Explosive Findings Cut Costs for Quarrying
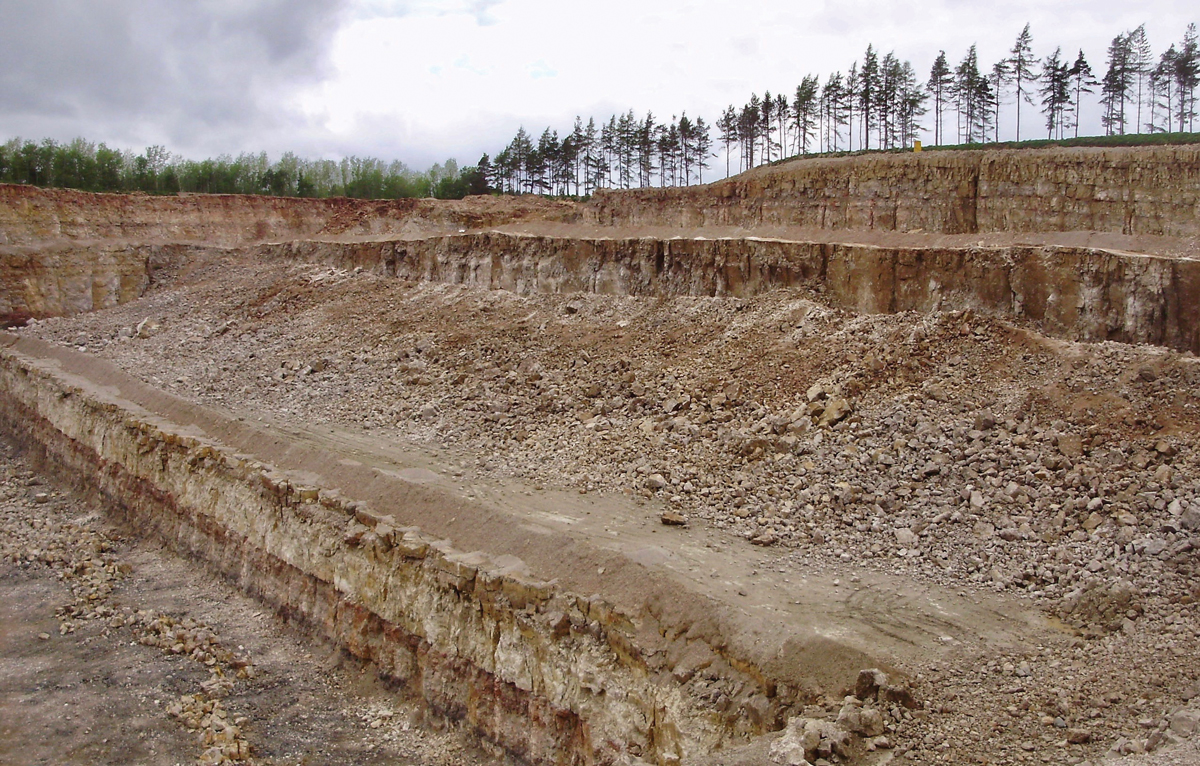
First published in the August 2019 issue of Quarry Management
Robin Gillespie outlines the development and utilization of electronic delay detonators at Shap Quarry
Progress in business is often measured by increased profitability. How that progress comes about can be the result of technological advances, improved operating practices, smarter deployment of resources; the list is endless. But the common theme that flows through these incremental gains is invariably innovation, something in which the mineral extractives and quarrying sector excels.
The Knowledge & Innovation segment of the Institute of Quarrying’s (IQ) Skills Wheel focuses on all areas of site operational issues. The Skills Wheel shows the core skills and areas of knowledge that all employees should aim to develop as part of their commitment to lifelong learning. This development is supported and recognized as part of IQ’s Continuing Professional Development (CPD) programme.
Robin Gillespie FIQ is Hanson UK’s area operations manager for the north of England. He is also the first person in the mineral extractives and quarrying industry to achieve a first-class honours Bachelor of Science in Minerals Management from the University of Derby’s Centre for Mineral Products. Robin’s dissertation investigating the use of electronic delay detonators (EDDs) versus traditional pyrotechnical detonators is now widely acclaimed by Hanson UK for its innovative findings.
Robin says: ‘Advances in the development of explosives engineering have resulted in quite significant improvements in rock fragmentation. The development and utilization of the electronic delay detonator has undoubtedly been at the forefront of the technological breakthrough.’
Robin’s BSc (Hons) research project also explored the potential downstream economic benefits resulting from the use of EDD technology, specifically at Shap Quarry, in Cumbria.
