Plant Makers Face Up To Industry Challenge
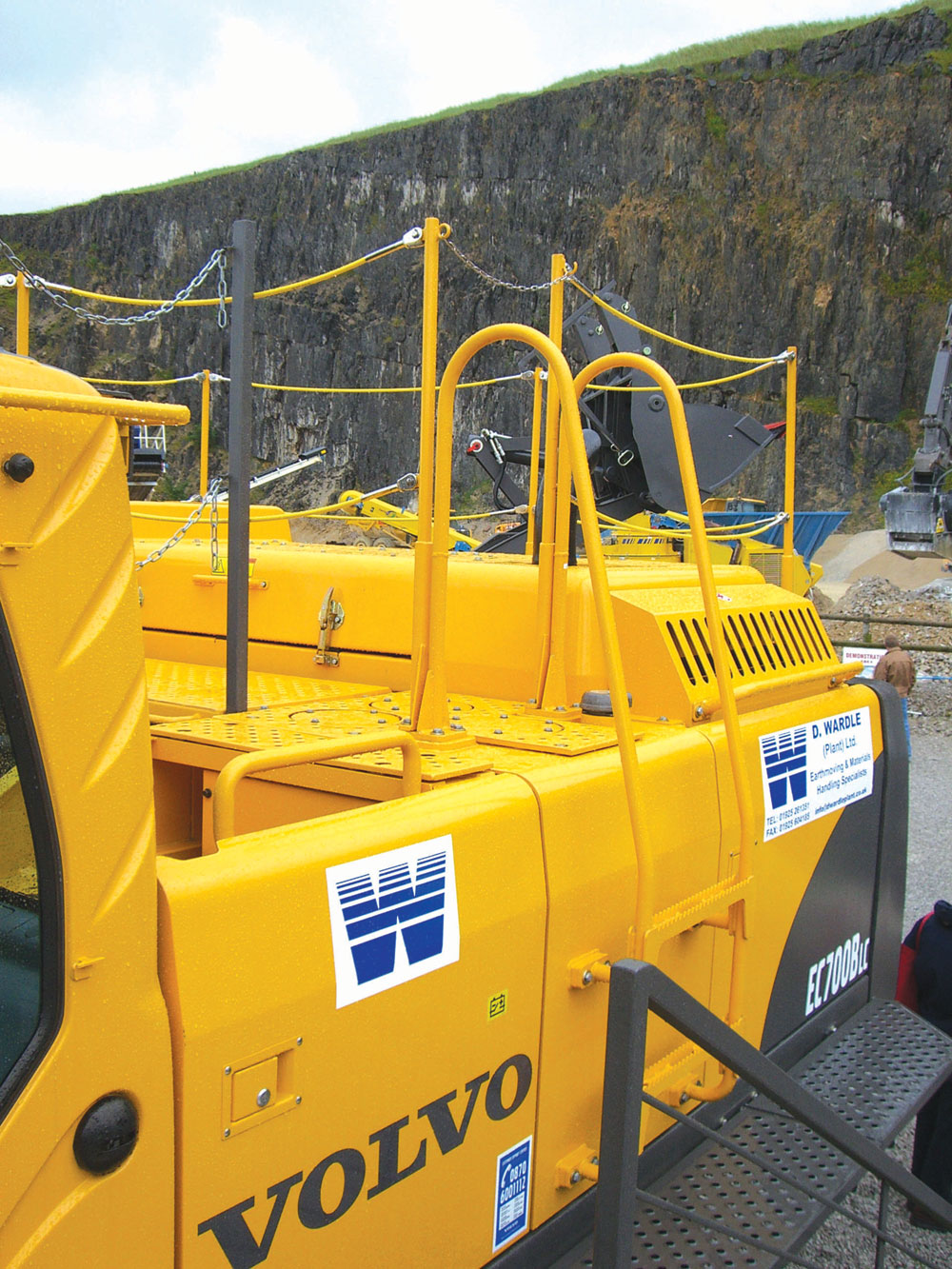
Supplying plant that is inherently safe – as standard
By Martin Isles, chairman of the UEPG Health and Safety Committee, Brussels, and director of health and safety with the QPA
Widespread attention is being focused on the Quarry Products Association’s list of ‘25 Commandments’ (see below), the UK nucleus of a growing international campaign to improve plant health and safety standards. Why? Because the European quarrying and quarry products industry is on an irreversible crusade towards eliminating workplace accidents and occupational ill-health. To achieve this, an essential part of the solution requires mobile plant design to be inherently safe, as standard.
