Fuel Duel
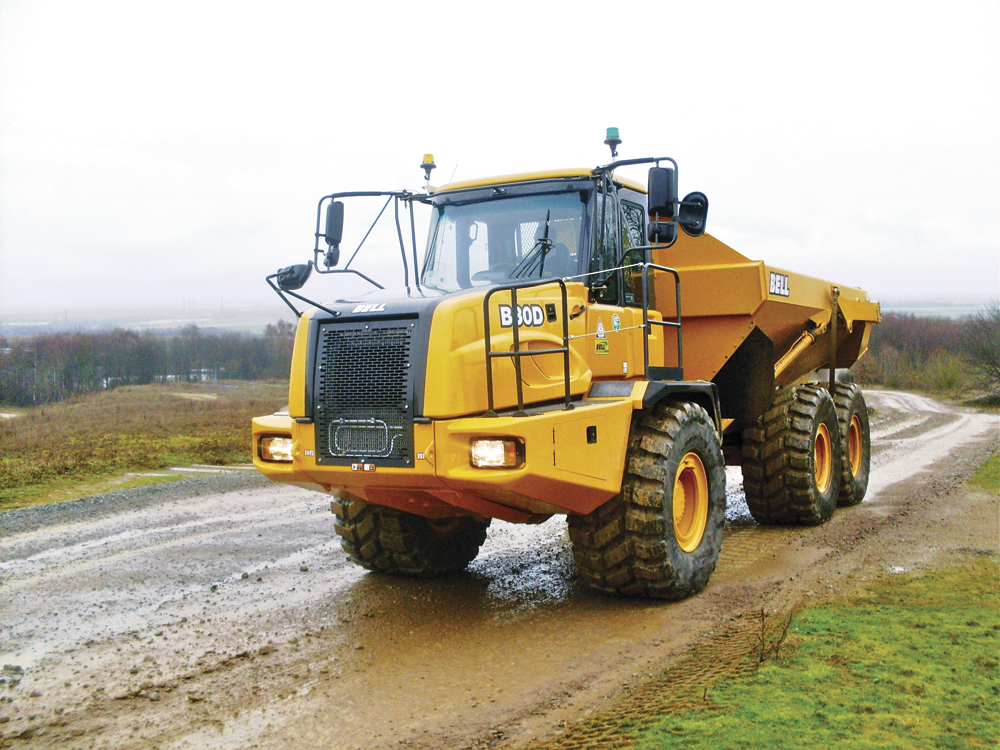
Bell’s new SCR technology outshines competition in independent test at Millbrook, highlighting significant fuel-cost savings for operators
Much has been said about the cost of moving materials by articulated dumptruck (ADT). Initial purchase price, residual value, repair and maintenance costs, carrying capacity and fuel burn are all factors for the owner to take into consideration.
However, the cost of fuel has increased so much recently that fuel burn (litres per hour) has risen to the top of the pile when evaluating which machine to purchase.
Changes in legislation to minimize emissions have also led equipment manufacturers to re-design their trucks, with some going down the exhaust gas recirculation (EGR) route and some down the selective catalytic reduction (SCR) route.
Both options result in reduced emissions, but in very different ways. The EGR system recirculates the exhaust gases and captures the soot, burning it off at very high temperatures (usually increasing overall fuel burn). The SCR system is an after-burn treatment system whereby the exhaust gases are treated with AdBlue prior to being emitted to the atmosphere (ie no intrusion of recirculated gases into the engine).
This technology change has led to various equipment suppliers producing new series’ of ADTs. Bell have continued with the success they have had with Mercedes engines over the past 12 years in their ADTs. This means that Bell’s new MK6.3 ADT, which complies with Euro Tier 3b emissions regulations, is based on Mercedes’ proven SCR technology.
The major factors behind Bell making this decision were:
- Lower owning and operating cost: less redesign of the overall machine was required, so minimum impact to machine price increase; better fuel economy with no changes to the engine; and no changes to service intervals or service components.
- Better productivity and uptime: no regeneration stoppages; overall power to weight for acceleration and speed; no retraining for operators and field technicians.
With these changes in mind, Bell UK decided to commission the Millbrook Proving Ground to conduct an independent test whereby two different ADTs could be put through their paces on two measured, timed and independently monitored track-based drive cycles.
Testing time
Millbrook Proving Ground is one of Europe’s leading locations for the development and demonstration of every type of land vehicle, from motorcycles and cars to commercial, military and off-road vehicles. Bell UK chose this arena so that the results would be transparent and credible within the industry.
The trucks tested were the latest Bell B30D MK6.3 and the latest Volvo A30F. Both were fitted with tailgates and 750mm wide tyres. Manufacturers’ specifications were given to the Millbrook team so they could ensure the manufacturers’ guidelines were adhered to. Both machines were operated by trained, independent Millbrook personnel.
To accurately measure speed, distance and location, a GPS data-logger was fitted to each truck prior to the test commencing.
The first test undertaken was designed to measure and compare fuel consumption results on a high-speed steady-state route, with the second test being on a more typical cross-country route. Both machines were ballasted to their rated payload and fuel consumption was measured over two repeatable tests.
High-speed steady route
Before conducting this test the trucks were driven through a warm-up schedule consisting of three laps of the high-speed circuit at a top speed of 40km/h. The trucks were than accurately filled with fuel prior to the actual test.
The test consisted of accelerating from rest to 40km/h for a distance of 40km. On completion of the test the trucks were taken back to be refuelled and, with the Bell B30D, AdBlue usage was also measured.
Cross-country circuit
Once refuelled, the trucks were taken 10 times around the cross-country circuit, which consisted of a 3.1km off-road test track featuring various uphill and downhill grades to simulate on-site conditions. The machines were then refuelled, with AdBlue usage measured again on the Bell B30D truck.
Test results
On the high-speed steady-state route the Bell B30D MK6.3 proved to be 6% more fuel efficient, while on the cross-country circuit it was found to be 17.6% more fuel efficient.
These results show that the harder that each truck worked, the more fuel efficient the Bell B30D became over the Volvo A30F; the cross-country circuit being more typical of the general muck-shifting environments that most of the trucks of this size operate within.
When equated back to actual cost, with fuel now costing in the region of £0.70 per litre, and based on an average fuel burn of 12 litres/h, the Bell B30D’s saving on fuel alone equates to £1.48 per hour.
Neville Paynter, managing director of Bell Equipment UK, said: ‘The tests at Millbrook pretty much confirm what we thought, and we’re delighted with the results. It’s particularly significant today, when fuel prices continue to eat away at operators’ margins.
‘Bell have always led the field in fuel economy, but this is the first time that our new SCR technology has been scientifically tested against one of our competitors’ trucks. The test conditions were very strict – the Millbrook assessors wouldn’t let us anywhere near while the data was being collected. Not only that, we put the B30D up against a machine that is one of the leaders, if not the leader, in its class in terms of popularity.’
Mr Paynter added: ‘It should give our customers absolute confidence that they are saving thousands of pounds in fuel costs – the single biggest expense now for a plant operator. The indicators from this independent test are highly significant for anyone who operates ADTs, and we do not envisage any manufacturer challenging us.’