On the Path to Net Zero
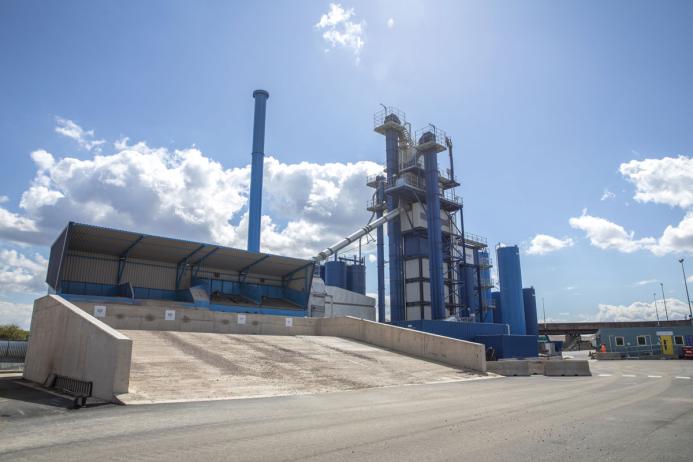
First published in the December 2023 issue of Quarry Management
The impact of climate change and the transition to a zero-carbon society are arguably the most important challenges for our generation. Whilst the construction sector has made significant progress in reducing carbon emissions, there is still an urgent need to do more if the UK is to meets its ambitious net-zero targets by 2050. QM recently visited Tarmac’s Birmingham asphalt plant in Washwood Heath to find out how the site is supporting the acceleration of the company’s journey towards net zero and a more sustainable construction value chain
According to research findings from the Construction Products Association (CPA), the building industry accounts for over 40% of the UK’s greenhouse gas emissions and therefore has a major responsibility to reduce CO2 throughout the construction lifecycle.
For manufacturers, the net-zero transformation is challenging, but it is also a huge opportunity for the construction, minerals, and logistics value chains to make a fundamental change and further drive the industry’s circular economy ambitions.
Parts of the wider UK construction supply chain are already taking a lead in addressing the net-zero challenge and many blue-chip companies, including Tarmac, have accelerated their decarbonization efforts to support the UK’s ambition of net-zero carbon emissions by 2050.
‘Climate change is arguably the biggest environmental challenge of our times, and the construction materials industry must be at the forefront of decarbonizing the built environment,’ said Chris Swan, head of rail at Tarmac.
‘As a dynamic, progressive, and forward-thinking organization, we are fully committed to supporting the UK’s ambition of reducing all greenhouse gas emissions to net zero by 2050. And with net zero becoming an ever-greater priority, we are constantly reviewing how we operate to integrate new technologies, innovations, and solutions to enhance efficiency and decarbonization.’
For the construction sector to deliver for the UK’s net-zero economy, it is essential that the rail freight industry is able to transport aggregates, cement, and other mineral products efficiently, reliably, and sustainably to rail-connected terminals, facilities, and depots throughout the UK.
According to the Mineral Products Association (MPA), quarrying and aggregates firms currently transport up to 20 million tonnes of construction products every year, set against total annual production of around 160 million tonnes of primary aggregate.
The construction and rail freight industries have worked closely together to increase the ability of rail to carry aggregates and building products, but the MPA says there is potential to do even more with the support of the Government, especially given the role of rail freight in reducing carbon emissions and meeting net-zero targets.
‘Moving aggregates and construction materials by rail reduces CO2 emissions by 76% per tonne moved, compared with the equivalent road journey,’ said Mr Swan. ‘Rail freight is, therefore, hugely important for us as a business. We have a corporate responsibility for taking action to combat climate change and shifting towards a carbon-neutral economy. And to help achieve this, we’re continually enhancing our rail capabilities and increasing our capacity to meet customers’ requirements for sustainable construction materials, whilst demonstrating a strong commitment to build a greener, circular future, with the primary aim of becoming a net-zero CO2 company.’
In the West Midlands, the mineral products sector has invested millions of pounds in new rail sites and improvements to its operations, resulting in a 50% increase in rail freight over the past decade and a significant reduction in HGV journeys, road traffic, and carbon emissions.
Tarmac’s Birmingham asphalt plant in Washwood Heath, for example, has been built with sustainability in mind. Opened in April 2021, the site is primarily rail-fed, with aggregates arriving from the company’s Tunstead Quarry in the Peak District and other Tarmac-operated quarries in Leicestershire, mid-Wales, and Derbyshire.
Since its opening, the Birmingham Plant – which also supplies drystone, high-PSV gritstone and ready-mixed concrete – has removed around 20,000 truck journeys a year from UK roads. The trains making this journey also run on hydrotreated vegetable oil (HVO), which forms part of Tarmac’s wider commitment to reducing CO2 from their transport and logistics across their operations.
‘The investment in Washwood Heath is an important part of our rail strategy to bring high-quality construction materials and support the delivery of major infrastructure projects in Birmingham and across the West Midlands,’ commented Mr Swan. ‘Rail freight terminals have been established at strategic locations around the Birmingham area, and we continue to play a lead role in advocating and promoting the use of rail freight in the construction industry as well as advancing innovation and collaborative working.’
For Tarmac, and the other leading players in the quarrying sector, it is vital that these existing sites are protected and allowed to be used to their full potential. They help to reduce road congestion, improve air quality, and minimize CO2 emissions – all contributing to a lower-carbon built environment and driving the Government’s decarbonization agenda.