Global manufacturers and suppliers of mobile plant are urged, most strongly, not only to listen to, but to address the needs of their customers. The quiet evolution of international standards, though moving at a significantly slower pace, is seen as an indispensable foundation towards achieving this goal. In this age of transparent communications, manufacturers who are perceived as blocking or frustrating the positive development of such standards will not endear themselves to their increasingly global customers. Inadequate design of mobile plant is now being recognized in multinational head offices in France, Germany, Mexico, Switzerland, as well as in America, the UK and elsewhere.
While in the past, in some quarters, there was begrudging tolerance of poor- quality health and safety machine design solutions, the tables are now well and truly turning. Strengthening resolve towards industry-wide ‘Zero Injury’ initiatives are causing users to flex their corporate procurement muscles ever more strongly. No element of the supply chain can, or will, escape this scrutiny. Thus, global manufacturers are being called to task to provide world-class solutions to designs for health and safety.
Positive indications
The good news is that the ‘green shoots’ of positive progress are now beginning to appear. Informed commentators have ascribed the credit for this new-found impetus to the ‘quarriers’ and their health and safety regulators having teamed up internationally – most notably with the USA and Germany – via the ‘Atlantic Alliance’, with the active support of the countries comprising UEPG, the European Aggregates Association.
‘Real world’ problems – overdue solutions
The clear message, though, from the users, regulators and insurers, is that many current designs still fall woefully short of health and safety expectations.
A recent survey by Hanson Aggregates UK, part of the international Heidelberg Cement Group, revealed the finite nature yet widespread scope of the current challenge facing the manufacturers. The survey also shows the extent of ingenuity by the user company’s employees in overcoming many of the problems – at the user’s cost, and in reaction to actual incidents – all of which may have been avoided if the original machine design had been adequate in the first place.
In 2006–07, statistics from the Health and Safety Executive (HSE) showed that in Great Britain, a staggering 34% of all reported incidents were ‘slips, trips, and falls’, including, importantly, ‘falls from height’. So, what are the related challenges specifically facing the plant makers?
The following are examples of direct quotations from the survey referred to above, which covered 216 discrete items of mobile plant and recorded a cumulative total of 545 hazards. Worryingly, 73 of these hazards were recorded against machines that were no more than two years old. Typical entries include:
Excavators
It is interesting to note that this survey was carried out, and contributed to, by operational personnel, not by health and safety specialists. So the results focus on those issues that were directly apparent to machine operators and maintenance fitters – the front-line personnel and the very people that are confronted by these avoidable risks, many on a daily basis (see below).
So, who are the offending machine manufacturers? The list is so long, it is a struggle to think who was left out!
Your operators and maintenance crews deserve better!
[img_assist|nid=14461|title=Access 2|desc=|link=none|align=left|width=266|height=200]UEPG advises each of its national member associations, not least the QPA, to encourage all their member companies to look carefully into such matters and, importantly, to involve the relevant workforce personnel. The benefits to those operatives and maintenance workers that arise by eliminating the risks associated with working at height, in particular, will become immediately apparent. Such actions are those of socially responsible users, not ‘awkward customers’.
To reach the goal of zero injuries must be an expectation – not merely an aspiration – of every company in the business of aggregates quarrying and quarry products. There must be a unified acceptance and determination from president to procurement manager, from dumptruck driver to director that health and safety will be regarded as the number one core value.
