Celebrating 10 successful years of the Honours Degree in Mineral Products Management
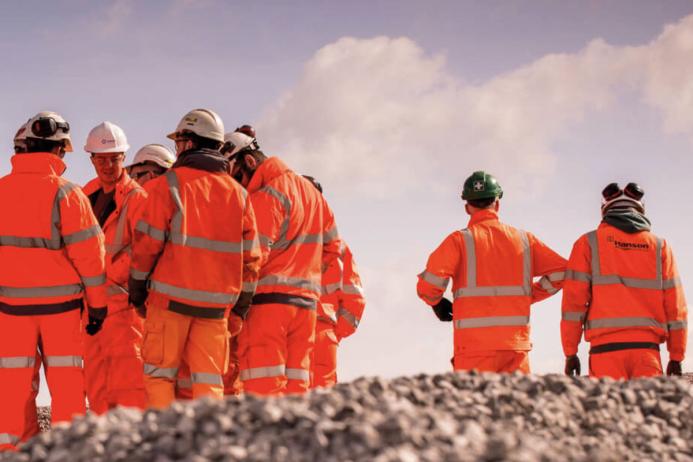
First published in the February 2025 issue of Quarry Management
By John Austin, senior lecturer, Centre for Mineral Products
Developing the skills and competence of the mineral sectors workforce is key to ensuring that the industry continues to innovate, finding solutions to the multi-faceted challenges around sustainability. For 10 years the Centre for Mineral Products (C4MP) at the University of Derby has been delivering industry-relevant qualifications that have become the benchmark for aspiring professionals in providing the valuable underpinning knowledge that supports their career.
The Centre for Mineral Products delivers a range of programmes covering different pathways within the mineral products sector. These are created in conjunction with its industry partners: The Institute of Asphalt Technology, The Concrete Society, The Heavy Clay Technology Association, The Road Surfacing Treatments Association, and The Institute of Quarrying.
Students are distance learners working full time in the minerals products industry. Generally, graduates from five foundation degrees and a higher apprenticeship feed into the two-year BSc Honours in Mineral Products Management. This programme is delivered in partnership with The Institute of Quarrying and is considered to be the pinnacle of the students studies within the Centre.
The honours students study five modules, including a double-credit work-based project. Project topics are chosen by the students and their employers, with guidance from the C4MP team. Projects could focus on a specific area on site or there might, perhaps, be a wider scope regionally or nationally.
For students undertaking the honours programme, it brings many personal and professional development opportunities to set them up for their future career. For employers and the wider minerals products sector, the work-based projects deliver new insights, often directly delivering an immediate financial benefit for the organization. What follows is a summary of the actual impact these projects have made in the real world.
Project 1 – Methods to eliminate deleterious materials leaving quarries – James Forrester TMIQ
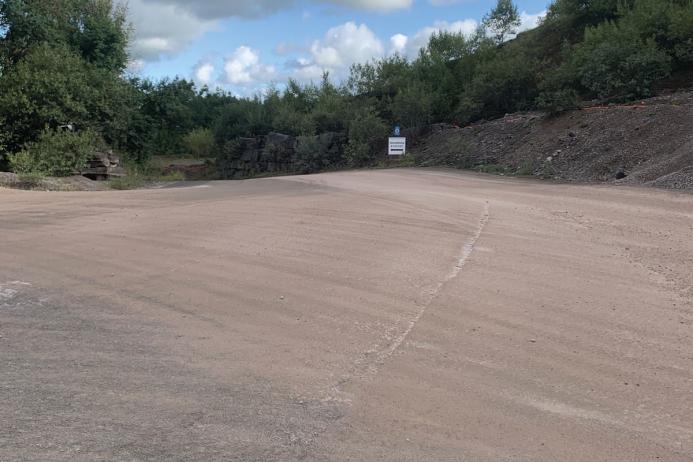
The aim of this project was to investigate and determine the optimum method to minimize deleterious materials leaving site. The project assessed the effectiveness of current wheel-cleaning systems along with other alternative solutions.
