Material Supply In A Low-Carbon Economy
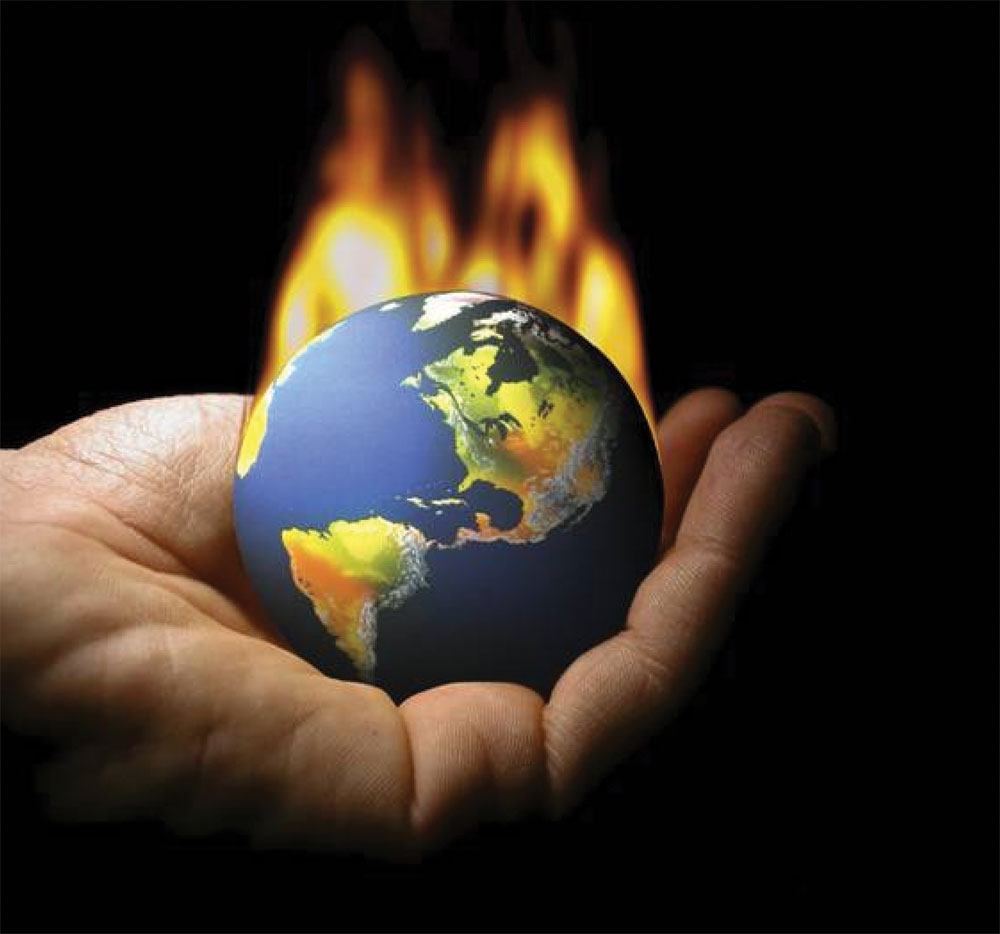
By Colin Jenkins, managing director, Aggregate Industries UK, Aggregate Products Division. This article is based on a presentation given at The Institute of Quarrying’s 2008 annual conference.
What do we mean by a low-carbon economy and what would it be like to live in one? Taken to the extreme, a low-carbon economy would have no fossil fuel-driven transport and societies would be largely self-sufficient – living ‘The Good Life’ but perhaps not in such an entertaining way as the 1970s sitcom suggested.
Zero-carbon living is not just about short-term expedience but about delivering long-term solutions. We cannot continue emitting carbon dioxide at the current rate; climate change is happening and we have to change the way we do things as a society. Clearly, it is in industry’s interest to minimize fuel consumption and waste. Lower fuel usage means lower carbon emissions, and the quarrying industry has a key role to play in meeting the challenges of the low-carbon economy.
London, in particular, faces many challenges from climate change and regeneration. The 2012 Olympic build and legacy programme has shown one way to address these challenges. At the core are two issues – design and material supply – which exist at opposite ends of the procurement chain and do not interact sufficiently.
The fundamental challenge is securing a sustainable supply of building materials, of which a substantial part will be aggregates (primary, secondary and recycled). Over the past four years the aggregates industry has reduced the amount of carbon dioxide produced per tonne of production, but we should not be complacent – there is still some way to go.
What are the barriers holding us back?
Legislative barriers
Securing planning permission requires a considerable amount of time, energy and resources before the essential materials needed to meet society’s demands can be extracted.
