The Design Of Quarry Faces And Slopes
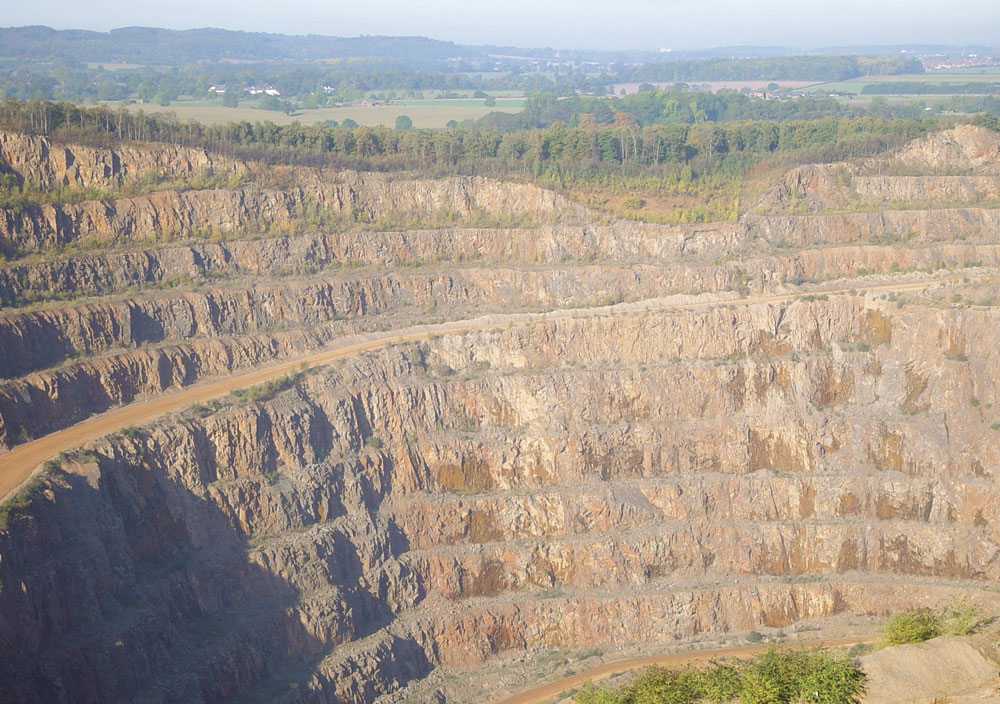
Meeting the safety objectives of the Regulator while satisfying the excavation objectives of the operator
By G. D. Matheson, Matrock Consulting Ltd, and B. Duthie, Key GeoSolutions Ltd
Quarry design involves two separate objectives which can at times appear conflicting: the safety objectives of the Quarries Regulations 1999, the accompanying ACOP, and the HSE relating to the safety of people in and near a quarry; and the excavation objectives of the quarry operator relating to extraction costs, maximization of reserves and profitability. It is suggested that a compromise is needed between these two objectives and that a successful outcome is where risks to people are minimized and the quarry can be operated safely and profitably. This article briefly considers the issues involved and outlines a Total Design Concept which is believed to be able to satisfy both objectives.
Safety objectives
The aim of the Quarries Regulations is to minimize the risk to health and safety through effective quarry design and operation. Requirements regarding safety are stated in the Quarries Regulations 1999 and guidance on how such safety might be achieved before, during and after construction is included in the ACOP and HSE publications.
In the Quarries Regulations 1999, Regulation 30, ‘General duty to ensure safety of excavations and tips’, states:
‘The operator shall ensure that excavation and tips are designed, constructed, operated and maintained so as to ensure that:
- instability; or
- movement
which is likely to give rise to a risk to the health and safety of any person is avoided’.
The requirement to design quarry faces is unequivocal and several techniques are available. One involves minimizing any natural instability by setting a face orientation which optimizes stability while minimizing the induced instability by adopting an appropriate method of excavation1. However, the variability of geotechnical conditions in a rock mass and the difficulty in predicting in advance the conditions likely to be encountered in a rock face mean that the process can only be one of optimization. This means that some instability can still be expected on a face after excavation; this could pose a risk to the safety of people in the quarry.
Similarly, the link between instability, movement and the risk to people is clear: excavations must not, at any time in their life, give rise to a risk to the safety of people. Conversely, however, this also infers that instability or movement on a rock face may be acceptable providing that it is not likely to give rise to a risk. This is a key issue and fundamental in developing a strategy which satisfies the excavation objectives (see below). In this context, it is also important, when dealing with safety, to recognize that risk can never be completely eliminated.
It follows, therefore, that two possible actions are available to deal with face instability which poses a risk. One action would be to carry out maintenance work on the face during construction, such as scaling or re-profiling to remove instability; the other to manage the risk, for example by constructing stand-off and/or containment bunds to contain rockfall. Both actions, individually or in combination, could ensure that people are not exposed to the risk of rockfall. An interpretation is that it is acceptable to leave unstable areas providing that the risks have been effectively managed. Indeed, it is further argued that there is no need to maintain a face if there is no risk to people or the risk is managed out.
If it were deemed necessary to be able to maintain quarry faces throughout the life of the quarry, this would mean that extremely wide benches would have to be designed in to allow plant access. It is suggested that this is impractical and would have a profound effect on the design of rock faces and quarry slopes, the operating costs and the profitability of the quarry, and make most quarries economically unviable.
