Don’t Fall For Bad Access
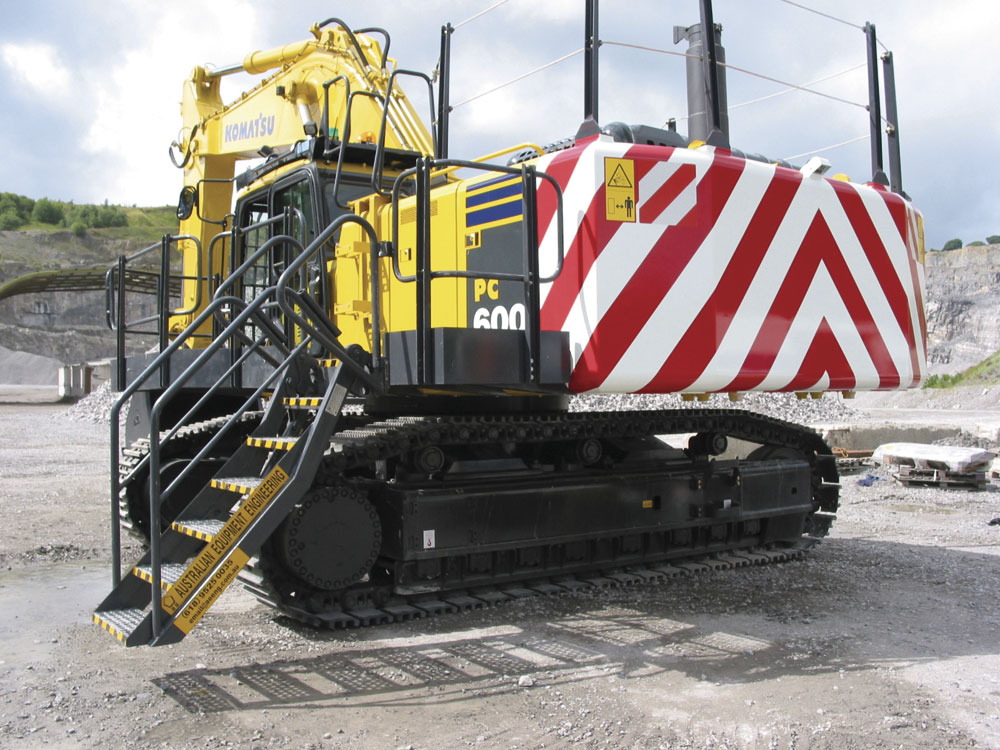
Managing the risk of falls from vehicles
By Helen Turner, Health and Safety Executive
Historically, mobile plant and other vehicles have been the main source of accidents in the quarrying industry. The large number of movements on site each day, coupled with the nature of mobile plant and its working environment, meant that around half of all fatal accidents in quarries prior to 1997 were vehicle related.
During the 1990s quarry operators, with the HSE’s active support, were at the forefront in trialling different types of aids to driver vision, with the aim of reducing or eliminating blind spots. It rapidly became the industry norm to fit convex mirrors and rear CCTV to mobile plant. This improves driver safety by making visible edge protection, tipping points, obstructions and ditches, and improves the safety of those outside the vehicle by allowing the driver to see smaller vehicles or pedestrians nearby. Additional reversing aids, such as radar, are also specified as standard by some quarry operators, or fitted where risk assessment identifies them as necessary.
This action by the industry has had a fundamental effect on improving safety. Under the successful Hard Target initiative for reducing reportable quarry accidents by 50% between 2000 and 2005, continuing efforts to end ‘struck by vehicle’ accidents have continued, with a reduction of 63% over five years.
The industry’s attention is now turning to another aspect of mobile plant that causes significant injuries and lost time – that of falls from vehicles. Some operators have attributed up to a quarter of all the accidents in their quarries to climbing on or off mobile plant, either for driving or maintenance purposes.