Method
The project evaluated differing cleaning solutions such as wheel baths, wheel washes, hire of second wheel wash unit, waterless wheel cleaner, and relocation of the wheel wash unit.
The wheel bath unit quickly became soiled and dirty reducing the effectiveness of the unit over time.
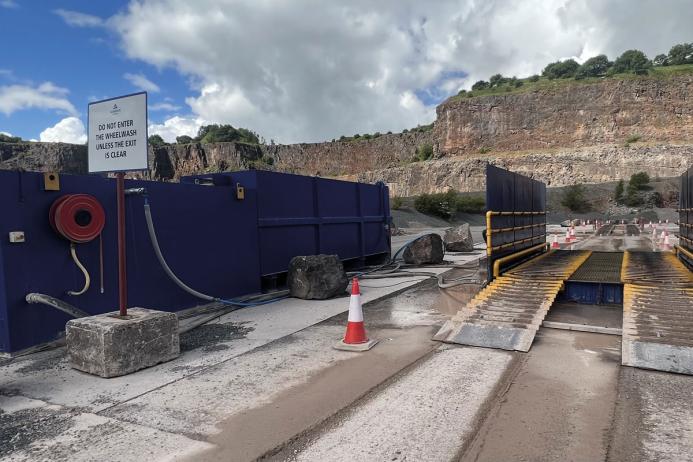
A pressurized spray wheel wash unit, as shown in figure 2, was located 150m away from the site entrance. It generated better results compared with the wheel bath, however, there continued to be some soiling of the roads after the wash.
Additional rumble strips that shake the vehicle to remove the deleterious material were installed before and after the wash. Whilst these were successful in removing some soiling, they failed to eliminate the issue.
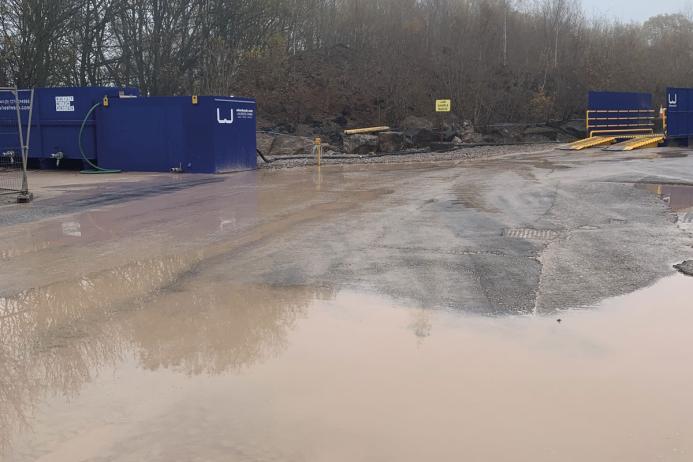
A further wheel wash unit was hired to trial on site, however the location of this wheel wash proved to be unfavourable as the dirty water from the wash collected on the road, as shown in figure 3.
A further waterless wheel cleaner was installed, comprising of rumble strips only. The trial was not a great success, failing to remove sufficient deleterious material.
The final stage of the trial was to move the second wheel wash a further 450m into the quarry, sited on a level concrete pad. This proved to be the most effective solution.
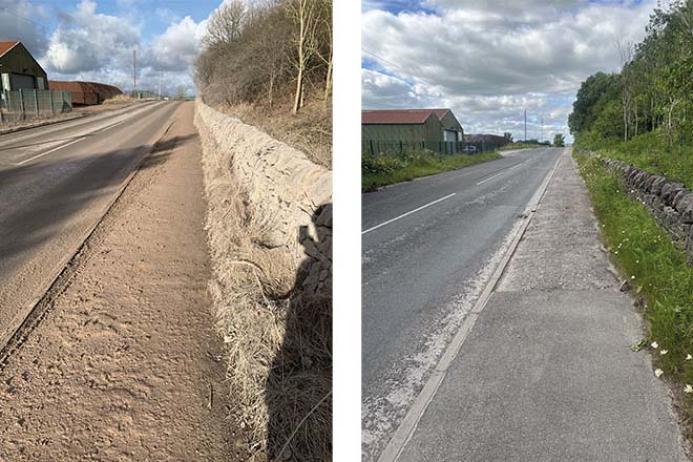
Results
Significant improvements with the site road conditions are clearly visible and there have been positive comments from the local community.
