Bells At Lee Moor
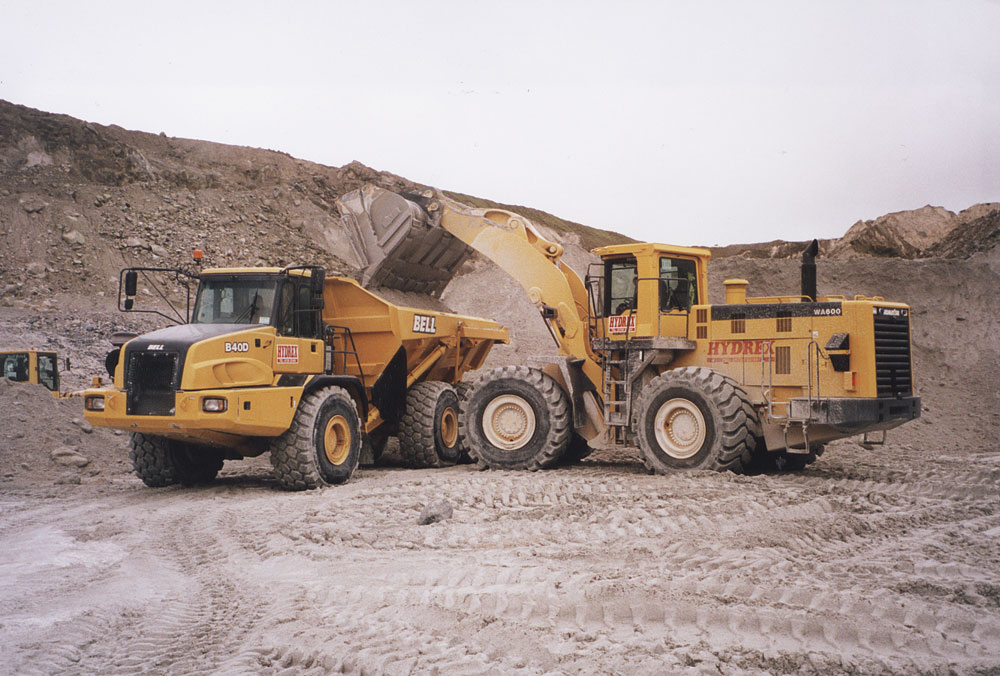
Hydrex and Imerys load up with Bell ADTs
The recent decision by French-owned kaolin producers Imerys to convert their Lee Moor site in Devon from a hydraulic mining operation to a dry mining technique has, according to the company, resulted in reduced mining costs, more flexible mining and greater selectivity at the site. However, as well as benefiting Imerys, the transition has also proved advantageous for two other major companies — Hydrex and Bell.
Bristol-based Hydrex Equipment Co., identified by Imerys as one of their preferred equipment suppliers, have been contracted to supply a mobile plant fleet which, each year, will be required to move some 4 million tonnes of material consisting of matrix, sand and rock. Hydrex recently acquired 18 South African-manufactured Bell B40D articulated dumptrucks from Bell Equipment’s UK base at Burton upon Trent, 13 of which have been allocated to Imerys’ Devon and Cornwall operations, including nine to Lee Moor.
According to Tony Knight, Imerys’ mobile plant operations manager, initial feasibility studies to convert the mining technique at Lee Moor were conducted in 1997, and a new processing plant for the dry mining operation finally came on stream in 2001.
The origins of clay mining in Cornwall, however, date back to the 18th century with the discovery of china clay in 1746. Today, some 250 years later, the product is Britain’s second largest raw material export after North Sea gas.
Imerys Minerals, one of the world leaders in the production of china clay and kaolin, operate in 34 countries and employ some 14,500 people globally with 2,500 in the UK. The company has its European clay headquarters in St Austell, Cornwall, and operates china clay quarries in Cornwall and South Devon; ball clay operations in North and South Devon and Somerset; carbonate operations in Salisbury and at Beverley, near Hull; and a processing plant at Stoke-on-Trent.
The production of china clay at Imerys’ UK quarries amounts to around 2.5 million tonnes a year, 88% of which is exported. Major markets for the product include Scandinavia, where it is used in the manufacture of paper, and Spain, where it is used in the production of sanitaryware and tiles. The company’s largest china clay pits are at St Austell, where some 9,000–11,000 tonnes of finished product are produced every week.
