The Path to Cement Carbon Neutrality
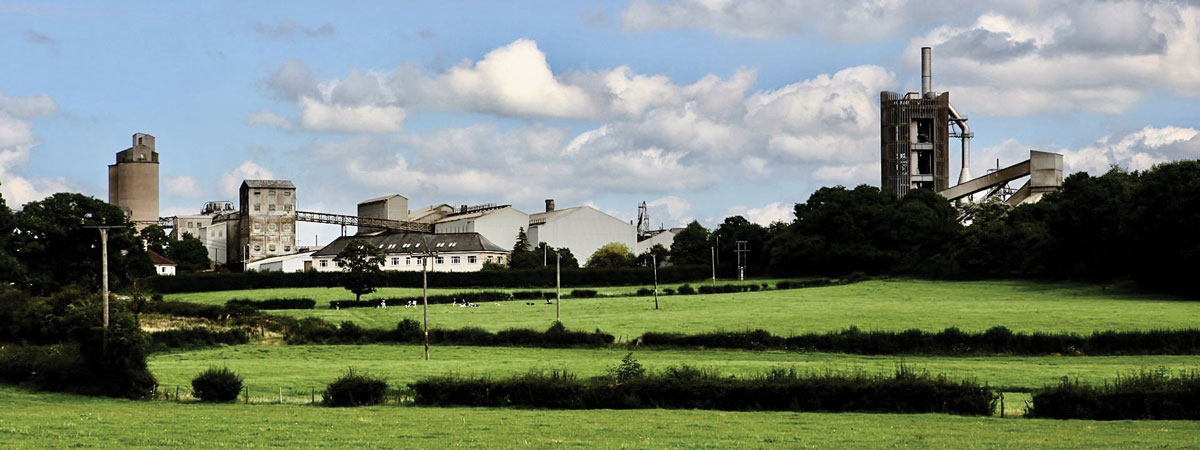
First published in the June 2021 issue of Quarry Management
Hanson are focused on climate protection and committed to fulfilling their share of the global responsibility to keep the rise in worldwide temperature well below 2°C, as set out in the Paris Agreement. Marian Garfield, sustainability director, explains the company’s path to reducing carbon emissions
As a leading cement manufacturer, we take our responsibility very seriously. Hanson is part of the HeidelbergCement Group – one of the world’s largest building materials companies (number one in aggregates production and ready-mixed concrete, and number two in cement), with around 54,000 employees working at more than 3,000 production sites in over 50 countries on five continents. In the UK, Hanson operate more than 300 sites and make 6,000 deliveries a day.
Hanson UK’s pathway towards cement carbon neutrality has been ongoing for many years. Our sustainability responsibilities have long been embedded in our business and between 1990 and 2020, we reduced our CO2 emissions in the UK by almost 50%.
This was achieved through a number of measures, including:
- Process improvements – significant investment in new plant and equipment, for example, installing modern automated control systems.
- Clinker replacements in our cement – maximized to those allowed within national cement standards.
- Increased use of alternative fuels – replacing the transitional coal by more than 60% by using waste paper and plastics, waste liquid fuels, biomass and other fuel types.
- Increased usage of Regen GGBS (ground granulated blast-furnace slag) in our concrete, reducing overall embodied CO2 in our products.
HeidelbergCement also have a strong track record in reducing CO2 emissions: by 2019, they had already achieved a 22% reduction in the specific net CO2 emissions per tonne of cementitious material compared with 1990 levels.
They were awarded a place on CDP’s 2019 and 2020 Climate Change A-list and were also the first cement company to receive approval from the Science Based Targets initiative (SBTi) for science-based CO2 reduction targets to limit global warming to below 2°C.
In September 2020, HeidelbergCement adopted a ‘beyond 2020’ strategy, with sustainability as one of six core areas, and they have committed to reduce net CO2 emissions per tonne of cement by 30% by 2025 (based on 1990 figures) and will realize their vision of carbon-neutral concrete by 2050.
These are ambitious targets but are based on a bottom-up roadmap, which has been built plant by plant, country by country, across the company’s 50 countries of operation.
Plans to reduce HeidelbergCement’s carbon footprint and increase energy efficiencies have been embedded as hard targets and are linked to every manager’s remuneration and a large part of our investment and research efforts have been, and will continue to be, directed towards achieving this goal.
The most important levers in Hanson UK’s pathway towards cement carbon neutrality are:
- Major investments in plant efficiency across all operations – small thermal and efficiency improvements are still possible.