Relocating the wheel-cleaning facilities has not only improved the condition of the public highway, but has also generated financial savings from the reduced hire of the second wheel wash and from a reduction in mains water and road sweeper usage.
James Forrester TMIQ commented: ‘I achieved a great sense of pride and accomplishment in the successful completion of my project, which was part of my degree. It was rewarding to see that my work had a positive impact not only on site, but also with the local community. Researching the topic necessitated thinking outside of the box, which opened my eyes to a varying range of solutions. The skills I have gained through the completion of the project are skills I am now utilizing in my current role.’
Project 2 – An investigation into the use of electronic delay detonators (EDD) vs non-electric detonators (Nonel) – Robin Gillespie FIQ
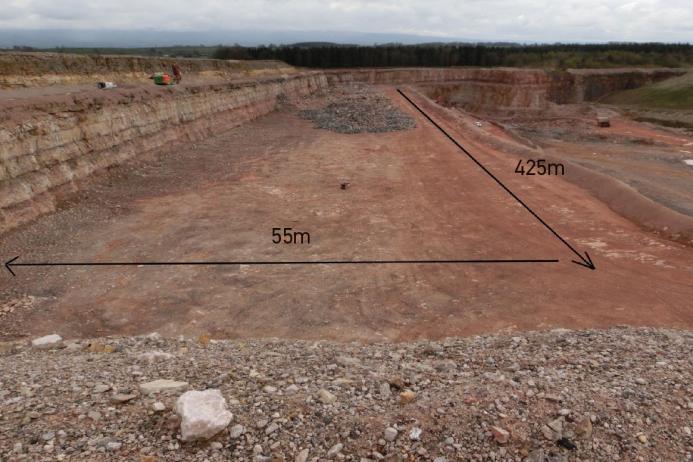
The safety and environmental benefits of electronic detonators are well documented; however, the economic argument for the use of this technology is unclear and, as a result, usage (at the time of this project) in the UK was just over 50%. Usage has increased in subsequent years.
The claimed advantages of the EDD outweigh the Nonel-based system in many aspects of performance. The fact that the EDD can be up to five times more expensive is mitigated by the improvement in blast performance. This can be achieved with or without alterations to the blast pattern.
Blast designs that utilize the precision, accuracy, and two-way communication of the EDD can be safer, have improved fragmentation, increased productivity, and reduced energy requirements. Furthermore, they can produce more stable faces and enable wider blast patterns to be employed, thus reducing cost.
Method
The trial area shown in figure 5, was selected as it had consistent geology and sufficient reserves for six representative blasting trials. The first trial benchmarked the current Nonel initiation system. Five more blasts were then carried out, one additional Nonel plus four EDD blasts. The last two EDD blasts had geometrical changes made to the pattern, with the final EDD also having the timing reduced.
Consistent measurements were recorded for each blast including:
Face excavator fuel usage
Percentage oversize
Percentage undersize
Primary crusher power consumption
Primary crusher throughput
Full blast design details
Results
It was concluded that the use of EDDs offered an improved blasting performance through optimization of the blasting process. EDDs allowed for a wider blast pattern, which delivered a 9.6% saving in drilling and blasting costs. Additionally, the improved fragmentation achieved by using EDDs resulted in a 7.6% reduction in primary power costs, and a 14.1% reduction in face excavator fuel costs.
Transferring to EDD’s would generate a potential annual saving estimated to be £54,800.
Robin Gillespie FIQ commented: ‘Lifelong learning is so important for our industry and formal academic qualifications can help you develop both personally and professionally. Without it I wouldn’t have unlocked the potential cost savings identified in my report. Those findings have already been introduced on site and recommended for implementation internationally with potential annual savings of £750,000.
