Advanced Vibration Management
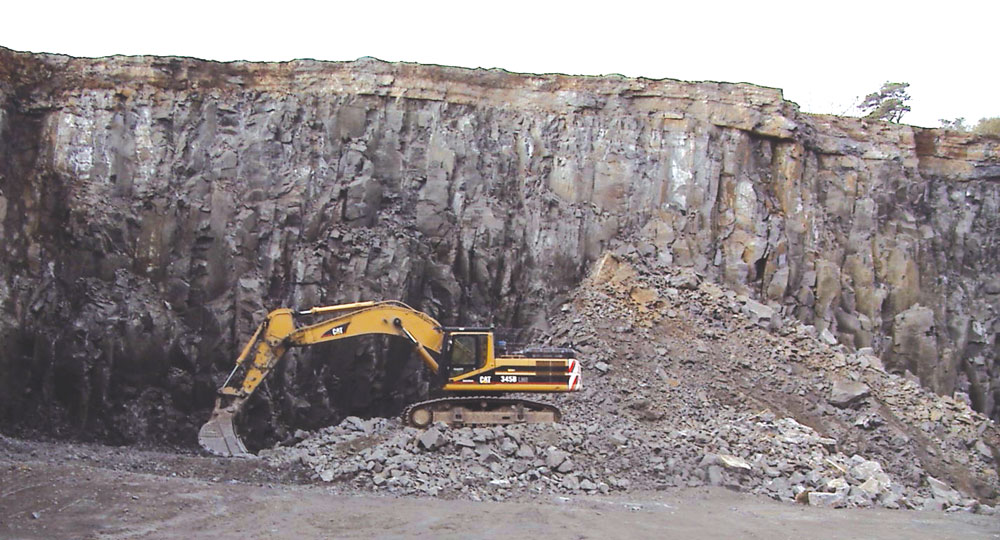
Quarry production blasting in environmentally sensitive locations
By Brian Burke, blast-based services, Orica Mining Services (UK)
Stringent environmental regulatory controls are the accepted norm for many quarrying operations, and complying with these controls while operating at an efficient production level is a major challenge for the industry. The prediction and control of ground vibration and airblast levels are key factors for quarrying operations in meeting this challenge.
As areas of extraction progress towards vibration- and airblast-sensitive structures, the challenge of operating within environmental constraints becomes more difficult. Typically, the charge weight per delay time must be reduced in order to comply with environmental restrictions, which inevitably leads to an increase in production costs as blast performance is adversely affected.
The ability to predict ground vibration and airblast levels directly influences subsequent blast designs and, ultimately, the quarry’s downstream production costs. Increasing the accuracy of predictions allows higher charge weights to be utilized while maintaining environmental compliance.
Charge weight scaling
Traditionally, charge weight scaling laws are used as a basis for predicting blast-induced ground vibration. This involves developing an attenuation relationship between ground vibration and distance. Usually a square root scaling relationship is used, in the form:
v = a(SD)–b
where:
v = ground velocity
SD = scaled distance = distance/?(charge weight)
a & b = site constants
For vibration-sensitive structures (points of interest) located at a constant distance from a blast, scaled distance values increase as charge weights are reduced. As areas of extraction progress toward vibration-sensitive structures, the challenge for quarry operations is to reduce scaled distance values while meeting environmental constraints, ie maintaining high charge weights (thereby maintaining production efficiency) at relatively small distances.
Advanced vibration management
Orica have the capacity, through their Advanced Vibration Management (AVM) service, to measure, analyse and predict blast-induced ground vibrations using a proprietary model for the management and control of vibration at sensitive locations. Utilizing this service, predicted vibration levels can be incorporated to optimize blast designs subject, to maximum allowable ground vibration levels at specific points of interest1&2.
Typically, electronic initiation is used as part of the vibration-management service, as the timing precision and programming flexibility affords results with the most effective vibration-control mechanisms3. The need for this type of service is increasing as urbanization encroaches on quarries, restricting their ability to operate. Vibration restrictions can also limit the mineable assets of quarries. An improvement in blast vibration prediction and control will effectively increase those mineable assets – a valuable outcome in an environment of increasing urban encroachment and sensitivity to blasting operations.
