Blueprint For Change
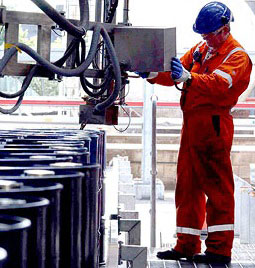
Carbon Trust blueprint could save the aggregates industry £45 million a year
By Leon Labovitch, ALSF programme manager at the Carbon Trust
The economic downturn has had a significant impact on the aggregates industry, with sales dropping by as much as 25% across the board. At the same time, local government, central government and Highway Authority clients, looking to ‘green’ their supply chain in order to hit UK carbon-reduction targets, are putting quarry managers under increasing pressure to cut their own carbon emissions.
Faced with these challenges, many quarry managers are looking for ways to improve their operational efficiency and ensure that their business not only survives, but thrives in the long term.
Help is at hand from the Carbon Trust’s new ‘blueprint for change’, which could see the aggregates industry save £45 million a year by using energy and fuel more efficiently. The blueprint was developed in consultation with the UK’s leading aggregate companies, the Mineral Products Association (MPA) and the British Aggregates Association (BAA), and was funded by the Government’s Aggregates Levy Sustainability Fund (ALSF).
The blueprint takes a consistent and co-ordinated approach to cutting the industry’s carbon emissions and cost base right across the site, from asphalt burners and conveyor belts to haulage. It provides quarry managers, and all staff working in quarries, with the practical advice and knowledge they need to identify where cost and carbon-reduction measures can be introduced across the quarry’s operations.
By adopting simple measures, an average quarry could cut its energy use by 20% and save up to £200,000 each year. These measures would also save the industry 713,000 tonnes of CO2 in the next three years alone, allowing quarries to improve their sustainability credentials.
As an energy-intensive business, the aggregates industry has an opportunity to lead the charge in demonstrating best practice in reducing carbon emissions and improving operational efficiency.
The blueprint recommends a toolkit of 30 actions that quarry owners and aggregate producers across the UK can take to reduce their carbon footprint, and includes recommendations for the eight key actions that will save the most money and cut the most carbon. These are:
1. Keep stockpiles dry
When stockpiles become wet as a result of being stored in the open air, it takes more time and energy to dry them. Reducing the stockpile’s moisture content by just 2% can cut energy use by as much as 25%, as well as reducing drying time and increasing throughput. Reducing water content by this small amount could save the industry up to £13 million every year. For a single asphalt plant, that could mean savings of at least £100,000 a year.
Options to reduce moisture include using a cover over the stockpile to stop water getting in; introducing a drainage system underneath the stockpile to allow water to drain away; positioning stockpiles on a natural slope to help water drain away; and rotating stockpiles to ensure the driest aggregate is used while the other stockpiles dry out.
2. Check asphalt burners
By ensuring that burners are working efficiently, quarry managers can cut energy use and see strong gains in productivity and profitability. A key measurement to assess efficiency is to test the level of carbon monoxide the drier produces in the flue. If this is high it often means that the drier is not burning efficiently and that fuel is being wasted. However, levels can easily be checked using a carbon monoxide analyser. A combustion engineer can help to fix the problem and, as a result, save the operation up to £15,000 a year.
Another important opportunity for cost and carbon reduction is to take a close look at asphalt drier drums. Inside the drum, the aggregate should be falling in a uniform curtain otherwise it will waste energy. An engineer can check lifters in the drum, as well as the insulation and seals, to ensure they are working efficiently.
3. Plan journeys using satellite tracking
Using satellite navigation to work out the fastest routes to destinations can save up to £250 in fuel costs per vehicle every year. Quarries can also look at tracking and monitoring fuel usage to identify where unusually high amounts of fuel have been used and take the necessary steps to fix the problem. Further savings can be made by improving quarry haul roads.