Why are we so regulated and why does it take so long to get permission? Quite simply, laws exist to provide minimum standards; standards which, historically, have not been achieved voluntarily by this industry.
The extractive industry is one of the most regulated in the UK and, unlike other commercial and industrial developments (which have a permanent consent), our planning permissions – our licence to operate – are subject to review every 15 years.
Our historical performance has been, in part at least, responsible for the regulations we have today; to change that, we have to listen to our stakeholders, understand their concerns and move to better ways of contributing to a low-carbon economy.
Geological barriers
We cannot change the location of aggregates – only plate tectonics can do that. Minerals have to be extracted where they naturally occur. What then happens to them, how we move them or use them in other products determines the carbon footprint of the final product. Manufactured products, whose raw materials may be moved a number of times in the process leading up to final installation, lead to greater CO2 intensity.
Greater London has little locally occurring material left yet it consumes, on average, some 20 million tonnes of aggregates annually. Virtually its entire primary aggregate requirement has to be brought in from outside the region.
Although much of this is transported by rail or water to depots or wharves, at some point it has to be put on a lorry to travel by road to the construction site.
Fuel for delivery is, therefore, a large source of CO2 in our product’s carbon footprint. As an industry, we have encouraged hauliers to improve their driving skills to reduce fuel consumption. The operation of larger vehicles and also back-hauling is employed to increase vehicle utilization whenever possible, as it is in our interest to minimize this financial and environmental cost.
It is also in our interest to push for increasingly efficient engines, and yet here too we have a conflict. The Euro 5 diesel engine standard for lower exhaust emissions actually uses more fuel per mile, so reduced emissions or lower consumption, which is it to be?
Investment in infrastructure, not only building new roads but also investment in local rail networks and improved access to waterways, would make a significant overall contribution to reducing carbon levels. For example, rail produces 3.0kg of CO2 per tonne of material transported compared with road at 4.24 kg/tonne. Although these things are not always in our control, with careful planning and commitment we can influence a change.
Commercial barriers
Construction materials have to meet customers’ expectations and their delivery is, of course, ‘part of the job’. Contractors and suppliers have, for many years, been required by some clients to provide evidence of capability and performance as part of the selection process prior to or during tender. Much of this is derived from public-funded schemes with government determined to raise standards in the marketplace.
The scope of this evidence has widened over the years to include most elements of sustainability. The amount of detail required to be submitted has gradually increased – but this can be an opportunity for those who have already internalized the cost of sustainability to show value to clients. Quality price bids are becoming increasingly common in an attempt to place more emphasis – or perhaps value – on sustainability. Consequently, the quarrying industry is increasingly being asked to demonstrate its sustainability and environmental credentials, and we welcome this raising of the bar.
Our customers and their clients are also specifying their own environmental and sustainability requirements, often driven by the planning system and government policies, and also by developers who see commercial benefit from adopting sustainable principles.
The Government’s vision for Corporate Social Responsibility (CSR) is ‘to see UK businesses taking account of their economic, social and environmental impacts, and acting to address the key sustainable development challenges based on their core competencies wherever they operate, locally, regionally or internationally’.
This vision committed all government departments and agencies to produce sustainable development plans – these plans, naturally, feed into the requirements placed upon us by our customers and clients.
The Highways Agency published its first Sustainable Action Plan in 2007, and while the plan focused directly on the organization’s offices, staff, customers and contractors, consideration was given to product lifecycles, procurement, processes and materials used in the construction and maintenance of the road network, and the Agency’s target to reduce congestion.
The Highways Agency’s plan states that they ‘…will influence their contractors and suppliers through the procurement process…’.
Local authorities too have developed sustainable-development plans. For example, Cambridge City Council state: ‘Development will only be permitted if it meets the principles of sustainability’. All developments require the completion of a sustainable checklist and the submission of a sustainability statement.
The Code for Sustainable Homes sets target dates for achieving zero-carbon or carbon-neutral homes. The construction and use of homes are given a star rating to demonstrate environmental performance. Requirements include ‘embodied energy’ of materials and are based on BRE methodology.
All these demands have similar aims but their implementation and assessments vary. Fortunately, through BREEAM (Building Research Establishment Environment Assessment Method), some commonality and standards are being introduced. Architects and designers rely on this information to aid them in the decision-making process. These are necessary and welcome changes. We cannot delay developing and implementing the best sustainable option; we must be prepared to mitigate environmental and social costs. Are we ready to meet that challenge?