- Increased use of alternative raw materials and fuels.
- Substitution of the CO2-intensive clinker in cement by secondary cementitious materials – new cement types being introduced to the market to reduce embodied carbon (increased limestone products).
- Fuel switching to hydrogen.
- Increased share of sustainable low-carbon concrete products – traditional and alternative secondary cementitious materials set to increase (calcined clays and recycled concrete fines being explored).
- Carbon capture, use and storage.
Fuel switching
Hanson are taking part in a groundbreaking research project, fed by the Department for Business, Energy and Industrial Strategy (BEIS) and awarded through the Mineral Products Association (MPA), which could lead to cement and lime kilns operating with a net-zero-carbon fuel mix.
A BEIS-funded feasibility study in 2019 found that a combination of 70% biomass, 20% hydrogen and 10% plasma energy could be used to eliminate fossil fuel CO2 emissions from cement manufacturing. Our aim is to test that theory by researching the potential of hydrogen and plasma technology to reduce carbon emissions through switching from fossil fuels on an industrial scale at our Ribblesdale cement works in Clitheroe, Lancashire.
The project results will be shared with UK and global industry to maximize the environmental benefit of the technology. If successful, the UK cement industry could save around two million tonnes of CO2 a year: equivalent to the annual emissions from 266,000 households.
In a separate project, Hanson UK are working in collaboration with the Energy Safety Research Institute at Swansea University to test green hydrogen as an alternative energy source.
A hydrogen demonstration unit, which generates green hydrogen through the process of electrolysis, has been installed at our Regen GGBS plant in Port Talbot. Its aim is to replace some of the natural gas used to power the plant with green hydrogen.
Renewable energy is generated through wind and solar on site and directed into the electrolyser or water-splitting device, which can efficiently use this energy to split water into hydrogen and oxygen. The hydrogen is then passed into the burner to enrich the combustion mixture, saving carbon emissions from the burning of natural gas.
Carbon capture and storage
Hanson UK’s involvement in the HyNet North West project is the latest example of our commitment to cutting CO2 emissions.
The consortium has been awarded funding totalling £72 million to create the world’s first low-carbon industrial cluster through its development of a hydrogen and carbon capture and storage (CCS) project. The project will play a critical role in the UK’s transition to net-zero greenhouse gas emissions by 2050 and the fight against climate change.
The HyNet North West region stretches from Flintshire and Wrexham, through Cheshire, Liverpool and Greater Manchester into Lancashire. It has the largest concentration of advanced manufacturing and chemical production in the UK, including Hanson’s Padeswood cement works, near Mold, Flintshire.
As a consortium partner, we are carrying out a CCS feasibility study at Padeswood to provide a clear design basis and cost estimate for a carbon capture plant and connection to the planned HyNet North West CO2 transport and storage system.
The project has the potential to reduce regional CO2 emissions by up to 10 million tonnes – including up to 800,000 tonnes from the Padeswood plant – every year by 2030: the equivalent of taking four million cars off the road.
In Norway, HeidelbergCement will realize the first industrial-scale CCS project at any cement production facility in the world at their Brevik plant. Work on the new facility has begun, with the goal of starting CO2 separation from the cement production process by 2024.
The result will be a 50% cut in emissions from the cement produced at the plant with 400,000 tonnes of CO2 being captured annually and transported for permanent storage offshore under the seabed.
HeidelbergCement are also scaling up their CCS project following the successful first phase of their LEILAC (Low Emissions Intensity Lime and Cement) project.
As part of LEILAC 1, a CO2 capture pilot installation with a capture capacity of 25,000 tonnes of CO2 per year was constructed at the company’s plant in Belgium in 2017. The second phase involves an installation around four times larger at HeidelbergCement’s Hanover cement works in Germany, which will capture 20% of the plant’s emissions, corresponding to around 100,000 tonnes of CO2 per year.
The first project design phase is due to be completed by the end of June 2021 and the demonstration installation is expected to be ready by the end of 2023. LEILAC 2 is expected to be completed by 2025.
The LEILAC technology, developed by HeidelbergCement together with Australian company Calix and a European consortium, has the potential to enable the cement and lime industries to reduce their emissions dramatically.
We have made good progress since 1990 in our roadmap to net-zero carbon and beyond, but there is still work to do and we will continue to focus on reducing our carbon footprint and increasing energy efficiency.
- Subscribe to Quarry Management, the monthly journal for the mineral products industry, to read articles before they appear on Agg-Net.com