A Healthy Future
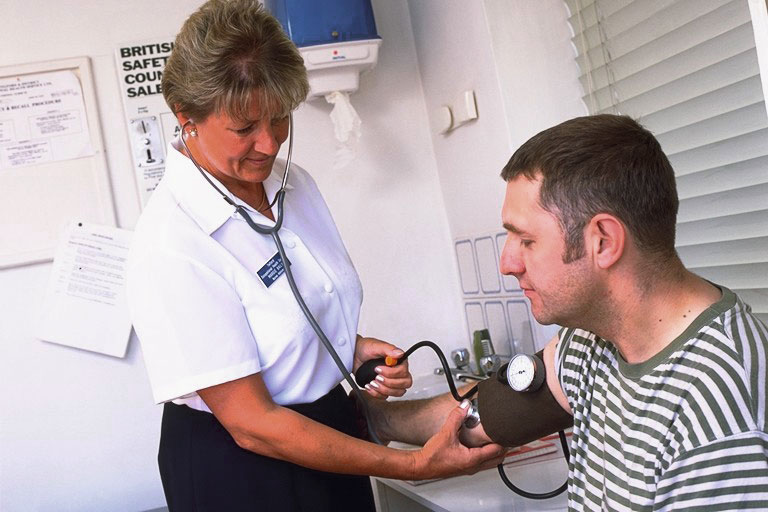
Life after the Hard Target
By Helen Turner, HSE Manufacturing Sector – Quarries Group
The success of the Hard Target (as reported in the January issue of QM) was a tremendous achievement, and due to the efforts of very many people throughout the quarrying industry. Above all, the 52% accident reduction achieved since 2000 has been the result of individual commitment by senior managers in leadership positions, safety representatives supporting and representing their colleagues, and workers doing their bit to ensure their own workplace is improved. Support has been provided by trade associations, training organizations, education establishments and professional institutions, who have all worked to provide opportunities, structures and resources to move the industry forward.
In order to deliver a further 50% accident reduction by 2010, under the new QNJAC initiative ‘Target Zero – a World Class Industry’ (see: www.hse.gov.uk/quarries/programme.htm), the quarrying industry must now renew its efforts and focus clearly on some key objectives. One such objective must be to address the causes of work-related ill health.
Size of the health problem
The HSE’s published statistics show that in 2004–5, two million people nationally were suffering from an illness which they believed was caused or made worse by their current or past work, and 576,000 of these were new cases in the last 12 months. Twenty-eight million working days were lost due to work-related ill health, compared with 7 million due to workplace injury. Clearly, this represents a huge drain on industry’s resources, and has a dramatic effect on people’s lives and livelihoods – yet even health and safety professionals tend to focus more clearly on safety issues than on health risk management.
Those working in the quarrying industry may be exposed to a number of significant health risks (if these are not properly managed), including:
- silica and other dusts
- noise
- vibration
- respiratory or skin sensitizers
- musculoskeletal injury
- harmful substances
- radiation
- stress.
QNJAC’s response
In March 2005 the QNJAC adopted a health target to ‘provide workplaces with the lowest possible levels of foreseeable occupational health risk’, and to this end all employees will participate in:
- an occupational health-management programme
- risk-based occupational health surveillance
- appropriate occupational hygiene monitoring.
Guidance on what the occupational health-management programme should include was published in 2004 on the QNJAC web site. ‘Occupational Health Management in the Quarry Industry’ can be downloaded from: www.hse.gov.uk/aboutus/meetings/qnjac/qnjac-ohg.pdf
This publication builds upon the previous guide to health surveillance, published by the QPA on behalf of the QNJAC a few years earlier, but also includes a great deal more, such as workplace welfare requirements, sickness absence management and first aid. Further reading and other sources of information are suggested.
Clearly, as with any other type of health and safety effort, occupational health risk management should be risk based. The approach needed for managing health risks is essentially the same as for safety or other business risks, and although specialist advice and support may sometimes be needed, there is plenty that can be done by a non-specialist to recognize and reduce health risks. The HSE’s ‘Five steps’ approach to risk management can be applied (a free leaflet, INDG163, is available or can be accessed at: www.hse.gov.uk/pubns/indg163.pdf).