‘After completing the course my whole outlook on life changed, probably due to the critical thinking skills I acquired. The course opened a whole new world in terms of mineral processing techniques, as opposed to basic crushing and screening.
‘In my opinion, anyone operating at mid/senior management level would benefit from the knowledge and skills provided by completing this course. As an area operations manager you need this level of higher education to successfully comply with the job description.’
Project 3 – A comparison of green concretes in the context of the Circular Economy – Danielle Dawson
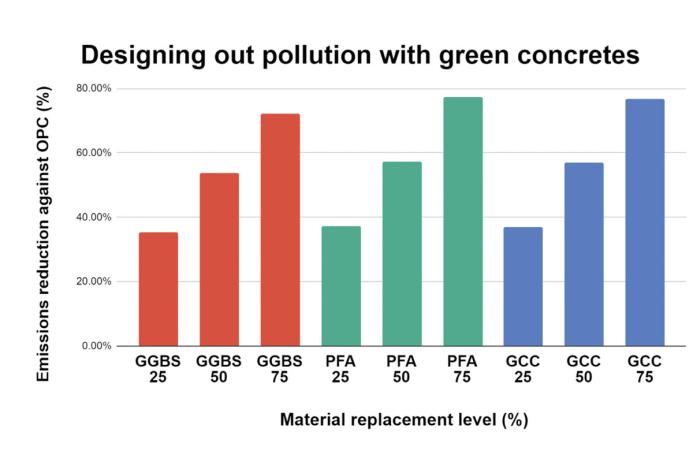
The aim of this project was to increase knowledge and understanding of green concretes in the context of circular economy (CE), and compare various concrete’s durability and carbon intensity.
Method
Concrete cubes were produced in the lab. The mix designs had been based on a wet-pressed kerb mix. Four sets of trial mixes were prepared, one ground granulated blast-furnace slag (ggbs), one pulverised fly ash (PFA), one ground calcium carbonate (GCC) and one ordinary Portland cement (OPC) control mix. There were four further mixes per set with replacement levels of 25%, 50%, and 75%. The control mix provided standard results for ‘normal’ pollution and carbon emissions to compare against the substitutes.
Results
By inputting the trial mixes into the carbon calculation tool, data was gathered on carbon emissions reduction per mix, as shown in figure 6.
