Quarrymen: The Next Generation
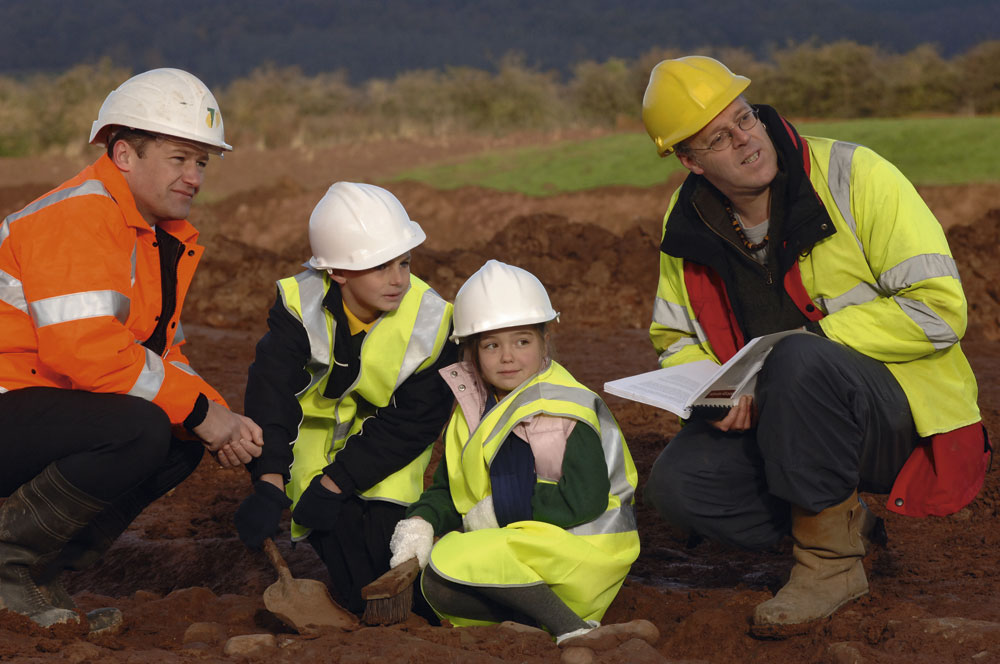
Where are future quarry managers going to come from?
When I was asked to speak at the 2005 Institute of Quarrying conference on ‘Quarrymen – The Next Generation’ (meaning where are future quarry managers going to come from?) a few things immediately came to mind. First, I remembered that The Beatles were originally called The Quarrymen. Secondly, it made me think of Star Trek — as in ‘Star Trek – The Next Generation’. And finally, I thought how the term ‘quarrymen’ is quite blatantly gender biased and does not sound at all encouraging or welcoming to women.
Random thoughts? At first they were, but on reflection they had meaning.
It is difficult to imagine a young aspiring band of today calling themselves ‘The Concrete Technicians’ or something similar. Perhaps that is a sign of how perceptions have changed for our industry.
Additionally, if like me, you have followed the Star Trek series over the decades, you will have watched the technology on the Starship Enterprise become ever more advanced. Things now move much faster and the lives of the crew, particularly the captain and the officers, have become ever more complicated with mounting risk and responsibility at every turn.
Quarry managers are the officers on our ‘starships’, and the demands we make of our quarry managers have increased enormously since Captain Kirk first ‘boldly went’ in the late 1960s. When speaking to a senior director about the lot of a quarry manager recently, he felt that, in comparison, 20 years ago quarrying was a relatively relaxed environment. Now he could see how quarry managers would feel themselves to be ‘accountable for everything’, with support sometimes not always what it could or should be.
Tarmac quarry managers and their deputies need to be fully competent from the time they take on their responsibilities. It is essential that they understand and comply with quality standards, the ever-tightening Environmental Management System and Tarmac’s continuous drive for a Zero Tolerance safe and healthy working environment. They also have to keep up to speed with IT systems, maintenance regimes, cost control, cost reduction, employee communications, development and leadership, and of course, always keep the customer satisfied.