With more than 60 rail-connected sites nationwide, Tarmac are keen to use more rail freight to move aggregates and manufactured mineral products year on year, and considerable efforts have already been made by the business to switch from road freight to rail and sea.
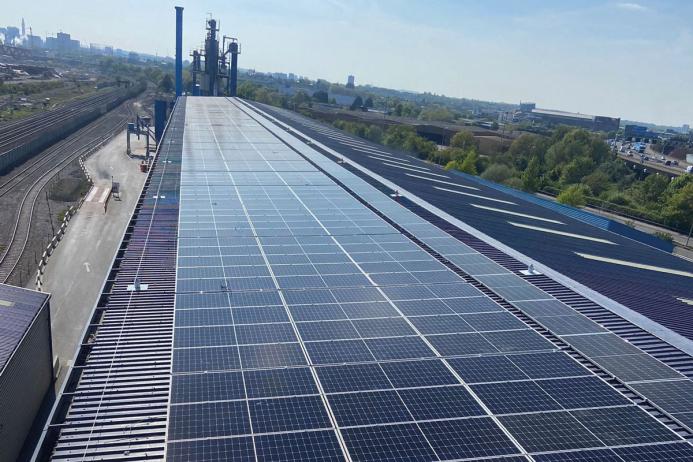
Low-carbon future
Last year, Tarmac installed over 400 solar photovoltaic (PV) panels at their Birmingham asphalt plant, as part of their commitment to meeting net-zero targets. Designed and installed by award-winning solar energy specialists Custom Solar, the solar PV panels generate up to 194,000kWh of renewable energy a year, supplying around 10% of the site’s overall electricity demand.
The Washwood Heath site is the first of Tarmac’s asphalt plants to install solar panels, and the company has been working on designs to roll out the technology at other similar sites across the UK, which will place less demand on the national electricity network and make operations even more sustainable.
The addition of the PV panels is the latest in a series of sustainability measures introduced at Tarmac’s rail-fed Birmingham Plant, which also welcomed the UK’s first battery-electric truckmixer.
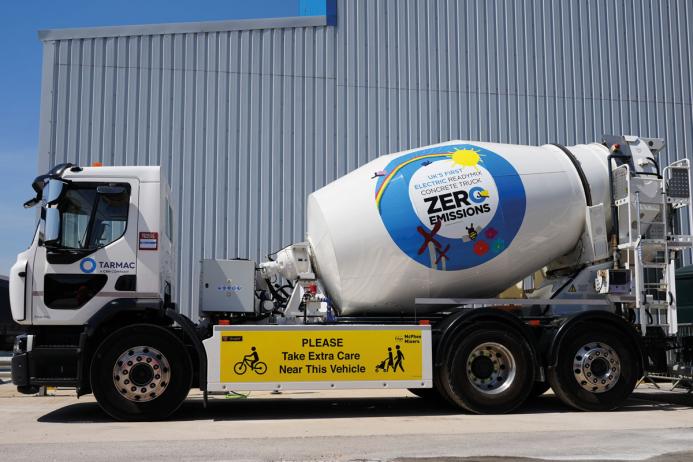
The e-mixer, created in partnership with Renault Trucks and TVS Interfleet, is saving around 42 tonnes of CO2 annually, with zero emissions per mile compared with 1.55kg of CO2 per mile for its fossil fuel equivalent.
Tarmac are committed to helping their customers drive decarbonization across UK building and infrastructure projects, particularly when greener highway construction/maintenance is becoming an ever-greater priority in the transition to net zero. At the company’s flagship Birmingham Plant, Tarmac have been proactively making significant improvements to their aggregate, asphalt, and concrete product portfolio.
The ultimate goal for the business is to save energy in the materials production process and reduce the carbon footprint of roads, by developing more carbon-efficient technology and new specifications that can be adopted across the UK.
‘We are always embracing innovation and making continuous improvements to boost sustainability, efficiency and productivity, not just of Tarmac operations, but the performance of the construction industry as a whole,’ said Brian Kent, Tarmac’s national technical director.
‘The Washwood Heath site is one of 40 asphalt plants across our asset portfolio to adopt warm-mix temperature technology, which has the potential to reduce the embodied carbon of asphalt by up to 15% compared with traditional hot mixes. By reducing the temperatures needed during asphalt production, we can minimize energy consumption and achieve greater reductions in asphalt-related carbon emissions.’
Capable of throughputs up to 300 tonnes/h, Tarmac’s Birmingham Plant is currently using 25-30% recycled asphalt planings (RAP) but has the potential to increase this to up to 40% in the future. The site is also moving towards producing rubber-modified asphalt from shredded tyres, which will see up to 750 tyres recycled per kilometre of new road.
‘Being a more sustainable industry means having efficient and effective operating processes, minimizing waste and recycling more, finding innovative product-led solutions, and taking proactive steps in enhancing biodiversity,’ commented Mr Kent.
From generating its own energy with solar photovoltaic panels, to transitioning mobile plant/vehicles to electric, to removing 20,000 truck journeys a year from the roads, the rail-fed Birmingham Plant has clearly demonstrated Tarmac’s impeccable environmental credentials as the business rises to the challenge of addressing climate change and helping to create a low-carbon economy of the future.
Subscribe to Quarry Management, the monthly journal for the mineral products industry, to read articles before they appear on Agg-Net.com