Wheel Wash Plays Key Role At Cumbrian Asphalt Plant
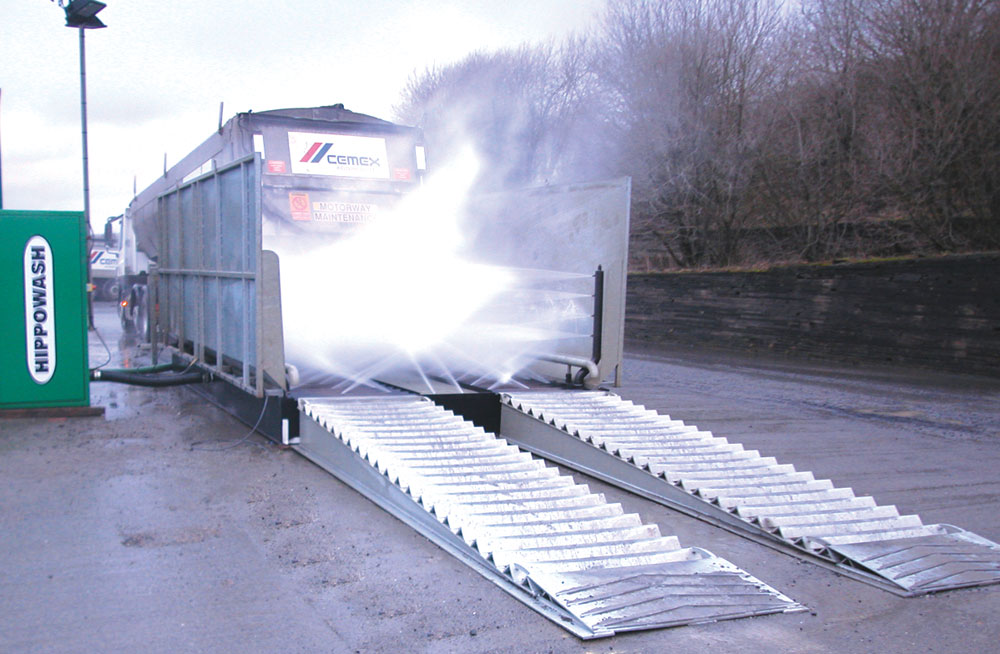
New Hippowash wheel-washing system for CEMEX plant near Shap
A new vehicle wheel-washing system, supplied and installed by Hippowash, is ensuring vehicles leaving CEMEX’s newly commissioned asphalt plant, near Shap, in Cumbria, do not carry any dirt or debris out on to the public roads.
The new asphalt plant is capable of producing up to 100,000 tonnes of coated stone per year, primarily using aggregates from the adjacent Shap Blue Quarry. The coating plant can operate 24h a day, seven days a week, generating an average of up to 50 vehicle movements per day, including sand deliveries.
This round-the-clock capability allows the plant to fulfil night-time contracts in order to avoid disruption to day-time traffic. The planning consent for the new coating plant stipulated that the facility must have a vehicle washing system to ensure that surrounding roads remain clean all year round. CEMEX chose the Hippowash Classic model based on its proven track record in harsh quarry operating environments, together with its energy and water-saving design features.
A new concrete road was built for the above-ground Classic washer, which has a 6m wash platform, constructed from inverted steel angle. The vehicle wheels go through two complete revolutions over this wash section and, together with the similarly constructed entry and exit ramps, this configuration optimizes mechanical mud removal as part of the overall cleaning cycle.
The wash system is fully automatic and requires no driver involvement; vehicle detection sensors start the main wash pump as a vehicle approaches the wash. Up to 1,600 litres of water per minute are delivered through 130 brass jet heads, cleaning the wheels and under-chassis as the vehicle passes, with mud and debris-laden water falling into the integral sump. As the vehicle exits the wash and passes the second sensor, the main pump automatically switches off.
Meanwhile, the sump pump is left to grind up the solid material and send it, together with the dirty water, to an external waste-water clarifying system. The lamella design of this unit rapidly removes over 95% of solids down to less than 20 microns, leaving clean water for the next wash cycle. The settled sludge can then be easily disposed of via the hoppers at the bottom of the clarifier, as required.
This closed-loop water system, together with the galvanized side screens, minimizes water wastage and removes the need for expensive, water-hungry lagoons.
Minimizing power requirements and optimizing energy usage are essential for busy wash systems, and unlike most competitive units the Hippowash Classic uses an inverter-driven main wash pump. This not only gives up to 50% energy savings compared with traditional motor starting methods, but also allows unlimited pump start-ups without any detrimental effect on pump longevity.
In addition, the power to the main wash pump can be reduced during periods where only lighter dust-suppression type washing is required. According to Hippowash, typical annual savings in energy costs can be in excess of £10,000.
CEMEX’s vice-president of aggregates and asphalt, Lex Russell, commented: ‘The Shap operation has to be available round the clock to supply much-needed asphalt to road construction projects. It is vital that we comply with legislation relating to keeping public roads clean, especially in the winter when the site can be particularly muddy.
‘The Hippowash system not only ensures the vehicles leave the site in a very clean condition, but also provides valuable cost savings relating to energy and water usage. The equipment has proved to be very reliable and installation was carried out well within our time frame. The automatic washing system and water-filtration plant allow a steady throughput of vehicles with minimal maintenance requirements.’
Hippowash, Poplar Grove, Crewe, Cheshire CW1 4AZ; tel: (01270) 252669; fax: (01270) 252670; email: sales@hippowash.com