The transition from wet to dry mining at the Lee Moor site, located on the edge of Dartmoor, not far from Plymouth, called for a change in haulage vehicles from the rigid trucks used in wet mining to a fleet of ADTs for the dry operation.
‘We carefully researched both the equipment to be used and the supplier,’ ‰ explained Tony Knight. ‘The criteria demanded that the supplier had to provide competitive rental rates and had to be a company possessing a solid infrastructure which would be able to sustain the availability of its equipment. Furthermore, the machines had to conform to Imerys’ specifications and to environmental and safety requirements.
‘Our machines use around 200,000–250,000 litres of fuel and oil in the course of a week, so we were looking for economies of scale on fuel consumption,’ said Mr Knight, who added that the articulated dumptrucks are used to haul dry matrix from the quarry face to the processing plant, a distance varying from 3?4km to 3km, as well as for the removal of waste from the processing plant to the waste tips, a haul distance of anywhere between 1.6km and 5km.
These matrix and waste operations are carried out over 12h shifts, seven days a week, depending on product demand, and Imerys carry out stringent and continuous trials on the haulage machines to determine their fuel consumption. According to Mr Knight, the operating costs of the mobile plant at Lee Moor constitute about 60% of the overall mining costs.
In mid-2001 Imerys tested a Bell B40CM ADT, their first experience with this make of truck. Following a four-month evaluation, with the machine being monitored against other ADTs of competitive manufacture, the results indicated that the fuel consumption of the Bell machine was some 5–8% less than its counterparts. It also performed well in terms of cycle times and provided high levels of mechanical availability, while holding its own in all other areas of operational performance.
‘We were impressed with the performance of the Bell ADT, but this didn’t mean that our contractual agreement with Hydrex Equipment was dependent on the selection of Bell machines,’ added Mr Knight. ‘The choice of mobile plant was mutually agreed between Hydrex and ourselves, based on the budgeted requirement to move
4 million tonnes of material a year.’
Andrew Simcox, managing director of the Hydrex Group, said Imerys’ transition from wet to dry mining had resulted in both companies working together on the project in a synergistic team effort.
‘The Hydrex Group, whose turnover for 2002 is expected to be around £40 million, consists of several complementary operating divisions — Construction Services, Industrial Services, Rail Services, Machine Sales and Parts Sales — but it is the process-orientated Industrial Services division, which operates some 400 units of major capital equipment, that is implementing the Imerys contract,’ explained Mr Simcox.
He added that Hydrex Equipment had formed a relationship with Imerys about two years ago when they supplied equipment to the company on a smaller scale and opened a depot at their St Austell base.
‘We set out to understand Imerys’ business and method of operating. Their total equipment requirements for Lee Moor included ADTs, dozers, hydraulic excavators and four wheel loaders ranging from 24 tonnes to 45 tonnes. However, owing to the challenging gradients and harsh conditions in the clay pits, trucks offering maximum braking efficiency were a key factor.’
Hydrex tested the Bell B40D units in a competitive demonstration over a two-week period, monitoring their performance against two other leading ADTs. The results of this demonstration revealed that the Bell units were the most fuel efficient, while their standard multiple wet-disc brakes and transmission retarders provided very effective braking capabilities. The B40Ds also demonstrated very good traction and gradeability, and Hydrex’s operators were said to be highly impressed with the machines.
‘Having satisfied ourselves with regard to the capabilities of the machine, we also talked to other Bell users who confirmed that Bell Equipment provided an efficient and reliable after-sales support service,’ said Mr Simcox. ‘Based on this research, we purchased 18 B40D units, nine of which have been allocated to Lee Moor and four to Dorothy pit in St Austell. The other machines were purchased to work in an unrelated civils application in Scotland.’
Bob Aldridge, sales and marketing manager for Bell Equipment UK, described the Imerys/Hydrex/Bell deal — one of the largest single orders for B40Ds supplied by Bell in the UK — as a tripartite partnership, as opposed to a machine rental agreement on the one hand and a machine sales deal on the other.
‘The success of this venture is entirely dependent on the synergistic relationship formed by the three companies, with each having a key role to play,’ he said.