Concrete Supply Solutions To The Channel Tunnel Rail Link
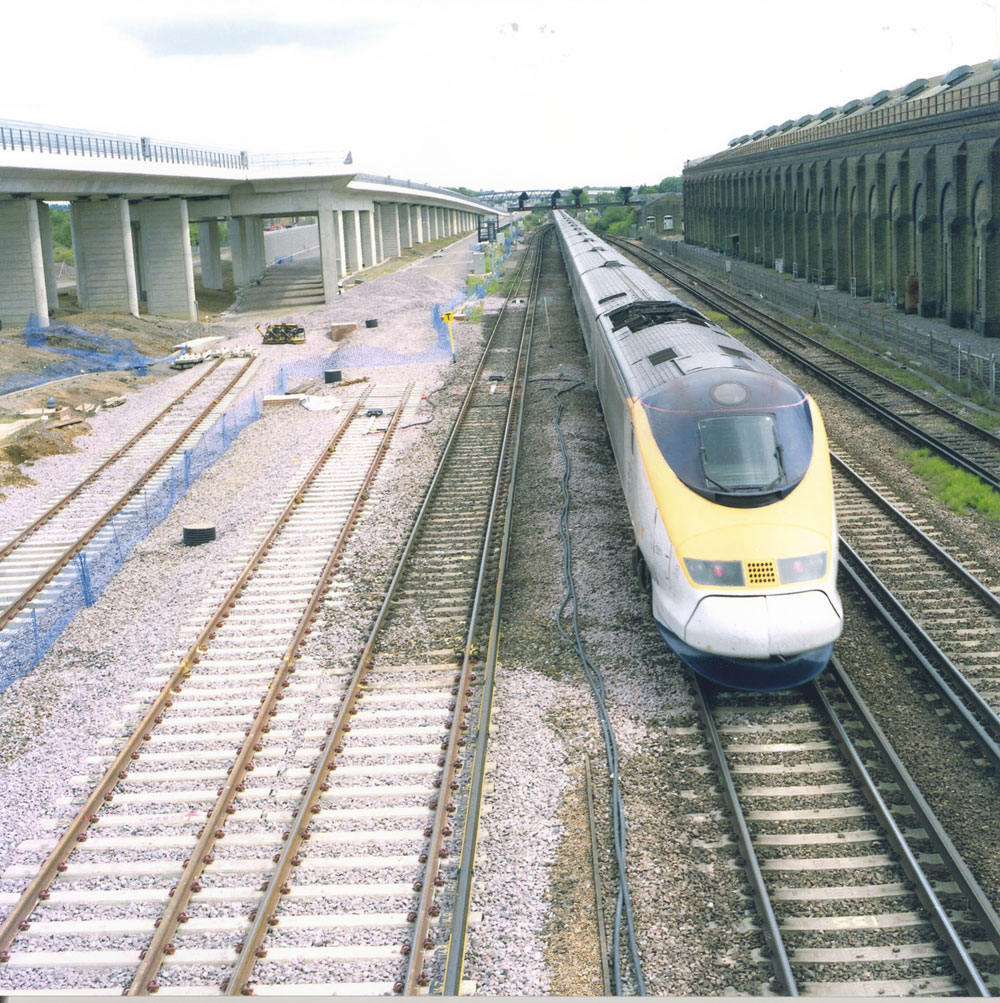
Brett Concrete's role in mix design and plant options on one of Europe's major construction projects
The Channel Tunnel Rail Link (CTRL) has been a very visible feature of construction in south-east England since 1998. Since that time it has been one of the major, if not the major construction project in Europe. The whole project is due for completion in 2007, although Phase 1 was opened to rail traffic in September 2003.
The scale of the project has posed many challenges to suppliers and contractors alike, particularly in terms of resource provision from the skills, personnel and materials perspectives. In this respect the ready-mixed concrete industry has sometimes been accused of being inflexible and unable to respond to changing circumstances, however the range of concrete types that have been supplied to the CTRL proves the opposite and highlights that suppliers are able to work in conjunction with contractors and clients to satisfy the most demanding of requirements.
