Making Earthmover Tyres go the Distance
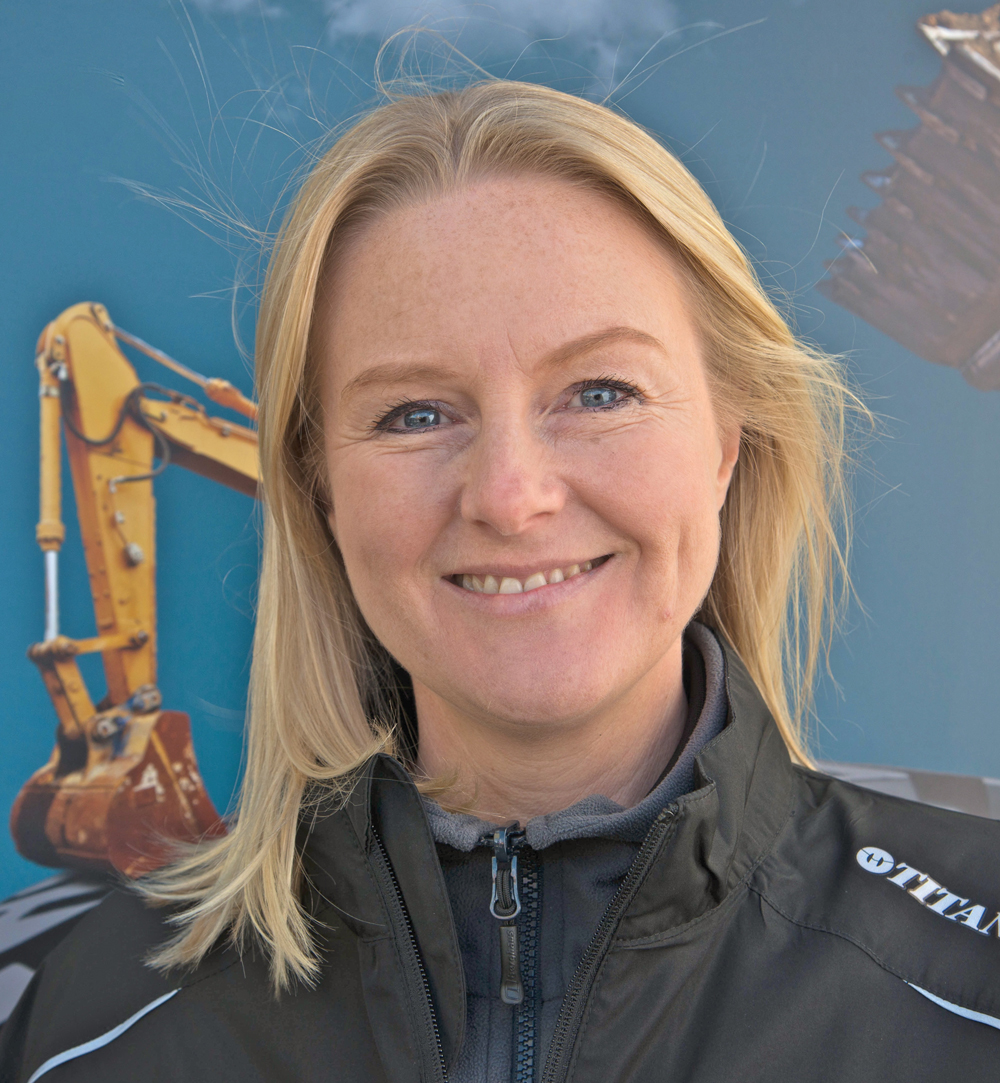
First published in the November 2016 issue of Quarry Management as Making Tyres go the Distance
In light of a recent industry report highlighting that a third of manufacturers consider site maintenance to be reactive rather than regular, global tyre manufacturers Titan Tyres are urging those in the extractives sector to regularly carry out safety checks on their tyres to keep them running for longer – and keep employees safe.
With damaged tyres costing companies not just the price of replacement, but also potential site downtime and project delays, Titan are encouraging manufacturers to put in place a regular maintenance programme to preserve tyres and keep them in good condition.
Lindsay Hart, European tyre sales manager at Titan Tyres, explained: ‘Leaving your tyre maintenance until it’s too late can incur costs of thousands of pounds for businesses – but it’s a cost that could be avoided by investing time in regular visual inspection and monitoring.
‘Considering the harsh environments that earthmover tyres are up against, it’s not surprising that they are often exposed to serious impacts and cuts that, if not monitored and treated, can lead to costly damage. A few simple tests and repairs built into the timing plan, however, can make all the difference, and save a tyre before the damage goes too far.’
Titan have compiled a simple set of maintenance checks that, if carried out regularly, can make tyres go the distance:
1. Lighten the load:
Every tyre is designed to carry a specific load at a specific inflation pressure. The inflation pressure of a tyre carries this load and the tyre’s carcass strength determines the pressure capacity, so it is important to ensure that the tyre is not overloaded. Putting additional load on a tyre will result in over deflection and reduced tyre performance. The load capacity of a tyre is also related to the travel speed of the vehicle. Industry standards associations, such as ETRTO and T&RA, publish a table of loads at specified speeds, providing a helpful tool to explain how the speed, load and pressure ratings correlate.
2. The importance of pressure:
Incorrect tyre pressure can cause a multitude of irreversible problems including premature wear and carcass fatigue. As part of regular vehicle checks, cold inflation pressure should be monitored on a weekly basis. Inflation pressure recommendations should be determined for each wheel position taking into account the actual loads that the tyre is subjected to. These vary with service type, distance and speed. Correct inflation pressure ensures the designated load can be carried at the required speed and helps reduce impact breaks, tread cuts and separation.
3. Inspect your sidewalls:
A daily visual inspection is essential to allow any changes or issues to be spotted and assessed early on, so action can be taken before tyres become irreparable and unusable. Checking regularly for cuts, bulges, uneven wear or foreign objects wedged in the surface of the tyre is extremely important. Frequently, tyres can continue running with superficial tread and sidewall cuts, and small cuts can be repaired without removing the tyres. If a cut penetrates the belts or cord body, the tyre should be immediately dismounted for repair by a tyre service team.
4. Get the balance right:
It is important to ensure, on a regular basis, that tyres are correctly aligned to prevent premature and uneven tyre wear, and to eliminate vibration (which can impact on health and safety protocols) and damage to the vehicle’s suspension, steering and bearing systems. Tyres fitted on dual assemblies must match in overall diameter. Differences in the size of the two tyres on a dual assembly will mean that the load is unevenly distributed, with the larger tyre carrying the greatest share of the load. This can result in a much faster wear rate as well as putting the tyre under unnecessary stress and making it more susceptible to damage. The smaller tyre will also suffer from irregular wear pattern reducing the life of the tyre. As well as size, duals must be matched in industry code and construction type – radial and bias should not be combined on a dual assembly.
5. Check the rotation:
Tyre rotation is also an essential part of any tyre maintenance programme to ensure even tread wear and long tread life. Rotation is necessary due to the uneven wear characteristics of each wheel position on the vehicle as front tyres are used in steering, while the rear tyres remain relatively ‘stationary’. The act of steering a vehicle creates scrubbing which can cause more stress for front tyres than those at the rear. Flip-rotating tyres on the axle will help minimize uneven wear and moving front tyres to the rear after a certain number of hours will ensure best use of the tyres over their lifetime.
For further information visit: www.titandistributionuk.com or www.titan-intl.com
• Subscribe to Quarry Management, the monthly journal for the mineral products industry, to read articles before they appear on Agg-Net.com