It is possible, however, to satisfy the safety requirements if the emphasis is changed from maintenance to management of risk, which the authors suggest is the main aim of the Regulations.
Excavation objectives
It is vitally important to a quarry operator to be able to exploit the reserves of rock in a quarry to the maximum. This objective is best satisfied by forming individual quarry faces as steep as possible, with benches as narrow as possible, and faces as high as possible – consistent, of course, with stability. It is these parameters which control the slope angle of the quarry and maximize the reserves that can be exploited. Changing them can have a profound effect on the reserves that can be exploited and can have major financial implications.
Face Angle
The effect of reducing face angle on a three-benched quarry slope is illustrated in figure 1. The reserves sterilized/lost increase progressively to 12,744 tonnes for each 10m length of face as the face angle is reduced from 90° to 65°.
Bench width
The effect of increasing bench width on a three-benched quarry slope with faces at 70° is illustrated in figure 2. The reserves sterilized/lost increase progressively to 6,075 tonnes for each 10m length of face as the bench width increases from 5.5m to 10.5m.
Face height
The effect of reducing face height by introducing a bench on a single 20m face is illustrated in figure 3. The reserves sterilized/lost by splitting a 20m face at 70° into 2 x 10m faces with one 7m bench amounts to 1,890 tonnes for every 10m length of face.
It should be noted that the above calculations relating to face angle, bench width and face height are based on relatively short (10m) lengths of quarry slope and simple geometry; they will need to be increased many times to take into account actual quarry dimensions. The outcome is that very large quantities of material are involved which are likely to have a significant impact on quarry viability. Consequently, it is financially important to a quarry operator to have faces as steep and as high as possible and to have benches as narrow as possible; this results in steep slope angles which maximize reserves.
Face maintenance
A requirement that face maintenance must be able to be carried out throughout the life of a quarry would have profound implications for quarry design and costs. It is suggested that the only safe and practical method of maintaining a face is by mechanical plant. On a final benched quarry slope plant access to each bench must, therefore, be possible and, since the building of ramps or pads on the bench below an unstable face is unlikely to be accomplished safely, that plant must be able to reach the crest of the face. This means that the bench width needed to allow safe plant access and the relationship between face height and plant reach must be considered. In this scenario, the maximum reach of excavators will, therefore, determine the maximum theoretical face height.
It is estimated that a minimum bench width of 15m would be required for a long-reach excavator to operate safely. On a quarry slope formed by three 15m faces at 70° with a minimum bench width of 15m, the reserves lost would amount to approximately 10,000 tonnes per 10m of face when compared with a 7m bench width (fig. 4). When this loss is scaled to actual quarry dimensions, very large quantities of reserves are lost. This is even greater if the crest stand-off is increased or smaller plant and reduced face heights are used.
Total Design Concept
The authors suggest there are techniques which can be used to design and excavate quarry faces and form slopes which will satisfy both the safety and the excavation objectives. One solution is the Total Design Concept. A detailed explanation of this concept is beyond the scope of this article, but it involves designing faces which optimize stability2, using excavation techniques which minimize disturbance1 and designing benches (on single faces this would be the quarry floor) according to Alejano3 but with additional bunds and a covering able to contain rockfall from the face(s) above.
Ongoing risk assessment is carried out using hazard appraisals and geotechnical assessments on the faces immediately following excavation in the style of the Quarries Regulations (1999), using simple risk-assessment techniques4. This confirms that the bench design is capable of containing rockfalls and that the risk to people is minimized; if it is not, maintenance and/or risk management is carried out and the design is updated accordingly. Rockfalls are therefore avoided or contained, no access to benches above is needed, and risk is effectively managed. The result is final quarry slopes which are virtually maintenance free (fig. 5), not because of the absence of instability in the faces but due to the fact that the risk to people has been effectively managed.
Conclusion
It is suggested by the authors that a new approach to quarry design based on the Total Design Concept can satisfy both the safety objectives of the Quarries Regulations (1999) and the excavation objectives of the quarry operator. A further advantage of the concept is that it allows a ‘cradle-to-grave’ approach to be applied to quarrying in which the risk is consistently managed throughout the life of the quarry.
Methods based on the concept have already been successfully used to update the designs of several large quarries in the UK, and a professional paper is in preparation.
REFERENCES
- MATHESON, G.D.: ‘The stability of slopes exposing rock’, Proc. Int. Symp. on Failures in Earthworks, Inst. of Civil Engineers, London, 1985.
- MATHESON, G.D.: ‘The collection and use of field discontinuity data in rock slope design’, Quart. Journ. Eng. Geology, Geol. Soc., London, 1989, vol.22.
- ALEANJO, L.R. et al: ‘Slope geometry design as a means for controlling rockfalls in quarries’, Int. Journ. Rock Mechanics and Mining Sciences, 2007, vol. 45, pp1252-1272.
- MATHESON, G.D. and G. REEVES: ‘The identification, appraisal and assessment of hazards on quarry rock faces in terms of the UK Quarries Regulations’, Paper submitted to Quar. Journ. Eng. Geology, Geol. Soc., London, 2010.
This content of this article is taken from a talk given to the Scottish branch of the Institute of Quarrying at Stirling on February 2010 by the senior author (GDM)
For more information, contact Brian Duthie on tel: (01952) 822960.