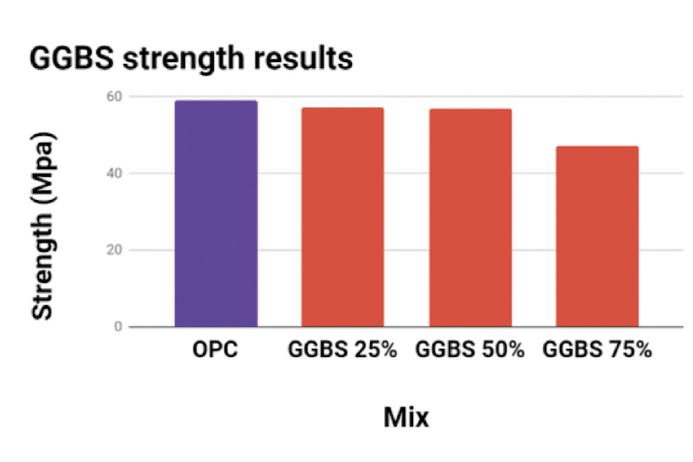
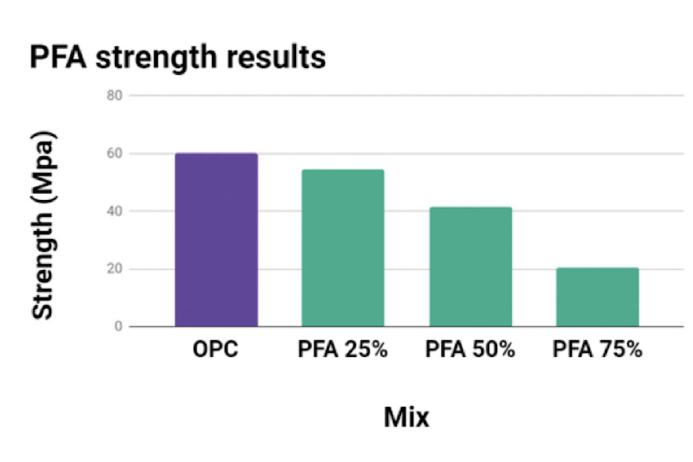
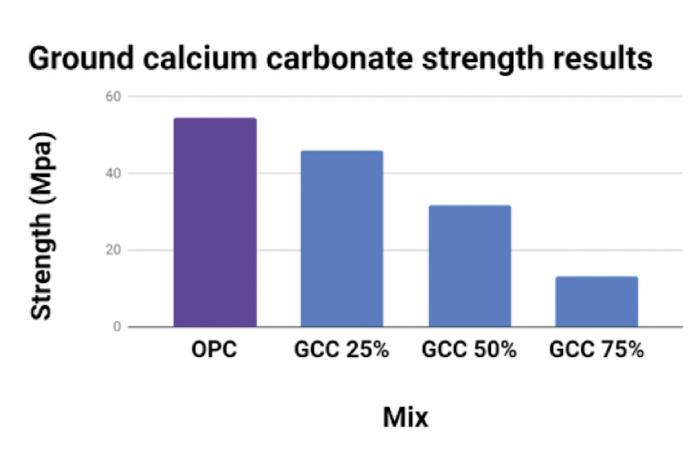
The strength performance of the different trial mixes are shown in figure 7.
Although the ggbs results are very similar to the control OPC mix, these results indicate that its use does not increase the durability of the concrete.
The PFA mixes showed higher strength loss compared with the control OPC mix. High replacement levels would severely decrease the durability of the concrete. This would reduce the lifespan of the concrete and would not fulfil the CE strand of ‘Keeping products and materials in use’.
The use of GCC as a cement replacement in this trial showed significant strength loss against the control OPC mix. This indicates a potentially detrimental impact on durability and performance of the concrete.
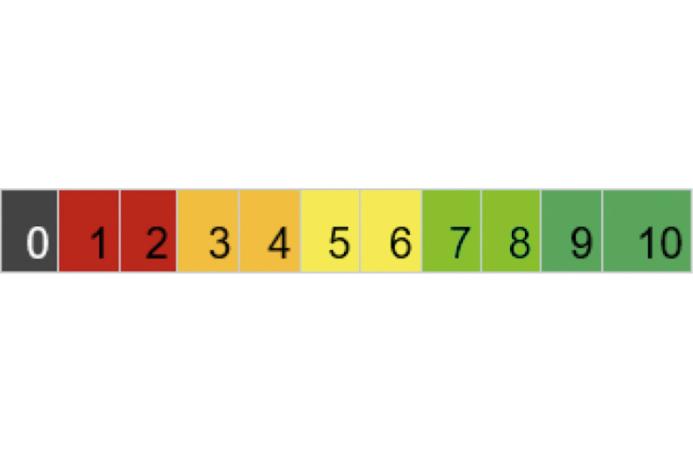
Each cement alternative was scored on how well they meet each circularity indicator, and thus contribute to a circular economy. The scoring system is 0–10, with 0 being the baseline which is in line with current OPC concrete. Higher scores indicate greater circularity, lower scores less circularity. For example, a score of 10 shows that the indicator is completely circular with no flaws; a score of 5 shows that the indicator is an improvement on current methods but it may not be completely circular. Negative values are possible if the alternative is worse than OPC.
