Water Pollution Wake-Up Call
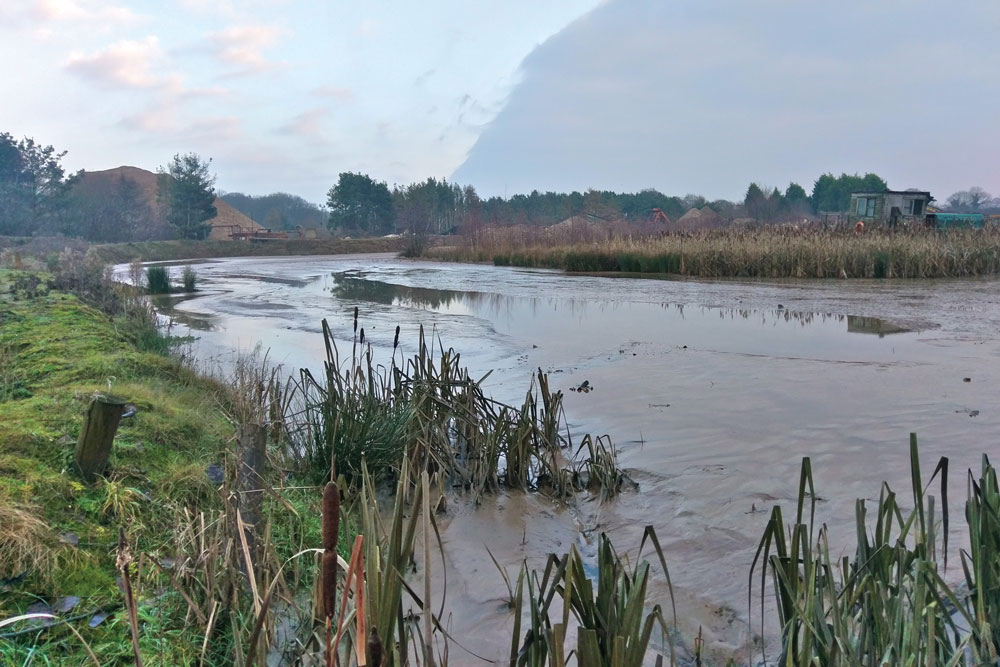
First published in the July 2017 issue of Quarry Management
Thames Water’s recent £20.3 million fine for polluting the environment represents a wake-up call not only for the UK’s municipal water industry, but also for anyone in the quarrying industry involved in pumping water off site and releasing it into the environment. Dr Richard Coulton, founder of water treatment specialists Siltbuster Ltd, elaborates.
Although the magnitude of the fines for pollution incidents has been increasing following the introduction of new sentencing guidelines in 2014, the judgement against Thames Water established a new framework against which future fines will be set.
The 2014 Guidelines set out a standardized approach in which sentences for a pollution event are determined on the basis of not only the significance of the incident, but also the size of the company and the degree of corporate culpability. In particular, the Guidelines provide a culpability range from ‘low or no culpability’ (eg where the incident was the result of accident or action of a rogue employee) to ‘deliberate’, where there was an intentional or flagrant breach of the law by those in a position of responsibility.
The systemic failures identified by the Thames Water case led Judge Sheridan to conclude that these events must have been the result of deliberate action by those in authority within the company. In giving his judgement, Judge Sheridan took the sentencing process a step further by applying the following principles:
- It should not be cheaper to offend than to take appropriate precautions;
- Shareholders need to understand that the environment is to be treasured and protected, and not poisoned;
- Fines need to be sufficiently large to get that message across.
What does this mean for the quarrying industry?
Clearly, the implication from this case is that all quarries discharging water off site have little choice but to ensure they adopt best environmental practice. Those that do not will face the risk of incurring fines greater than the cost of complying. If nothing else, the Thames Water case makes it clear that environmental compliance is now the least-cost option.
