Electronic Delay Detonators
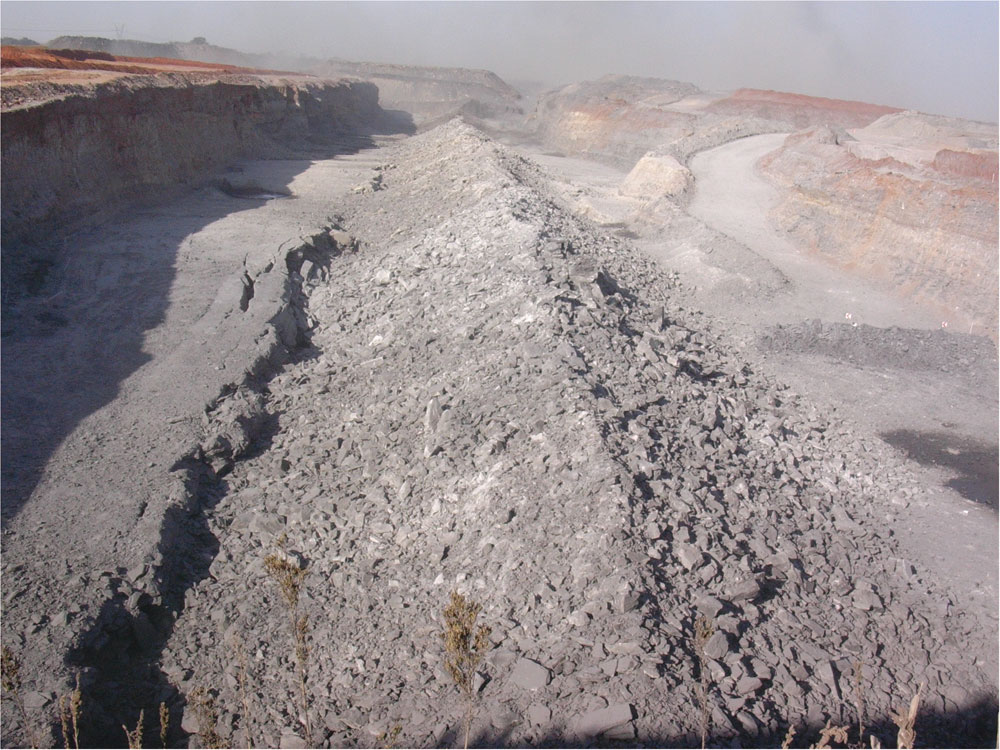
Adding value to rock-breaking operations
By Charles Pretorius, independent blast consultant
In 2008 this article (published here in abbreviated form) won the Institute of Quarrying’s Caernarfon Award, which is presented every third year for the best paper given at an Institute conference, seminar or meeting anywhere in the world, and which is adjudged to have contributed the most to the advancement of some aspect of the industry.
The purpose of this paper is to illustrate in a very simple, non-technical manner how Electronic Delay Detonators (EDDs) can be used to add value to quarrying and mining operations.
EDD systems have been developed over the past 20 years, but it is only during the last 10 years that they have been commercially applied. Recently, there has been a steady increase in the usage of EDDs, not only because the systems available have now reached an acceptable level of reliability, but also because the benefits of using EDDs are now much better understood by the market. Nevertheless, there is still a lot of ignorance in the industry, as well as a lack of understanding of how the full potential of EDDs can be realized; ie how EDDs, through proper blast design and blast planning, can add significant value to various aspects of the operation, improve overall profitability and viability, and even extend the economic life of an operation.
Differences between EDDs and conventional detonators
The main aspects which differentiate an EDD from a conventional pyrotechnic delay detonator are accuracy and programmability.
EDDs typically have an accuracy of between 0.5 and 1.0 milliseconds (ms), which is about 50 times more accurate than pyrotechnic delays. But even with such high accuracy, there is already a need for even greater accuracy.
Typically, EDDs can be programmed with a delay of between 1.0ms and 2,000ms at 1.0ms intervals. The accuracy is normally in the order of about 0.1% of the delay period, but EDDs with a fixed accuracy of about 0.5ms, regardless of the delay period, are also available.
It is these two attributes, ie firing time precision and programmability over a large time range at very short delay intervals (giving the blast engineer literally thousands of delay periods to choose from), which distinguish EDD systems from other initiation systems and which are responsible for the vast and significant benefits obtainable when using EDDs.
