It Pays To Analyse
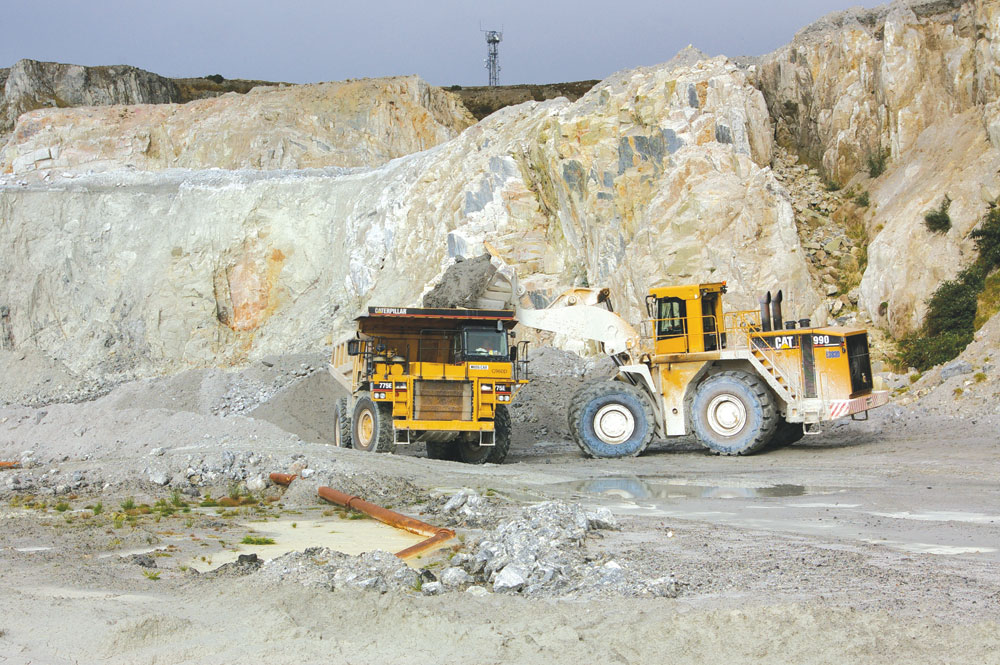
How Finning are using new technology to help customers reduce operating costs by tens of thousands of pounds
In the first trial of its kind, Caterpillar dealers Finning recently put a Cat 775F rigid dumptruck through its paces at Imerys’ vast Melbur Quarry china clay operation, in Cornwall, to prove that it pays to analyse fleet production.
The objective of the exercise, and the reason why Imerys released the Cat 775F from its normal duty, was to find out if Finning could prove how they could reduce the company’s fleet operating costs by tens of thousands of pounds, using the latest electronic wireless monitoring technology.
Operating eight Caterpillar off-highway trucks and a Cat 990 Series II wheel loader, the site itself produces china clay for the UK and overseas markets. With the Melbur fleet having been serviced and maintained by engineers at Finning’s local branch in Nanpean for a number of years, the data captured by the team on the Imerys-owned Cat fleet proved the starting point for the use of Caterpillar’s Fleet Production Cost Analysis (FPC) software.
The package allowed Finning staff to input parameters and the fleet mix in order to calculate where production savings could be made. Having identified the potential to make significant reductions in operating costs, relating to a reduction in parts, maintenance and overall fuel burn, Finning were challenged by Imerys to prove that their recommendations could deliver practical savings in the real-life application.
Instead of transporting hundreds of tonnes of highly abrasive material from the quarry face to designated tip areas at the site, the Cat 775F was, therefore, put to the test on a number of different gradients, with varying rolling resistances, to see how it performed.
Phil Lewis, Finning’s product manager for hydraulics and service, explained the importance of the tests, how they were set up and how the team of four, including Steve Platt, Finning’s Imerys customer account sales manager, Nanpean-based contracts manager Steve Tasker and a member of the Imerys operator team, worked together to collect the information. ‘What we are trying to achieve by offering this service to our customers through our 12 newly appointed regional customer account managers, is to deliver a step change in the way the industry thinks,’ he said.
