Compact Mobile Concrete Batching
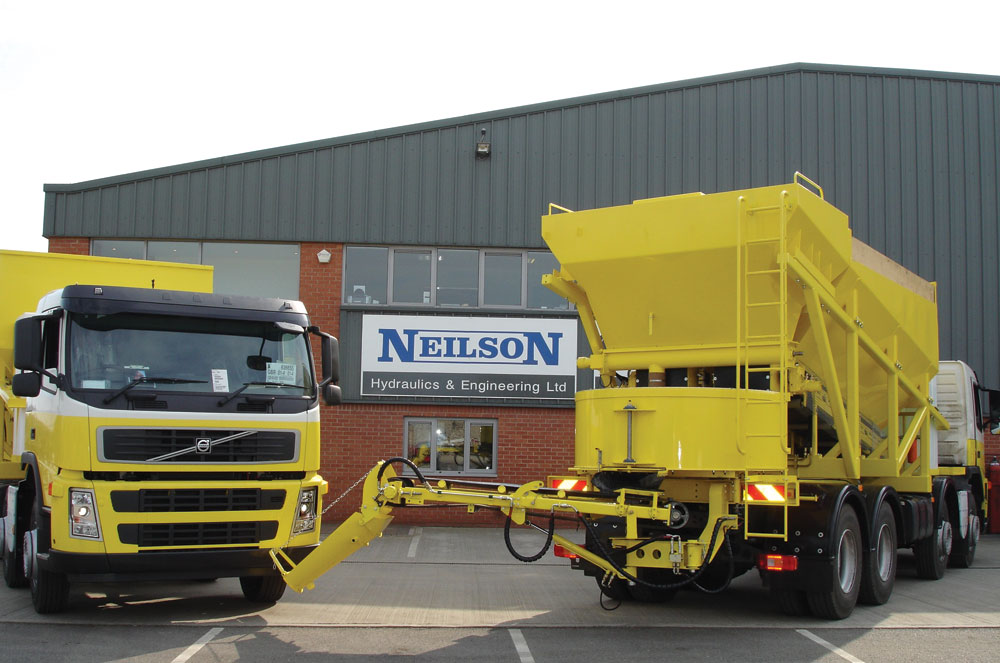
Benefits of the Flow Stone mobile concrete batching system
By Norman Opie, director, Flow Stone, Neilson Hydraulics
Batching by weight has long been established as the most accurate and efficient method of concrete production. Market innovators Neilson Hydraulics launched their Flow Stone mobile batching system in early 2005 and have refined its design for 2008/09, incorporating more than three years of operational feedback to reflect the demanding environment in which the system operates.
The Flow Stone mobile batch weighing system is a quick and accurate method of ensuring that quality concrete of the right strength is available on demand on site, without any waste or mess. It works by duplicating the control and accuracy of static batching plants to serve all markets for concrete, screed and mortar.
Flow Stone system
Owing to the precision of its weigh cells, Neilson Hydraulics say the Flow Stone system is probably the most accurate ‘mix at site’ concrete system available, which means there should be no market sector for concrete, screed and mortar that the system cannot supply, providing there is a quality assurance system in place to confirm material source and specification.
Unlike volumetric truckmixers, QSRMC have confirmed that no ‘special’ regulations need to be applied to the Flow Stone system, and that users could adopt QSRMC’s standard regulations for fixed plants. This means the Flow Stone system is not restricted to producing 25N/mm2 strength concrete, as is the case with volumetric machines.
Volumetric metering of cement to a continuous mixer is dependant upon a constant value for the cement’s bulk density. This can vary from 1,000 to 1,400kg/m3, depending on age, method of storage (25kg bags/silo/big bags etc) and whether it has been aerated or vibrated.
Truckmixers have an added problem in that transport causes vibration, thus the longer the journey, the more compact the cement will be. A 10% variation in bulk density, and therefore weight of cement per cubic metre, is thus entirely possible. Batch mixers avoid this error by weighing all components, whereas volumetric mixers often overdose cement (and thus increase costs) in order to avoid producing under-strength concrete.
Transporting the dry ingredients and batching plant to site also eliminates the typical ‘ready-mix’ problem of waste from over-ordering, making it a particularly suitable solution for small builders, fencing contractors and council road repairs. The initial batch of concrete can be specified, batched and discharged within minutes of the truck’s arrival at site, with the additional benefit that the customer that dictates the exact amount of concrete for the foundation, slab etc, thus avoiding the cost of disposal of excess concrete.
