A Century Of Success
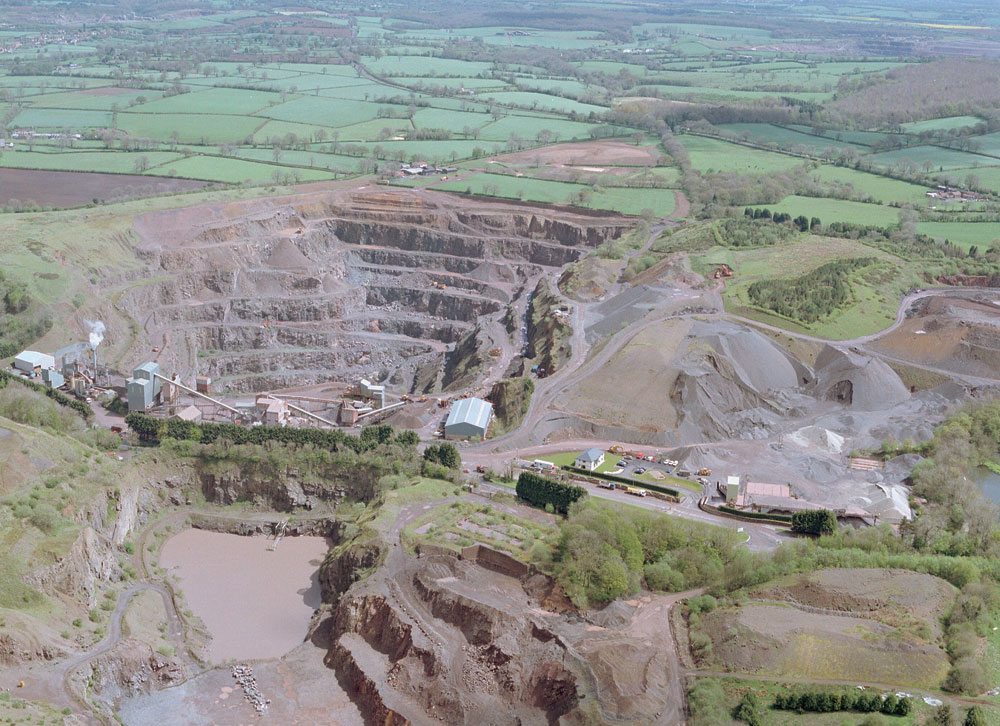
John Wainwright & Co. celebrate 100 years as a limited company
As the 19th century drew to a close, the growing demand for good-quality building stone for roads and railways in the south of England led to rapid growth in the commercial extraction of limestone deposits in the Mendip Hills. To help satisfy this demand, a shrewd Somerset businessman by the name of John Wainwright began acquiring land and quarries in the region and established John Wainwright Quarries in 1891, at a time when much of the extraction and processing work was still being done by hand. Although he purchased a number of limestone quarries, his most significant acquisition was Moons Hill Quarry, located on the only ‘hard-stone’ outcrop in the region. This site was purchased in 1897 and has formed the basis of the company’s success through to the present day.
Back at the beginning of the 1900s, however, the business was in need of a large capital investment in new crushing machinery. This was partly financed by J.P. Luff, a prominent local figure who became a partner in the business, which in 1902 was formed into the limited company John Wainwright & Co. Ltd. With business booming and profits increasing, in 1905 the company invested in a fleet of 500 railway wagons, but a few short years after this major development John Wainwright died, leaving Mr Luff in sole charge of the company. In 1934, during the lean times of the depression, the company made the decision to divest all its limestone interests, instead choosing to concentrate on hard-stone production at Moons Hill.
In the 70 or so years since then, a succession of replants at Moons Hill has seen production capacity increase from around 13 tonnes/h in the 1930s to some 350 tonnes/h today. Likewise, a Stothert & Pitt coating plant installed at the site in 1934, which had a modest output of 80 tonnes a day, was replaced in 1972 by a Parker Starmix plant capable of producing 80–100 tonnes/h.
Despite all the industrial and social upheavals of the 20th century, the company retained its independence throughout, with three successive generations of the Luff family at the helm prior to the appointment of Peter Barkwill as managing director in 1997. Today John Wainwright & Co. supply a range of high-quality roadstones, surface-dressings and coated products into Somerset and surrounding counties as far afield as West Sussex and Oxfordshire. They also supply their own highly successful surfacing and contracting division, which was established in January 2001.
Moons Hill Quarry
The Moons Hill Quarry complex (the site also includes the adjacent Stoke and Sunnyhill quarries) covers an area of 240 acres at the eastern end of Beacon Ridge, close to the village of Stoke St Michael and about four miles from Shepton Mallet. The quarry exposes part of a unique sequence of andesites created by volcanic activity approximately 425 million years ago. The main rock mass comprises a hard, grey/ brown or greenish pyroxene-andesite, which is described under its trade group as ‘basalt’.
In laboratory tests this basalt has been found to have a PSV of 56, an AAV of 3.7, an AIV of 13, an ACV of 14 and a soaked 10% fines value of 320, making it the only hard-stone material in the region suitable for use in road surfacing. Reserves of stone at the site comprise some 51 million tonnes with planning consent, together with a further 16 million tonnes of unconsented material.
The premium-grade basalt is generally capped by substantial thicknesses of overburden and 20–30m of lower-quality weathered material, of which around 150,000 tonnes/year is processed separately using hired-in mobile plant to produce a range of secondary-grade aggregates and fills. Some of the overburden is utilized in landscaping and screening bunds around the site, with the remainder being placed in tips.
