Promoting Intelligence in Aggregates
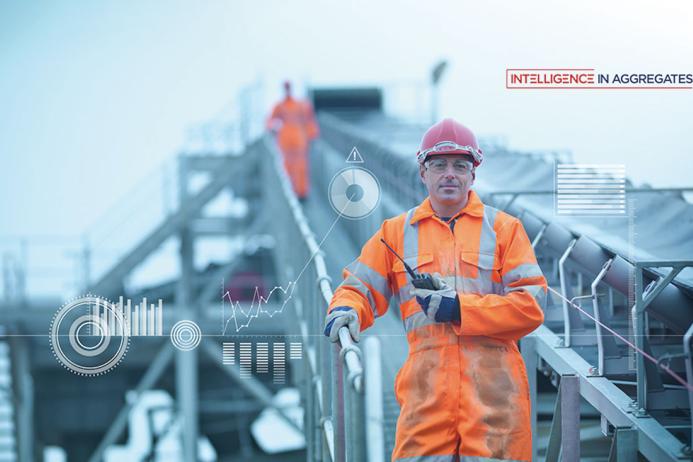
First published in the June 2023 issue of Quarry Management
Automation systems business development manager Trevor Herbert discusses Mitsubishi Electric’s commitment to improve productivity and boost equipment reliability in the aggregates industry
Maximizing uptime, increasing productivity and reducing operating cost will be high on the agenda for any quarry manager. Mobile plant providers and their dealers have been playing an increasingly active role in this process, using telematic monitoring to report on the real-time operating condition of haul trucks, excavation and loading machinery, whilst employing fluid analysis and preventative maintenance to reduce unexpected downtime and costly machine breakdowns.
Mitsubishi Electric’s automation systems business development manager, Trevor Herbert, believes the time is right for companies to broaden this focus, to include a wide range of static plant within the quarry in this technology equation. While many larger sites will have some form of monitoring of crushing, screening and washing equipment productivity, along with the miles of conveyor systems that feed them, very few are employing the in-depth condition monitoring that has become commonplace on much of their mobile plant for those static installations.
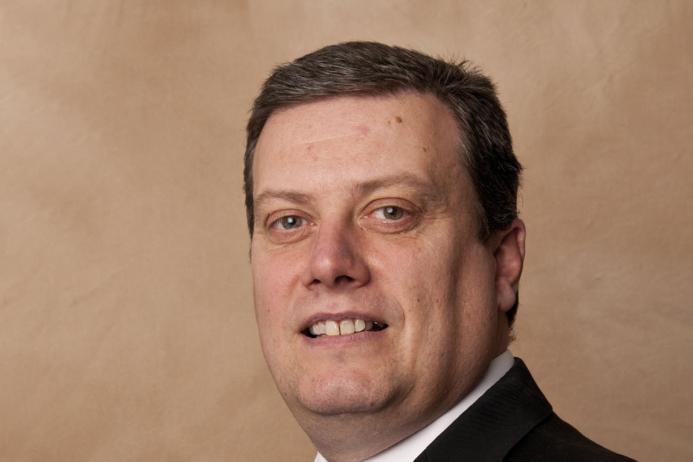
‘There is a lot of outdated equipment out there, some that is 30 to 40 years old,’ said Mr Herbert. ‘Today you don’t get much more than standard control room information and this leads to a reactive process, repairing breakdowns on site after they occur. We realize that for better plant performance, we have to look at asset utilization, availability and a move from reactive to proactive maintenance.’
Installing monitoring technology within the harsh operating environment of mines and quarries has never been an easy task. However, companies like Mitsubishi Electric now offer a wide range of smart asset-monitoring solutions, specifically built to withstand these arduous working conditions. The good news for operators is that moving towards this technology does not have to happen all in one go. Companies can introduce monitoring and operational technologies in phased steps, spreading the investment cost and allowing easier adoption on site.
‘We build smart condition-monitoring technology into our variable drives and other automation components, that allows us to see potential problems before they occur,’ said Mr Herbert. ‘We can also retrofit smart condition-monitoring solutions on to older components, but fault-diagnostic analytics is built into all of our new products and solutions.’
