Protecting Personnel
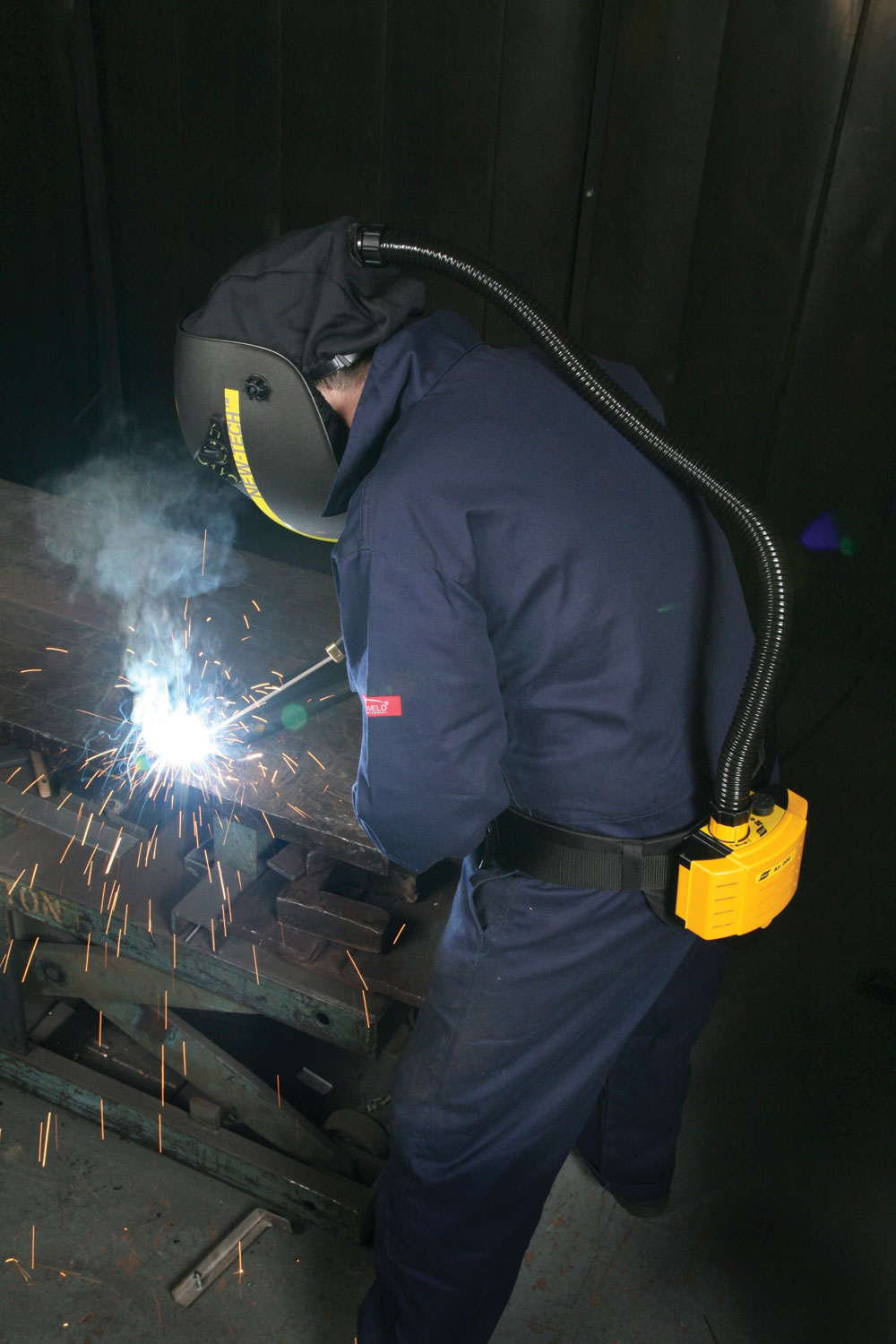
Mark Homan, global PPE/welding accessories business manager at ESAB, points out what quarry managers need to know
Businesses have both legal and moral obligations to safeguard their workers and one of the first steps required to ensure health and safety in the workplace is a risk assessment. Where such a process identifies that unacceptable risks are present, the hazards (defined as things that have the potential to cause harm) should be designed-out and, if this is not possible, control measures put in place to reduce the probability of an accident occurring and/or the severity of the consequences.
Industries such as quarrying, asphalt and concrete production, and recycling are inherently hazardous and there are some hazards that cannot be designed out, such as dust, noise and vehicle movements. Furthermore, measures such as physical guarding cannot be used against all hazards present. These industries are, therefore, more reliant than many others on personal protective equipment (PPE).
