Ensuring Concrete Quality
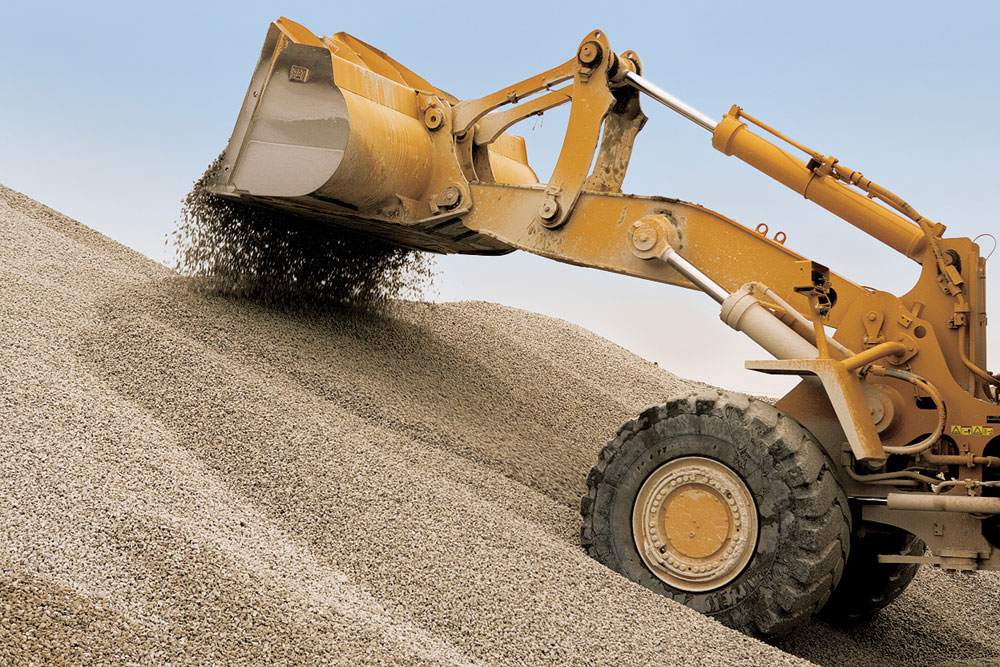
When supplying major construction projects, it is essential that thorough and accurate concrete testing is carried out to meet client requirements and ensure safety, explains John Sutton, group marketing manager at ELE International
With a wide variety of quarried materials used as aggregates in concrete, a combination of properties can be achieved to meet the requirements of a specific application. To ensure that the mix meets these specifications, in addition to testing the aggregate for properties including particle size, shape and texture, density, and chemical resistance, it is vital that the concrete incorporating the aggregate is tested thoroughly and accurately. The latest generation of sample testing technology is allowing concrete to be tested considerably more efficiently and reliably than has previously been possible, helping to realize sound structures, improve long-term safety and reduce costs.
Testing aggregates
Before aggregate is supplied for use in a concrete mix, it should be tested to determine whether it offers the necessary properties. The qualities crucial for one type of application may be unsuitable for another, so the tests required will vary depending on what the concrete is to be used for.
Specific sampling techniques and procedures are documented in various standards, including BS 812: Part 101 and ASTM D75. In general, however, the aim is to obtain samples that are representative of the average quality and then use either riffling or quartering techniques to reduce a bulk sample to a size suitable for testing. Riffling is typically used to reduce material in a dry condition, while quartering can be used to reduce damp material down to a quantity able to be subsequently dried and riffled. In this process, a sample is flattened, divided into quarters, and two opposite sections discarded. The remainder is then remixed and quartered again, and the procedure repeated until a sample of the required size is obtained.
It is often necessary to determine the particle size, shape and texture of an aggregate. This is done primarily by observation and the use of sieves and shakers. An aggregate may be rounded (water worn or shaped by attrition), irregular (either naturally irregular or partly shaped), angular (well defined), flaky (with a small thickness in relation to its other dimensions), or elongated (with a length larger than its other dimensions). Likewise, a sample may be categorized as glassy, smooth, granular, rough, crystalline, or honeycombed.