He continues: ‘Emerging technological advances rarely have the opportunity to reduce safety risks and make net manufacturing cost savings. It is also exceptional that something that is smaller than a pencil and costs less than £20 can make such a major difference to a very traditional industry such as quarrying. This technology is the electronic delay detonator.’
James Thorne, IQ’s chief executive officer, says: ‘The continuing professionalization of our industry bodes well for its future. Our partnership with the University of Derby’s Centre for Mineral Products is really raising standards and upskilling individuals, who, in turn, are adding value back into the industry.
‘What’s hugely satisfying is that the take-up on the courses at the university continues to grow. Given the relatively short time since its establishment, this is a true reflection of the hunger for knowledge that is shared across our industry.’
Robin Gillespie is the embodiment of this investment. He continues: ‘The safety and environmental benefits of electronic detonators are well documented; however, the economic argument for the use of this technology is unclear and, as a result, usage in the UK currently stands at just over 50%. The advantages of the EDD far outweigh the non-electronic (Nonel) detonator-based system in every aspect of performance. The fact that the EDD is up to five times more expensive is overcome by the improvement in blast performance. This can be achieved with or without making changes to the blast pattern.
‘We reviewed case studies at a number of quarries around the world and the story is the same; that EDDs, used correctly, improve blast optimization at almost any type of quarry. Blast designs that utilize the precision, accuracy and two-way communication of the EDD can be safer, have improved fragmentation, increased productivity, and reduced energy requirements. In addition, they can produce more stable faces and allow wider blast patterns to be employed, thus reducing cost.’
The northern decline of the third bench at Hanson UK’s Shap Quarry was selected as the test site due to its consistent geology and sufficient reserves for six representative blasting trials. The first trial benchmarked the existing non-electronic initiation system. Five further blasts were carried out; one additional Nonel plus four EDD. The last two EDD blasts had geometrical changes made to the pattern, with the final EDD having the timing shortened.
The same measurements were recorded for each blast, including:
- face excavator fuel bum
- percentage oversize
- percentage undersize
- primary crusher electricity consumption
- primary crusher throughput
- full blast design details.
A detailed review of the study results concluded that the use of EDDs at Shap Quarry offered an improved blasting performance through optimization of the blasting process. EDDs allowed for a wider blast pattern, which delivered a 9.6% saving in drilling and blasting costs. Additionally, the improved fragmentation achieved by using EDDs resulted in a 7.6% reduction in primary electricity costs and a 14.1% reduction in face excavator fuel costs.
Shap Quarry has subsequently transitioned to using EDDs on all production blasts. The project is being watched with great interest by many people within Heidelberg Cement. The results show that improved fragmentation and a reduction in operational costs are achievable through the increased use of EDDs. This will encourage other sites to review their choice of initiation systems and increase the use of this particular type of system.
One of the leading suppliers of heavy building products in the UK, Hanson are committed to developing talent throughout their business to drive innovation and future business growth. Karen Wright, talent and development manager, explains: ‘We provide a number of structured support programmes providing the training and necessary skills for those that aspire to be our future business leaders.
‘Robin is a great example of what other science and engineering graduates could achieve on our graduate management trainee programme. These are in place to attract, develop and retain the talent that Hanson and the quarrying industry need for the future.’
Professor Judith Lamie, Pro Vice-Chancellor, External Affairs, at the University of Derby, said: ‘The University’s Centre for Mineral Products, in partnership with the Institute of Quarrying, delivers industry-standard and globally recognized qualifications to the mineral products sector. We have a long-standing commitment to training and development in the mineral products industry and are extremely proud of our students who qualify in this field.’
Mark Osbaldeston, head of the Centre for Mineral Products at the University of Derby, adds: ‘Robin took the bull by the horns and set about researching his dissertation with a huge amount of vigour. His is an excellent example of how challenging the status quo can really deliver dividends. Just because something has always been done a particular way doesn’t make it untouchable. It’s about challenging things and always finding a better way.’
Robin’s dissertation earned him an impressive 86% score towards his Bachelor of Science in Minerals Management from the University of Derby’s Centre for Mineral Products and played a major part in securing the top grade.
Robin concludes: ‘Lifelong learning is so important for our industry and formal academic qualifications can help you develop both personally and professionally. My studies unlocked the potential cost savings identified in my report. Those findings have already been introduced at Shap and recommended for implementation at Heidelberg Cement quarries around the world, with huge potential annual savings.’
- Subscribe to Quarry Management, the monthly journal for the mineral products industry, to read articles before they appear on Agg-Net.com