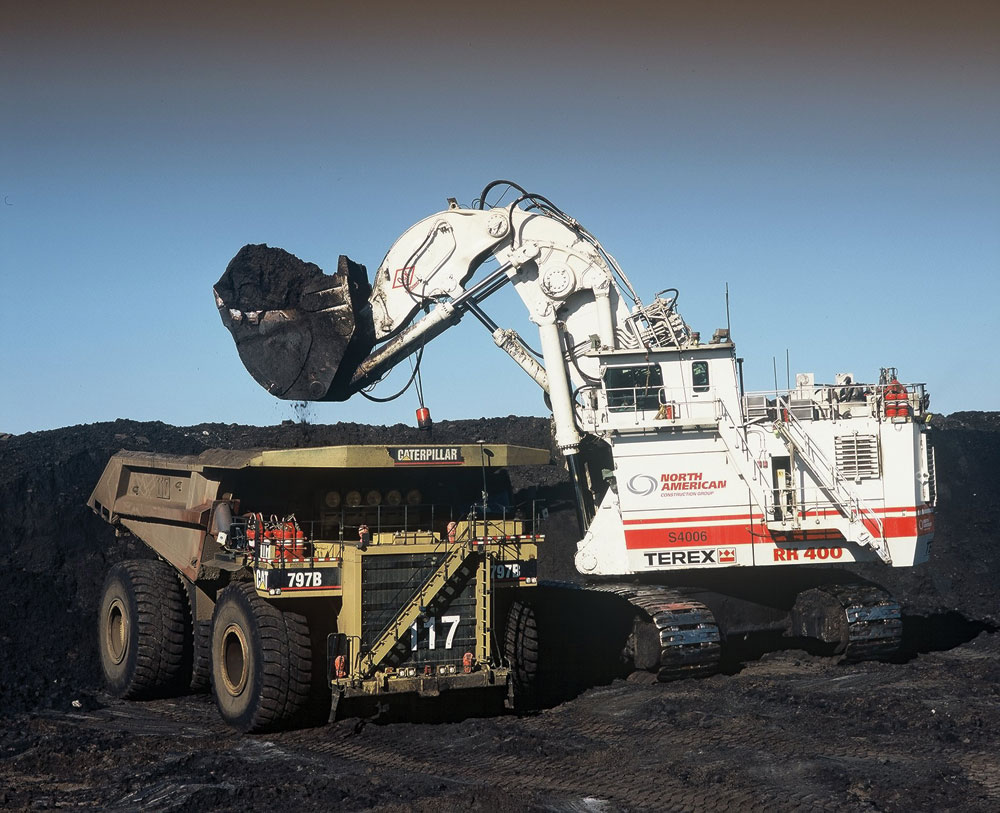
Professional selection and operation of hydraulic excavators
By Dirk Tegtmeier, product manager, Terex O&K
Loading equipment represents the first link in the chain of material flow in most quarry and open-pit applications. All subsequent stages, such as hauling, crushing, processing etc, depend on the loading machine’s productivity at the working face. While it is true that the performance of an excavator or a rubber-tyred wheel loader is defined by a number of key technical specifications, which set physical limits, it is also the case that the right equipment choice for a specific application and best-practice operation determines whether the machine can be utilized to its fullest potential – or not.
Broad range of different loading equipment
Leaving bucket-wheel excavators, surface miners, conveyor belts etc aside, when focusing on discontinuous mining the quarry or mine manager basically has three options when selecting a new loading tool. These are: wheel loaders; hydraulic excavators, either in front-shovel or backhoe configuration; and rope shovels. The deployment of rope shovels, however, is generally restricted to huge mining operations, with some geographical exceptions, such as China, India or the ex-CIS countries, where locally made electric shovels in the 5m3 to 10m3 class are still quite common and can be found in some quarrying operations.
The ideal working environment for an electric shovel is a combination of a high working face, which is essential for an appropriate bucket fill, together with a well-blasted material that is not too hard to dig. The power supply cable at the rear of the machine does not present much of a handicap if the operation is more or less stationary. At the top end of the range, ie above 30m3 bucket capacity, rope shovels are still competitive today in their specific working conditions.