The production of ‘special’ concretes/mortars is also simplified using a batch-weighed system. The addition of liquid or powder additives and fibres can be done by weight, and mixing time can be adjusted to suit certain additives that require a defined period of mixing to allow the appropriate chemical reaction to take place. The batching process also eliminates the need for the expensive fibre or powder/granule feeders used with continuous volumetric mixers.
The Flow Stone system differs from a static batching plant in that it utilizes the mixer pan as the weigh vessel, into which aggregate, sand, cement and water are sequentially conveyed/pumped, weighed and mixed prior to being discharged and the batch ticket printed.
Outputs vary with mixer volume and type, and a planetary mixer option has recently been developed that offers outputs from 4 to 20m3/h. Models are available with a wide variety of options to create a bespoke service.
Skid- or site-trailer-mounted static versions can be supplied with up to four aggregate hoppers, two cement silos and three additive pumps. These can be powered by a three-phase electrical supply, generator or hydraulics and a donkey engine. The truck-mounted option is hydraulic, with the hydraulic pump being driven by the truck PTO.
The PTO/hydraulic powered model shown in figure 1 is mounted on a 44-tonne Volvo chassis and carries the equivalent of 9m3 of concrete.
Hook-frame-mounted versions with increased capacities up to 8m3 of ‘unmixed’ concrete are suitable for dual-purpose use, either as static or mobile self-contained batching plants.
Mixing
The documented mixing and discharge cycle is fully automated and initiated by a single ‘on’ switch. The mixer computer controls the aggregate hoppers, cement silo(s), conveyer belts and water/additive pumps. The mixing cycle lasts 2–3min minutes depending on the required mix recipe, slump etc, and the panel display allows the process to be monitored while in progress.
An integral printer provides full documentation for each mix, identified by a unique batch number, and lists the individual weights of the aggregate, cement, water and additive(s) used.
An optional remote control can be fitted for improved operating efficiency and convenience.
As with static plants using weigh/batch software, multiple repeatable recipes can be called up based on industry or company standards. The software ensures that a batch will not complete in the event of an exhausted hopper, silo or tank, which means that operator error and wastage is reduced. The batch computer also ensures that constituents/concrete are to within 1–2% by weight.
Neilson Hydraulics have incorporated a number of safety and operational features in the Flow Stone system to simplify its operation, making it easier to use for staff who may have limited technical expertise, while ensuring the concrete produced complies with pre-programmed recipes. Wear parts are confined to the mixing pan, which has replaceable Hardox 400 liners and plastic mixing paddles. The loading and mixing system is capable of passing oversize aggregate with little damage.
Other than the Danfoss hydraulics, all other Flow Stone system components are modular in design and manufactured in the UK, with the control panels being built in house. Spares are readily available, allowing operators to benefit from the prompt and efficient service necessary to maximize plant utilization, while providing high-quality concrete.
To ensure compliance to customers’ quality systems, Neilson Hydraulics also offer a quarterly calibration and service programme, which ensures that the batch weights of ingredients, and the concrete sold, are to within ±2%.
An additional innovation particularly applicable to recycled aggregates or the processing of trench arisings that require a high-shear mixing action, is the option of independently driven hydraulic planetary mixing rotors. These rotors (maximum 400 rev/min) prevent ‘balling’ and help break down sticky and viscous materials, such as clay.
Neilson Hydraulics say their expertise with hydraulic drives has led to a flexible design where the speed of the rotors and main pan drive can be varied independently and automatically in response to varying materials and power requirements during the mixing cycle.
The processing of trench arisings, which often have a high clay content, requires the clay to be broken down using a high shear action, to allow complete mixing with cement and/or hydrated lime in either a wet or semi-dry process. Accurate dosing, by weight, of the cementitious material controls the ultimate strength of the processed arisings for trench backfill. This is important because HAUC and similar bodies require backfill strengths to be within strict limits.
The planetary mixer option can be fitted as an alternative to the standard pan mixer on both the truck and the static units, allowing specialized concretes, mortars and screeds to be produced, as well as reducing mixing times.
For further information contact Norman Opie on tel: (01709) 821002; email: norman.opie@neilson-hydraulics.co.uk; or visit: www.flow-stone.co.uk