Statistical vibration prediction model
Advanced vibration management is based upon a statistical vibration-prediction model. This model uses a Monte Carlo technique and has been successfully utilized in the Australian mining industry to control vibration and airblast for over 10 years4. The capability of the prediction model has been, and is still being continuously improved on the basis of comprehensive field studies and research work5.
The application of the model – the Monte Carlo engine – requires the definition of a variety of input parameters, as shown in the block diagram in figure 1. The input parameters include the vibration seed shape waveforms from signature blastholes, the single blasthole scaling law, the ground velocity, the delay scatter of the initiation system, the charge weights, the delay time sequence and the geometric layout of the blast pattern with respect to the monitoring site. The model also considers the blasthole screening effect, ie the vibration reduction through fractured rock caused by previously fired blastholes in the initiation sequence.
In simple terms, the model simulates the vibration and/or airblast at a point of interest for a given blast design by the superposition of a sequence of phase-delayed single-blasthole signatures. The prediction output formats include:
- Probability of exceeding a prescribed peak vibration level for a specific compliance location.
- Histogram for the expected peak vibration level for a specific compliance location.
- Predicted time-history envelope for a specific compliance location.
- Mean amplitude spectrum for the expected vibration at a specific compliance location.
Case Study – Howick Quarry vibration-management project
Howick Quarry is located in Northumberland, to the north of Newcastle, and is owned and operated by Tarmac Ltd. All drilling and blasting operations at the site are carried out by Ritchies, the drilling and blasting contractors. The geology of the site consists of a layer of basalt (approximately 15m) sitting on a layer of limestone. A thin, discontinuous deposit of limestone intermittently caps the basalt and is intersected periodically as extraction progresses. The quarry is worked as a single bench in order to extract the basalt (fig. 2).
As the quarry progressed, the area of extraction in the north-west region of the site approached two residences. The environmental planning limit for blast-induced ground vibration at the quarry is 6.0mm/s for 95% of blasts (measured at any residential property). Throughout 2005 the area of extraction progressed closer to residences A and B (as shown in figure 3). The planned extraction of available mineable assets would progress to within 80m of residence B. As the area of extraction approached the residences, the charge weights used were reduced, bringing an associated increase in production costs. In close proximity to the residences, the quarry conservatively limited their blast designs to scaled distance values greater than 40m/?kg, in order to ensure compliance with the vibration limit of 6.0mm/s. Charge weights as low as 3kg were used in 2005. The least squares regression best-fit line for the peak particle velocities measured at the quarry in 2005 is shown in figure 8. The best-fit line is derived from 26 production blasts carried out in the north-west section of the quarry during 2005.
Due to the increased production costs associated with adhering to the environmental vibration limits, the quarry management decided to implement an advanced vibration-management project. The scope of the project was to allow blasting at lower scaled distance values while complying with the vibration limits, and to extract all of the mineable assets in the north-west section of the quarry. The site exploration study for the project was implemented in 20056 and the project’s production blasting phase began in January 2006.
Site investigation study
The initial step in an AVM program must always be a comprehensive site investigation study, as the vibration modelling capability is entirely dependent on the quality of the input parameters for the ground model. The site parameter study has three main objectives:
- to record the single-blasthole seed waveforms, which represent the unique geological site signature between the quarry blasting area and the monitoring locations – the points of interest (POIs)
- to establish the site-specific scaling law for single decks of charge, which describes the expected vibration level as a function of charge weight and distance
- to determine the wave propagation velocity through the ground for the primary wave.
All three objectives can be achieved through the firing of single blastholes. In this case 12 single blastholes were fired for the site parameter study6. After realization of the site investigation and subsequent processing of the recorded data, the site-specific model could be established for each point of interest. With the site-specific model in place, a vibration-control and blast-optimization programme could start.
Production blasting
AVM production blasting involves optimizing the design for a production blast based on simulations of the vibration prediction model. The site-specific parameters, along with the blast design data, are input and a prediction for the vibration levels at each POI is derived from the model.
An example of the blast-optimization process is outlined in figures 4–6. All blast design and vibration modelling is performed using SHOTPlus-i Pro software, Orica’s proprietary blast-design software incorporating the vibration prediction model. The geometric locations of the blastholes, together with the charging details, are shown in figure 4.