Rubber-tyred wheel loaders distinguish themselves by their mobility. They can change loading area quickly and easily, and are able to adapt to various production requirements. This becomes particularly relevant in selective mining applications where the source of raw material within the deposit, and therefore the loading area, can change several times during each shift in order to meet quality requirements.
Another benefit of wheel loaders is their ability to conduct ‘load and carry’ operations. In this case loading and hauling is executed by a single machine, which is more efficient when the haul distance is very short, in contrast to the use of a dumptruck, which would spend most of its time at the loading and dumping area instead of performing transport labour. This method is often used in connection with in-pit-crushing where mobile or semi-mobile crushers are used. The maximum economic distance for load and carry depends on the rolling resistance and gradient and can be determined at between 150m and possibly 200m.
It is the ground conditions that limit the general feasibility of a rubber-tyred loader application, as a flat and even surface in the loading zone is an essential precondition. Another requirement is sufficient space for manoeuvring, in contrast with a hydraulic excavator, which can fill its bucket and dump from the same spot.
Up to 50m3
Hydraulic excavators used in the construction and mining industries are offered in a wide range of different sizes and versions, including wheeled and tracked units. A variety of attachments are available to adapt the machines for multiple applications, eg hydraulic breakers, hammers and grabs or special-shaped buckets. Entry into the quarrying market starts with an operating weight of approximately 45 tonnes; this is a market that has seen a large influx of manufacturers recently. Very large mining machines, however, are produced by only a small number of manufacturers.
The first hydraulic excavators were launched in the early 1960s and were soon introduced into the extractive sector. Their weight grew rapidly and units with a standard bucket volume of between 20m3 and 30m3 established themselves in open-pit mining between 1980 and 1990. Today, hydraulic shovels have nearly caught up with electric shovels – with the 1,000-tonne Terex O&K RH 400, which features a 100-tonne bucket payload per cycle, serving as the market’s flagship (fig. 1).
The human factor
Apart from the service weight, which is the major technical specification for the classification of hydraulic excavators, there are other, more important performance data, such as bucket capacity, engine output and digging forces. However, many other factors also influence excavator output, measured in loaded tonnes or bank cubic meters, but each technology is only as good as the human interface behind it, which is, of course, the operator. It follows, therefore, that a comfortable working environment will result in added productivity, as will proper training.
For this reason, features such as an ergonomic seat/controls and a radio are regular components of the modern cab. Noise insulation and compliance with the standards for operator vibration are also important. An additional ‘second’ air-conditioning system is installed (even redundantly) in some units, particularly those destined for use in countries with hot climates, such as Australia, while the RH 400s used at Syncrude’s oil sand operations in Canada have an additional amenity cab behind the regular one, providing a microwave oven, wash basin and refrigerator.
Many suppliers also offer special training courses, including classroom lessons and on-the-job training, where, in addition to the normal briefing after the commissioning of a new excavator, experienced operator instructors will teach the ‘secret tricks’ behind the most productive operation of the machine.
Shovel and truck match
One question that always arises when discussing shovel and truck applications is the best match of loading and hauling equipment. In general, the number of passes required to completely fill a truck should be between three and seven buckets; each rule, of course, has its exceptions. For example, an extended hauling distance allows for a larger truck relative to the size of the shovel, as the increased percentage of unproductive waiting time of the truck at the loading area (more passes required) is balanced by a longer haul. Conversely, a short distance to the dump area or crusher requires quick loading of the haul unit. In all cases, a key consideration is whether productivity is truck- or excavator-driven. A high level of utilization of the truck is supported by minimal idling time during loading; while a high level of utilization of the hydraulic excavator calls for larger trucks to maintain a low level of unproductive spotting time between the departing and arriving trucks.
A hydraulic shovel, or indeed any other loading tool, achieves the best possible utilization when dumping directly into the hopper of a mobile crusher, since the spotting time is reduced to zero, except for the occasional movement of the crusher. The best overall approach involves consideration of the entire scenario, ie the costs per tonne, isolated for excavator and for truck, have to be investigated based on different numbers of loading cycles. Both individual cost curves can then be summed up to find the lowest total cost, thereby revealing the best match. Needless to say, any equipment combination should work with an even number of passes only, as half-filled buckets are a waste of time and energy.