A suitable and sufficient risk assessment will be necessary to establish where PPE is necessary and the nature of the equipment required. For example, eye protection must be of the correct type to protect against the hazards present, as must helmets, footwear, gloves, hearing protection and other types of PPE.
The different types of protection are detailed in relevant national and international standards, so the manager responsible for health and safety needs to ensure that the correct standard is referenced and the right type or grade of PPE is issued in relation to the hazards present.
However, specifying PPE is only half the battle. Safety glasses offer no protection if they are in the pocket of the person who is supposed to be wearing them; similarly, ear plugs do not attenuate noise sufficiently if they are worn incorrectly. In the UK and many other industrialized nations, companies have a legal duty to provide PPE and workers are legally obliged to use their PPE.
Traditionally, the route to enforcement has been prescriptive rules and procedures, usually supplemented by signage, but these measures are only effective if workers appreciate fully the risks involved and believe that they will be caught and disciplined if they do not use their PPE. For many people, working for several years without suffering an injury – despite not using appropriate PPE – makes them complacent; they therefore tend to think that an accident will never happen to them.
An alternative strategy for managing compliance is to change the workers’ perception of risk so that they think it is highly likely that they will suffer an injury if they are not using their PPE, and to change the mindset of all workers so that the use of PPE is effectively policed by co-workers, rather than managers. In these circumstances, workers feel that they will be corrected by their peers if they do not use PPE correctly, which acts as a strong incentive. This approach can also have a significant impact on health and safety in general, not just in relation to PPE compliance.
Most companies like to display on health and safety notice boards the improvements they have achieved over a period of time with respect to accidents in the workplace. This mindset of workers working together with the employers to improve these statistics is beneficial to all concerned.
As with any other product, purchasers of PPE are usually faced with a choice of similar products at a range of different prices. It is often true that the more it costs the better product, but paying a higher price for one item of PPE rather than a lower-cost alternative can be hard to justify. However, there are some factors that should be considered. For example, if one particular pair of ear defenders is more comfortable than another, there is a higher probability that they will always be worn when required. The same applies to helmets, eye protection, gloves and other protective clothing.
Auto-darkening welding helmets are very popular today, but few people realize that some of the low-cost products on the market do not perform as well as might be expected. Manufacturers quote a switching time for the auto-darkening function, but seldom state at what ambient temperature the switching time is measured. Because of the way auto-darkening filters function, the switching is faster at higher temperatures.
So a manufacturer quoting a switching time of, for instance, 0.0001s may not state that this is at 55°C, which is higher than the temperature at which most welders will be working. These low-cost products probably still meet the requirement of the EN 379 standard, but a welder working all day producing tack or spot welds will notice the difference due to the small amount of additional light that is allowed through the filter by the slower-than-expected switching time.
Furthermore, for products with a bright state 3, the amount of light reaching the eyes actually increases by an additional factor of 2.7. Employers should remember that tired eyes and worker discomfort can lead to reduced productivity and more mistakes, which will ultimately cost a great deal more than a higher-quality welding helmet.
The same argument about discomfort also applies to the weight and balance of the welding helmet. Heavy helmets and off-balance headgear can lead to neck strain, discomfort and headaches, resulting in lower productivity, more mistakes and a greater need for rework. Just 5min a day of lost production due to worker discomfort adds up to 19h over a year. At a cost of £11 per hour, this equates to a loss of £209 per year per operative, simply because the headgear is uncomfortable.
It can be seen, therefore, that paying a little more for PPE can often benefit the quality of the work performed, as well as workers’ productivity. Together, these two factors can easily outweigh the additional cost associated with purchasing better-quality PPE.
It is also worth remembering that the cost of PPE will always be lower than the costs associated with an accident. Following an accident, uninsured losses might include lost production, the cost of organizing an investigation, the cost of court appearances, fines, payments to the injured worker and the costs associated with adverse publicity.
Assuming that the right PPE has been purchased and workers are using it correctly, the next important step to take is to ensure that it is inspected and maintained correctly. Worn or damaged PPE will not function adequately, especially at critical moments. Managers, therefore, need to implement a PPE maintenance programme so that the equipment is inspected and maintained at appropriate intervals, and in the event of any damage or wear becoming apparent to the user.
During the last half century there have been significant improvements in workplace health and safety, which is evident from falling statistics for injuries, ill-health and, most importantly, fatalities. PPE has played an important role in achieving these results, but its selection and use requires continuous vigilance in order to keep abreast of the latest technological developments, current regulations and standards, and to ensure that worker complacency does not lead to non-compliance.
ESAB has a wealth of experience in PPE and a broad range of products suitable for use by workers involved in welding, cutting and other operations. For further information tel: (0800) 389 3152; email: info@esab.co.uk