In addition to size, shape and texture, the density of an aggregate may also be measured. Particle density in mg/m3 can be determined using a number of methods, which are specified in the relevant testing standards, depending on the type and size of the material to be tested. A common method of testing density is by using a buoyancy balance, which typically consists of a rigid support frame incorporating a water tank mounted on a platform. A mechanical lifting device is used to raise the water tank through the frame height, allowing the specimen suspended below the balance to be weighed in air and water.
A number of tests can also be carried out on aggregate to measure how it will react in the presence of organic matter and certain chemicals; typically, chloride and sulphate content are measured using test strips. The data obtained from these tests can be used to ensure that the necessary precautions are taken in the mix design stage of a project, to avoid potential weaknesses. If an aggregate contains organic impurities it may be unsuitable for inclusion in concrete as these may interfere with the chemical reactions during the hydration process. Likewise, it is often important to test an aggregate for its resistance to physical changes in its environment, such as variations in temperature. The soundness and shrinkage of an aggregate can have a considerable effect on the long-term durability of the concrete that it is used to produce.
Finally, the mechanical properties of aggregates can be tested, ensuring that engineers are able to choose the most suitable material for a specific application. Dedicated testing equipment is available that can be used to determine properties such as resistance to impact, crushing and abrasion, simply and accurately. The aggregate’s resistance to polishing can also be measured to test how it will be affected by continuous contact with vehicle tyres, specifically in road-surfacing projects.
Quality control and concrete
When a suitable aggregate has been selected after extensive testing, the concrete that it is used in also needs to be thoroughly tested, both as a fresh mix and in the form of hardened samples.
Concrete is generally chosen for construction projects due to its combination of strength and versatility; however, with this flexibility come important issues that must also be addressed. Despite thorough knowledge of the aggregate used, the nature of other materials and of production processes, it is unlikely that any two batches will be identical in their qualities. Mixing methods can, for example, vary from batch to batch, or supplier to supplier, potentially resulting in finished precast components or liquid mixes with an unacceptable level of variance.
Stringent quality-control processes are essential when using both fresh concrete for pouring and spraying (shotcrete), and precast components such as liners and lintels, as the implications for inadequate quality checks can be fatal. In addition to the need to ensure the health and safety of construction workers, there are considerable commercial and legal repercussions, with the potential costs associated with court action, compensation and repairs, as well as the potential for negative publicity. Furthermore, the life of a structure can be significantly reduced as a result of incorrect formulation or consistency in mixing.
Testing concrete
These risks can be significantly minimized through sample testing using the latest generation of testing technology and processes, which now form an essential part of construction projects. Indeed, the cost of testing is relatively small when weighed against, first, the cost of a construction project as a whole, and, secondly, the potentially unforeseen expenses caused by structural failure or premature deterioration. Although many concrete testing techniques have been in existence for some time, the introduction of new technology is now making a considerable difference to the speed, accuracy and consistency with which these processes can be carried out.
Fresh concrete
Fresh concrete should be tested both before and during a project, to assess the suitability of the mix for its specific application, and to ensure that the concrete being used is providing a consistent standard throughout. Three proven methods of testing fresh concrete at different levels of workability are the slump test, the flow table test, and the Vebe consistometer test.
The slump test measures the consistency of freshly mixed concrete of medium consistency and is the most widely used method for assessing its workability. It involves filling a conical mould with a sample of wet concrete mix, compacting the sample and then lifting the cone. The slump is calculated by the difference in height of the mass before and after the cone has been removed.
The second method, the flow table test, is used where high workability mixes with a slump of 180mm or more are specified. This method determines the flow index of the concrete as an arithmetic mean of the diameter of the sample after it has been worked with a flow table that is dropped through a known height.
A third test for fresh concrete is the Vebe consistometer test, which is generally used with particularly stiff mixes. This test begins with the slump test as above, in which the result will be virtually zero. The sample is then subjected to vibration in a cylinder and the time taken for the sample to mould itself to the cylinder is measured. The longer the time in seconds, measured as Vebe degrees, the lower the workability.
