Clearing The Air
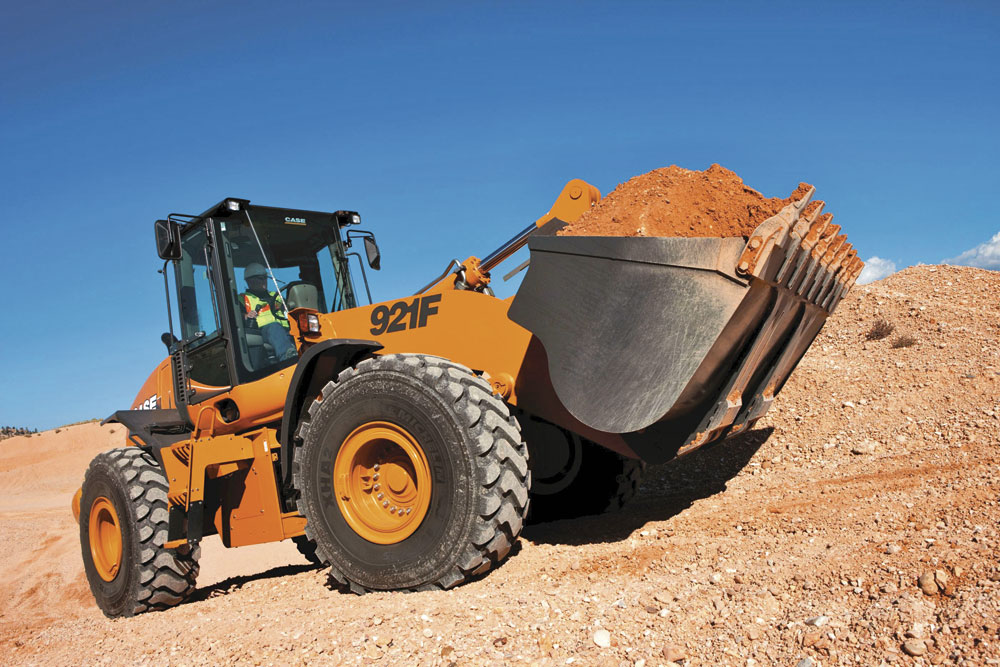
As the move is made to Tier 4 Interim emission control, and with Tier 4 Final looming on the horizon, manufacturers are taking varying approaches to exhaust after-treatment in order to comply with the legislation. Dan Gilkes investigates
Regulation and legislation shapes almost every aspect of the way that companies work today. From health and safety to manual handling, hazardous substances to explosives, every activity in the quarrying business is clearly defined.
It is no different in the plant and machinery market where new exhaust emission legislation is once again coming into effect as the move is made to Tier 4 Interim (or Stage IIIB in the USA). This time, however, the engine regulation will not only affect the bottom line, in terms of productivity and running costs, but in many cases will require new working practices as well.
For almost three decades now, emissions legislation has become increasingly stringent both in the EU and in the US market, where the Environmental Protection Agency (EPA) sets the standards. While passenger car regulators have concentrated on carbon dioxide (CO2) as the main pollutant, heavy diesel engine legislators have called for ever-smaller emissions of particulate matter (PM) and oxides of nitrogen (NOx).
Developments have already come a long way, with engines currently producing a fraction of the harmful emissions of 20 or 30 years ago. For instance, one on-highway truck of 30 years ago would have produced the same amount of PM as 50 of today’s vehicles. Now, however, the regulations are calling for a further 90% reduction in PM, compared with Tier 3/Stage IIIA, and a 50% drop in NOx.
For engine manufacturers this has led to increased efficiency within the engine through the use of four valves per cylinder, increasingly complex turbochargers (including variable-geometry turbochargers), higher-pressure common-rail fuel-injection technology and more sophisticated engine electronics. However, it is only possible to go so far within the cylinder itself, and the point is now approaching whereby further reductions in emissions must be created outside the engine, through the use of exhaust after-treatment.