Brett Concrete Ltd have supplied concrete to four major CTRL contracts (430, 420, 342 and 320) and have worked in partnership with contractors and the project manager, Rail Link Engineering (RLE), as well as acting as suppliers either solely on contracts or in conjunction with other suppliers as part of a joint-venture operation. The company’s approach to supply throughout the entire project has encompassed several fundamental tenets, namely: exploring partnerships, engendering a positive proactive approach, utilizing teamwork and clearly communicating in a consistent manner with all those involved in the supply chain.
Since commencing concrete deliveries in the autumn of 1998, Brett Concrete have supplied some 750,000–800,000m3 of concrete to the project.
THE CONCRETE SPECIFICATION
The CTRL concrete specification was extensively based on the Department of Transport Specification for Highway Works with contract-specific amendments as appropriate and required. Structural and piling concrete was essentially Grade 40 with specific durability requirements depending on the contract conditions. Concrete in the ground had to meet a range of Class 1 to Class 4 sulfate conditions.
Compliance was achieved by means of 4 analysis with the familiar moving margin depending on the standard deviation of the previous 40 results. The overriding requirement within the specification was for all concrete in contact with ground or air to be in compliance with the oxygen- and chloride-diffusion characteristics detailed below, and in reality this requirement was the main driver in terms of mix-design characterization.
The parameters within the structural concrete specification were as follows:
- Chloride diffusion coefficient to be less than 1x10-12m2/s
- Oxygen diffusion coefficient to be less than 5x10-8m2/s
At the commencement of the contract only limited knowledge was available to Brett Concrete about the mix parameters that would satisfy the requirements of the specification. Nevertheless, greater knowledge as a result of testing allowed the company to significantly improve their understanding of these parameters and to refine mix designs accordingly.
CONCRETE SUPPLIES TO PHASE 1
Brett Concrete were involved in two major contracts (430 and 420) with differing supply characteristics, both of which are now complete.
Contract 430
On Contract 430 (Ashford town centre to Lenham Heath) Brett Concrete entered a formal partnership arrangement with the contractor, Skanska Construction UK Ltd, and the project manager RLE. This arrangement meant that Brett were fully involved in developments on the supply side and were able to contribute fully to the decision-making process. The partnership also led to the development of a pricing formula based on material price and production-cost declarations.
On this contract, the initial considerations concerning concrete supply concentrated on the provision of sustainable sources of materials. The initial tender volume of approximately 285,000m3 meant that the supply of marine gravel concrete was not feasible due to constraints on the availability of coarse aggregates. Brett Concrete therefore sourced a sustainable supply of coarse Glensanda granite aggregate from Foster Yeoman’s wharf on the Isle of Grain, which was used in conjunction with marine sand landed at other wharves in Kent.
Concrete mixes were optimized for performance in conjunction with Skanska. As a means of moving away from the usual discussions about the workability of concrete, all structural concretes were designed with a target workability of 100mm and as pump mixes; a philosophy that was readily embraced by Skanska and RLE.
All concerned with the supply of concrete appreciated the costs of unnecessarily rejected concrete and the difficulty of disposing of such material on site. To overcome this a comprehensive water-addition procedure was developed and used, with the assistance of the project manager and contractor, for both piling and structural concrete options.
This procedure detailed the process for initial testing on site and the exact methodology to be followed if water had to be added, including the compulsory taking of extra cubes for strength testing. The procedure was distributed to all drivers, plant staff and representatives of the independent test house employed to carry out the compliance testing on site. Similar procedures, fundamentally based on the original generic procedure, have been used on all of Brett Concrete’s subsequent supply contracts.
A range of mix-design options was developed and offered to the contractor and RLE to optimize the commercial benefits available. In respect of the piling concrete, four ground granulated blast-furnace slag (ggbs) replacement level options were offered, with a range of 50–80% ggbs being available. Each of the different mixes attracted a different price and the contractor was able to take advantage of the price differences to suit particular circumstances.
In cases where piles were to be in the ground for a number of months before further work, higher replacement levels of ggbs were used; ultimately, almost all of the piling concrete was placed with 70% or 80% replacement.
All of the mix options were trialled through the formal trial mix procedure prior to being accepted as available approved options for use on site.
