How Retread Tyres Offer a Beneficial Alternative to New Earthmover Tyres
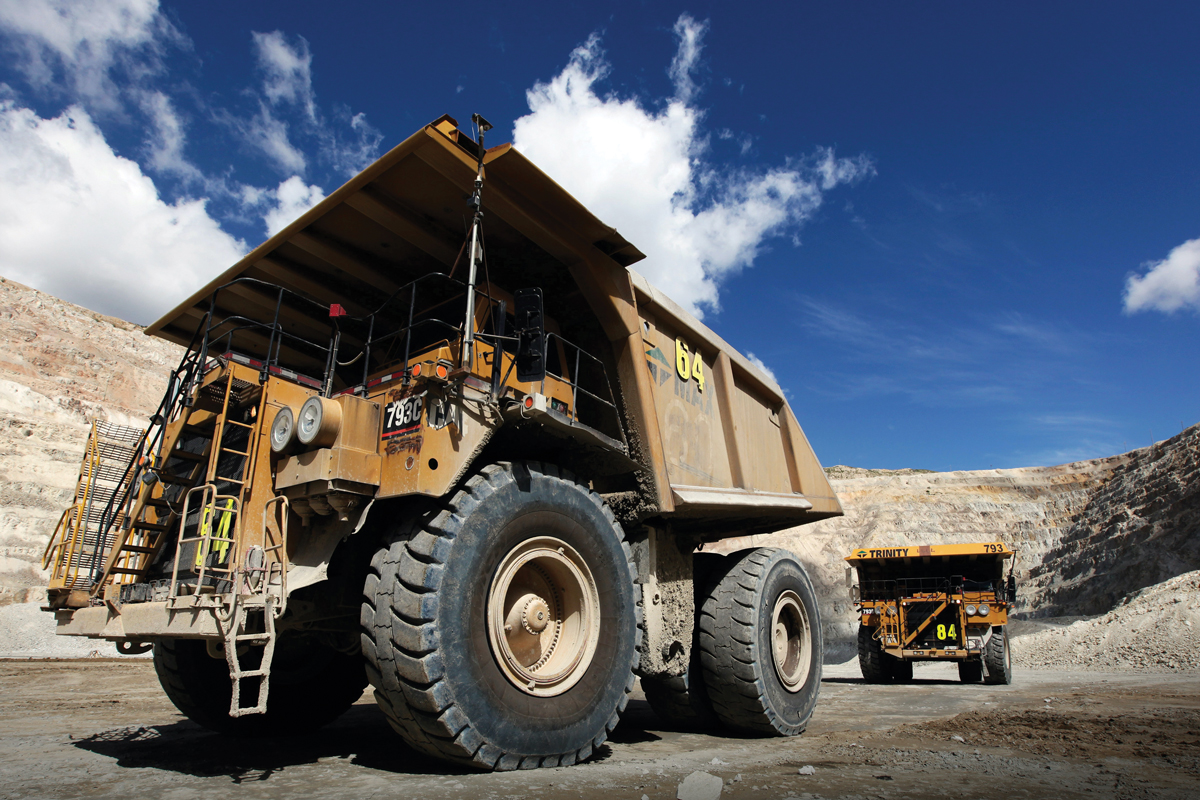
First published in the June 2020 issue of Quarry Management as Going the Distance
Kal Tire UK have more than 40 years’ experience and knowledge of manufacturing retreaded off-the-road (OTR) tyres, and as quarry operators continue to face both cost and environmental pressures – retreading is perhaps more relevant today than ever before. At the beginning of this year, before the coronavirus lockdown, QM visited the company’s Alfreton manufacturing facility, in Derbyshire, to see how retreading offers a cost-effective and environmentally beneficial alternative to the purchase of new earthmover tyres.
As the coronavirus (COVID-19) pandemic continues to evolve, these are indeed challenging and extraordinary times. The impact of COVID-19 is being felt by all companies across the globe and the strategic focus for many is now turning to what the competitive landscape will look like in the aftermath, what it means for their business and how to come out in front.
