Original Thinking on Safe Tipping with Articulated Dumptrucks
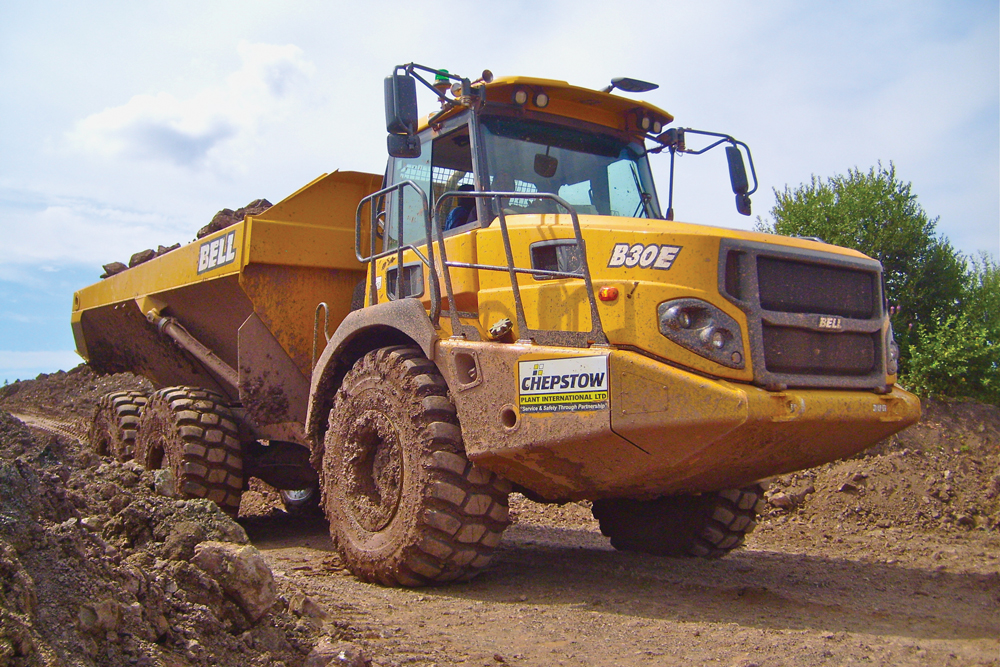
First published in the November 2017 issue of Quarry Management
Bell Equipment establish position as safe tipping software forerunners with help from Chepstow Plant
The digital age has truly arrived in the quarry and with it the inclusion of safe tipping software within ADTs is certainly becoming more evident, with on-board technology proving vital in the prevention of accidents and expensive machine damage. However, very few manufacturers include this technology as standard, which has led to many ADTs being retrofitted with software capable of working compatibly with inclinometers.
The aim is to improve the tipping safety of machines built without integral safe tipping technology. But, as this post-manufacture practice shows signs of increasing, Bell Equipment point out that they have been incorporating integral ‘Safe-Tip management’ systems as standard within their Fleetm@tic on-board GPS and data software since 2008.
Indeed, the company has invested heavily in research to develop systems that prevent its ADTs from performing unsafe or overloaded tips, and considers the development and installation of integral safe tipping solutions ‘a non-negotiable’ essential, citing its own software as being ‘as fundamentally important as the engine itself’.
Bell’s ‘Safe-Tip’ software works by cross-referencing the machine’s angle reference, taken using its integral inclinometer, with the computerized Fleetm@tic on-board weighing feature, situated within the vehicle’s cab. A pitch-and-roll sensor then sets appropriate limits for safe bin-tip activation. If the vehicle is positioned at an angle where a bin lift could cause instability, the machine’s operator will be warned of a potentially dangerous action on the display monitor, and will consequently be able to cancel the load manoeuvre and prevent the bin from tipping.
Not content with allowing their system to potentially loose headway, Bell’s commitment to developing and installing effective digital safe-tip solutions has, in parallel with the ADTs themselves, evolved in recent years.
Since commencing the launch of their E-Series machines in 2014, Bell Equipment have further developed their on-board ‘Safe Tip’ software by working in conjunction with client and safety research partner Chepstow Plant International, who have pitched themselves as an operator seeking to create a safer tipping environment as standard, and have set the bar as an industry front-runner in providing their own clients with machines that can consistently and realistically set the payload within protected parameters.
Chepstow have a long-established relationship with Bell that has been developed over many years, and with more than 17 Bell ADTs currently operating within the company’s plant fleet, managing director John Corcoran says the brand continues to perform ‘safely and reliably’ for his firm, enhanced by Bell vehicles’ inclusion of ‘Fleetm@tic’ technology. It is this on-board digital reporting system, says Mr Corcoran, that has successfully provided Chepstow with automatic reports, alerts, production data and pole-to-pole satellite coverage over the years, allowing the firm’s Continuous Improvements (CI) department to manage its fleet with greater control and efficiency.
The ‘Safe-Tip’ software is installed within the ‘Fleetm@tic’ system and is used by the CI team to prevent accidents and analyse findings. Recently nominated as a finalist for an MPA Health & Safety Award for ADT stability development, the department has chosen to further its own capabilities by providing real-time information to Bell Equipment, under an initiative created to constantly evolve their ADT technology with every new model and system update.
Mr Corcoran explained: ‘Safety is the number-one priority in our industry and protecting our employees and customers is of paramount important to us. Fleetm@tic, Bell Equipment’s purpose-designed on-board fleet-management system, is allowing us to do this effectively. Our first-hand knowledge of the technology along with our continuing commitment to safe working practices also makes us the ideal development partner for Bell, and we are keen to be involved with the continued development of the system and the extent to which it can be used.
‘However, the system will always only ever be a supporting security device that has to be managed and integrated into a workforce that has an interdependent behavioural approach to safety. Most recently, we have been looking at how it can support site and operator safety. This has resulted in the system being able to monitor not just a machine’s production performance, but also vital safety elements such as physical stability and tipping points.’
It is this partnership that has allowed Bell to continually, effectively and realistically fine-tune their ‘Safe-Tip’ on-board offering. As such, improvements including the development of more effective tipping angles and more precise reporting systems are now evident within the company’s latest E-Series machines.
Nick Learoyd, managing director of Bell Equipment UK, explained: ‘Safety, for both the operators of our ADTs and the ADTs themselves, has been fundamental to the Bell Equipment ethos since our first trucks were designed and manufactured. This has continued and led to the development of our industry-leading Fleetm@tic system. Working with Chepstow Plant has allowed us to fully research what this system is capable of, with on-the-ground trials providing invaluable information to help us fine-tune its features and performance. As such, we are confident that the latest E-series ADTs have only cutting-edge safety technology on board. However, as our ‘Safe-Tip’ software has been fitted ‘as standard’ to Bell Equipment models since 2008, even our pre-owned models can be considered the safest on the market, compared with their contemporaries,’ he added.
- Subscribe to Quarry Management, the monthly journal for the mineral products industry, to read articles before they appear on Agg-Net.com