Safety First
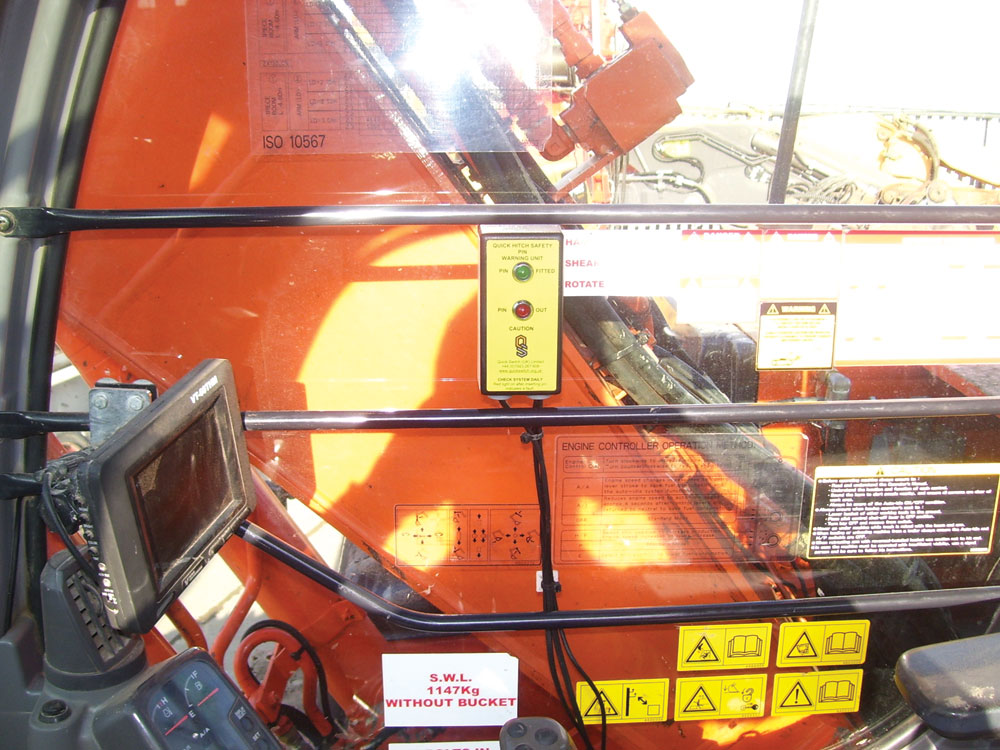
Hertfordshire-based Quick Switch (UK) Ltd have unveiled a new quick-hitch safety-pin warning device that could save the lives of operators working around excavators fitted with semi-automatic quick hitches
Following a spate of accidents and four fatal incidents between December 2006 and November 2007, all of which involved semi-automatic quick hitches, the Health and Safety Executive called for European mobile manufacturers to cease production and supply of semi-automatic hitches on new machinery from 1 October 2008.
The ‘ban’, however, is not retrospective, leaving tens of thousands of quick couplers still in active use on UK construction, demolition and quarry sites. So, why has the HSE not banned all semi-automatic quick-hitch mechanisms on existing machinery?
‘Because they are mechanically safe, provided they are used correctly,’ explained Howard Button, chief executive of the National Federation of Demolition Contractor (NFDC). ‘The semi-automatic hitch is not the problem; it’s down to operator misuse.’
Indeed, according to HSE statistics, ‘approximately 13% of all accidents investigated on excavators are attributed to the bucket detaching from a quick- hitch and injuring a ground worker…However, there may be many more dangerous occurrences that occur when a bucket detaches unintentionally from the hitch, but without injury because no one is underneath at the time. This means that quick hitch failures are relatively common, although injuries are less so.’
Despite this major finding, the HSE identifies semi-automatic quick hitches as the common cause for buckets and attachments becoming unexpectedly detached from mobile equipment. Instead, it approves the use of manual and automatic quick-hitches, but not everyone in the industry is convinced.
There remains a similar concern over some of the more advanced automatic hitches as mud, rubble and other contaminants can block the locking latches, making them potentially as unsafe as their semi-automatic cousins. There is also the issue of automatic hitches discouraging operators from interacting with their machines, as this instils a culture of ‘staying in the cab’, which could lead to potential safety hazards.
In short, automatics have their own drawbacks, and the debate on which type of quick-hitch is safer will continue across the plant and minerals industries.
For the tens of thousands of semi-automatic systems still in operation in the UK, Quick Switch (UK) founder (and inventor) Tony Bianchi has developed a simple yet effective solution to ensure that semi-automatics can be used safely.
The Quick Switch system is a safety-pin detection device that works by having a sensor positioned by the safety pin aperture of the semi-automatic hitch. This, in turn, detects the presence or absence of the required retaining pin.
The sensor is linked to a warning device in the driver cab, which sets off an audible alarm and displays an ultra bright flashing red LED if the operator attempts to use the machine without the correct pin in place. When and while the safety pin is in place, the driver will see a simple green LED indicator.
‘Because the sensor has quite a specific sensing range, we have used this to our advantage by installing the bracket and sensor in such a way that the correct-sized pin has to be used,’ explained Mr Bianchi. ‘An undersized, inappropriate or temporary pin will not be detected or will only be detected intermittently, thereby activating the alarm.’
Mr Bianchi also said his system acts as a mini metal detector and, therefore, is not tricked by mud, other contaminants, or by the insertion of lengths of reinforcing steel bars, aluminium or other ‘make-do’ measures on site.
Developed over the last two years with approximately 12,000 live test hours under its belt, the Quick Switch system is much more than merely a ‘knee-jerk’ reaction to the current furore over the use of semi-automatic quick- hitches. It meets the requirements of the Supply of Machinery (Safety) Regulations 1992 and is manufactured with an Environmental Protective rating of IP69K.
‘The system has been designed for optimum shock and vibration resistance, and with an extended temperature range of –40°C to 85°C, it can operate in either Antarctic or Saharan conditions,’ said Mr Bianchi. ‘The system has a lot more to it than meets the eye and we have had to meet very stringent standards and regulations…It has taken a lot of time and money to ensure that we have got it right.’
Although the Quick Switch system has been designed specifically to address an operator’s failure to engage the retaining pin, the 12,000-plus hours of site testing has led to additional and unforeseen benefits. For example, using the product could create a strong motivation to ensure that the safety pin does not go missing.
‘There should be no more lost pins with this system,’ explained Mr Bianchi. ‘Because of the nature of the warning, the pin should rarely, if ever, get lost. The operator tends to remember where the safety pin is if he is the one who has to listen to the siren because he has tracked it into the mud.’
A further benefit is that the Quick Switch unit can act as a plant theft deterrent against opportunist thieves. ‘Removing the pin at night can be beneficial as an anti-theft alarm,’ said Mr Bianchi. ‘An opportunist attempt at robbery or kids trying to drive a machine for fun will result in the external siren going off unexpectedly.’
Ultimately, however, the Quick Switch system should be seen as a safety-warning device for semi-automatic quick-hitches. As HSE statistics have shown, some operators are failing to manually insert the retaining pin, causing buckets and attachments to become disconnected from their machines, and Quick Switch (UK) have designed a solution that addresses this growing danger on construction and quarry sites.
Quick Switch (UK) Ltd, PO Box 566, Abbots Langley, Herts WD5 5AX; tel: (01923) 267608.