How To Get The Most Out Of Earthmover Tyres
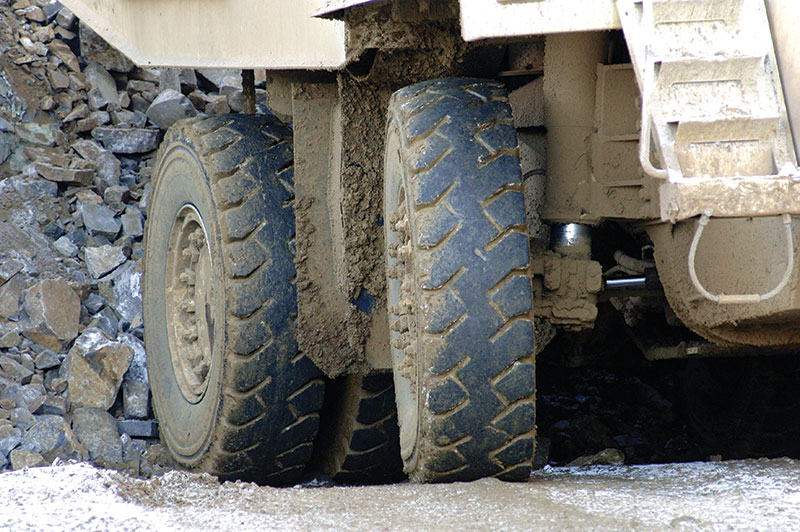
First published in the November 2014 issue of Quarry Management as Don’t Loose Your Grip
Michelin explain how the right tyre for the right job together with proper maintenance can help operators get the most out of their earthmover tyres
Tyres are often seen as a distress purchase by the earthmoving industry, which is perhaps not surprising given the investment required to replace them. But if the right quality of tyre is chosen for the right job, and those tyres are maintained properly, whole-life costs can be reduced significantly through longevity, fuel savings, improved performance and reduced downtime. Additional benefits of getting to know your tyres include added comfort, lower emissions and enhanced safety.
Choosing the right tyre
The industry has five machine category codes:
- C - Compactor
- G - Grader
- E - Earthmoving (Transport)
- L - Loader and Dozer
- H - Highway
The category for Compactor is used mainly in the road surfacing industry, Highway is used almost exclusively for mobile cranes, and specialized Grader tyres tend not to be used in the UK, where a Loader/Dozer tyre is preferred.
The industry has seven main tyre category codes:
- S - Smooth (no pattern, for mines and hard ground)
- 1 - Ribbed (circumferential ribs, for smooth surfaces)
- 2 - Traction (regular)
- 3 - Rock (regular)
- 4 - Rock (deep tread)
- 5 - Rock (extra-deep tread)
- 7 - Flotation (for soft ground)
Smooth tyres tend to be used in underground applications, Ribbed are mainly for ports and Flotation are for mobility over soft, yielding surfaces.
These codes are combined to highlight different applications, so an E3, for example, is a general-purpose transport tyre with a rock pattern, used where the risk of accidental damage is relatively low, while an E4 is a deep-tread transport tyre where a higher level of damage resistance and/or longer tread life is required.
Deeper-tread tyres have greater tread mass, but lower speed capability to offset the effects of the internal heat generated.
Some tyre manufacturers have developed products that do not fit exactly into the code system, so new codes, such as Super E3 or E3+, have been adopted to indicate a tyre that falls between the E3 and E4 groups.
Tread depths
Assuming that categories 2 and 3 have a standard level of tread depth of 100%, then category 4 will have approximately 150% compared with 2 and 3, and category 5 will have approximately 250%.
The deeper the tread depth, the lower the tyre’s ability to dissipate heat. Although an L5 tyre has about 2.5 times the original tread depth of an L3 tyre, it does not cost 2.5 times as much, so, ostensibly, the better deal would be to always opt for L5 tyres when buying loader tyres. However, a Michelin XHA2 L3 can be used for a maximum of 16km in an hour, while a Michelin X Mine D2 L5 tyre can be used for a maximum of 6km in an hour. If those maximums are exceeded, the tyres could overheat and fail.