There are two main approaches to after-treatment: exhaust gas recirculation (EGR) or selective catalytic reduction (SCR), or indeed a combination of the two. As the name suggests EGR, or in most cases cooled EGR, takes a portion of the exhaust gas and puts it back through the engine, burning off more of the emissions and cleaning up the exhaust. SCR uses a catalyst with an injection of aqueous urea solution, commonly known as AdBlue, or diesel exhaust fluid (DEF) that reacts within the catalyst to reduce NOx.
Manufacturers are also installing diesel particulate filters (DPF) in the exhaust system to capture the PM within the exhaust, which is then burned off at regular intervals through a process called regeneration. This involves the injection of fuel into the DPF with a high volume of air to create very high temperature burning, cleaning up the emissions.
Active regeneration requires the operator to actually push a button when the DPF needs to be burned off, while passive regeneration will automatically start the process when due. Volvo have opted to indicate to the operator when regeneration is required on their new G-Series wheel loaders, normally after around 7–8h of operation. The company says that this is due to some of the types of operation that its loaders are involved in, such as handling sawdust or flammable waste, where it might be better to remove the loader from a potentially dangerous operation during regeneration as the DPF will get very hot. In either case, the process should not affect the performance of the machine, which can carry on working throughout.
For those manufacturers that have opted to go down the SCR route there is the issue of AdBlue, which is stored in a separate tank that has to be filled on a regular basis along with the fuel. AdBlue consumption is only around 5% of the fuel use, so refilling will not be required on a daily basis.
Though this technology will be familiar to many quarry operators running on-road tippers, it will create a new part of the daily routine for others. It will be particularly important for plant hire companies, especially those offering self-drive rental machines, to ensure that customers are aware of the need for AdBlue and the location of the tank.
One concern voiced by some observers is that, on a number of machines, the AdBlue tank filler is positioned next to the fuel filler, the only difference being the colour of the cap. It is easy to imagine the mistakes that could be made on a dark, rainy winter morning as the wrong hose is inserted into either the fuel or AdBlue tank.
In addition, if the AdBlue is allowed to run low, most machines will then revert to partial power until the tank is topped up, which will no doubt lead to many calls to technicians and hire companies as performance drops seemingly for no reason.
In addition, it appears that the purity of the additive is equally important, to avoid damage to the dosing system and the catalysts. Methods of storage will be an important consideration too, as AdBlue can deteriorate with time.
The good news for customers is that Tier 4 Interim machines seem to be achieving the impossible by offering increased power and lower fuel consumption. This is in part due to improvements in combustion efficiency, and also to the fact that engineers can now leave some of the exhaust clean-up until the gases have exited the engine.
Engine and machinery manufacturers have all had to tackle the same problems, but have gone about their resulting machine designs in different ways. JCB, for instance, insist that they can achieve Tier 4 Interim on their four-cylinder engine without having to resort to after-treatment, although the firm admits that it will probably be necessary for Tier 4 Final in 2014.
‘Meeting Tier 4 Interim legislation is a massive challenge but also a huge opportunity for innovation, an opportunity to come up with a solution that has real advantages for our customers,’ said Alan Tolley, JCB’s director of engine programmes.
‘Our strategy, therefore, has been to meet Tier 4 Interim emission standards without a DPF, but also to achieve this without any exhaust after-treatment. We have focused our research and development efforts on a high-efficiency combustion system. This approach also gives us very low fuel consumption levels, up to 10% lower than for Tier 3.’
CNH companies Case and New Holland have a variety of engine suppliers, but the main power behind both firms is fellow Fiat company Fiat Powertrain Technologies (FPT). It comes as no surprise, therefore, to see that both companies will be using a combination of cooled exhaust gas recirculation (CEGR) and SCR technology with the urea additive. These technologies have both been well proven by Fiat’s on-highway truck brand Iveco, so there should be few concerns for customers in the off-highway market.
Volvo also have heavy involvement in the on-highway markets, which gives them a lead when it comes to meeting the off-highway emissions regulations. Volvo’s V-ACT (Volvo Advanced Combustion Technology) engines have high-pressure fuel injection, cooled EGR, new engine management and an integrated exhaust after-treatment system, including a particulate filter and thermal regenerator. This regenerator incinerates the PM in the particulate trap at temperatures up to 700°C.