Alongside the utilization question, the following issues must also be considered for each set-up: if the excavator, and therefore its bucket, is comparatively large, the impact on the truck body and suspension while dumping will also be greater. Nevertheless, the hydraulically controlled bucket clam function on face shovels and the bucket curl operation on backhoes do allow for a smoother discharge than is possible with a rope shovel, where the dipper door is unlatched rapidly and the payload is released at speed. However, a smoother and careful dumping process does take longer, and an oversized excavator reduces the likelihood of the operator being able to fill the truck to its precise rated payload in fewer passes. Also, the backhoe generally cannot load a truck from the rear, as the bucket can be wider than the truck body, so a different arrangement from the side of the truck facing the excavator is necessary.
The other extreme – a hydraulic excavator that is too small in comparison to the truck – is better accommodated when the backhoe version is used. Due to its position above the truck, visibility operator is largely unaffected and, thanks to the larger working range of the attachment, in most cases, it is possible to load the truck body evenly. The front-shovel faces more difficulties with an oversized haul unit. The machine has to be very close to the truck to place the bucket over the body for discharging, and as a result the hydraulic cylinders are in danger of hitting the side wall of the truck, thus calling for a careful and, therefore, slower operation. Another risk is the small amount of clearance to the counterweight when slewing back to the working face or when applying double side loading.
Faceshovel or backhoe?
A general answer to this question cannot be given, and preference for one of the two attachment options sometimes depends on the individual attitude or experience of the mine/quarry management. Some mining contractors, for example, prefer a backhoe because its versatility creates better potential for follow-up jobs if the machine is subsequently moved to a different site. There are also operational attributes that characterize the application of a faceshovel or a backhoe.
When working with a front-shovel attachment, the excavator and dumptruck need to be at the same level with the loading unit in front of the digging face. This provides a clear advantage for the operator, especially in difficult digging applications, as the working face is clearly visible from the cab, which helps the operator to find the best point for bucket penetration, such as fractures or layer boundaries. The position of the loader on the same level as the truck also allows for cleaning of the ground surface to prevent tyre damage, although auxiliary jobs of this nature should generally be carried out by support equipment, eg a dozer, leaving the shovel to concentrate on loading the hauler(s).
The physical digging force of a shovel is generally greater than a backhoe with the same bucket capacity, which is one reason why they are the preferred choice for hard rock applications. Another important factor is their operating position in front of the blasted pile, where the front-shovel unit can start digging immediately. A backhoe machine, on the other hand, has to prepare a ramp to get on to the material and travelling on a shot hard rock pile involves high levels of wear to the undercarriage components, particularly when the machines are larger and, therefore, heavier. Nevertheless, a backhoe can sometimes be the better alternative for a free-digging operation, as the working mode of the bucket is more of a ‘scratching’ action and the material is ‘clamped’ between the bucket and tracks, while a front shovel tends to ‘compact’ the material while penetrating.
Many quarries are facing growing problems with their blasting operations as the boundaries of the site approach residential districts, or vice versa. This can result in annoyance or even danger caused by flyrock, vibration, dust, noise emissions etc. As a result, some operators are looking for alternative methods to loosen the material without any blasting. Terex O&K have delivered a 265-tonne RH 120-E backhoe excavator specifically designed for this purpose to a large cement works in southern Germany (fig. 2), but instead of using a quick hitch to interchange between ripper tooth and bucket, O&K favoured a combined tool – a ripper bucket – to allow the loosening and loading of the material in one action. Instead of the standard 15m3 bucket, the RH 120-E in question is equipped with a special, extremely narrow 9.0m3 bucket, which is reinforced with a centre rib in the shape of a ripper tooth. After commissioning a production test was performed over an 8h period with a target set at 850 tonnes/h in the toughest zone of the deposit. This was achieved with an average bucket fill of 81%, which is reasonably good for a free-digging application. The specific powder factor for the previous blasting operation in this area had been between 120 and 140 grams of explosives per tonne.