Tread patterns
In general, the more rubber mass in the contact area with the ground, the slower the tyre will wear; the less rubber in contact with the ground, the greater the tractive effort from the tyre.
Loader tyres
There are two main types of operation that a wheel loader will undertake – working at the face in relatively arduous conditions and load and carry applications. Quarry managers need to take into account the exact conditions in which machines will be working and manage tyres according to the relative importance of tread life, damage resistance and traction.
Face machines, where damage resistance and tread life are priorities, would favour deeper-treaded tyres, whereas more open-treaded tyres would be better where traction is the key.
Wheel loader loading practice
Operator behaviour also affects tyre longevity and effectiveness. For example, tight turns and high speed will wear tyres more quickly. Presenting the dumptruck at a 45° angle to the material to be loaded is much more tyre friendly (see fig. 1).
Dumptruck tyres
Articulated dumptrucks (ADTs) are mainly fitted with traction tyres where it is possible to trace the tread groove from one shoulder of the tyre to the other. This leaves the choice between E3 (standard) or E4 (approximately 1.5 times the tread depth of E3) but usually only with a ‘traction’ tread pattern to cope with the demands of poor haul roads (fig. 2).
Rigid dumptrucks (RDTs) offer a wider choice, with the option of ‘rock’ or ‘traction’ patterns (fig. 3). A rock-type pattern offers high damage resistance and relatively long tread life but will provide less traction and will have a relatively small maximum distance per hour capability. The traction tyre will be good for traction and maximum distance per hour, but damage resistance and longevity will be reduced.
Factors affecting dumptruck tyre life
Tyre pressure
Pneumatic tyres are designed to be filled with a gas. In order to get the maximum tread contact area, the internal pressure is matched to the load imposed: the higher the load, the higher the pressure and vice versa.
A low pressure in relation to the load imposed results in a reduction in traction, uneven tread wear on the shoulder, wear from the flange on the tyre and increased fuel consumption. At extremes, the casing will be in danger of fatigue and failure.
A high pressure in relation to the load imposed also leads to reduced traction and uneven tread wear – this time in the centre. There is less resistance to damage and the risk of wear from the bead seat.
No matter whether the tyre is over- or under-inflated, there will still be the same amount of torque, steering, braking and load carrying to be undertaken. With less than the full tread footprint in contact, there is less rubber to transmit these forces and, therefore, wear is accelerated.
Running a tyre 20% under-inflated reduces tread life by about 25%, while 20% overinflation reduces tread life by about 30%. Running for just a couple of weeks at plus or minus 30% will have a major impact on tread wear (fig. 4).
Haul road gradient
Increasing gradients above 8% will result in substantially reduced tyre life. A 10% slope can lead to tyre life reduction of about 20%, while that figure jumps to more than 50% when haul trucks operate ‘downhill laden’ compared with running uphill laden on an 8% slope.
Haul road terrain and road conditions
If rock-free soil is taken as the ideal terrain for tyre life, that longevity is reduced by 10% when scattered rocks are present – and a similar reduction is seen on a maintained road with smooth gravel. A poorly maintained road with ungraded gravel reduces tyre life by at least 30%, and scattered blast rock reduces life by at least 40%.
Speed in curves
Having tight turns on a haul road can also have an adverse effect on tyre tread life. The tighter the turn, the lower the speed should be. Tight turns result in dynamic load transfer and can cause rapid tyre wear.
Conclusions
The factors outlined above have one thing in common: they can be controlled locally by the site.
Getting the most out of earthmover tyres should be a three way operation: the tyre manufacturer should provide recommendations for pressure and maintenance; the tyre service provider/dealer should examine the tyres on a regular basis and provide advice on when the tyres need to be changed and pressure maintenance; and the site itself should have a routine of visual tyre inspection and haul road maintenance.
If all three are in place and quarry managers learn how terrain and usage affect tyre life and performance, the savings and productivity benefits can be significant.
- Subscribe to Quarry Management, the monthly journal for the mineral products industry, to read articles before they appear on Agg-Net