Most of the stone is worked from a series of 11 benches in the main 460ft deep excavation. The majority of these benches lie below the water table, which necessitates the pumping out of around 1.5 million m3 of water every year, a huge task that accounts for 25% of the site’s total annual electricity bill. Future operations at Moons Hill will see the main void reach a maximum depth of 600ft.
Drilling and blasting work is carried out by Frome-based contractors WCD Sleeman & Sons Ltd, who have retained the Moons Hill contract since 1983. After blasting, the material released is loaded into one 50-tonne and two 40-tonne Aveling Barford dumptrucks for transport to the primary crusher.
Processing operations
At the primary crusher house the rock is fed from a 100-tonne feed hopper to a Nordberg C125 primary jaw crusher by means of a vibrating grizzly feeder which removes any fragments less than 75mm. These are transferred to a Pegson 2.4m x 1.2m scalping screen which separates the –40mm material for transfer to the scalpings stockpile. Oversize product (–75mm +40mm) from the scalping screen is fed directly to a 20-tonne capacity surge bin where it is combined with –150mm crusher run from the primary crusher. From here the material can either be fed directly to the secondary crusher, or it can be sent to a –150mm crusher-run stockpile for subsequent delivery to the secondary stage via a recovery tunnel conveyor system.
The secondary crusher, a Nordberg standard-head 1352 Omnicone, operates at a nominal capacity of 325 tonnes/h at a close-side setting of 60mm. The secondary product is fed directly, via a short conveyor, into the tertiary crusher, a Nordberg short-head 1352 Omnicone which operates at a nominal 220 tonnes/h at a close-side setting of 30mm. The combined effect of the secondary and tertiary crushing stages is a –40mm product which is then passed over a 4.2m x 1.5m Pegson Vibro King selector screen. This allows –6mm material to bypass the quaternary stage while the oversize material is fed into a storage bin mounted above the quaternary crushers.
The –40mm +6mm is choke fed into a line of three crushers — a Pegson 700 Autocone, a Nordberg HP200 short head, and a Sandvik H3800 medium-fine — via individual chutes fitted with clamshell doors. The quaternaries are set to produce a –20mm product which is remixed with the –6mm pre-screened material before being conveyed to the final screens.
Final screening takes place on a series of three Don Valley linear-motion screens fitted with Tema Isenmann polyurethane decks. These are capable of screening up to 350 tonnes/h and are set to produce final product sizes of: dust, 5mm, 6mm, 10mm, 14mm and 20mm. Any rejects (+20mm) are recirculated back to the quaternary crushers in a closed-circuit arrangement. After screening, the various product sizes are either stockpiled for sale as dry products or conveyed to the coating plant. All materials destined for surface-dressing applications are fed to the washing plant before being sent to ground stockpiles.
The Parker Starmix asphalt plant, which has produced over 3 million tonnes of coated materials since it was installed in 1972, has been modified and upgraded a number of times over the years but is now scheduled for replacement in the near future. Capable of producing up to 1,000 tonnes a day, the plant draws 80–90% of its feed stock from the main screen bins but is also supplied by four 12-tonne capacity ground hoppers. Mixed materials are delivered by skip hoist to one of three hot-storage hoppers which have a capacities of 70, 50 and 25 tonnes, although a direct discharge facility is also available.
Markets and distribution
Moons Hill Quarry currently has a market-driven output of around 700,000 tonnes a year, although in more buoyant times has produced up to 1.25 million tonnes. The quarry’s main markets are in Somerset, Dorset and Wiltshire and other counties south of a line between the Wash and the Severn, to north of which competition with the Leicestershire hard stone quarries increases significantly. However, Moons Hill roadstone has been used as far afield as Istanbul, for resurfacing work on the Bosporus Bridge, as well as on bridges a little closer to home such as the first Severn crossing and the Avon Bridge. The inert nature of the Moons Hill basalt also makes it particularly suitable for other more unusual applications, such as the construction of bank vaults and seaside aquariums.
Coated products are generally delivered within an 80-mile radius, with significant quantities going into Devon and some even reaching as far as London. And since establishing an in-house surfacing and contracting division last year, the company now has even more of a ready market for its coated products. This business offers a full works package from material supply through civils to surfacing and white lining.
Product deliveries from Moons Hill are effected by the company’s fleet of 22 smartly liveried vehicles, together with outside hauliers as demand dictates. In total the quarry employs 65 staff directly and between 22 and 39 others on a contract basis. Because of the aggressive nature of the basalt on machinery and equipment, the quarry has extensive workshop facilities with three full-time static plant fitters, two fabrication workers and two mobile plant fitters.
Environment
Although Moons Hill Quarry is accepted locally as an important part of the community and as a valued source of employment, with its deep void and various product and waste stockpiles, John Wainwright & Co. have taken great steps to reduce Moons Hill’s impact on the local landscape and have adopted a proactive approach to the environment. Over the years much work has been done to screen local residents from the visual impact of the quarry, including the construction of landscaped bunds and the planting of tens of thousands of trees. The company is also committed to maintaining the flow in the local stream during the drier summer months by pumping water from a 420 million litre storage reservoir. Moreover, at the southern end of the site a disused part of the quarry has been turned into a attractive fishing lake surrounded by woodland. With enough mineral reserves to last well into the 21st century, further enhancements will be made on an ongoing basis as part of the quarry’s long-term phased restoration plan. The company is currently working towards an integrated management system encompassing ISO 14001, ISO 18001 and ISO 9002.
Acknowledgement
The editor wishes to thank John Wainwright & Co. Ltd for permission to visit Moons Hill and, in particular, Peter Barkwill, managing director, and Ian Timberlake, commercial director, for their help in preparing this report.