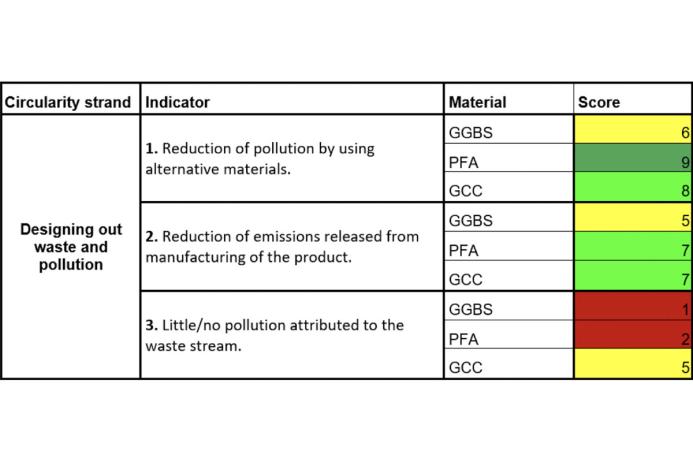
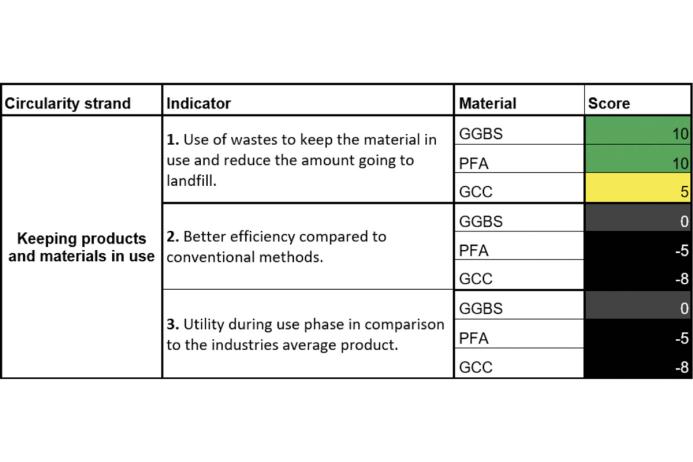
The ‘Designing out waste and pollution’ and ‘Keeping products and materials in use’ areas of CE are predominantly focused on the pollution aspect of CE. Table 1 and Table 2 show the scores given against each indicator, highlighting the differences between the trial mixes.
Comparing green concretes in the context of CE involves thorough understanding of how the wastes are produced, their emissions factors, and their performance in concrete. The most circular of the green concretes is ggbs, followed by PFA and finally GCC. However, the result of this study suggests that even though these materials contain circular credentials, they are far from being considered wholly circular.
Danielle Dawson commented: ‘I’m currently working within the cement division, exploring cutting edge technologies on how we can decarbonize our industry. The BSc has equipped and encouraged me to challenge the industry, making me confident in my knowledge.’
Project 4 – Increasing productivity and minimizing wastage – Ben Campbell TMIQ

The aim of this project was to identify and reduce the production constraints on site, increasing the overall efficiency of the plant. The project focused on the primary impact crusher and was split into two trial phases: first, optimizing the clearance between the rotor and the impact aprons; and secondly, adjusting the composition of the blow bars to prolong use.
Method – phase 1
The settings for the impact aprons would be critical before embarking on the blow bar trials. Figure 9 shows the main adjustable components of the horizontal impact crusher.
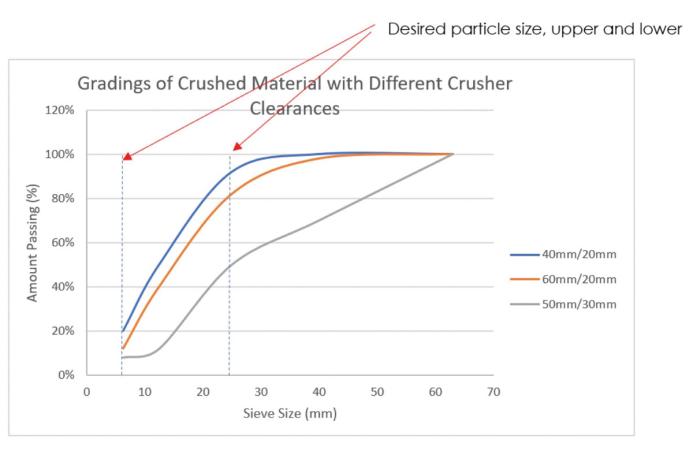
Results – phase 1
The clearances for the impact aprons were derived from research and the impact crusher manufacturer recommendations, with the results shown in figure 10.
