Controlling Dust Quietly
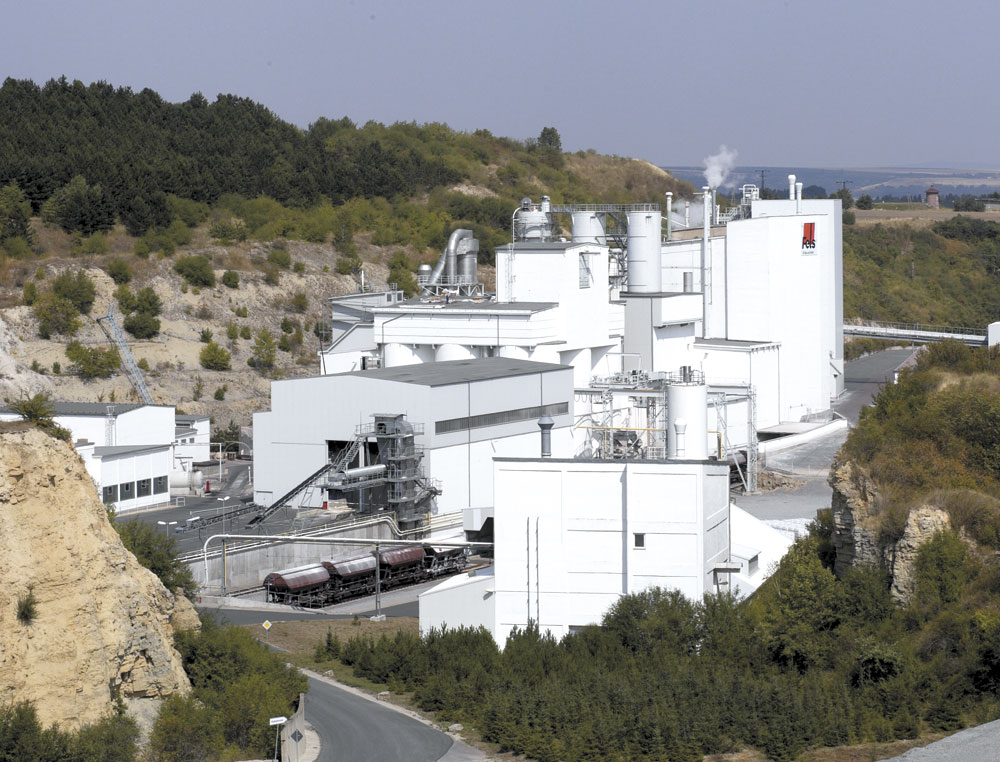
Tackling dust without increasing noise emissions
By Gus Bishop, Dantherm Filtration Ltd
Few would argue that quarries and associated processing plants are inherently dusty and noisy operations. Short-term peak emissions of dust and noise, eg from blasting, may be unavoidable, but other longer-term or continuous sources of noise and dust – likely sources of complaints from near (and not so near) neighbours – are treatable to varying degrees. It is clearly beneficial to make use of available materials and features to minimize emissions, particularly in sensitive directions; for example, overburden that must be removed initially may be used to form a baffle at the site perimeter; and crushing, screening and grading plant should be located to minimize nuisance noise. Obviously, established quarries with a floor well below the surrounding ground level will cause fewer problems, at least with respect to noise.
Amid the range of sounds emitted by static and mobile machinery, the relatively low grade noise from dust-extraction fans and discharge systems may be dismissed as insignificant. However, neighbour complaints can arise from continuous tonal noise from dust-extraction fans and ducting, particularly during extended shift working. Quarries and their processing areas are, of course, designated workplaces, subject to the provisions of COSHH Regulations, limiting airborne dust, and The Control of Noise at Work Regulations 2005, with the recently introduced lower action levels.
Mineral extraction may be associated with on-site production facilities such as clay preparation for brick making, cement manufacture or asphalt production. In such cases, with the exception of asphalt mixing, a centralized dust-extraction plant could be economic, to serve material crushing, grading, screening and conveying adjacent to the production plant should a compact layout be possible.
