Net zero plant and logistics – the opportunities uncovered
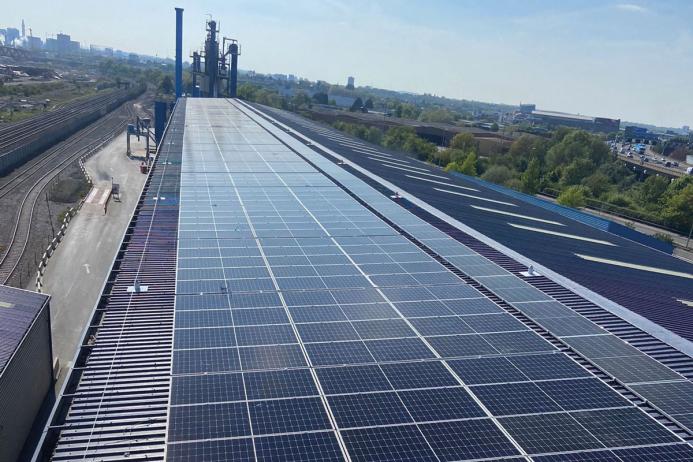
First published in the July 2024 issue of Quarry Management
Ben Garner, low-carbon logistics lead, Tarmac
When thinking about the journey to net-zero highways construction in the UK, many people’s first thoughts are focused on the opportunities to cut carbon in manufacturing and materials processes. While of course this is paramount, industrial infrastructure and logistics must also decarbonize as much as possible to meet the targets.
With transport accounting for around a quarter of the UK’s emissions, achieving net zero requires new technologies and infrastructure. We need to take a complete view of the journey of plant and logistics – decarbonizing how the industry moves its materials will be key.
Here are some of the opportunities that we are uncovering at Tarmac, and how they are already making an impact.
More efficient asphalt plants
With a focus on ways to decarbonize our materials, our Birmingham plant at Washwood Heath was built with sustainability in mind. The production of asphalt is fundamental to the highways industry and ongoing work is needed at this stage in the process to meet net-zero targets.
Opened in 2021, the site is primarily rail-fed, and was the first of our asphalt plants to install solar photovoltaic (PV) panels.
Maximizing the rail network helps to reduce road congestion, improve air quality, and minimize CO2 emissions, reducing CO2 emissions by up to 76% compared with road transport. Using low-carbon fuels such as hydrotreated vegetable oil (HVO) for rail has also been shown to reduce a train’s carbon emissions by up to 90% compared with traditional red diesel.
More than 400 PV panels are supplying around 10% of the site’s electricity demand. We are now working to roll out this technology at other similar sites across the UK to place less demand on the national electricity network, as well as to make operations even more sustainable.
The development of the UK’s first all-electric concrete mixer was also successfully rolled out for use at the Washwood Heath plant. This reduces up to 42 tonnes of CO2 annually with zero emissions at tailpipe per mile, compared with 1.55kg of CO2 per mile for its fossil fuel equivalent.
Tackling the last mile
There has already been a lot of progress made to tackle last-mile logistics due to rapidly changing policy requiring logistics teams to stay ahead of the curve. One emerging policy is low- and ultra-low emissions zones (ULEZs). Today, 30% of the UK population live in a town or a city with a low- or zero-emission zone.
Against this backdrop, last-mile logistics has started to evolve through schemes such as EV100, encouraging organizations to transition 100% of their fleet to electric vehicles (EVs).
Learnings from development of the e-mixer, such as lightweighting and fuel efficiency measures alongside a digital operating system, can also be applied to diesel vehicles. This opportunity is already in development and could help to reduce carbon in internal combustion engines as part of the ongoing transition to electric.
We also see alternative fuels such as HVO or other biodiesels as an essential part of the move to net zero. These are transitional fuels that have the potential to improve our carbon footprint today while we work to make zero-emission solutions viable at scale. They have a big part to play, provided they are responsibly sourced.
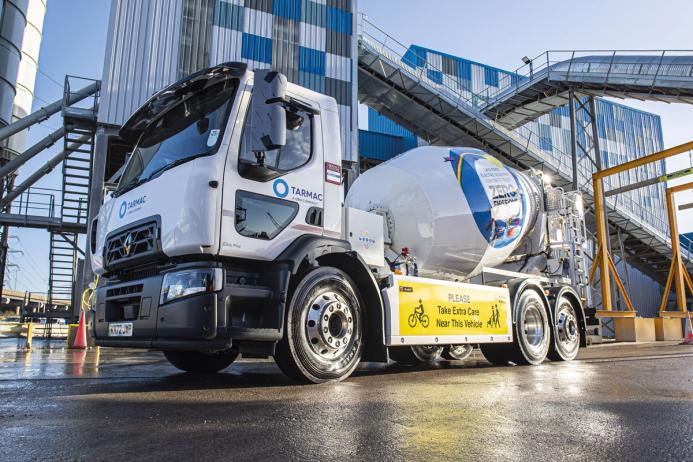
Investment in wider logistics infrastructure
It is now well understood that meeting net zero will require the electrification of society, but a big challenge lies ahead in establishing the infrastructure to support it. Investment and planning will be needed to expand the UK’s EV charging and hydrogen networks, the generation and transportation of which will power heavier road and plant vehicles as we transition to net zero.
In the coming years we will also need to consider the impact of increased battery weight on the carrying capacity of large goods vehicles. The EU is already looking to increase the maximum permissible weights and axle weights on certain battery-electric large goods vehicles to maintain current vehicle payloads, and this is currently under review in the UK. Without these changes we will see more large goods vehicles on the road and greater logistics costs. Therefore, the impact of both scenarios on the road network – more trucks or heavier trucks – will need to be considered.
Encouraging behavioural change
Beyond the long-term net-zero changes, there are opportunities to deliver behavioural change in the short term to cut carbon emissions on a daily basis.
For example, smart telematics systems on vehicles encourage more energy-efficient driving. Data to highlight rapid acceleration, heavy breaking, and idling engines could reduce fuel consumption by up to 10% as we train drivers to become more carbon conscious.
There remain big challenges ahead to ensure our industry meets net-zero targets, but logistics teams are building from a strong foundation of technological and behavioural changes. What is needed now is to scale-up delivery and establish an integrated low-carbon logistics model to meet the needs of highways.
Subscribe to Quarry Management, the monthly journal for the mineral products industry, to read articles before they appear on Agg-Net.com