The quarrying industry is already acting on this issue. In the same way that visibility equipment was trialled in the 1990s, during the last few years many quarry operators have been trialling, making and purchasing additional equipment to improve access and egress for drivers of mobile plant. Measures to reduce falls risks include (1):
- Avoiding the need for climbing on to vehicles where possible.
- Providing steps and handholds where access is still required.
- Looking for safety features when buying a new vehicle.
- Trying out different types of footwear to see which provides the most slip-resistance for the environment employees will be working in.
- Explaining the dangers to workers of walking on a trailer.
- Explaining to workers that they should never have their back to an edge of a trailer if they are within 1m of it.
- Ensuring workers understand the risks of jumping down from any part of a vehicle so that it becomes unacceptable practice.
- Regularly checking the condition of handholds, guard rails etc to detect deterioration in load-bearing capacity.
In late 2006 the Quarries National Joint Advisory Committee (QNJAC) formally endorsed the work of its working group on mobile plant (2). The group reported on the safety features of mobile plant that quarry operators wish to see, and which they are aspiring to make the norm. This included aspects relating to safe access, such as:
- stairways or inclined ladders rather than vertical ladders
- bottom steps with very limited or no movement
- a landing platform with handrails
- non-slip surfaces
- good grip on the leading edge of steps
- lighting switched on/off from ground level, where appropriate
- routine/daily maintenance carried out from ground level, where possible.
Manufacturers are working together to develop an improved international standard on access systems which will result in reduced risks with earthmoving machines. In the meantime, some manufacturers are improving their machines in line with the draft standard, and the results were evident on a number of machines on display at the recent Hillhead exhibition.
At the same time as addressing safe access on their own plant, operators are also recognizing the need to assist hauliers to comply with their health and safety obligations, with regard to the safety of drivers when receiving and managing loads on quarry sites. Improving the interface between quarry operators and contractors, including hauliers, is one of the priorities identified by the QNJAC. A subcommittee chaired by the QNJAC representative of the Road Haulage Association is leading the way on this priority for the quarrying industry and has identified as key, communication and co-ordination between hauliers and quarry workers. By improving effective communication between quarry and haulier personnel, including their employers, promoting safe working practices and a ‘Right First Time’ culture, it is anticipated that accidents associated with the interface between quarry and road haulage operations can be reduced.
By ensuring effective arrangements between employers and those on the ground, and an understanding of each others’ needs, the root cause of several different kinds of accidents can be addressed, including not only falls from vehicles, but also vehicle instability and illegality, and slips and trips. Some of the issues for consideration include:
- Site layout, vehicle segregation, signage and lighting.
- Vehicle suitability for the load, and for the loading and delivery sites.
- Vehicle design for safe access, eg control and maintenance from ground level, automatic sheeting, CCTV to view the load area.
- Effective two-way communication between loader and haulier drivers regarding the load and its placement in the vehicle.
- Improving training/skills of loader drivers to understand the importance of even load distribution appropriate to the type of vehicle and to reduce the need for load trimming. This is a significant cause of unnecessary climbing on to vehicles and falls accidents, as well as possible vehicle illegality on the road (eg uneven load distribution affecting axle weights) or vehicle instability when tipping at the customer’s site.
- Providing gantries or other safe access systems, for example to allow loads to be trimmed safely or for hauliers to use if safe on-vehicle systems are not provided.
- Safe vehicle cleaning facilities so that access areas can be kept free from contamination.
- Driver training and empowerment to understand the importance of safe access and egress, reporting of faults, and their own role and responsibility for preventing accidents.
By March 2008 it is hoped that the QNJAC will have developed a haulage ‘Good Practice Toolkit’ of practical measures for quarry and haulage operators.
Further guidance on many aspects of workplace transport safety, including a new site inspection checklist, is available on the HSE’s website (3).
References
- www.hse.gov.uk/fallsfromvehicles/index.htm
- www.hse.gov.uk/aboutus/meetings/qnjac/index.htm
- www.hse.gov.uk/workplacetransport