High-grade Concrete Mixing
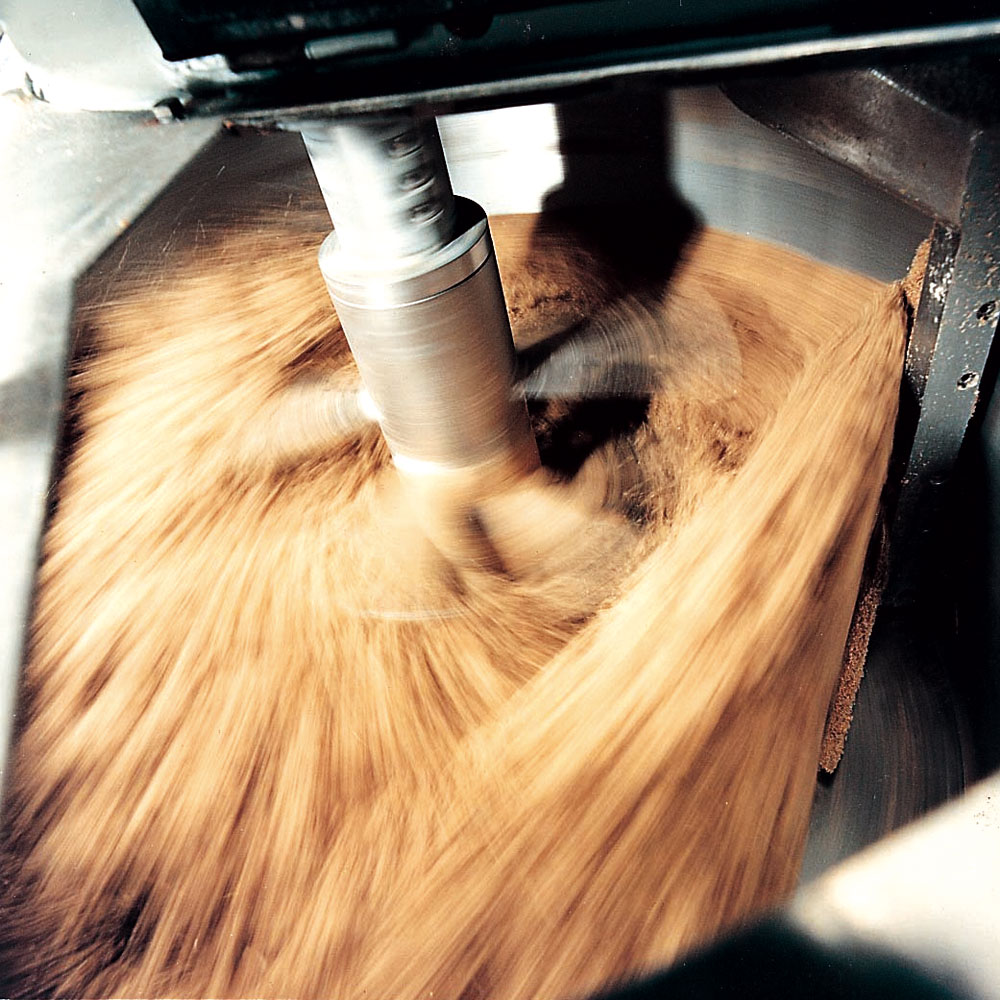
Ensuring a high specific input of energy into the mix
Concrete has been in use as a mass building material comprising just cement, aggregates and water for a very long time. During the last 20 to 30 years, however, the development and use of high-performance speciality concretes has taken place alongside the continued use of mass concrete. These newer concretes may contain up to six types of component; the established and essential three plus other solid and liquid additives and air. A great deal of research and development in technical institutions and universities throughout the world has been carried out. Nevertheless, it appears that no objective rules have yet been specified and adopted concerning the process of mixing concrete; it remains something of an art, ie concretes, even high-grade materials, are still mixed according to ‘feel’.
In spite of the lack of objective guidelines or standards in concrete mixing, a consensus that a high specific input of energy into the mix is a crucial factor, particularly in the production of high-grade concrete, has arisen among researchers. The mixing of concrete may now be defined, therefore, as the achieving of a homogeneous distribution of all components by the introduction of energy into the mix.
It is recognized that the satisfactory preparation of speciality and ultra-high-performance concretes is much more difficult than the preparation of mass concrete and demands, among other things, a particularly high specific energy input. Gustav Eirich of Hardheim, Germany, claim that their mixers have led the field in this respect for a considerable time. Therefore, some time ago the company decided to concentrate its development programme on mixers and procedures adapted to the production of the newer materials. Table 1 shows the specific power input figures applicable to the types of mixer commonly used in concrete mixing. The value achieved by the current models of Eirich mixer is 3.75kW/100kg of hardened concrete.
Eirich still sell their well-known D-type countercurrent, intensive, horizontal, rotating pan mixers to long-established customers who wish to continue with the same type of machine for maintenance and spares reasons. These mixers are available in sizes up to a nominal batch capacity of 8,000kg and may be equipped with two rotating plough systems, an additional high-energy multi-level rotor and side-wall scrapers.
The R-series of inclined, rotating pan mixers, on which Eirich have for some time concentrated their development programme, includes machines of up to 11,200kg nominal batch capacity. This type of mixer is of simpler design than the horizontal pan machine, being fitted with a single eccentrically mounted, separately driven, multi-level mixing rotor and a fixed wall and pan-bottom scraper, which continuously directs the mix to the centre of the pan. In both types the base of the mixing pan is completely swept during each revolution and both types can achieve the high specific energy input figure indicated above. The result, say Eirich, is that high-quality mixes with uniform component distribution can be achieved within relatively short batch times.
The inclined pan mixer, it is claimed, offers several advantages, the first being that applied energy is transferred into the mix more efficiently, because mixing is partially achieved by the action of gravity as a result of the tumbling action induced by the pan’s rotation. Experience has also shown that pan wear is reduced by comparison with other types of mixer.
An additional, very valuable feature is that the mixing rotor and pan drives are completely decoupled; this allows the speed of the rotor to be varied independently of pan speed within a range of peripheral speeds between 2m/s and 40m/s, and also allows the rotor to be rotated either in the opposite or in the same direction as the pan. This facility is very important in that it allows the machine to be used for multi-stage mixing. The need for this arises when, for example, a relatively fragile, lightweight aggregate or fibre has to be incorporated into a very fine-grained mix. The latter is very difficult to mix satisfactorily and requires an exceptionally high rotor speed and specific energy input. The lightweight aggregate or fibres would, of course, be disintegrated by such vigorous action. The variable-speed rotor, however, allows the machine to achieve the difficult mix and then to gently incorporate the other components of the batch.
The versatility of the R-type mixer and its high specific energy input allow it to be used for facing concretes, in which pigments need to be uniformly dispersed, and which are used in relatively small volumes to enrobe blocks made of lower-grade, less-expensive concrete. The R-type machine is also widely used for the preparation of high-grade and speciality mixes, such as ultra-high-strength concretes, foamed concrete, self-compacting concrete, and railway sleeper concrete. In the case of aerated concretes the air content frequently needs to be adjusted in the final stage of the mixing process. This is achievable with several models of the R-type mixer, which have been adapted to work under vacuum.
Orthos (Engineering) Ltd, No. 2 The Point Business Park, Market Harborough, Leics LE16 7QU; tel: (01858) 464246; fax: (01858) 434480; email: sales@orthos.uk.com