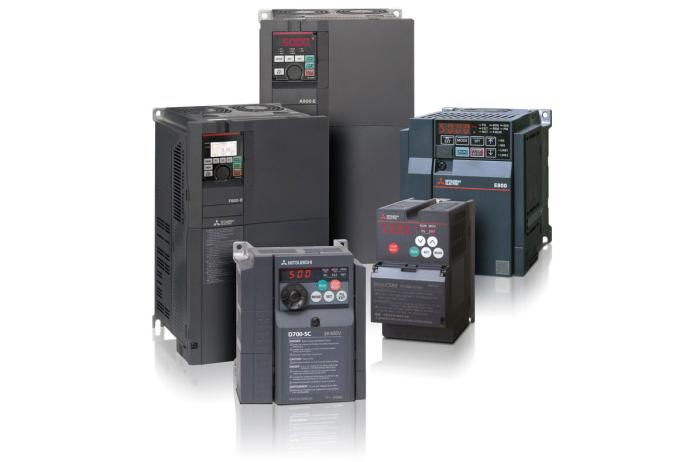
Mitsubishi Electric are not simply looking at the hardware however, the company also focuses on the software, to create complete automation solutions for quarries. From intelligent devices, such as variable-speed drives, through to programmable logic controllers (PLCs), Mitsubishi Electric use open connectivity to bring together components, including those from other automation vendors, to create a complete picture of the health of the quarry operation. Using plant visualization software, it is then possible to integrate the entire quarry into a complete automated solution.
Further good news for operators, by installing smart technology, companies can also save money in everyday operation. In traditional quarry works, conveyors may run all shift at a single speed, whether they are moving material or not. The same is true for washing plants, crushers and screens. By slowing conveyors and pumps when full production is not required, through the use of variable-speed drives and control systems, it is possible to reduce energy use, wear and tear, and operating cost.
On one UK site, Mitsubishi Electric carried out a detailed energy audit on the crushers, pumps and bulk-handling conveyors for the customer. As an example, one piece of equipment that was assessed was a 55kW lagoon pump. Traditionally, this pump had operated for 9h a day, five days a week, for 50 weeks a year. Within that time, it consumed 132,353kWh of energy, at a price of £0.23 per kWh. That put the average energy cost at £30,449.19 per year, producing the equivalent of 93 tonnes of CO2.
By equipping the lagoon pump with a variable-speed drive from Mitsubishi Electric’s FR-800 series, it was possible to reduce the average pump speed by 10%. That resulted in an annual energy saving of 32,884kWh and a reduction in the site’s carbon footprint of 23 tonnes of CO2. It also increased the lifespan of the pumping equipment and improved motor control, whilst the investment in the new drive was paid back in less than a year.
That reduction in CO2 emissions has become an increasingly important metric for many aggregate producers. Any company aiming for net zero in such an energy-hungry industry will need to access the sort of accurate data that comes with automation and total site visibility.
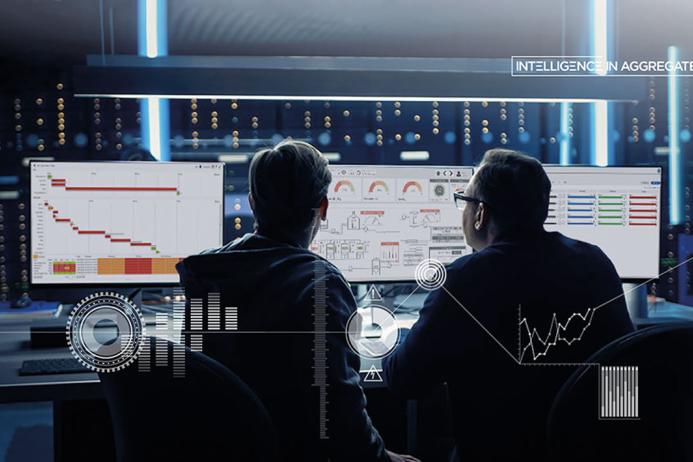
Mitsubishi Electric recognize that different quarrying companies will be at various stages along the path to site automation and they will require a range of site solutions. They may also need to see a return on investment from the initial drives and systems installed, before moving on to additional areas within the quarry.
‘You can start on the journey, but you don’t need to get there straight away in one go,’ said Mr Herbert. ‘It is possible to install variable-speed drives now and then integrate them into a larger quarry-wide system later. We can also add a plant visualization system to an existing site using other automation manufacturers’ equipment. We are building the open-communication architecture and data-analysis capability to work from top to bottom. We are looking to improve automation at all levels.’
Businesses that are interested in improving automation within their quarries, can contact Mitsubishi Electric directly, through the company’s website. Using their own teams and with trusted third-party providers, Mitsubishi Electric offer a range of value-added services, from energy walkarounds and analysis of existing systems, to site design improvements for the future.
Under the umbrella of the recently launched Intelligence in Aggregates initiative, the company is committed to improving productivity and boosting equipment reliability, through site surveys, installation and integration of drive systems, and automation and visualization of the quarry process.
‘These are just some of the services that we can provide to the industry,’ said Mr Herbert.
Subscribe to Quarry Management, the monthly journal for the mineral products industry, to read articles before they appear on Agg-Net.com