Quarry operating companies employ many resourceful and innovative people, but the industry should not have to rely on its own people to apply remedies. There is no excuse for perpetuating known hazards in the face of known solutions. In short, there is no substitute for safe design.
Partnerships for a safer future
Plant manufacturers and plant users who work in partnership, with shared goals and shared understanding, can achieve the required solutions, thereby helping to make this industry safer and more sustainable as a result.
At its international conference in September 2008, the ‘Atlantic Alliance’ extended its focus, in similar vein, to fixed and mobile process plant manufacturers, suppliers and turnkey contractors, to ensure that safety is to the fore in designing for the operators, inspection personnel and maintenance crews.
Partnership is the key to progress on all these fronts, and the QPA will be announcing several initiatives in this regard in the coming months.
The QPA’s ‘25 Commandments’
As a result of protracted consultation with a wide range of stakeholders, the QPA has endorsed the following list as being a fundamental part of the users’ requirements for standard fitment to new and re-engineered items of mobile ‘loose’ on-site plant and transport supplied for use in the UK:
Is it right that, today, workers should have to stand on unguarded counterweights to top up radiators? Why should the user have to provide platforms or telehandlers to access radiators safely?
It surely is not hard to realize that if a mudguard is integrated with an engine inspection cover, then with mud build-up, it will become much heavier to lift, especially with flimsy gas struts that deteriorate with age. Did the designers think beyond a clean new machine?
Refilling autolube reservoirs is one of the biggest maintenance issues. A simple ‘site fix’ has been to extend the filler hose so that it can be accessed at ground level. Why couldn’t the machine designers have thought of ground-level solutions?
Re-fuelling usually requires access by platform or by hanging off the steps. Why can’t all manufacturers provide fuel fillers accessible from the ground?
Cleaning windscreens can be a risky business due to sloping shiny surfaces and precarious footplates. Of course, they can be cleaned from the ground with long-handled brushes, but it is pleasing to see that many machines now provide cab-top perimeter rails. Why don’t all machines have windscreen rails and platforms? If your prospective new machine does not have this facility, chose one that does.
One of the archetypal designs flaws, still ignored by virtually every manufacturer, are those jagged pieces of metal on the roller carrier frames of any tracked machine, each euphemistically called a ‘step’. Plant makers need to realize that this 1950s style of access up and over the tracks is simply no longer acceptable. If small Australian engineering companies can solve it, then so can the major machine manufacturers.
It is reasonable to expect a site’s plant yard to be well lit, but for the excavator working at the face of a rock quarry or at a distant sand and gravel excavation, this is rarely the case. If your operators are arriving at their face machines in the dark, can they switch on the lights before accessing the cab of the machine? If not, why not? New face machines, in particular, should be rejected if they do not come fitted with a remotely operable lighting system, as standard.
Recurring damage to mobile plant, eg to access steps, must not be considered inevitable. Instead, the root causes should be identified and suitable action taken. Clearly there may be other contributory factors. However, the chances are that some aspect of inadequate machine design is at the core of the problem.
By Martin Isles, chairman of the UEPG Health and Safety Committee, Brussels, and director of health and safety with the QPA
Widespread attention is being focused on the Quarry Products Association’s list of ‘25 Commandments’ (see below), the UK nucleus of a growing international campaign to improve plant health and safety standards. Why? Because the European quarrying and quarry products industry is on an irreversible crusade towards eliminating workplace accidents and occupational ill-health. To achieve this, an essential part of the solution requires mobile plant design to be inherently safe, as standard.
Global manufacturers and suppliers of mobile plant are urged, most strongly, not only to listen to, but to address the needs of their customers. The quiet evolution of international standards, though moving at a significantly slower pace, is seen as an indispensable foundation towards achieving this goal. In this age of transparent communications, manufacturers who are perceived as blocking or frustrating the positive development of such standards will not endear themselves to their increasingly global customers. Inadequate design of mobile plant is now being recognized in multinational head offices in France, Germany, Mexico, Switzerland, as well as in America, the UK and elsewhere.