The ruling has potential significance at all levels of company management, from the grass-roots operators to the directors at board level. Whilst operators on the ground are often responsible for the physical actions that cause a pollution incident, the company itself is also often culpable due to poor management or failing to adequately promote the importance of environmental protection.
To minimize this risk, quarrying companies need to extend the philosophy of ‘zero harm’ beyond the protection of personnel and the public to include the surrounding environment. Without the adoption of such a philosophy a company operating multiple quarries could, for example, find itself defending a case of deliberate culpability as a result of a number of unrelated pollution incidents.
In addition to the direct cost, companies found guilty of an environmental breach would also be faced with indirect costs together with the loss of corporate credibility, local goodwill and, potentially, future business opportunities, not to mention the public relations costs incurred in trying to restore a damaged reputation.
How big a risk is water pollution within quarrying?
Most quarries have excess water to dispose of back to the environment. This arises from a number of sources, including groundwater seeping into the site, precipitation falling directly on to the site (or inflowing as surface water from the surrounding area) and excess process water. The characteristics of each of these streams can be very different depending on the superficial and solid geology of the site, and the processing method.
Irrespective of the source, water treatment at most quarries involves the removal of suspended solids and the capture of any hydrocarbons spilt as a result of hydraulic hose failure or fuel spills. Depending on the site geology or process involved, the water may also need to be treated to correct the pH and remove dissolved metals.
Critical to the successful management of water at all quarries is segregating clean water and pumping this away before it has the chance to become dirty. This strategy has a number of advantages, namely:
- It minimizes the amount of dirty water to be treated, reducing the size of any treatment lagoons/ponds or water-treatment plant required;
- It minimizes the cost of treatment;
- If all the water from the site is discharged via a single consented point, the clean water can be mixed with the treated water, helping to further reduce the suspended solids concentration (although from the perspective of the Regulator, dilution is not an acceptable method of treatment).
Groundwater seeping into the site is normally managed by either a single sump or a perimeter drain excavated around the base of the quarry. The inflow groundwater should be virtually solids free and, therefore, provided it does not contain any dissolved contaminants or have a low pH (and is kept away from the dirty water collected near the working face), can be discharged off site without further treatment. Suspended solids in the incoming seepage is a sign that the ground around the quarry is being eroded by the inflowing water, which can lead to the formation of sinkholes in sand deposits or erosion of material from weather joints in the rock, in which case the source of the solids should be investigated and, if appropriate, remedial measures put in place.
Lowering the groundwater to allow quarrying to be undertaken in dry conditions introduces air into the rock, which, in pyrite-bearing strata results in the oxidation of the pyrite, generating sulphuric acid and dissolving iron (and any other soluble metals, such as aluminium and manganese) into the water. Unfortunately, unlike the suspended solids problem, which stops once the quarry is reinstated, pyrite oxidation continues long after the quarry has been abandoned and represents a long-term environmental legacy that the quarry owners have to take responsibility for. Although not common, this problem can represent a significant ongoing cost both during quarrying and on closure.
As surface water streams etc are normally diverted around the quarry (and therefore do not need treatment), the main source of surface water entering the quarry is precipitation, either falling directly into the quarry or on to adjacent slopes draining into the quarry. This water becomes contaminated with suspended solids as it flows into the excavation. Where possible, it is important to keep this water separate from the unpolluted groundwater and, if space allows, ideally the quarry should operate two sumps (one for clean groundwater and the second for solids-laden surface water). As the footprint of most quarries is relatively large, significant volumes of water can fall on the site during storm events. Rather than sizing the treatment plant to handle the peak inflow, the water can be stored in a temporary/balancing lagoon from where it can then be treated and discharged off site a reduced flow rate.
In upland regions, the presence of humic acid in runoff from peat-covered areas may also need to be managed. This may require pH adjustment and the addition of coagulants/flocculants to remove finer suspended solid particles.
