Visible Felt Leadership
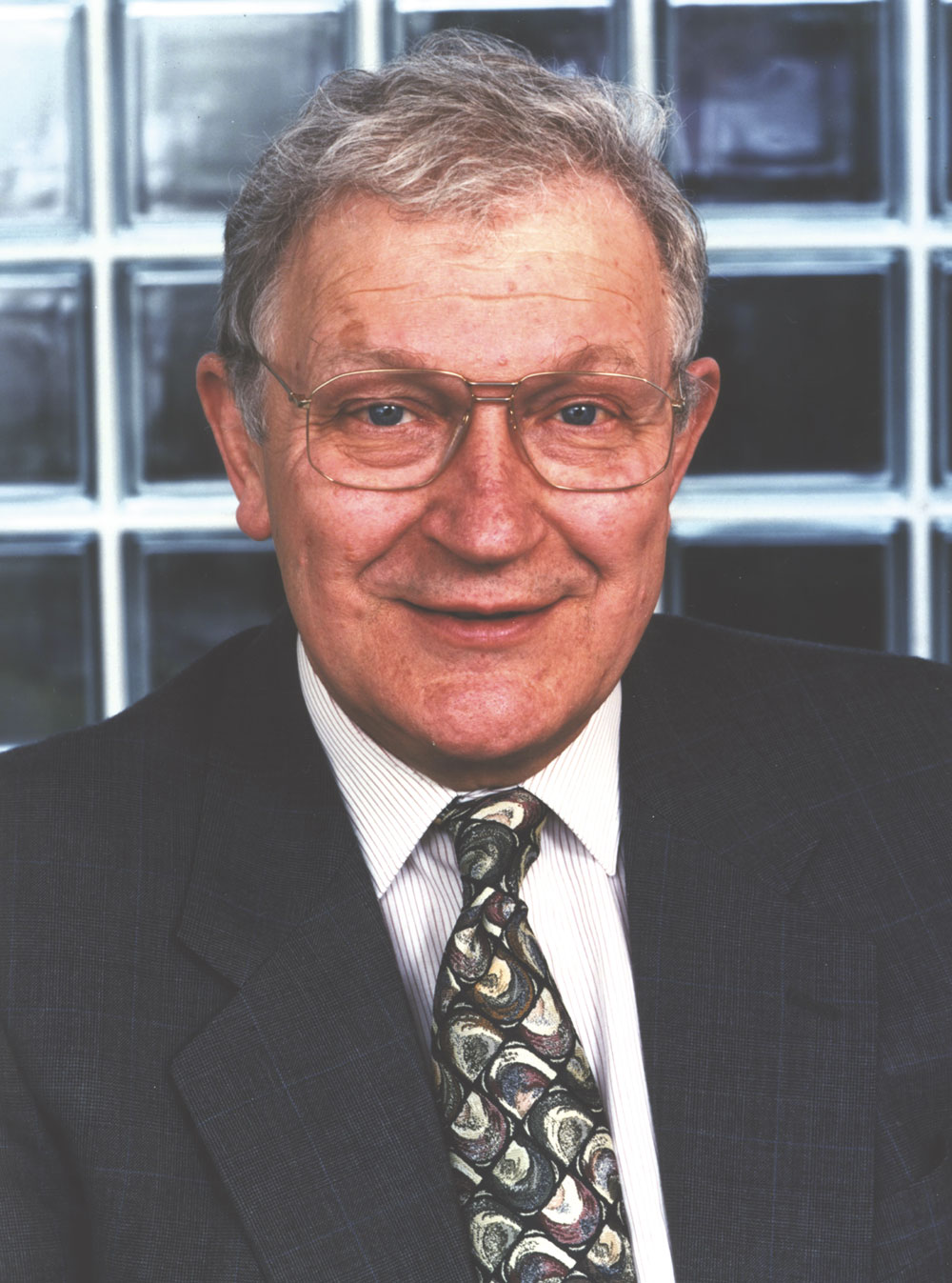
Some thoughts on the importance of leadership in the management of safety in the quarrying industry
By Prof. Peter McKie CBE
In this article, Peter McKie, former chief executive officer of DuPont UK, summarizes the key points of his McPherson Lecture presentation at The Institute of Quarrying’s 2004 annual conference symposium on the theme ‘Developing a Culture of Health & Safety’
The quarrying industry has made a significant improvement in the management of safety in recent years. The achievement of the ‘hard target’ goal of a 50% reduction of injuries in five years is commendable, but the question now is how will we continue this improvement in the future, and can we achieve a safety performance whereby a lost-time injury is a very rare event?