Similarly, structural concrete was offered with a range of ggbs options at 50%, 60% and 70%. This had the benefit of allowing large pours, such as bases and pile caps, to be placed using a low-heat option to minimize heat generation and limit the possibility of thermal cracking, while use of the 50% option permitted the placement of slender elements or elements where rapid formwork turnaround was required.
This approach to mix design had the benefit of maximizing the returns available to the contractor and project manager, and allowed the most economic options to be assessed and utilized for each particular situation.
Consideration of the batching plant required to supply the contract was also of prime importance; in this case two site plants were commissioned: a Steelfields Major 60 wide-line plant with a 3m3 capacity pan mixer, supplemented by an Elba 60 plant with a 1m3 capacity pan mixer. In addition, the local static plant in Ashford was upgraded so that it could support the supply of concrete to the project. All plants supplying the project were equipped with the latest computer-controlled batching systems, supplied by Command Alkon.
Workability control in the pan mixer was achieved by means of an ammeter fitted in the batch cabin, while concrete produced by the dry-batch process was controlled both visually and through the use of truck-based workability meters. These proved to be extremely successful.
All of the structural and piling concrete contained admixtures and these were stored on site in bulk double-bunded storage tanks in volumes of up to 10,000 litres; delivery was typically by tanker direct to site.
Haulage for the project was provided by a contract haulier who provided a core truck fleet with additional support depend-ing on the programmed quantity of concrete to be delivered in any given period. All trucks were equipped with regularly calibrated (every three months) water meters, so that if water needed to be added on site the exact amount discharged was known and could be recorded easily.
At the end of 2002 the project was awarded the accolade of ‘Major Project of the Year’ in the Annual British Construction Industry Awards sponsored by New Civil Engineer magazine and the Daily Telegraph.
A letter of recognition received by Brett Concrete from the project director noted: ‘To win this award is a real achievement and, as such, recognizes the hard work carried out by everyone on the contract. It is also recognition of the quality of the work carried out and the teamworking that helped the project to be completed on time.
‘Brett Concrete played a major role in this achievement, producing and supplying quality concrete throughout the project to allow the works to be completed on programme, supported by a first-class team who worked extremely closely with Skanska.’
Contract 420
On Contract 420 (Boxley to Lenham Heath) Brett Concrete led a consortium that was put together to supply both the aggregate and concrete requirements of the project. The consortium, KCML (Kent Construction Materials Ltd), was a joint venture between Brett, Hanson and RMC.
Brett Concrete project managed the supply and acted as the liaison and contact point between the contractor and the supply consortium; taking the lead in regular progress meetings on site as required, Brett were able to liaise with the other suppliers as appropriate.
The consortium appointed a project manager and shipper, both of whom were based on site in the main project office. They formed the primary day-to-day link with the contract and were able to bring in specialist support as required.
Up to seven supply plants were made available by the consortium, all of which utilized marine aggregates and were able to use a single consistent mix design for each of the mix options developed. Formal plant trials were carried out on each plant for the piling and structural mix options. The consortium was able to show that the sources available were all demonstrably similar to QSRMC requirements. Part of the approach was to ensure that all plants carried the same admixtures and cementitious materials and, where necessary, supply sources were changed to meet this requirement.
This project benefited from having the resources of three major suppliers at its disposal with a single point of contact to ensure consistency of approach.
CONCRETE SUPPLIES TO PHASE 2
Supplies to the second phase of the project have, in may ways, been more challenging than on Phase 1, essentially due to the different nature of the concrete mixes required, over and above the more normal structural and piling options; these include steel fibre-reinforced shotcrete supplies (Contract 342) and segment concrete (Contract 320).
Contract 320 is now 99.5% complete, while concrete works for the structures on Contract 342 are approximately 85% complete.
Steel fibre-reinforced shotcrete
Supplies of steel fibre-reinforced shotcrete were required for temporary works to allow construction of the foundations associated with a major bridge slide on the North Kent Rail Line, which forms part of the Ebbsfleet Contract 342 works.
Initial indications suggested that a total volume of 400–500m3 would be required but in fact some 2,500m3 have actually been supplied, mainly due to the ground conditions encountered in a chalk spine that had to be excavated.