Dealing with dust
As part of general accident reduction targets set by the Health and Safety Executive (HSE), the abatement of dust, in particular silica dust, has been identified as an important factor. The maximum exposure limit (workplace exposure limit, or WEL) for crystalline silica is set very low, at 0.3mg/m3 (8h time-weighted average or TWA). Most other undefined mineral dusts have TWAs of 10mg/m3 for inhalable dusts and 4mg/m3 for respirable dusts. These limits are published in the regularly updated HSE handbook EH40/2005 – Workplace Exposure Limits. While personal protective equipment (PPE) may be employed, it should not be the first defence against potentially harmful emissions.
Drilling machines, whether larger, relocatable units or hand-held devices, should have effective dust control, with wet drilling preferred where practicable. Mobile plant is an obvious source of dust. To protect operators, cabs should be fitted with positive-pressure air-filtering systems. Control rooms and other site offices may be similarly equipped. Careful loading of crushers, with minimal drop heights, will assist the dust collection at these machines, particularly as relatively low wind speeds on site can negate the effect of partial enclosure hoods. Other outdoor applications may be served by atomized water sprays. Adjacent conveyors should be enclosed where possible, with dust extraction hoods at their loading and delivery points. Belt conveyors should be fitted with effective and accessible scraper bars to prevent spillage from the return belt, and these should be fitted with dust-extraction hoods. A conventional reverse jet pulse-cleaned bag filter could serve the crusher and adjacent conveyors. Much nuisance dust from mineral processing machines may be described as ‘fugitive’; that is, the dust-extraction hoods apparently work well, but the areas around machines remain randomly dusty. For example, screens for progressively grading particle sizes may be fitted with part-enclosure hoods, with further dust hoods on vehicle loading spouts beneath the hoppers. If this plant is housed in a building, it may be beneficial to add forced ventilation to the enclosed area, in this case maintaining a slight negative pressure, again served by the centralized dust collector.
Many secondary processes are situated at quarry sites. However, hot-mix asphalt production requires dedicated filtered extraction principally to ventilate directly fired aggregate driers, with a smaller extraction requirement from mixers. The moist, dust-laden extracted air/gas is first passed through a skimmer-type pre-separator to remove larger particulates, which are returned to the mixer. The dust-laden air/gas, at about 120°C, is then passed through a bag filter fitted with media resistant to hydrolysis. As driers are normally directly fired, the air/gas passing into the filter contains a high concentration of flue gases with unburnt hydrocarbons, so the filter unit has to be thermally insulated to prevent damaging internal condensation. The discharged dust can be reprocessed for use as filler.
Where brick making or cement manufacture is associated with quarry workings, specialist dust-extraction solutions can be applied, including, for example, higher-temperature extraction to ventilate brick kilns and to handle cement clinker or ventilate ball mills.
Noise reduction
Noise in dust-extraction systems is principally generated by the extraction fans. However, potentially annoying lower- frequency noise may emanate from the filter body and hopper due to internal air turbulence. Blade-type volume-control dampers in main ducting can also contribute markedly to the overall noise. It is often economic, as well as desirable, to control larger fans by means of inverter drives, eliminating the need for energy-hungry, noisy dampers. The noise from fans can usually be sufficiently attenuated by means of air silencers and acoustic enclosures. However, in-line air silencers offer some resistance to the air and, therefore, add to the energy requirements of the plant. Other, often more efficient dynamic acoustic treatments are therefore worth investigating. These are available from some specialist acoustic companies and may successfully attenuate tonal emissions from constant-speed fans without using extra energy. If possible, all such equipment should be sited to make use of any available natural screening features, possibly including adjacent buildings. In the quest to limit noise emissions for both site workers and neighbours, regular maintenance is very important. Hard-worked machinery operating in potentially abrasive atmospheres can soon lose efficiency – and become noisier – if neglected, leading to breakdowns and unwanted complaints. So, being a good neighbour can also prolong plant life and save money.