Some quarry operators already have established occupational health arrangements. These need to be regularly reviewed to ensure that they are, and remain, fit for purpose. Some of these schemes were started several years ago and should now be thoroughly re-evaluated to ensure that they are properly risk based, or in the light of changing legislation (for example new requirements regarding vibration and noise), kept current with regard to good occupational health practice.
Health surveillance
Health surveillance is required pre-employment (Quarries Regulations 1999, Regulation 43) and under the Management of Health and Safety at Work Regulations 1999, Regulation 6, provided that:
- There is a reasonable likelihood that a disease or condition may occur as a result of the work activity being undertaken.
- There are valid techniques to detect the condition at an early stage.
- Health surveillance will be of benefit to individuals or groups of workers.
The QNJAC guide sets out the types of health surveillance required for the main health risk agents found in quarries. It is essential that this too is risk based, and matches the actual work activities of each individual. There is little to be gained by adopting a ‘one size fits all’ approach to health surveillance and having everyone undergo the same surveillance at the same intervals (eg every three years), regardless of their actual job role and the health risks they may, or may not, be exposed to in their work. Such an approach, while it may be administratively easy, can lead to some health risks being overlooked, some people being tested unnecessarily and others not being tested frequently enough to detect problems or to reflect job changes. It also has the potential to waste a great deal of time and money without reaping the intended benefits. Those actually undertaking the surveillance must have a good understanding of the industry, its processes and working environments, and be clear about the workplaces, tasks and duties of the individuals being assessed.
There is also little to be gained by undertaking health surveillance and then being unable (or unwilling) to do anything with the information. While there are issues of medical confidentiality, the data provided must allow the employer to manage risk to an individual or group, where the surveillance shows that they are being adversely affected. For example, if an employee is found to be showing signs of work-related hearing loss, action needs to be taken by his manager to ensure that this does not develop further, such as:
- checking that noise-reduction measures are in place and working correctly
- ensuring that the employee is following a safe system of work
- ensuring that the employee has the correct hearing protection, and knows when and how to use it
- redeploying the employee to different work with lower exposure to noise.
Rehabilitation
If someone is off sick, for example with a musculoskeletal injury, it is in everyone’s interest to get the person back to work as soon as possible. This is likely to be the case whether or not the original problem was work related. Being off work for a lengthy period can have severe negative effects, as a result not only of the original injury, but also, perhaps, because of the inability to contribute either financially or practically to family life, and/or because of the loss of social contacts, leading to low self-esteem, depression and other psychological effects.
Numerous examples, including some from companies in the quarrying industry, have shown that the cost to an employer of a proactive approach to sickness absence management, and a structured rehabilitation scheme to assist employees back to work, is more than offset by the financial losses of not having one. The QNJAC’s expectation is that quarry operators will implement sickness absence management and rehabilitation schemes in line with the HSE’s and QNJAC’s guidance. Plenty of information is now available on how to set up such schemes and a good starting point is the HSE’s web pages at: www.hse.gov.uk/sicknessabsence/
Working with contractors and other partners
Contractors working in quarries may be exposed to the same health risks as employees of the operator; in some cases they may be at higher risk of health effects because of the nature of work they are doing. In the same way that the operator needs to ensure the competence of all those at work in the quarry, the operator also needs to ensure that contractors’ employers have suitable occupational health arrangements in place. Regulation 11 of the Management of Health and Safety at Work Regulations 1999 and Regulation 39 of the Quarries Regulations 1999 require co-operation and co-ordination between employers where they work in partnership, and this is true of health risk management as well as safety.
The sharing of resources may well be an effective way to manage health risks – for example, when a specialist is visiting to carry out workplace monitoring or health surveillance, it makes sense to co-ordinate arrangements with contractors or others working on site or at neighbouring quarries to share the specialist resources and thus reduce costs for each operator. The principle of partnership between different employers, all contributing to improvements in health and safety, is developing as a strong theme of the Hard Target and of Target Zero.
Looking to a healthy future
In five years’ time, if the quarrying industry makes a concerted effort to fulfil the QNJAC vision, all quarry workers will understand both health and safety risks to which they may be exposed. They will understand why it is important to participate in health surveillance. Quarry operators will work together, and with contractors, suppliers and others, to ensure a co-ordinated approach to health risk management, and effective rehabilitation schemes will be the norm. This will in turn save the industry a considerable amount of money, and quarrying will be a step closer to being a ‘World Class Industry’.