While in the past, in some quarters, there was begrudging tolerance of poor- quality health and safety machine design solutions, the tables are now well and truly turning. Strengthening resolve towards industry-wide ‘Zero Injury’ initiatives are causing users to flex their corporate procurement muscles ever more strongly. No element of the supply chain can, or will, escape this scrutiny. Thus, global manufacturers are being called to task to provide world-class solutions to designs for health and safety.
Positive indications
The good news is that the ‘green shoots’ of positive progress are now beginning to appear. Informed commentators have ascribed the credit for this new-found impetus to the ‘quarriers’ and their health and safety regulators having teamed up internationally – most notably with the USA and Germany – via the ‘Atlantic Alliance’, with the active support of the countries comprising UEPG, the European Aggregates Association.
‘Real world’ problems – overdue solutions
The clear message, though, from the users, regulators and insurers, is that many current designs still fall woefully short of health and safety expectations.
A recent survey by Hanson Aggregates UK, part of the international Heidelberg Cement Group, revealed the finite nature yet widespread scope of the current challenge facing the manufacturers. The survey also shows the extent of ingenuity by the user company’s employees in overcoming many of the problems – at the user’s cost, and in reaction to actual incidents – all of which may have been avoided if the original machine design had been adequate in the first place.
In 2006–07, statistics from the Health and Safety Executive (HSE) showed that in Great Britain, a staggering 34% of all reported incidents were ‘slips, trips, and falls’, including, importantly, ‘falls from height’. So, what are the related challenges specifically facing the plant makers?
The following are examples of direct quotations from the survey referred to above, which covered 216 discrete items of mobile plant and recorded a cumulative total of 545 hazards. Worryingly, 73 of these hazards were recorded against machines that were no more than two years old. Typical entries include:
Excavators
- poor lighting of steps and approach area
- little or no fall-prevention measures on walkways to the engine
- poor access – tracks being used as part of the access
- steps on roller carrier frames regularly damaged (rock quarry face applications)
- steps on roller carrier frames constantly buried in mud (sand and gravel quarries).
- poor access for cleaning windows
- poorly designed, damaged or even missing access
- poor access and little fall protection when refilling the autolube
- inadequate access to fill radiators, change light bulbs etc
- wheel arch integrated with engine inspection cover – difficult to lift
- to open cab door requires operator to lean away while on access steps.
- nothing to stop operator falling off dumper while raising the bonnet
- too great a reach to the first step
- headlight shroud seen as a potential trip hazard
- no rails behind operator when dipping or filling up the oils
- cab doors and mirror arms blocking or making access difficult.
It is interesting to note that this survey was carried out, and contributed to, by operational personnel, not by health and safety specialists. So the results focus on those issues that were directly apparent to machine operators and maintenance fitters – the front-line personnel and the very people that are confronted by these avoidable risks, many on a daily basis (see below).
So, who are the offending machine manufacturers? The list is so long, it is a struggle to think who was left out!
Your operators and maintenance crews deserve better!
[img_assist|nid=14461|title=Access 2|desc=|link=none|align=left|width=266|height=200]UEPG advises each of its national member associations, not least the QPA, to encourage all their member companies to look carefully into such matters and, importantly, to involve the relevant workforce personnel. The benefits to those operatives and maintenance workers that arise by eliminating the risks associated with working at height, in particular, will become immediately apparent. Such actions are those of socially responsible users, not ‘awkward customers’.
To reach the goal of zero injuries must be an expectation – not merely an aspiration – of every company in the business of aggregates quarrying and quarry products. There must be a unified acceptance and determination from president to procurement manager, from dumptruck driver to director that health and safety will be regarded as the number one core value.