From the evidence gathered in this trial, a 40mm/20mm clearance setting produced the most desired products.
Method – phase 2
Differing blow bar compositions were trialled to establish the best performance. It should be noted that the blow bars are changed weekly due to the nature of the material being crushed. Three differing blow bar compositions were selected for the trial: first, the original equipment manufacturer (OEM) high-durability blow bars; secondly, high chromium blow bars; and finally, recycled blow bars created from re-forging pre-used blow bars.
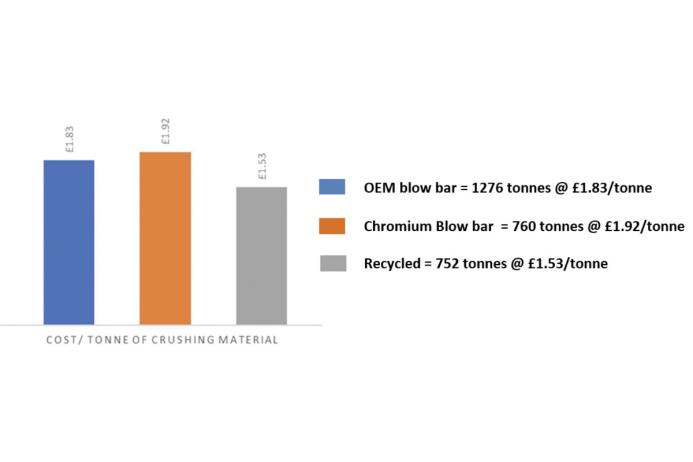
Results – phase 2
The trials proved that the OEM blow bars were most durable, resulting in the lowest overall operating cost. This was due to the potential sales revenue loss associated with the frequency and time changing the recycled blow bars. In conclusion, the OEM blow bars are to be used during periods of high demand and the recycled blow bars during periods of lower demand.
Since the completion of the project further trials have been conducted with the recycled blow bars by addition of further chromium when they are being re-forged. The initial results are proving to be promising.
Ben Campbell TMIQ commented: ‘The degree course really helped me develop independent thinking, especially through the ‘Work-Based Project’ module. This module was great for applying what I learned in real-world settings, pushing me to be creative and self-reliant. The course also provided in-depth knowledge of the mineral products industry and business management, giving me a well-rounded understanding of both specific and broad concepts. Overall, it broadened my perspective on the industry and the business world, boosting my confidence to take on projects and solve problems effectively. I’m looking forward to adding more experience to my knowledge in the years to come.’
Simon Smith FIQ, operations director at Longwater Gravel, said: ‘The BSc (Hons) in Mineral Products Management has allowed Ben and his fellow students to show that they are ‘the very best’. Achieving the qualification requires enthusiasm, commitment, and a lot of hard work, all key attributes for those who will have a role in inspiring, motivating, and leading a successful and sustainable minerals industry.’
Mark Osbaldeston MIQ, head of the Centre for Mineral Products, said: ‘After 10 very successful years, it is pleasing to see that the honours programme has delivered on its initial aims. This programme sets the standard within the sector and continues to invite learners to challenge the norm and question the accepted operating practices of our industry. Congratulations to all passed graduates; here’s to the next 10 years.’
Summary
Since the BSc honours in Mineral Products Management started in 2014, more than 100 learners have now graduated. Currently, there are a further 31 students on the programme. Previous and current work-based projects have contributed to health, safety, environment, technical, and operational performance improvements, with the conservative projected savings from completed projects in the region of £21 million. For further information and application details, contact: mineralproducts@derby.ac.uk
For further details on any of the projects covered within this article, contact: j.austin@derby.ac.uk
Subscribe to Quarry Management, the monthly journal for the mineral products industry, to read articles before they appear on Agg-Net.com