Last year’s Conexpo show saw the introduction of four Volvo loaders, the L150G, L180G, L220G and L250G, all equipped with Tier 4 Interim engines. The show was also a launch pad for the F-Series articulated haulers from the Swedish company, again using Tier 4 Interim/Stage IIIB engines.
Caterpillar also revealed their first Tier 4 machines last year, the initial one being the 336E crawler excavator. The firm has chosen not to use SCR at present, opting instead for EGR, an oxidation catalyst and a DPF on its ACERT engines. Caterpillar admit, however, that SCR is a technology being considered for Tier 4 Final/Stage IV.
For those companies not using in-house engine design, there is a lot of reliance on suppliers such as Cummins. The US firm has announced that its QSX15 and QSX11.9 engines will benefit from higher maximum outputs as the company announced its solution for Tier 4 Final. The 15-litre QSX15 engine will be tuned to produce a peak of 675hp, up 75hp on its Tier 4 Interim output, as a result of a blend of technologies for the after-treatment of particulate matter and nitrogen oxide. The 11.9-litre QSX11.9 engine also gets more power for Stage IV, with a new rating of 525hp.
Both engines share technology that combines a Cummins particulate filter with selective catalytic reduction, known as CPF-SCR, meeting legislation while giving higher power outputs and lower fuel consumption. Cummins claim the CPF-SCR after-treatment raises the threshold of what can be achieved in the trade-off between lower emissions and higher performance.
The smaller capacity QSL9 engine also benefits from this after-treatment process. The 9-litre, six-cylinder engine uses a blend of Cummins’ compact catalyst and selective catalytic reduction, known as CCC-SCR, to produce up to 400hp without any performance compromises. It is a package that will also be installed on QSB6.7, QSB4.5 and QSB3.3 engines to offer a common after-treatment solution from 75–400hp.
Perkins will offer a heavily revised 400-Series engine platform, known as the 400F. This range of three- and four-cylinder engines is based on the proven 400D range, but with the integration of a diesel oxidation catalyst (DOC) and diesel particulate filter, combined with electronic governing.
By refining the Tier 4 Interim compliant 400D into the 400F, Perkins say they have avoided the need to develop an all-new engine platform, creating a simple solution for OEMs. And with the DOC/DPF acting as the exhaust silencer, installation space required for this engine remains unchanged. The after-treatment system is predominantly a passive one, requiring ash removal every 3,000h. However, where the engine is to be used in low-duty applications, Perkins have integrated an automatic burner into the DOC/DPF to allow active regeneration to take place during engine idle, without intervention from the operator.
So what does the quarry operator need to consider on site? As well as storage and distribution of AdBlue and diesel exhaust fluid, there is the fuel itself to consider. Tier 4 Interim engines require ultra-low-sulphur diesel (ULSD) with a sulphur content of 15 parts per million or less. Fuels with a higher sulphur content can damage engine components and cause problems for owners.
Operators may also want to ask their fuel supplier about the cetane rating of the diesel that they are delivering to the site. The cetane rating of road fuel is a minimum of 51, in line with EN590. However, red diesel can vary, with gas oil, in particular, having a minimum level of just 45. Some companies are, therefore, promoting the idea of fuel additives to boost cetane ratings, leading to improved combustion and better engine reliability.
Some manufacturers are also calling for the use of low-ash engine oils, as they are more resistant to heat and allow engines to run DPFs with long regeneration intervals.
Fleet managers might also want to look at tightening up their service schedules too. Cooling, in particular, is very important for a Tier 4 Interim engine, as there is greater heat produced by EGR and the various after-treatment systems. This means that the latest machinery will have larger cooling packs and it will be important to keep these clean and free of dust for the most efficient use.
The bad news is that Tier4 Interim machines will be more expensive to buy – all that after-treatment does not come cheap. But the good news is that operators can expect 5–10% better fuel consumption and improvements in power and productivity.
For those thinking of holding off changing equipment for a year or two until things settle down, it will all happen again in 2014, as Tier 4 Final regulations come into effect. Of course, with cleaner air conditions for everyone it is hard to complain, but fleet managers will want to take fuel and possibly AdBlue, maintenance and daily checks into account when looking at new machinery.