In the UK, business activity has plunged to an unprecedented level. Key industries such as quarrying, manufacturing and construction are now taking a measured approach to safeguard their workforces and mitigate the financial impact of COVID-19.
Given the economic downturn, managing mobile plant efficiently, driving operational costs down and implementing energy-saving initiatives will become more important than ever for quarrying/mining businesses, to ensure that they not only survive the coronavirus impact, but also thrive commercially in the long term.
In these extremely challenging market conditions, every part of a quarrying operation will be under close scrutiny, as construction materials firms look to take complete control of their machinery, fleet maintenance and operating costs, with the overriding focus on delivering the lowest cost per tonne.
‘To meet the challenges of the mineral products sector, businesses need mobile plant and processing equipment that operates efficiently, safely and reliably,’ said Alwyn Cox, general manager of Kal Tire UK, one of Europe’s leading earthmover tyre specialists.
‘In an industry focused on reducing running costs, improving sustainability and sharing best practice in health and safety, we have already taken major steps in providing outstanding aftermarket care and delivering tyre-management solutions that maximize safety, productivity and value for our customers in the heavy-duty earthmover sector.’
Perfect partner
Founded in 1977, Kal Tire UK – formerly known as OTR Tyres Ltd – started out as an independent tyre supplier servicing the opencast coal industry in England. Since then the Alfreton-based company has grown rapidly, moving away from its traditional customer base to serving and operating in all OTR market sectors, including quarrying, construction, waste management and port handling.
In 2009, the OTR Tyres business became part of Canada-based Kal Tire’s Mining Tire Group (MTG) and the trading name ‘Kal Tire UK’, along with a new brand identity, was adopted to reflect the global identity of its parent company.
‘Kal Tire’s acquisition of OTR Tyres was a win-win for all,’ recalled Mr Cox. ‘It allowed both businesses to improve their market position internationally and deliver the best tyre products and global best practices for safety and service in the heavy-duty earthmover tyre market. The acquisition was also an excellent strategic fit for Kal Tire Mining Tire Group; both firms shared the same core values, commitment to raising health and safety standards and client-focused approach.’
Headquartered in Vernon, British Columbia, Kal Tire MTG are one of the world’s leading OTR tyre manufacturers and dealers, employing more than 2,700 team members in 19 countries across five continents. The company’s long-standing experience and expertise in servicing the heavy mining industry stretches back over 45 years and its success today can be seen in more than 150 open-pit and underground mines across the world.
Mutual success
With quarrying/mining operators under constant pressure to reduce costs and increase productivity, nothing is more important than uptime. Earthmover tyres typically account for 25–30% of haulage operating costs in quarries and open-pit mines, so the ability to control theses overheads is not only a valuable asset-management tool, but also a critical part of the overall production process.
By implementing a holistic approach to a fleet’s overall performance and putting in place a machinery maintenance strategy that is geared towards operational safety and prolonging the service life of parts/components, quarry operators can improve their equipment uptime and productivity. However, there remains a tendency for the maintenance of mobile plant and processing equipment to be carried out on a reactive basis, despite a number of significant disadvantages to this approach.
This is because planned and regular maintenance are often viewed as an expensive requirement involving skilled labour and machine downtime. This is a mistake that many businesses make and can often be directly related to a decline in plant performance which, in turn, affects the bottom line in terms of running costs and profitability.
The need for tyre management and maintenance becomes even more critical given the harsh and demanding environments in which earthmoving equipment is expected to operate in the mineral extractives sector.
Carrying out regular maintenance inspections on key items of mobile plant – not least OTR tyres – will help maximize machinery uptime, improve operational efficiency and ensure that the risk of expensive reactive work is reduced substantially through scheduled servicing and routine safety checks.
Kal Tire UK are one of very few earthmover tyre companies in the sector offering a complete tyre-management programme that includes selection, repairs, tracking and reporting, maintenance and site studies, all carried out by fully trained service technicians. The business recognizes that if customers are going to manage their equipment successfully, it needs to support them with a bespoke solution every step of the way – from tyre sourcing, fitting and maintenance to optimizing productivity and performance.
