Wind Of Change
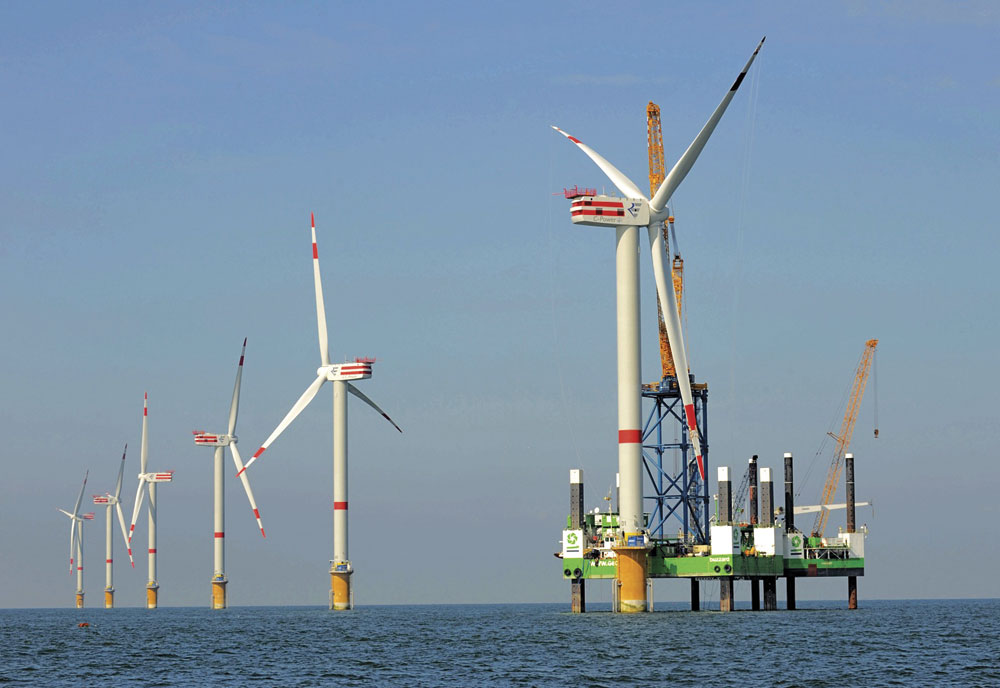
The supply of submarine concrete for the offshore wind sector calls for early engagement and heavyweight answers, say Tarmac
Early involvement and good access to developers will be essential to help concrete providers tackle the UK offshore wind sector’s engineering challenges.
The findings of the UK Energy Research Centre’s ‘Cost of offshore wind in UK waters’ highlighted the gaps in the UK’s offshore wind energy supply chain. It revealed an over-reliance on overseas products and services that threatens to increase the capital costs of UK offshore wind farms to more than £3 million per megawatt.
Turbine foundations represent a quarter of all project delivery costs. As part of Round 3 Offshore Wind projects, the UK is expected to install around 8,000 offshore wind turbines during the next decade and it is estimated that some 2,700 turbines will require foundations at depths greater than 45m. While construction of these projects will not start until around 2014, it is critical that the evolving UK industry starts to understand how it can construct and transport foundations while driving down costs, prioritizing safety and ensuring installation and maintenance is made easier.
A number of industry commentators suggest that steel monopile foundations will fail to meet the requirements of Round 3 due to the fact that they will need to support larger and heavier turbines that are located in deeper water than previously developed sites. Concrete foundations are considered to offer a solution because they can provide a design life of more than 50 years with minimal maintenance.
Some tier-one contractors have already pledged a commitment to concrete gravity base foundations which would be precast and mass-produced in large-scale port-side facilities. Concrete gravity bases offer a solution to the challenges of deep-water installations because they require minimum seabed preparation. This technology would also allow the foundation to be refloated following decommissioning so that no material is left on the seabed.
‘With technology continually evolving, it doesn’t make sense for contractors to focus on specifying costly, ‘groundbreaking’ new concrete mixes for offshore wind foundations designed to last centuries,’ said Jim Troy, director of concrete & mortar technologies at Tarmac. ‘Offshore wind turbines designed and installed in 2014 will have been technologically leapfrogged by the time it comes to replacing them, and retrofitting the existing foundations to keep up with the new turbine designs will be a difficult and expensive process.
‘Instead, contractors should utilize existing proven concretes that have already been developed for challenging marine environments. For those concerned about longevity, the durability of such concretes means that they are able to withstand harsh underwater conditions and will perform well as a foundation beyond the lifetime of the wind turbine – which usually requires replacement after a period of 25 years. Some of the offshore oil and gas platforms have had their concrete bases in place since the 1970s and have not experienced any problems.’
Transporting heavy concrete foundations out to sea and manoeuvring them into position on the seabed is a big challenge for developers, but many Round 3 teams are already devising innovative logistical solutions to combat this. Mr Troy stresses that ensuring the security of supply of concrete should be the next important consideration for developers. ‘Contractors will need to work very closely with concrete suppliers early to plan logistics in detail and guarantee a steady supply of high-quality concrete,’ he said.
According to Geoff Fawkes from Tarmac’s national accounts team, concrete suppliers must be engaged early and firmly embedded in the supply chain because they can also add value to design decisions and proposed construction methods. ‘There are two viable options for constructing concrete foundations. You either opt for an in-situ concrete pour or manufacture precast units in port-side facilities,’ he said. ‘While the latter is currently being favoured, co-ordinating a continuous supply of concrete for a single foundation weighing around 6,000 tonnes will require meticulous planning over a two- to three-year lead time given the number of turbines that are planned to be installed as part of Round 3 offshore wind farms.
Mr Fawkes added: ‘Setting up a network of port-side facilities is acknowledged as key to the success of delivering Round 3, and gaining the planning consents necessary for large-scale concrete plants will be a big element of this. However, providing security of supply goes beyond building state-of-the-art facilities. Concrete suppliers need sufficient time to look at the logistics of sustainable aggregate and cement reserves as well as time to liaise with their own supply chain partners, such as admixture providers and other engineering and property requirements, as well as plant and equipment manufacturers.
‘Contractors have, for many years, ‘banged the drum’ for early involvement, but to deliver the scale of Round 3 projects there is a real need for concrete suppliers to have a place around the table in discussions with the contractor, the operator/client and the designer,’ he said.
‘With the complexity of these projects, contractors must accept that concrete cannot be seen as a commodity product and ensuring security of supply is an essential element of the overall project that will require careful planning. As suppliers, we also have a duty to provide solutions that can cut costs and optimize installation flexibility by working with the client and the turbine suppliers.’