During the design of the timing of the EDDs, there are two important aspects to take into account, namely the speed at which the shock wave travels through the rock, and the rock response time (the time it takes for the rock to move and provide burden relief for the next hole firing behind it). In the design of deck charges a third parameter becomes relevant, namely the velocity of detonation (VoD) of the explosives. It goes beyond the scope of this paper to deal with these aspects in detail, but the parameters can easily be determined through field measurements.
The shock wave speed and rock response time are derivatives of the other rock characteristics, such as rock density, rock strength and rock elasticity. These parameters are, therefore, indirectly taken into account. Only EDDs allow effective provision for these parameters in the timing design.
Importance and relevance of accuracy and programmability
The importance and relevance of accuracy and programmability are better understood by considering that the speed at which the shock wave travels through rock, and that of the VOD of explosives, are both in the order of 5,000m/s (15,000ft/s). This is equivalent to 1ms/5m (1ms/15ft).
If two holes or the initiation points of two explosive decks are between 5 and 10m (15–30ft) apart, the time it will take for the shock waves to intersect with the adjacent hole or explosives deck will be in the order of 1 to 2ms. Therefore, in order to have control over the interaction of the shock waves, the minimum requirement is that EDDs must be programmable in steps of 1ms with an accuracy of ±0.5ms as a minimum.
Accuracy and programmability are also necessary to compensate for inaccurate drilling or variations in the burden. How this can be achieved in practice is explained later in the paper.
At this point it is important briefly to consider the accuracy of pyrotechnic delays in comparison with EDDs. A pyrotechnic shock tube (non-electric) system requires a down-hole delay and a surface delay. The surface delay determines the delay between the different firing times of the blastholes, while the down-hole delay ensures that the surface initiation system has progressed far enough ahead of the firing holes to prevent cut-offs and misfires due to fly-rock.
The choice of surface delays will typically be limited to 9ms, 17ms, 25ms, 42ms, 67ms, 84ms, 100ms and 125ms, or something similar.
Typical down-hole delay times are 350ms and 500ms with an accuracy of ±5%, that is ±17.5ms and ±25ms respectively. To ensure that the blastholes fire in the correct sequence, it means that the minimum delay between holes, in case one fires ‘late’ and another fires ‘early’, must be 34ms and 50ms respectively. When stating this, the inaccuracy of the surface delays is not taken into account, nor is enough delay allowed for proper rock movement (burden relief).
To allow for sufficient burden relief in accordance with the rock response times, the delays have to be even bigger. When using pyrotechnic delay elements it is, therefore, not possible to incorporate the dynamics of shock wave interference into the timing design. In other words, it is not possible to make use of benefits achievable when incorporating the interaction of the shock waves into the blast design to have either positive (constructive interference) or negative (destructive interference) waves. In the case of pyrotechnic delays, the delay periods are far too long for the waves to interact in such a manner that improved fragmentation or reduced vibration can be designed into the delay times.
Benefits of using EDDs
Owing to their accuracy and programmability, EDD systems have numerous application benefits which could be utilized to add value to an operation. Some benefits will have an immediate impact on the bottom-line profit, while others will contribute to the long-term viability of the project; these will have to be quantified in terms of a discounted cash flow over the life of the mine or quarry. Because of this, and because the benefits span across different business units, the decision-making must involve middle and senior management who are responsible for the overall profitability of the business.
Safety: EDDs provide certain unique safety benefits. Because all EDDs receive their firing command at the same time, at which time the internal clock of each EDD starts ticking (down the hole), it means that the possibility of the initiation lines being cut off, and misfires as a consequence, is eliminated. Also, because there is a two-way communication with the detonators, the functionality of the detonators can be established before initiation. EDD systems with remote blasting capabilities also make blasting safer. The whole blasting area can be observed from the firing point and the blast can be terminated at any point in time should unsafe blasting conditions be observed.
Environmental impact: Vibration levels, fly-rock and noise are better controlled with precise and programmable firing times. This allows for blasting in close proximity to built-up areas and other structures, which, in turn, could increase the reserves and extend the life of the operation.
Fragmentation: Fragmentation, in terms of average size and size distribution, is more controllable and can be either increased or decreased. The amount of oversize, undersize and unwanted fines can also be reduced. As a result, this has the benefit of better loading rates, crusher throughput, milling rates and ore recovery.