‘Instead of selling customers machines and parts, and helping them to repair them, we are trying to change the culture of the sector by embedding the repair-before-failure philosophy. In doing so, we want to actually reduce costs for customers, in what I suppose could be seen as a consultancy role.
‘We know from our knowledge gathered over many years, that one of the main repair indicators with any large item of plant is the amount of fuel an engine has burnt, and not necessarily the hours it has done. What we are saying is, engine life is directly linked to fuel burn and our customers variable costs are, therefore, also linked to fuel burn.
‘The idea of the trial and testing was to understand how much fuel burn and strain was placed on the Cat 775F under different conditions over a set distance of 100m and with a set typical load of 66 tonnes. This way we would be able to show Imerys how changes to the site, such as decreases in gradients and rolling resistance, could ultimately pay dividends, helping them achieve an improved cost per tonne, per litre ratio.
‘Using the Caterpillar wireless electronic technician transmitter (ET), which links into the vehicle’s on-board computer, we were able to remotely log into the live operation of the machine from an outside position, at a safe distance from the truck.
‘Usually used to help our service teams perform machine diagnostics and calibrations, the ET device allowed us to download information as it happened. At the end of each exercise we were able to see the time it took to travel the 100m distance, the fuel consumption rate or burn, the engine’s revs/min, the gears used and the ground speed of travel, from a standing start. Therefore, by varying the gradient and rolling resistance, we were able to collect sample data on the typical operation of the Imerys truck fleet.’
Having identified different parts of the quarry with different gradients and different levels of rolling resistance, the team were able to collate data from five typical test sites. In order to achieve the correct timings, distance and gradient, Finning used an inclinometer, measuring wheel and stopwatch to collate some of the data needed. At the same time, Phil Lewis was able to capture the machine data via ET, while Steve Platt was able to monitor the driving of the Imerys operator to ensure the style remained constant.
‘Whenever you are putting together an experiment of this type, keeping as many points constant is crucial,’ explained Mr Lewis. ‘We were fortunate that throughout the day the weather stayed the same, as that would have certainly made a difference as the tests moved on.’
The results achieved by the team are shown in table 1.
Examining some of the detailed results that emerged, Steve Platt said: ‘Looking at the rolling resistance, which is classified as ‘the amount of tyre penetrating into the working surface’, with, for example, a 4% rolling resistance relating to 25mm of penetration, just comparing the difference between the industry standard 3 and 14 at 0% gradient is staggering. You can see from the chart that you would have to use more than double the amount of fuel to travel the same distance!
‘Of course, these are extreme conditions, but using a combination of the Cat FPC software and averaging the results, we were able to calculate that each of the eight trucks would burn an additional 0.6 litres loaded and 0.4 litres unloaded per cycle, moving through the same cycle four times an hour – giving a total saving of 4 litres per truck, per hour.
‘Taking the average hours run by each of the eight trucks in the fleet to be 3,200 hours per truck, per year, and the average cost of red diesel at 65p per litre, the possible savings over a year for the fleet could be £66,560.’
However, fuel cost savings are just part of the equation. The hidden cost that Finning are trying to show customers relates to the additional cost of maintenance. ‘As fuel burn is directly related to engine and component wear, if you reduce fuel burn by 5% you also extend the life of components by 5%,’ explained Mr Platt. ‘Therefore, if you translate this to an engine overhaul cost of say £30,000, a 5% increase in component life is an additional saving of £1,500.’ It is this factor that Finning are now able to quantify using this new technology.
But the good news does not end there, as there is an additional benefit to be gained by changing haul roads – speed. ‘In any quarry environment you have targets, so if you can work faster you are not only more likely to achieve or exceed these targets, you are also able to take strategic decisions regarding your fleet management and rotation,’ said Mr Platt. ‘You can see from the results that, in the best-possible scenario, we were able to travel the 100m in 18s, with the worst case scenario of 41s being more than double the time.’
Seeing the results of these tests and the many calculations that can be made with the figures created, it seems clear that the argument for fleet production analysis has never been stronger, and that there can be an instant return from the management of haul roads.
As the pressure continues to grow on quarry managers to reduce operating costs, there is a strong argument for investment in haul road maintenance using specialist equipment, such as motorgraders, as the savings to be made can more than pay for the added investment and longer-term payback in many ways.