4. Drive in an energy-efficient way
As aggregate reserves are often located far from large cities, the cost of distributing aggregates can be high. Drivers can reduce expensive fuel bills through specialized training with Safe and Fuel Efficient Driving (SAFED), which provides tips and techniques to get more miles out of every gallon, ranging from reducing idling times to checking tyre pressures regularly. The training can save companies between £1,000 and £2,000 in fuel each year for every vehicle. For a large fleet of trucks, this can lead to significant savings.
5. Manage loads into crushers and conveyors
Managing loads and crushers efficiently can save a business up to £7,000 a year. For example, the impact of light loading or leaving a crusher running when no rock is passing through can waste significant amounts of energy. Quarries should consider managing load throughput and choke feeding to ensure they get best value for money from the rock crusher when it is switched on. Conveyor belts are also a key culprit for wasting energy as they are often left running with no load. Switching them on in the correct sequence and managing the loads well will help conveyors work to maximum efficiency. It is also important that operators check the tension of the ‘V belt’ to ensure slippage losses are minimized.
6. Ensure compressed-air systems are well maintained
Look after your compressed-air system: even a small split in the pipe can waste hundreds of pounds in energy each year, yet it costs just a few pence to fix it immediately. It is also worth investigating whether a low-pressure fan could replace an energy compressed generator.
7. Understand your energy use
One of the keys ways to understand how and where energy is being used is through sub-metering. By monitoring the use of gas, electricity and diesel in different operations, quarries can quickly discover where the most energy is being used. This will help to identify and fix any issues that arise. Energy sub-meters will also show exactly how much money is saved when a quarry switches off equipment not in use or performs regular maintenance checks.
8. Involve employees in saving energy
As in the home, clever technology will only go so far. People have to play their part in using less energy too. By getting colleagues and employees involved in devising energy-saving ideas, quarry managers can ensure the entire workforce is engaged. This means that energy-saving measures are more likely to have a successful long-term impact.
Implementing change
By taking a holistic view of expenditure and putting in place a carbon-reduction strategy, quarries can improve energy efficiency, business effectiveness and profitability, helping them to thrive in the long term and survive in the short term.
Quarries that move early on cutting carbon will not only generate substantial cost savings and revenue gains, and make their tenders more attractive to carbon-conscious procurement bodies, but will also strengthen their long-term competitive position.
In order to help quarry managers implement and embed the carbon-cutting actions that bring the highest potential cost saving, the Carbon Trust has developed an educational DVD aimed at all quarry staff. The DVD provides practical advice on how quarries can reduce their operating costs, energy use and carbon emissions.
Quarries can also take advantage of on-site surveys from the Carbon Trust to get a professional overview of energy-saving opportunities that exist across their organization. A specialist team will visit the site, identify a package of measures tailored to the organization’s needs and help to put an action plan in place.
Any improvements to operations and equipment made to the site are likely to have long-term cost-saving and efficiency benefits for the business. Depending on their annual energy spend, some quarries could be eligible to apply for an interest-free energy-efficiency loan from the Carbon Trust. These loans can vary from as little as £3,000 up to £400,000, allowing aggregates companies to upgrade to more energy-efficient equipment that will deliver cost savings across their life-cycle. In most cases, the energy savings achieved more than cover the cost of repayments, which are paid back over a period of up to four years. This simple step can help quarries access some of the best equipment on the market and help them achieve cost savings for years to come.
To obtain a copy of the DVD, or for further advice, visit: www.carbontrust.co.uk/aggregates or call the Aggregate Team at the Carbon Trust on tel: (0800) 085 2005.
The Carbon Trust is one of the world leaders in reducing carbon energy consumption and helping businesses save costs. Since it was founded it has supported businesses across a range of sectors, helping to save over £1 billion in energy bills.
Top Energy-saving tips
- Keep stockpiles dry
- Check the flame and drum set-up of asphalt burners
- Drive in an energy-efficient way
- Use satellite tracking to plan transport
- Manage loads into crushers and conveyors
- Ensure compressed-air systems are well maintained
- Use meters to manage energy use
- Get involved in your company’s energy-saving efforts.
Top energy guzzlers
- Asphalt burners
- Road transport
- Mobile plant for loading and hauling
- Crushers
- Conveyor belts
- Compressed air.