Slope stability: Better control of vibrations and back-break damage allows for increased slope stability. Not only does this reduce the risk of slope failures, it actually allows for steeper slopes, deeper pits, a reduction in the amount of waste rock to be mined and extends the economic life of a mine. Although the financial benefits are not always visible in the short term, the long-term financial benefits could be very significant. It could affect the viability of an operation and should be taken into account by the geotechnical engineers and mine planning engineers during the initial design stage and viability study of the pit. EDDs could be used as a proactive measure.
Selective mining: EDDs make it possible to control the movement of the blasted material. There could be more than one initiation point without the danger of misfires occurring due to initiation lines being cut off. Waste rock and ore can be blasted in separate directions or the movement can be restricted. This supports selective mining and contributes to improved plant productivity, better utilization of ore reserves and better ore quality control; all helping to improve the economic viability of the operation.
Flexibility: The fact that EDDs are programmable allows for flexibility. It allows the timing to be adjusted at any stage to fit the particular circumstances. There can be a lot of variables within a particular blasting block and between blasting blocks, affecting the optimal delay time of each and every hole.
Simplified logistics and lower inventory levels: Because EDDs are programmable there is only one stock item to control. This simplifies the logistics and inventory management significantly; especially for operations with long lead times between order and delivery.
Important and distinguishing aspects
This section provides a brief description of some of the important and distinguishing aspects of the system used in the two case studies presented later.
The EDD system is supported by a blast design software package that is unique to the system.
The blast design process is fully integrated with the actual programming (timing) of the EDDs. The main benefit of such a system is that ‘what you design is what you get’. The whole blast design is optimized on a PC. During this process, all relevant information is taken into account, namely the actual blast geometry and hole positions, the geophysical properties of the blast and surrounding area, and the desired outcome. The program is very practical and easy to use with various levels of sophistication depending on the user’s needs.
It is possible to simulate the blast on the PC to optimize aspects such as:
- fragmentation and size distribution
- vibration levels
- wave interference patterns.
Once satisfied with the blast design, in terms of the delays and the outcome, the delays are digitally transferred from the PC to the detonators in the ground (fig. 2). The whole process is as follows:
- First, the design is done on the PC.
- The timing delays are then exported to a hand-held terminal (a Psion), which is the interface between the PC (office or blast engineer) and the field (shotfirer).
- The timing is then digitally transferred, via the base station, to the actual detonators. The base station is connected to the detonators by means of conventional blasting wire.
- The last step is the actual blasting. This is done remotely, via radio communication, from a safe place (500–2,000m away); ideally from a position where the whole blasting area can be observed. More than one blast can be addressed from the same point during the same blasting period, using one blasting box but multiple base stations.
It is important to note that, during these processes, all the delay timings are digitally transferred. There is no possibility of ‘finger errors’ and, therefore, ‘what you design is what you get’.
Another distinguishing feature of the system is that the identities (IDs) of the EDDs are automatically allocated/determined according to the line number and position of the EDD in the line. It is important, therefore, that the blasthole pattern on the PC matches the actual blast pattern and that the holes on the PC are ‘connected’ in the same sequence that they will be (or have been) connected in the field. This is part of the assurance that ‘what you design is what you get’.
The series connection allows for one-on-one communication and programming; something that is not possible with parallel-connected EDDs. This allows the blaster to ensure that each and every EDD is functioning correctly. In the event of a problem, the exact position of the problem can be identified, eg when an EDD has not been connected to the chain.
The actual hole positions are imported to the PC using surveyed files; normal conventional survey systems or GPS identification can be used. By making use of actual hole positions, the timing can be adjusted to compensate for variations in the burden due to inaccurate drilling, back break or inclined (sloping) free faces. This is also dealt with automatically by the blast design software.
The whole timing design is managed and controlled by the blasting engineer. This can be done on site or remotely. If the site is remote with no blast engineer available on site, the surveyed files can be sent by email to the engineer; he then does the design and returns it by email back to the site. This ensures that each blast can receive the necessary attention in a cost-effective manner.
The system being used is a remote blasting system, which has numerous benefits:
- No blasting lines are required between the point of blasting and the actual blast. This saves time, is convenient and, most importantly, provides for safe blasting practices. This is particularly true when performing blasts in deep open pits with steep benches, where finding a suitable spot from which the blast can be initiated could be difficult. In such cases it often happens that the shotfirer does not have a clear view of the blasting area.
- The EDDs are energized (capacitors are charged) remotely from a safe distance.
- The shotfirer is able to stand at a suitable blasting point from where he can observe the whole blasting area. He then has the ability to visually make sure that the blasting area is safe before he pushes the blast button. He can also stop and cancel the blasting process, including disarming of the EDDs, at any stage right up to the moment before blasting.