These design parameters and the site-specific data are then run through the vibration prediction model. The variability of the input factors according to probability distributions is modelled through Monte Carlo simulation, along with the superposition of seed waveforms, and a predicted output is given for the vibration levels at the POI. Vibration prediction outputs are shown in figures 5 and 6.
Project outcomes
AVM production blasting was carried out at the quarry throughout 2006 and 2007. The improved accuracy of vibration prediction afforded by the vibration-management service allowed blasting to be carried out at lower scaled distance values while complying with the quarry’s environmental limits. The resulting fragmentation from a typical production blast is shown in figure 7. It should be noted that the technical capability to implement the optimized blast designs in situ – as provided at Howick by Ritchies drilling and blasting service – is a fundamental component of the vibration-management service.
The least-squares regression best-fit line for the peak particle velocities measured at the quarry in 2006 and 2007 is shown in figure 8. The best-fit line is derived from 54 AVM production blasts carried out in the north-west section of the quarry during 2006 and 2007. Scaled distance values of less than 40m/?kg were regularly used for the project’s production blasts without exceeding the vibration limit of 6.0mm/s. The lowest scaled distance value used was 24m/?kg.
The maximum instantaneous charge weights per blast utilized ranged from 5kg to 35kg, with an average value of 13.3kg during the project’s production blasts of 2006 and 2007. As shown in figure 9, extraction of the available assets closest to the residences in the north-west section of the quarry has been successfully completed.
Conclusions
The implementation of a vibration-management project at an environmentally constrained quarry has been successful in improving the production efficiency of the blasting operation as extraction progressed towards vibration-sensitive structures. The improved accuracy of vibration prediction has allowed higher charge weights to be used, while production blasts have remained compliant with stringent regulatory ground-vibration limits. The project has also allowed the extraction of the total available volume of mineable assets in close proximity to residential properties. The AVM service has proven to be of benefit to the quarry operation in making optimum economic and design decisions based on the predicted environmental impact at sensitive structures.
During the course of the project, significant work was carried out to determine the effect of various ground disruption zones on transmitted vibration. This work covered a large number of variables including delay sequencing, spatial layout of holes and charge distribution, with the aim of determining the best procedure to reduce ground vibration within a disruption zone7.
Acknowledgements
The support of the quarry management and staff is gratefully acknowledged along with, in particular, Barry Smith (Ritchies), blast supervisor for the project, for his efforts throughout the blasting programme. The drilling and blasting experience and technical input of Ritchies staff throughout the project was vital in ensuring that complex blast designs could be successfully implemented.
The author’s involvement in this project is restricted to the vibration modelling and design of the project’s production blasts since September 2007, together with the regression analysis of the project’s data measurements. All data measurements prior to September 2007 were obtained by Nathan Cotter. Peak particle velocity results at Howick Quarry remain the property of Tarmac Ltd.
The significant work carried out at Howick since 2005 by the author’s colleagues at Orica – Mike Noy, Dirk Grothe, Dane Blair and Nathan Cotter – ensured the success of the Howick AVM project.
REFERENCES
- GROTHE,, D., and M. BREHM: ‘Analyse und Reduktion von Sprengerschütterungen’, Hrsg. Deutscher Sprengverband, Band 28, 2006, Heft 3, pp27-30.
- GROTHE, D., and P. REINDERS: ‘Advanced vibration in quarries using a predictive blast vibration model’, EFEE Conference proceedings, 2007, Vienna.
- BLAIR, D.P., and L.W. Armstrong: ‘The spectral control of ground vibration using electronic delay detonators’, Fragblast - International Journal of Blasting and Fragmentation 3, 1999, pp303-334.
- BLAIR, D.P.: ‘Statistical model for ground vibration and airblast’, Fragblast – International Journal of Blasting and Fragmentation 3, 1999, pp335-364.
- BLAIR, D.P.: ‘Non-linear superposition models of blast vibration’, Int. J. Rock Mech. & Min. Sci., 45, 2008, pp235-247.
- NOY, M.J., and D. GROTHE: ‘Monte Carlo vibration modelling at Howick Quarry, UK’, Orica Internal Report 58743, 2005, pp71.
- NOY, M.J., and D.P. BLAIR: ‘The development and implementation of a new ground vibration-screening algorithm,’ Orica Internal Report (in preparation).