It is clear that we demand a lot. However, the changing nature of the job cannot be to blame for the apparent shortage and projected shortage of good people.
Tarmac’s retention record among graduate recruitments is very good. Once we get young, talented people to join us, they quickly become aware of what Tarmac and the role have to offer. We retain people by providing real responsibility and challenging careers.
Attracting individuals to begin a career in quarrying is another issue. Over the centuries quarrying has logically been inextricably linked with mining. While mining in the UK was a vibrant core industry, we were able to follow in its ‘slipstream’ in sourcing talent for quarry managers and other key roles.
The sad story of the UK mining industry is well known. For the quarrying industry, however, the decline in mining provided a temporary and unexpected benefit. Quarrying was able to access the talent that the decline in the mining industry made available, delaying the impact of our own industry supply ‘time bomb’. Unfortunately, that seam of talent is now running out.
In addition, while the decline in the mining industry might have supplied us with talent on a short-term basis, long term its implications have been more negative. The reduction in mining in the UK has resulted in the continuing reduction in mining faculties at UK universities. Unfortunately, a general perception that quarrying is a ‘sunset industry’ means that applications to the few courses that remain are also in a downward spiral.
With fewer and fewer young people being given the opportunity to start a career in mining or quarrying our industry time bomb is getting closer and closer. It could be argued that we should position ourselves away from mining to enhance our reputation. However, partnering ourselves with our sister industry — construction — would also be littered with hurdles.
Research conducted by Tarmac and completed in 2004 as part of the ‘Skills for Life’ initiative shows that, like quarrying, the picture for the construction industry is not very encouraging. A survey of over 1,600 members of the UK public showed that the construction industry is bottom of the heap in terms of the most popular industries to work in (fig.1). Sadly, a quarry worker was the least popular profession in the construction sector (fig. 2).
To continue the space theme ….‘Houston, we have a problem’. But thankfully the problem is one that, as an industry, we can overcome.
In essence, a talented workforce is one of our best resources. A resource is a key asset for our business success. We are all competing for the same resource. The traditional local supply route for that resource is restricted. We try to open up new sources of supply but the external environment is not particularly helpful to us.
The features of this problem will be familiar to all of us and closely parallel another key resource vital to success within our industry — aggregates.
To address problems with aggregate supply we put real effort, time and money into gaining a clear picture of what we currently have (estates, land and minerals teams), we make the most of the resources we actually have (capex investment and process improvement) and we look again at the resources that may have been passed over in the past and endeavour to convert them into a new source of value (beneficiation and recycling).
We do not give up in the face of environmental and community difficulties, but develop close links and relationships with those bodies and institutions that can help us (PR, lobbying and community engagement). We jealously guard the resources we have and see them as a competitive advantage, but we also collaborate across the industry with the major players taking a lead. We also look further afield and, when the economics work, we import resources that are in short supply locally.
Surely we can learn from other aspects of our businesses, and since the features of both the above resource problems are similar, surely we should take a logical approach to our response. What could that mean for sourcing the next generation of quarry managers?
One thing our people do not have in common with aggregate reserves is that we can talk to them. And we should. It is tempting to look for new resources and overlook the maintenance of what we have. Our first step should be to invest in developing and supporting existing quarry managers and other such groupings at the heart of our businesses through effective and sustained learning and development. Tarmac have introduced a talent-management programme based on a model jointly developed across all sister Anglo American divisions.
Graduate recruitment has always been a means of sourcing talent and this is the equivalent of the highest-quality virgin aggregate. But graduate recruitment alone is not the answer. Traditional graduates will see the role of a quarry manager as a part of their development, but not as a career goal. After two or three years they will want to move on.
Additionally, if the Government reaches its goal of 50% of school leavers going to university, quarry companies will have to view graduates in a differentiated manner, just as universities endeavour to differentiate school leavers.
Tarmac have already introduced paths within their graduate programme that will recognize that some have clear high-flying international potential, others have more traditional potential and a further group will not necessarily be suited to senior levels of management, but will provide the bedrock talent at the heart of the business. As mentioned earlier, few will have mining or related degrees, so provision for extensive conversion will be required.