If government’s targets are achieved, by 2016 the only contribution to CO2 emissions from a home will be from the materials in its construction. Are we in danger of being left behind?
At Aggregate Industries we have invested in our business to be ‘a responsible source’. Holcim too have again been named ‘Leader of the Industry’ in the Dow Jones Sustainability Index and have thus been acknowledged as the company with the best sustainability performance in the building materials industry for the third year in succession.
But what are we prepared to pay to achieve the best sustainable option? Are we prepared, for example, to risk losing an order as we try to persuade a customer to order a more sustainable product, or do we allow our customers to continue as before?
Specification barrier
Throughout the UK, minerals are seemingly ubiquitous and commonplace in the form of rock, sand and gravel. Yet we transport Chinese and Indian stone over 8,000 miles to pave our streets and gardens and clad our buildings. We want to see shinier, smoother materials as we walk down the high street so we import materials from all over the world to meet these requirements.
As producers, we are in a position to influence that choice, but we need to be involved early in the design process.
Designing products that minimize their environmental impact has to be right. Ecopoints, developed by BRE, is a method of measurement of environmental performance that indicates the environmental impact of a product – the higher the point score, the worse it is. Indian sandstone, for example, has 6.4 ecopoints per tonne, compared to 1.9 per tonne for a wet-cast replica stone paving flag.
Could simpler, local materials be specified for use in projects designed to be deconstructed?
Durability of our products is our unique selling proposition as a sector and, in conjunction with our clients, we need to continue to demonstrate this. If we are really serious about achieving a lower-carbon economy, we have an obligation to work with architects, specifiers, clients and contractors and to share the risks and rewards involved in proving sustainable product solutions, or we need to edit the choice of our customers – for example, Wyvale have now stopped selling patio heaters.
Fundamentally, the built environment is not designed for deconstruction and until such time as it is, the use of recycled materials cannot be optimized. Their use has grown, triggered by taxes, specifically the landfill tax, as the chart (below) shows.
Working together we can increase the use of recycled products and we can gain approval for materials that have a higher recycled content.
We must demonstrate that these products work just as well as those made from primary materials. Perhaps then there will be fewer material specifications which would reduce processing and increase economies of scale. Put simply, less processing equals lower carbon.
Stakeholder barriers
Of course, public perception is fundamental to our licence to operate. The perception of our neighbours and the community to which we are linked is an important aspect we all take into consideration. Dust, noise and vehicle movements are often the top three issues on their agenda. There is no getting away from the fact that minimizing dust and noise is a significant technical challenge in winning mineral.
Our industry takes corporate social responsibility (CSR) very seriously indeed. We are changing. We are becoming better guardians of the environment. We have biodiversity and geodiversity action plans and we create and maintain wildlife habitats, and not just as a condition of planning. At the end of their lifetimes, our operations are often transformed from carbon producers to carbon consumers. The restoration plans and outcomes more often than not return operations that are biodiverse and environmentally enhancing.
So, what is the solution?
Careful planning is essential to ensure that environmental impact is minimized.
It is also in the industry’s interest to reduce carbon, and we have not been standing still. In 2004 the Quarry Products Association produced its first sustainability report on the industry – a benchmark to demonstrate its commitment to sustainability.
The change starts with us. Quarries are often well located, off the beaten track and hidden from view. Located in rural areas and open to the elements, there are many operations situated in places suitable for the production of renewable energy. Would we get planning permission? Would it be worth our while? Are we trying?
Increasing the use of rail and water requires planning permission. Transporting aggregates by rail produces at least 30% less carbon per tonne than transporting the same quantity by road. Large quantities by sea are even better. Flexibility in our opening hours to meet demands would minimize the distance travelled by road vehicles.
With permission, the importation of inert waste material into quarries without financial penalty would provide the opportunity to develop more environmentally friendly products.
Strategic planning is long term, providing long-lasting solutions, but there are many things we can do now to improve our current performance. Perhaps we should liken the materials we supply to a mortgage that has to be paid back in 30, 40 or 50 years’ time?
It is not only about stone in the ground; it is about choice and the price we have to pay today for a sustainable future. Are we engaging effectively with our customers and our customer’s customers – helping them to make better, more sustainable decisions?
Are we prepared to design our environment with deconstruction in mind? Are we prepared to take out the glass, porcelain, timber and plaster before demolishing a building? Maybe refurbishment should always be considered first.
The commitment to change has to be throughout the entire supply chain. We are changing our ways, the market is changing, society has to make a choice – and we have to influence that decision.
Acknowledgement
The author would like to acknowledge the support and help of Annette Roberts and Chris Higgs in preparation of this paper.