The mix design was essentially ‘prescribed’ with 430kg/m3 CEM I, approximately 60% fines content (marine sand), a maximum aggregate size of 10mm and the use of crushed rock (granite) aggregate. The mix had to be set-retarded for in excess of 12h using Delvocrete stabilizer and was required to contain 40kg/m3 of steel fibres.
The supply of steel fibre-reinforced shotcrete required the installation of a stainless steel admixture pump and special lines, as the stabilizer had a pH value of 2.
Steel fibres were imported from Germany in 20kg boxes and transferred into a dispenser that ‘blew’ them into the truckmixer. Other plant constraints meant that the concrete had to be dry batched with an extended mixing time of 30–45min to ensure the elimination of cement or fibre balls. Workability control was also critical with a target of 175mm slump ±25mm.
Haulage was provided under a contract between the contractor and the site-based haulage subcontractor; this allowed the contractor to have trucks available 24h a day.
Again the importance of understanding the contractor’s needs and discussing all details of the supply on a regular basis cannot be overemphasized.
Segment concrete
The volume of segment concrete required for the Thames tunnels on Contract 320 was approximately 45,000m3.
Hochtief Murphy constructed a purpose-built factory on site solely for the purpose of supplying this element of the contract. It consisted of a single carousel system capable of producing up to 140 segments a day.
The specification for the segment concrete contained requirements in respect of the following parameters: compressive strength, tensile strength, first-crack flexural strength and residual flexural strength. Additionally, a measurement of the distribution of steel fibres was also included. In addition to steel fibres the mix was designed to contain monofilament polypropylene fibres for fire-protection purposes.
As usual in a precast operation, efficiency in the turnaround of the moulds was paramount and the de-moulding strength of 18N/mm2 was required to be achieved at 6h or earlier (albeit after steam curing). The use of hot water at 55°C, when necessary, facilitated the stripping of moulds at 5h. Strength was assessed from cubes that had passed through the curing process alongside the segment moulds.
The target workability for the mix was required to be in the range of 20–30mm slump, to facilitate finishing of the extrados of the segments prior to steam curing, which typically commenced approximately 1h after the mould had been filled with concrete and vibrated.
Ground conditions necessitated compliance with Class 4 sulfate conditions, hence the use of a PFA-blended cement to achieve the early strength, stripping times and specification durability requirements.
Brett Concrete invested in fibre-handling and transfer devices to facilitate the loading of the steel and polypropylene fibres; both devices were linked to the plant’s batch computer to ensure consistent, accurate weighing and autographic recording of all materials in each batch of concrete. The company also arranged for containerized bulk deliveries of 400kg bags of steel fibres from Germany, and the bulk delivery of polypropylene fibres in 250kg boxes, to facilitate loading into the bulk dispensers.
The whole supply operation depended greatly on a proactive approach by the suppliers, customer and project manager alike. Undoubtedly, the process often proved time-consuming and frustrating, however the successful placement of segments in the tunnel provided sufficient reward for those involved.
The compliance requirements for this particular mix were onerous and influenced by many factors beyond the control of the concrete producer. These factors are discussed in two papers1&2 published in Concrete magazine.
By developing an understanding of the difficulties involved in the production of the concrete for this critical phase of the project, Brett Concrete were able to negotiate a position whereby the risk factors beyond the control of the concrete producer were accepted by the contractor — another example of a close working relationship.
CONCLUSIONS
The Channel Tunnel Rail Link has been a major feature on the construction landscape since 1998. The project has been demanding for concrete suppliers and the approach employed to meet these challenges has required the application of a flexible approach to both traditional and new methods of work, the embracing of teamwork and partnering principles and techniques, as well as continued close-knit communication between the supplier, contractor and client.
ACKNOWLEDGEMENTS
The author would like to thank members of Rail Link Engineering’s staff, in particular Peter Shuttleworth, for assistance throughout the project. Thanks are also due to the publicity department of Union Railways for permission to view information included in this paper.
REFERENCES
- BOURNE, A.: ‘Precast segments on the Thames tunnels’, Concrete, 2002, vol. 36, no. 4, pp32–33.
- BOURNE, A., and W. LEIGHTON: ‘Segment mix on the Channel Tunnel Rail Link’, Concrete, 2003, vol. 37, no. 4, pp13–15.