‘The traditional relationship between tyre manufacturers and quarries has always revolved around price, rather than value, or increasing tyre service life as much as possible,’ commented Mr Cox. ‘However, the construction materials market in recent years has evolved and changed, as more and more quarrying companies are looking at the bigger picture when it comes to fleet optimization.
‘As the UK market leader in earthmover tyre service and supply, we place a strong emphasis on innovation and operational best practice. We are constantly looking at innovative ways to improve our tyre products and full-service offerings, in order to be able to meet the demands of our customers.’
With approximately 100 team members operating from seven strategically located depots in Alfreton, Falkirk, Birtley, Cardiff, Standon, Liverpool and Launceston, Kal Tire UK are able to provide a rapid response to customers with urgent enquiries and tyre requirements.
Explaining what makes the company stand out from other OTR tyre suppliers and specialists, Mr Cox said: ‘We see our ourselves as partners to our customers by taking full ownership of the tyres on the client’s behalf. This close collaboration means Kal Tire get everyone involved on site, from the quarry manager and plant operators to tyre technicians, all taking responsibility for their role and, ultimately, maximizing uptime, reducing tyre-related costs and downtime, and contributing to a low cost-per-tonne productivity.’
A new lease of life
In better economic times, many quarry managers and fleet operators might have sneered at the idea of using remanufactured (reman) plant rather than investing in brand-new equipment that offers reliability and robustness. There is a widespread perception amongst consumers that reman parts and components might be of lower quality than their respective newly built products.
However, the remanufactured option has proven to deliver the same performance and reliability as an all-new product, while reducing the impact on the environment. There are also substantial cost savings to be gained from remanufacturing. Studies have shown that remanufactured parts cost 25–50% less than brand-new parts and reman products often come with a standard 12-month warranty, which helps protect the overall value of the plant.
While companies may have to restructure and rethink their business strategies with reduced workforces and tighter budgets due to the financial pressures of the COVID-19 outbreak, taking the remanufacturing approach could help quarrying firms prepare for the economic uncertainty.
At Kal Tire UK, retreading and remoulding services are performed at the company’s Alfreton factory, in Derbyshire, to give OTR tyre casings a ‘second life’ at the fraction of the cost of new tyres. As with all Kal Tire retreads, the company only uses quality casings and the latest compounds and processes to produce retread tyres that offer like-new performance and long, reliable service life for mine- and quarry-spec machines.
‘All worn tyres that arrive at the Alfreton site are rigorously inspected and tested to see whether they meet our stringent safety and quality-control requirements for new tyres,’ said Darren Flint, vice-president of tyre lifetime services and vice-president of European and West African operations for Kal Tire MTG.
‘From the customer’s point of view, retreading is an environmentally friendly and cost-effective solution that reduces the reliance on new tyre purchases. Every year, we retread around 2,000 tyres in the UK and save thousands of tyre casings from being prematurely sent to scrap piles.’
The Alfreton plant – which operates a Lean manufacturing methodology – offers customized retreads/remoulds (from 25in to 49in) to meet the needs of all OTR tyre users in the replacement tyre market. The factory also stocks and supplies manufactured earthmover tyres in a variety of compounds and tread patterns to suit site-specific conditions where standard specifications are deemed inappropriate for use.
As the demand for retreads and extending tyre life has grown, Kal Tire MTG have continued to invest heavily in new technologies, modern warehousing and digitalized processes to ensure their operations are smoother, smarter and swifter, not to mention more cost-effective.
Last October, Kal Tire MTG opened their sixth OTR retreading and repair facility in Cananea, Mexico, adding to the company’s existing sites in Canada, Chile, Ghana and the UK. Product innovation is the lifeblood of the business and the Latin American plant is the first Kal Tire retread facility to use robotic process automation for skiving and tread grooving.
The implementation of machine-control technology and automated production processes will allow the company to provide greater flexibility in terms of lead times and custom tread specifications, as well as increased efficiency, accuracy and safer use of tools and equipment.