Hardened concrete
In addition to determining the suitability and consistency of a mix by testing fresh concrete, hardened concrete should also be tested, both in the laboratory and on-site, to ensure that component parts have the desired properties and that concrete already in use has retained its qualities.
Plant-produced concrete is increasingly specified by contractors, normally in the form of precast components that are manufactured under controlled conditions, offering high levels of quality and consistency. However, even in these cases samples should be taken from site, or the production plant, to be tested under controlled conditions to safeguard against potential variability.
The density of hardened concrete can have a significant impact on its durability, strength and resistance to permeability. Density can be measured either by simple dimensional checks, followed by weighing and calculation, or by weight in air/water buoyancy methods.
Drying, shrinkage and moisture movement can also be measured in pre-hardened concrete samples. First, initial drying shrinkage tests can be undertaken, measuring the length of a moulded and cured specimen under specified conditions and comparing it to its final constant length when dried. Tests can also be carried out for drying shrinkage, which is the difference in length of a matured specimen cut from concrete and saturated, and its final length upon being dried. Thirdly, moisture movement, where the difference between the constant length of a specimen when dried and its length when subsequently saturated in water, is recorded. Each of these tests determines the change in length of a concrete sample brought about by a change in moisture content, allowing engineers to make accurate predictions of how a precast section will behave when in contact with moisture.
Compressive-strength testing
Perhaps the most important test for hardened concrete used in construction projects, however, is compressive-strength testing, which allows engineers to assess the strength of a concrete sample and its performance under actual loading, as opposed to the design loading. By testing in this way, any deterioration from chemical action, weathering, fatigue or excessive loading, can also be measured reliably.
The latest compression testing equipment, incorporating digital and microprocessor technology, makes the process extremely simple and accurate. This degree of closed-loop microprocessor control forms an invaluable element of today’s compression testing equipment, significantly increasing productivity and offering outstanding levels of accuracy and consistency in testing cycles.
Advanced microprocessor-controlled compression testing units, such as the ADR Auto range from ELE, can be used to provide accurate and detailed results quickly. Recording and analysing data automatically, the technology requires minimal operator involvement, allowing concrete suppliers to improve productivity and reduce costs. Combining robust construction with highly efficient operation, the machines are ideally suited to the high-throughput testing of samples, as well as being able to accommodate a wide range of sample sizes.
The latest machines also incorporate automatic test routines for Aggregate Crushing Value (ACV) and 10% Fines Value (TFV) as standard, controlling the loading of the sample at the entered pace rate until the load specified in the ‘failure threshold’ parameter is reached, at which point the load is released and the peak load displayed. The pace rate and threshold values can be edited as required.
The technology is fully compliant with the latest standards and specifications for concrete testing, and employs specially designed upper platen/ball seating arrangements to ensure there is no movement of the assembly after initial contact with the sample, as research has shown that any movement of the upper platen, coupled with frame deformation during the loading cycle of standard cube samples, can induce tensile cracks and result in variances in measured strength.
The machines use hydraulic power to provide the required pressure to the ram/cylinder unit of the load frame. As this is closed-loop microprocessor controlled, the need for expensive control valves and problematic oil-bleed-type valves is removed and the service life of components extended due to reduced operational stress. The testing process is largely automated; operators need only use a simple control panel for calibration, sample selection and test control, or to save, print or download test data to a PC.
Conclusion
The latest testing equipment and processes are allowing considerable improvements to be made in the quality control of concrete for construction projects, allowing suppliers to provide materials that are ideally suited to their clients’ individual applications. The result is stronger, more durable structures that are able to meet the needs of the initial design brief, thereby both increasing safety and having a positive impact on suppliers’ profits by ensuring consistently successful projects and satisfied clients.
For further information contact: John Sutton, group marketing manager, ELE International, Chartmoor Road, Chartwell Business Park, Leighton Buzzard, Beds LU7 4WG; tel: (01525) 249219; fax: (01525) 249249; email: john.sutton@eleint.co.uk