It is my belief that the industry can do so provided that it pays attention to the basics of good safety management. Areas that need constant attention include visible felt leadership, managing safety through the line managers, with the safety professionals playing a supportive role, and having a clear vision for the future state of the industry with the necessary policies to deliver this vision by achieving consistently high standards. In addition, it will be necessary to ensure that communications flow freely up and down throughout the organization and to make frequent training (and retraining) a key part of everyone’s job. Also, everyone in the industry must accept that they are responsible for the tasks they carry out and they must be held accountable for how they discharge this responsibility. Eventually in this chain of responsibility and accountability the industry is itself accountable to society for its safety performance. It is no secret that society is becoming ever more demanding in this respect and ultimately, of course, this is a good thing.
Out of all of these processes the most important is clearly that of visible felt leadership. Managers and supervisors demonstrate clear visible leadership by spending significant time in the field, observing work taking place and discussing their safety observations directly with the workforce. Where work is being carried out to their standards they must take the time to recognize this with their employees and give positive feedback. Where work is being carried out in an unsafe manner then they must stop the work immediately and ensure the behaviour is corrected. In this way the whole organization will be sent a clear message that unsafe acts will not be tolerated and everyone will see that the leadership of the company is dedicated to working safely. It is vitally important that these unsafe acts are eliminated, as studies show that the vast majority of injuries result from them.
The safety performance will benefit from management analysing the types of unsafe acts they observe, and by ensuring these acts are corrected at the source. In this way, and only in this way, can injuries be prevented from occurring. If this process is carried out effectively then injuries will indeed become rare events.
The question arises however, how can management ensure that a satisfactory safety culture is developed within the organization and how is this culture made self-sustaining and directed towards achieving superior performance?
The answer has to lie in developing the knowledge of each individual regarding the safety procedures and objectives and making sure that each employee clearly understands his or her role in achieving these objectives. Employees then need guidance and support as they develop the skills necessary to perform their role. These skills are much wider than just the technical ability to execute their work. They must be helped to understand the reasons why tasks are important and why these tasks must be executed properly each and every time. In this way employees will be encouraged to work independently without direct supervision, but always within the boundaries of the rules and procedures. A further development of the culture lies in establishing self-directing teams. In this mode of working all the members of the team unite around the common task and support one another in its execution. Each team member looks after his or her own performance and also takes a role in assisting the rest of the team monitor and improve their safety behaviour. In this mode of operation team members will be constantly on the lookout for unsafe acts anywhere within the team and they will be corrected immediately.
These team processes have been shown to be the most effective route to good, safe operation. Management must ensure that they support the team processes by providing space for the team to address their own issues and by resourcing the team as required.
With these thoughts in mind, and based on my recent exposure to the quarrying industry, I offer my thoughts on safety throughout the industry. Of course there is considerable variation from company to company but this is my view of the overall position.
I believe progress is being made and the performance trends support this. The target of 50% improvement over the last five years has been achieved and I am certain that the industry is not content with this level of improvement. A healthy dissatisfaction with the current performance exists and there is a clear, determined effort to make further improvements.
However, I do have some areas of concern. I am not convinced that everyone in the industry, or perhaps even a majority, believes that it is possible to work without serious injuries occurring. There is a fairly widely held belief that quarrying is a dangerous industry and a certain level of injuries is inevitable. Unless we can change this belief then it will become a self-fulfilling philosophy. Close to zero injury performance is being achieved in several parts of the industry so we must work to spread this performance industry-wide.
The industry is largely production orientated and production bonuses are relatively common. I wonder if this reinforces the belief that production is more important than safety? Allied to this concentration on production is a long hours/overtime culture. This may result in fatigue that in turn could add to the safety issues.
There is also a fairly widespread belief that there is an engineering solution to most safety problems with managers striving to make the workplace hazard free. While this is an admirable goal, it is impossible to achieve. It must be recognized that the workplace is never risk free and people must be constantly on their guard to minimize and manage risk. A more determined application of the risk-assessment process would help in this regard. It is essential, for example, that the risk assessment for a job is developed with the people charged with carrying out the work and that they have a full understanding of its content. All too often the risk assessment is seen as a piece of documentation to be held on file rather than a key part of the job line-up.
I also believe that there is a somewhat macho culture within the quarrying industry that leads to people over-stressing themselves. When this is combined with what is in
general an ageing workforce then there is a possibility for musculoskeletal injuries and other long-latency occupational illnesses to occur.
In summary, I believe the industry should first convince itself that all serious injuries could be avoided. Much more time needs to be spent in addressing the question of unsafe acts and the behaviour leading to these unsafe acts should be analysed and corrected at source. Leaders should spend considerable time in the field ensuring that they are connected with the workforce and are aware of how work is being executed. They should set high standards for how work is carried out and must emphasize that no work should be carried out which is considered to be unsafe.
I also believe that further work is necessary to address the question of occupational illness. It would be useful, for example, to more clearly record and track the performance in this area.
I am sure that the industry will indeed continue to make progress in the area of health and safety management and I look forward to the day when the quarrying industry leads the way in industrial safety performance.