Quarry operating companies employ many resourceful and innovative people, but the industry should not have to rely on its own people to apply remedies. There is no excuse for perpetuating known hazards in the face of known solutions. In short, there is no substitute for safe design.
Partnerships for a safer future
Plant manufacturers and plant users who work in partnership, with shared goals and shared understanding, can achieve the required solutions, thereby helping to make this industry safer and more sustainable as a result.
At its international conference in September 2008, the ‘Atlantic Alliance’ extended its focus, in similar vein, to fixed and mobile process plant manufacturers, suppliers and turnkey contractors, to ensure that safety is to the fore in designing for the operators, inspection personnel and maintenance crews.
Partnership is the key to progress on all these fronts, and the QPA will be announcing several initiatives in this regard in the coming months.
The QPA’s ‘25 Commandments’
As a result of protracted consultation with a wide range of stakeholders, the QPA has endorsed the following list as being a fundamental part of the users’ requirements for standard fitment to new and re-engineered items of mobile ‘loose’ on-site plant and transport supplied for use in the UK:
- Colour rear-view camera
- Additional convex mirrors
- Front view mirror
- Amber flashing rotating beacon
- Broadband ‘white noise’ reversing alarm
- Radar reversing aid
- Front radiator handrail
- Cab access handrails and walkway
- Seat belt warning device (visual/audible)
- Skip up warning device (audible) (dumptrucks)
- Strobe reverse lights
- Autolube system
- Smart retractable inclined stairway access
- Ground-level lockable isolation switch
- Ground-operated work/access lights
- Ground-level grouped service access
- Ground-level refuelling station
- Practical second egress from cab
- Air-conditioning
- Front-screen cleaning access
- Non-slip access surfaces
- Red and white safety chevrons on counterweight (excavators, loaders, graders)
- Handrails around upper body (excavators)
- Extended walkways and handrails (excavators)
- Manual fire extinguisher in cab
Is it right that, today, workers should have to stand on unguarded counterweights to top up radiators? Why should the user have to provide platforms or telehandlers to access radiators safely?
It surely is not hard to realize that if a mudguard is integrated with an engine inspection cover, then with mud build-up, it will become much heavier to lift, especially with flimsy gas struts that deteriorate with age. Did the designers think beyond a clean new machine?
Refilling autolube reservoirs is one of the biggest maintenance issues. A simple ‘site fix’ has been to extend the filler hose so that it can be accessed at ground level. Why couldn’t the machine designers have thought of ground-level solutions?
Re-fuelling usually requires access by platform or by hanging off the steps. Why can’t all manufacturers provide fuel fillers accessible from the ground?
Cleaning windscreens can be a risky business due to sloping shiny surfaces and precarious footplates. Of course, they can be cleaned from the ground with long-handled brushes, but it is pleasing to see that many machines now provide cab-top perimeter rails. Why don’t all machines have windscreen rails and platforms? If your prospective new machine does not have this facility, chose one that does.
One of the archetypal designs flaws, still ignored by virtually every manufacturer, are those jagged pieces of metal on the roller carrier frames of any tracked machine, each euphemistically called a ‘step’. Plant makers need to realize that this 1950s style of access up and over the tracks is simply no longer acceptable. If small Australian engineering companies can solve it, then so can the major machine manufacturers.
It is reasonable to expect a site’s plant yard to be well lit, but for the excavator working at the face of a rock quarry or at a distant sand and gravel excavation, this is rarely the case. If your operators are arriving at their face machines in the dark, can they switch on the lights before accessing the cab of the machine? If not, why not? New face machines, in particular, should be rejected if they do not come fitted with a remotely operable lighting system, as standard.
Recurring damage to mobile plant, eg to access steps, must not be considered inevitable. Instead, the root causes should be identified and suitable action taken. Clearly there may be other contributory factors. However, the chances are that some aspect of inadequate machine design is at the core of the problem.