The communication protocol prevents incidental initiation; all commands are encrypted and encoded and controlled by passwords to ensure that only commands received via the system from the legitimate shotfirer are recognized and obeyed. All external commands are not recognized and, therefore, accidental incidents due to interference from other sources cannot happen.
Case Study 1 Mobile crusher operation, Mpumalanga Province, South Africa
This is a study of seven blasts that were carried out at a rock-breaking operation where mobile crushers were used. The task of the operation was to crush the required amount of material in the shortest period and most cost-effective manner. The purpose of using EDDs was to provide very fine, fragmented rock to speed up the crushing operation.
In figure 4 the blasting parameters of the first blast are shown; a very quick (5ms) delay timing was used between holes along the rows. The blasting conditions were very difficult due the hardness of the rock, with all joints and planes tending to pre-define the fragmentation. The outcome was very good, as can be seen in figure 6.
The fragmentation achieved during blasts 2 and 3 was slightly disappointing because it was not as good as that achieved during the first blast. After considering different options, it was decided to do top and bottom initiation with two EDDs per hole, initiating the top and bottom EDDs at the same time. The reason for this was to further increase the interaction of the shock waves. By initiating the top and bottom of the explosives column at exactly the same time, the shock waves meet each other between the two initiation points. This is only achievable with the delay accuracy provided by EDDs. The result is considerable interaction of the shock waves within the block, which increases the amount of fractures that the gases then penetrate and open up before being lost to the atmosphere.
The last four blasts were done with a single explosives column, initiated simultaneously at the top and bottom. The results achieved were very good and the customer was highly satisfied (see fig. 7). The required amount of crushed material was produced in a much shorter period than initially planned with a significant improvement in the overall profitability of the operation.
Case Study 2 The world’s biggest EDD blast
A new world record was achieved with this blast in an open-pit strip mine. The size of the blast (775m x 35m), to create a new box cut for a dragline operation, is visible in figure 9. The whole blast was initiated from a central point using a single blasting box. The blasting box communicated, via radio, with seven base stations, each having five blasting lines connected to the blast (fig. 8).
The box cut was situated in mid-burden and there was another bench just above it. It was decided, therefore, to do the entire box cut in one blast (using 370 tonnes of explosives) instead of several smaller blasts. The advantage of this was that production work taking place on the upper bench would only be disrupted once, preventing a considerable amount of downtime.
The challenges of the blast were:
- To ensure that the sandstone layer was properly fragmented and did not end up in big slabs on top of the blasted material.
- To ensure that no damage was done to nearby power lines and a cell phone transmitting tower.
- To ensure that all holes were fired in the right sequence.
The blast consisted of around 1,000 production holes, each containing two explosives decks, and another 1,000 stab holes drilled in between. The production holes were approximately 8m deep, while the stab holes were around 4m deep. The purpose of the stab holes was to ensure enough energy (explosives) in the top layer of sandstone for proper fragmentation of this layer but to still have control over the amount, and direction, of fly-rock.
In total, 3,055 EDDs (two detonators per production hole and one per stab hole) were used for the blast, to ensure accurate firing in the correct sequence. All the EDDs were energized and initiated remotely from the blasting point. The end result was very good and all the criteria were met.
Conclusion
The accuracy and programmability of EDDs, combined (integrated) with the correct supporting blast-design software, allows for a lot of value to be added to an operation:
- Complicated blasts can be done with ease and accuracy.
- Vibrations can be controlled.
- Fragmentation can be controlled.
- The direction and amount of cast can be controlled.
The results are:
- Improved digging and crushing productivity.
- Safer working conditions.
- Extended life of mining and quarrying operations.
- Better ore recovery and beneficiation yields.
The cost of an EDD, when compared directly with the cost of a non-electric or shock-tube detonator, is significantly higher, but as a percentage of the total drilling and blasting costs the difference is not that significant. To justify their usage, the user must make sure that the full benefit EDDs can provide is realized. It is important, therefore, to ensure that the blasts are properly designed. It is also important to ensure that ‘what you design is what you get’. The fact that designs can be conveyed electronically means they can be sent back and forth by email. All operations, therefore, could make use of this technology; it does not matter how small or how remote a site is. A blast engineer is not required on site, and operators can also make use of blast consultants to do the design for them.
With the right system and proper blast design, significant value can be added to an operation.