As an industry we also need to develop effective, modern apprenticeship programmes to generate a further source of future quarry managers. Tarmac have already had some success in this area, and plan to extend it.
Earlier I painted a bleak picture of the uphill struggle we face in making ourselves an attractive industry — be it with our mining heritage or as part of construction. But that does not mean we face an impossible challenge.
Raising awareness of the benefits and rewards of a career in quarrying is essential — as is educating young people from an early age about the role quarrying has to play in their daily lives. We need to make quarrying relevant again.
Quarryville is an educational programme launched just over a year ago that resides on the Tarmac web site: www.tarmac.co.uk. It extends through many aspects of our industry, but it is designed to be of practical use for teachers and pupils in that it is structured to fit in with the curriculum and key stage learning requirements. This innovation has now been taken up by the QPA as part of the ‘Virtual Quarry’ web site, and is an example of how imaginative we can and must be (fig. 3).
The UK mining schools need continued support. Mining is a global growth industry and the major mining houses — Anglo American, Rio Tinto, BHP Biliton, Xstrata — have recognized the need to support the mining schools with offers of lectureships and chair sponsorships at Camborne School of Mines and Leeds. Whether or not they succeed is in the balance. As the indigenous industry players we must play our part.
The European universities have set a global trend of staying in business through collaborative arrangements, led by Delft in the Netherlands. We can support this collaboration, the pattern of which is extending to other continents.
It is crucial that we provide support and at the same time raise our profile through providing work experience for those who are actively seeking a career in the quarrying industry. Tarmac, as part of Anglo American, have been participating in the STEP (Student Technical Experience Programme) since 2002. From eight placements in 2002 to 27 in 2005, this is an area of growth, but another interesting trend is the increase in students from non-UK universities — now almost half.
This leads on to the final and possibly the most important element of the strategic response — importation on a global scale.
The UK mining school programmes are under severe pressure despite outside support from the mining majors. Steadily reducing from four, then to potentially only two providers in the UK, the options are limited. But a global survey by the Society of Mining Professors in October 2004 identified over 270 institutions that offer such programmes. Over 50 of these were located in Western and Central Europe. Many new or accession EU countries still have a mining industry in place, under pressure, but still in place.
It is true that the closure of mining faculties is a global phenomenon, but there are plenty still left. The UK is an attractive destination, but if we are only prepared to ‘fish for cod’ because that is what we have got used to over the years, we will increasingly come home with empty nets. Issues of language, work permits and standards have traditionally been seen as barriers. Such barriers do exist, but they are getting lower all the time. India will produce 2 million English-speaking graduates this year. The UK government has eased work permit matters with its ‘Highly Skilled Migrant Programme’ and many of the Central European countries realize the value of English as a second language. In the short time since the IoQ conference last year, it is clear that a major influx of people from the accession countries has happened and is with us now.
For those of us seeking to grow internationally it is an obvious move. I suggest it is just as valid for the local players, the SMEs.
At last year’s conference I was challenged that in sourcing managers from developing countries, we would be under-mining the skills base of these countries and acting immorally. My response is that if the traffic is one way and all we are doing is draining talent from these countries, we would be indeed acting immorally. But, given the excellence in operating standards that we can inculcate into those we recruit from developing countries in terms of health, safety and the environment, if we actively re-export skilled and SHE-aware managers back to their countries of origin, our actions are the height of morality. As the quarrying industry develops in such countries, it will be to our standards. Think of China and some of the horrific accidents and environ-mental disasters that are regularly in the news. We can make a positive difference. I would argue it is our moral responsibility.
There is certainly a potential problem in sourcing the next generation of quarry managers, but if we tackle the problem with the same vigour and inventiveness that we address the sourcing of that other vital asset — aggregates — we can succeed in finding the next generation. In the words of The Beatles (nee The Quarrymen) ‘We can work it out!’
Tony Davies, Head of Human Resources – Tarmac Group (Anglo American plc), presented this paper at the Institute of Quarrying’s annual conference symposium in October 2005.