[img_assist|nid=12239|title=Terex RH40E|desc=|link=none|align=left|width=269|height=200]In mentioning better visibility of the working face for the shovel operator, it is necessary to point out that, on the other hand, visibility of the truck body is better with a backhoe machine, especially when the truck is at a lower level, which is generally the case (fig. 3); this helps ensure a well-balanced load distribution within the body. The slew angle of the backhoe is usually in a range between 30° and 60°, facilitating quicker loading cycles, while the slew angle of the front shovel usually ranges between 60° and 90°.
Bench height
The workable bench height with a front-shovel attachment is generally higher in comparison with the backhoe. Increased floor space is required for backhoe operation when mining down to the same depth.
The height of the working face for a front shovel depends on the material and its behaviour. For ‘in situ and sticky’ material, which creates vertical faces, the height should not exceed approximately 75–80% of the maximum vertical reach of the bucket due to the restricted working radius at the top end of the digging range. As a rule of thumb, the ideal height under these conditions is equal to the roof of the cab (fig. 4). The higher the working level, the closer the undercarriage and the basic unit itself is to the face, thus increasing the risk of damage by falling rocks. However, if the material has a tendency to roll down, as in a blasted rock pile, and the slope is less steep and does not create overhangs, here the feasible height can be increased (fig. 5).
The bench height for a backhoe operation should correspond to the stick length of the excavator or truck body loading edge respectively. With the ‘double benching’ extraction method, however, it is possible to utilize the backhoe’s full working range and to expand the effective bench height at the same time (fig. 6). For this purpose, the excavator is located at a level approximately one third of the height of the entire face. During the first phase the digging section is located behind/beside the machine and above excavator level. For this purpose the material is scratched down the face and the bucket gets filled from a small trench at the base. Having worked a certain distance in this fashion, on the way back material from the lower level is removed in the second phase by means of a traditional backhoe action. However, the material parameters must allow for this working mode, which is not practical in severe conditions. The likelihood of loosening material above the excavator level is the limiting factor.
Truck spotting
The influence of properly arranged spotting of the dumptrucks is very often underestimated. When considering a constant excavator loading time, the productivity of a shovel and truck operation can be boosted by 10% if the spotting time can be minimized from 1min to 45s, as shown in the following example with a 525-tonne RH 200 (26m3) in combination with a 190-tonne truck (fig. 7):
Load per bucket = 26m3 bucket volume x 1.8 tonnes/m3 material density x 0.95 fill factor
Load per bucket = 44.5 tonnes
Load per truck = 44.5-tonne load per bucket x 4 loading cycles
Load per truck = 178 tonnes
Loading time = 3 full loading cycles x 30s cycle time + 5s dumping
Loading time = 95s
Productivity = 178-tonne load per truck/[(95s loading time + 60s spotting time) x (1h/3,600s)]
Productivity = 4,134 tonnes/h
Of course, quick spotting requires sufficient space in the loading area and this might not be constantly achievable. But, wherever applicable, production managers should encourage their drivers to position their trucks under the bucket in just one step without time-consuming manoeuvring. If a sufficient number of trucks are available, double side loading minimizes the spotting time, but this method requires the permanent support of a dozer for surface clean-up (fig. 8).
Needless to say, the excavator operator can contribute to better productivity. Alongside a[img_assist|nid=12240|title=Terex loading|desc=|link=none|align=right|width=250|height=200] good bucket fill, it is important to accomplish fast cycle times. Therefore, a small slew angle should be maintained. The penetration height into the face should be as high as possible in order to keep the lifting effort low. However, when digging a blasted pile it might be easier to penetrate at the bottom (as anyone who has ever had to shovel a couple of cubic metres of gravel into a wheelbarrow will confirm). During the changing of loaded and empty trucks, the hydraulic excavator operator can switch to the most unfavourable conditions – large slew angle and low penetration level – since a loading cycle under these circumstances is usually still quicker than the spotting of trucks and the excavator will present its full bucket before the empty truck is in position.
Final bucket
The influence of various individual factors on productivity and efficiency might appear negligible if perceived in isolation, but the sum total combined can make a tremendous difference to the performance of a hydraulic excavator. Steady monitoring of the application and continual improvement is the key to a successful operation.