‘The manufacturing sector is a highly competitive, fast-changing industry,’ commented Mr Flint. ‘In today’s dynamic business environment, we cannot rest on our laurels and as every entrepreneurial organization knows, you have to be thinking of tomorrow, the radically changing global markets and the innovative products and services that customers need.’
Competent workforce
Kal Tire UK see industry training as an integral part of their business and, as such, have continually invested in the ongoing professional development of their staff to ensure that every team member has the right level of skills, knowledge and, more importantly, competence to do their job properly.
The investment is also a clear indication of the company’s commitment to further improve its safety standards which, according to Jason Fury, health and safety manager of the UK and West African operations for Kal Tire MTG, is the highest priority for the business.
‘Health and safety are at the heart of everything that we do,’ commented Mr Fury. ‘All our team members are engaged with the ‘Journey to Zero’ programme, which is Kal Tire’s commitment to pursue the highest standards of health and safety, with the goal of ensuring every employee and visitor returns home free of harm at the end of each working day.
‘Fully trained operatives are valuable assets, so it is important that we ensure all our staff have refresher training and carry the necessary safety certification and credentials to be able to demonstrate their professional competence and help create a safe working environment by identifying, eliminating or reducing the occupational risks and hazards.’
As part of the competence drive, every Kal Tire team member has a tailored curriculum based on the requirements of their role. For example, the company certifies its tyre technicians through a rigorous training programme (over a 27-month period) that encompasses more than 300 course modules consisting of both technical learning and hands-on competency evaluations.
The firm has also established a comprehensive range of safe work procedures to get all employees thinking not just about their own safety, but also of colleagues, contractors and visitors. These include: daily toolbox talks that focus on timely and relevant topics (eg moving plant, working at height, earthmover tyre inflation etc), to ensure that safety awareness is always ‘top of mind’; and a wealth of guidance/information accessible through Kal Tire’s Leaning Management System (LMS), which is a complete library of all current procedures and best safety practices from the tyre industry.
As a business committed to driving the safety agenda, Kal Tire MTG have invested in a state-of-the-art health and safety management system aimed at embedding a culture of accountability and ‘thinking safely’ at every level of the organization.
The company’s Velocity reporting system monitors and tracks any accidents, incidents and near misses, giving employees, supervisors and managers total transparency and the same up-to-date information across the business. It also allows team members to create and carry out audits, implement corrective measures and raise actions related to unsafe behaviour, tools or equipment, which have the potential to lead to an incident.
‘Tyre fitting is an inherently high-risk activity in a high-risk environment with the potential for seriously life-changing injuries and, ultimately, fatalities,’ said Mr Fury. ‘Using a management system like Velocity facilitates worker involvement and improves a safety culture throughout the company. By making health and safety everybody’s responsibility, it should lead to a safer, more visible and healthier working environment that will have a positive impact not only on our employees, but also on our customers.’
Leading the way
Given the present UK economic slump, many quarry/mining operators will now be implementing more efficient ways of increasing mobile plant uptime, improving energy efficiency and, ultimately, achieving the lowest cost-per-tonne rates.
When looking at the big picture, heavy-duty earthmover tyres are no small investment. Damage to these tyres in arduous environments (eg quarries, waste sites, opencast coal mines etc) is inevitable, effectively costing businesses not just the price of replacement, but also potential machinery downtime and production delays.
In today’s cost-conscious climate, it is critical for quarrying firms to gain maximum value from their earthmoving fleet investments by increasing uptime and minimizing unplanned maintenance and tyre failure. Kal Tire UK have the expertise to deliver on this front. Whether it is helping customers to maximize tyre performance, improve safety, extend service life or reduce the total cost of ownership, the company’s cradle-to-grave approach has transformed how mobile plant operators are managing their heavy vehicles and equipment.
Like many forward-thinking organizations, Kal Tire UK still have a number of ambitious growth objectives to fulfil as they look to deliver full service and support in all sectors of the construction products industry, whilst underlining their status as the supply partner of choice in the OTR tyre market.
- Subscribe to Quarry Management, the monthly journal for the mineral products industry, to read articles before they appear on Agg-Net.com