Process water is a major source of contamination from quarries. In addition to suspended solids removal, with some processing applications the water will also need to be treated to correct the pH. For example, where acid leaching is used to remove iron staining from glass sand or to improve the whiteness of china clay, pH correction will be needed. Equally, it will be required where high-pH waters are generated as a result of concrete production. Attention also needs to be paid to the safe storage of processing chemicals, as in one recent case a quarrying company was fined £100,000 for releasing 500 litres of chemicals from its processing plant.
Suspended solids are typically removed from the water to be discharged off site by passing it through a series of settlement lagoons, where the coarse, rapidly settling solids settle out of suspension. However, such systems are not capable of removing clay and colloidal-sized solids, and in these situations it is necessary to chemically pre-treat the water with coagulants and/or flocculants to combine the finer particles into larger, more rapidly settling particles.
Although most quarries have a long operational life, the composition of the excess water pumped off site and the flow regime within the quarry is subjected to continual change as the excavation proceeds. It is, therefore, necessary to regularly review and update the water-management strategy to reflect these changes.
Whilst the discharge from each quarry is unique, the consequences of getting it wrong are identical irrespective of whether it is a hard rock quarry or a sand quarry. Putting it simply, it is illegal to knowingly cause the discharge of contaminated water into controlled waters (ie surface, ground or coastal waters). A typical pollution incident from a quarry causes discolouration of the water, smothering of the riverbed and, potentially, the death of aquatic species. In recent court cases quarrying companies have been fined £15,000 and £35,000 for discharging silt-laden water off site, and one particular company was told by the judge that if a repeat incident occurred from the quarry in question, or another of the company’s quarries, it would be considered to be a deliberate act and so any future fine would be significantly greater.
How should companies respond?
So, what can the quarrying industry do to help protect the environment and minimize the risk of being charged with deliberate culpability as a result of a series of unrelated incidents?
The key is to focus on three core areas. First, the board of directors needs to give environmental protection a similar level of importance as health and safety by:
- Developing a culture that recognizes and promotes the importance of environmental protection;
- Disseminating that culture throughout the business. Such a top-down approach must be adopted if quarrying companies are to avoid falling into the deliberate culpability category, should more than one incident arise;
- Putting in place a corporate audit procedure to ensure environmental protection policies and procedures are being followed, regularly reviewed and updated;
- Deciding whether water treatment and the associated environmental protection liabilities are best handled internally or via the appointment of a third party operator who would be responsible for environmental compliance.
Management also has a role to play in promoting a culture of environmental responsibility by ensuring that:
- Protecting the environment is given a high priority;
- Staff are adequately trained and understand their responsibility and the implications of their actions not only on the environment, but also on the company;
- Critical aspects of the water treatment process are identified and either duty/standby equipment installed or critical spares made available;
- Appropriate maintenance procedures are in place, used and regularly updated;
- A suitable environmental monitoring system is installed and kept operable;
- The collected data are analysed to not only provide performance verification, but also to pick up trends and provide meaningful defensive data in the event of an incident;
- Contingency plans are put in place, tested and regularly reviewed;
- An open relationship is developed with the Regulator (be it the EA/NRW/SEPA for discharge to water course);
- Operators are aware of their environmental responsibilities, the implication of their actions and are adequately trained;
- Adequate budget is provided to operate, maintain and, if necessary, upgrade water treatment equipment.
Last but not least, operational staff need to be:
- Adequately trained and supervised;
- Familiar with the operational performance of the water treatment plant;
- Trained to handle an emergency situation;
- Aware of the legal and financial risks of getting it wrong;
- Encouraged to report their concerns to management.
It is only by adopting a systematic approach to environmental management that both the risk of a pollution incident occurring and the magnitude of the resultant fines can be minimized by the quarrying industry. For more advice on treating quarry water, visit: www.siltbuster.com
- Subscribe to Quarry Management, the monthly journal for the mineral products industry, to read articles before they appear on Agg-Net.com