Piles Of Concrete
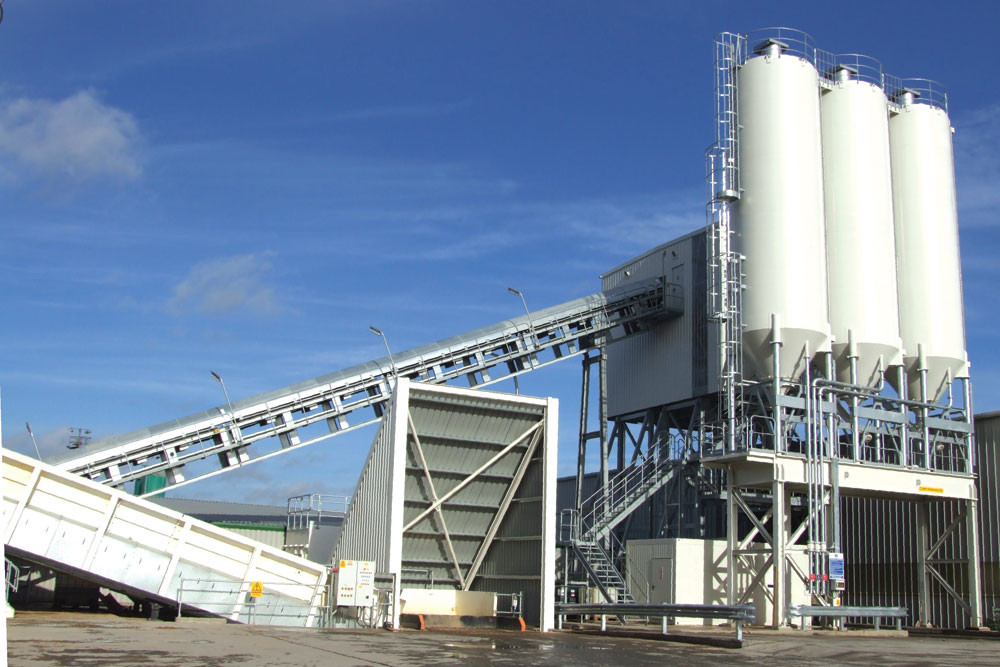
Precast concrete production plant represents a first in UK for Liebherr
The first mixing plant to be supplied by Liebherr for use in precast concrete production in the UK is currently providing CEMEX with a dedicated and virtually continuous chute-fed output for their long-term customer Centrum Pile Ltd.
The twin Betomix 2.25 mixing plant, which has been modified to both Centrum’s and CEMEX’s specific requirements, and includes a number of other special features, was fast-tracked throughout the planning, design, construction, installation and commissioning processes, allowing it to come into production just over four months from placement of the order.
CEMEX have supplied concrete to Centrum Pile for around 15 years and, at the Centrum site near Newark, in Nottinghamshire, the company has been providing around 150m3 on a daily basis to the reinforced concrete pile production facilities adjacent to CEMEX’s batching plant, which is located on the Centrum complex.
An increase in concrete volumes required by Centrum, combined with the completion of their brand new state-of-the-art automated production system, meant that CEMEX needed to source a larger and more productive mixing plant for the site.
Having enjoyed a successful business relationship with Liebherr over several years, it was a natural progression of this partnership that led CEMEX to turn to Liebherr once again for this latest solution to their needs. In turn, Centrum’s own specific requirements also had to be taken on board at the same time.
A visit to a Centrum complex in Denmark, where a similar operation was in place, showed the project engineering team exactly what was required to batch and deliver self-levelling concrete, via a chute system, directly into the feed hopper for Centrum’s automated pile production facilities.
Following the Danish site visit, detailed discussions with Liebherr’s technical personnel resulted in the design for the new plant, based on a twin Betomix 2.25 mixing plant with numerous bespoke adaptations specific to CEMEX and Centrum requirements.
The new plant is linked to the existing aggregate storage bins on the original concrete plant, with a new ground-level aggregate receiving hopper with a 2m wide inclined belt feeding a 140m3/h capacity totally enclosed bucket-type elevator.
In addition, an 8m long x 650mm wide cross conveyor has been installed to feed the existing tripper conveyor on top of the aggregate storage hoppers, while a 26m long x 800mm wide inclined chevron belt conveyor supplies the mixing plant, where a holding hopper with diverter delivers the correct aggregate volumes into the tandem Liebherr 2.25 ring pan mixers, including one agitator, which form the heart of the Betomix batching plant.
The mixing tower also features a 1,500kg capacity cement weigh hopper, a 750kg water weigh hopper and a high-pressure wash system for each of the pan mixers. The plant can be supplied with either reclaimed water from a 42,000-litre capacity agitated tank or fresh water from a 30,000-litre capacity tank. An admixture weighing device and associated pumps introduce required addictives from three bunded storage containers.
All aggregates and cements used by the plant are provided from CEMEX’s own resources and transported to the site in the company’s fleet of aggregate tipper trucks and specialist cement vehicles. Cement is held in three 100-tonne capacity silos, each one equipped with a screw conveyor for delivering the cement to the mixing tower weigh hopper.
The entire batching plant is located adjacent to Centrum Pile’s new production hall and has been raised above normal height on specially designed and constructed legs in order to achieve the required level for feeding the precast pile production plant hopper.
The concrete is delivered via an inclined chute, through an aperture in the production hall wall, directly into the receiving hopper, which, in turn, fills the pile moulds, complete with reinforcement cages, which pass beneath the hopper on a reversible conveying system.
The concrete delivery chute is retractable for cleaning purposes, while an on-site laboratory conducts regular testing to ensure mix design consistency and optimum quality control. An additional twin-chute configuration is linked to the truckmixer feed chute beneath the plant so that truck-delivered ready-mixed concrete can also be produced if required.
Controls for the plant presented Liebherr’s engineers and their IT specialists with some interesting challenges. Liebherr’s own sophisticated MPS II Litronic control system ensures correct batching and a Ginco interface control was installed to allow the system to ‘talk’ to the Centrum production hall’s own computer system.
The resulting ‘dialogue’ between the two systems, in conjunction with level sensors in the feed hopper, ensures that batched concrete can be called for as and when required, so that the correct feed is continuous and uninterrupted during the precast reinforced pile production process.
Commenting on the new plant, CEMEX’s engineering manager, Anthony Groom, said Liebherr’s specialist knowledge was invaluable in helping to develop the plant. ‘The modular yet versatile construction of the Betomix plant allowed us to stick to the very tight manufacturing schedule, in spite of the numerous modifications from standard required to accommodate the demands of....Centrum Pile Ltd,’ he said.
Liebherr, for their part, conducted the entire project on a turnkey basis from design through to commissioning, including all civil engineering works as well as the water system, compressed air systems and electrical installation work.
For further information, contact Liebherr-Great Britain Ltd on tel: (01767) 602100; email: info.lgb@liebherr.com